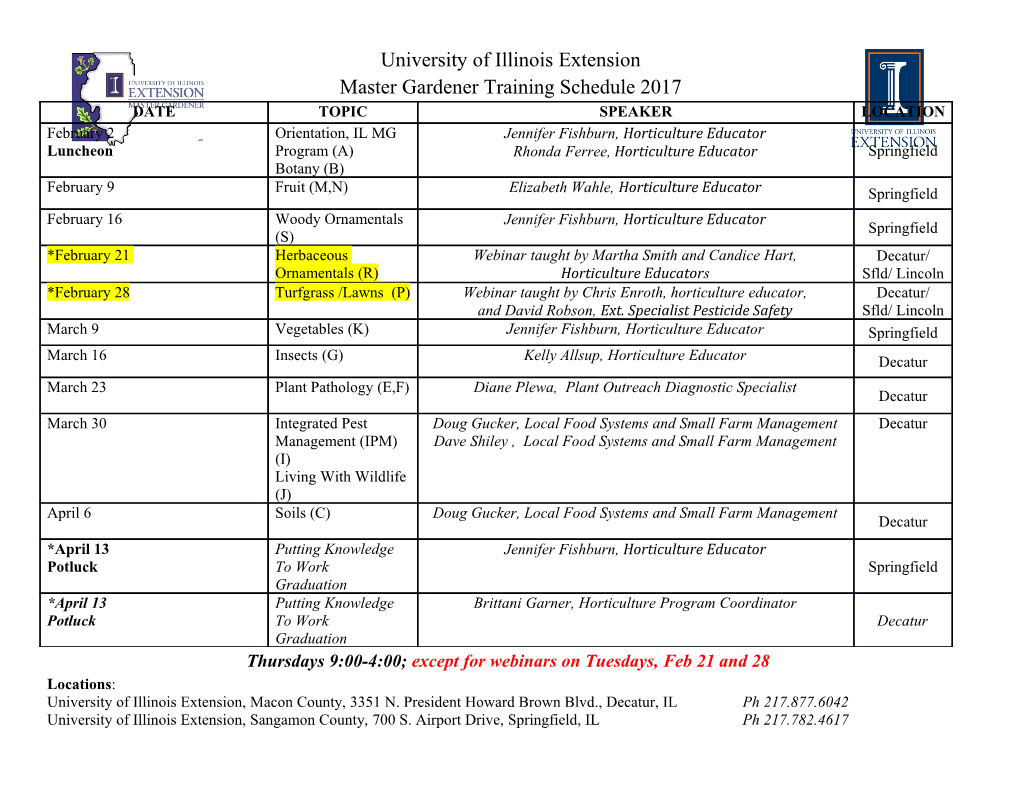
European Biofuels TECHNOLOGY PL AT FORM Biofuel Fact Sheet Dimethyl ether (DME) Lab scale Bench scale Pilot Plant Demonstration Production Introduction Molecular Formula Dimethyl ether (typically abbreviated as DME), also known as methoxymethane, wood ether, dimethyl oxide or methyl ether, C2H6O / CH3OCH3 is the simplest ether. It is a colourless, slightly narcotic, non- toxic, highly flammable gas at ambient conditions, but can be O handled as a liquid when lightly pressurized. The properties of DME are similar to those of Liquefied Petroleum Gas (LPG). H3C CH3 DME is degradable in the atmosphere and is not a greenhouse gas. Comparison of Fuel Properties See page two for Production Process. Property DME Diesel Density at 20 0.67 0.83 Applications °C [kg/l]* Due to its good ignition quality, with a high cetane number, Lower heating 28.4 43.1 DME can be used in diesel engines as a substitute for value [MJ/kg]* conventional diesel fuel. However, compared to diesel fuel DME has a lower viscosity (insufficient), and poor lubricity. Cetane 60 50 number* Like LPG for gasoline engines, DME is stored in the liquid state under relatively low pressure of 0.5 MPa. This helps to limit the Fuel 0.59 1 number of modifications required to the engine. Still, some equivalence* slight engine modifications are necessary, primarily relating GHG [gCO eq/ Waste wood to the injection pump and the installation of a pressure tank, 2 MJ]** DME: 5 similar to that for LPG. The fuel line must also be adapted with specific elastomers. Farmed wood DME: 7 DME in diesel engine burns very cleanly with no soot. Source: FNR 2012. * Median values are used for simplification. The infrastructure of LPG can be used for DME. As part of the Please refer to the standards for ranges. ** Directive 2009/28/EC, FP7 project BioDME, under the leadership of the Volvo Group, total for cultivation, processing, transport and distribution DME production is being optimized, especially for use as a transport fuel. Utilization European Projects on DME Substitute for diesel fuel; transportation fuel; power generation fuel; domestic gas BioDME - Production of DME from Biomass and utilisation as fuel for transport and for industrial use. Funded by 7th Relevant fuel regulations Framework Programme and Swedish Energy Agency. EN590 (diesel fuel) Main feedstocks Forest products, agricultural by-products, organic waste, energy crops, black liquor Scale of Production Demonstration scale Dimethyl ether (DME) Biofuel Fact Sheet Production process State of the Art DME is primarily produced by converting natural gas, organic The DME demonstration plant in Piteå, Sweden, which was waste or biomass to synthesis gas (syngas). The syngas is then put into operation in 2010, is the only gasification plant converted into DME via a two-step synthesis, first to methanol worldwide producing high-quality synthesis gas based on in the presence of catalyst (usually copper-based), and then 100% renewable feedstocks. The raw material used is black by subsequent methanol dehydration in the presence of a liquor, a high-energy residual product of chemical paper and different catalyst (for example, silica-alumina) into DME. pulp manufacture which is usually burnt to recover the spent The following reactions occur: sulphur. 2H2+ CO CH3OH 2CH3OH CH3OCH3 + H2O CO+H2O CO2+H2 Alternatively, DME can be produced through direct synthesis using a dual-catalyst system which permits both methanol synthesis and dehydration in the same process unit, with no intermediate methanol separation, a procedure that, by eliminating the intermediate methanol synthesis stage, the licensors claim promises efficiency advantages and cost benefits. Both the one-step and two-step processes are commercially available. DME can also be converted itself into olefins and synthetic hydrocarbons. BioDME plant with DME log truck in foreground © Chemrec 2011 Major stakeholders Further information Volvo Group, Sweden Up-to-date information on Diemethyl ether DME R&D&D Chemrec, Piteå, Sweden is available on the Euorpean Biofuels Technology Platform website www.biofuelstp.eu. Haldor Topsøe, Kgs. Denmark Preem, Sweden Total, France All trademarks, registered designs, copyrights and other proprietary rights of the organisations mentioned within this document are acknowledged. While the information in this fact sheet is believed to be accurate, neither EBTP members nor the European Commission, accept any responsibility or liability whatsoever for any errors or omissions herein nor any use to which this information is put. The Secretariat of the EBTP is partly supported under FP7 Grant Agreement 241269. However, the information expressed on this fact sheet should not under any circumstances be regarded as stating an official position of the European Commission. Design and content of this fact sheet are copyright © European Biofuels Technology Platform 2011. European Biofuels TECHNOLOGY PL AT FORM Biofuel Fact Sheet Ethanol Lab scale Bench scale Pilot Plant Demonstration Production Introduction Ethanol, also known as ethyl alcohol, pure alcohol, grain Molecular Formula alcohol, or drinking alcohol, is often abbreviated as EtOH. H C H OH H EtOH is a light alcohol and is a volatile, colourless, flammable 2 5 C liquid with a characteristic odour. EtOH burns with an almost H C OH invisible flame and is biodegradable. H H Without proper conditions, EtOH attracts water while stored. Comparison of fuel properties Another important feature of EtOH is the formation of an azeotropic mixture with water. Origin Ethanol Petrol See pages 2 & 3 for Production Process, State of the Art and Density at 20 0.79 0.74 Applications. °C [kg/l]* Lower heating 26.7 43.9 Major stakeholders value [MJ/kg]* Octane >100 92 The major bioethanol stakeholders in the EU are listed below: number* Abengoa Bioenergy, Spain Fuel 0.65 1 Tereos, France equivalence* CropEnergies, Germany GHG [gCO2eq/ Sugar beet Cristal Union, France MJ]** ethanol: 33 Agrana Group, Austria Farmed wood Verbio, Germany ethanol : 20 Agroetanol, Sweden Wheat straw Industria Meridionale Alcolici, Italy ethanol: 11 AlcoBioFuel, Belgium N.prior bioenergy, Germany Source: *FNR 2012. Median values are used for simplification. Chemtex, Mossi & Ghisolfi Group, Italy Please refer to standards for ranges. ** Directive 2009/28/EC, DONG Energy, Denmark total for cultivation, processing, transport and distribution Abengoa Bioenergy, a biofuels subsidiary of the Abengoa Utilization group, is the European leader of fuel bioethanol Substitute for petrol; petrol blend component; production. In 2011, its production capacity was equal to feedstock for petrol additive ETBE 3125 millions of litres, 1,500 of which was distributed on the EU market. In the fiscal year 2011/2012, the French Relevant fuel regulations industrial group Tereos registered a total production capacity of 543 Ml while the German group CropEnergies EN 228, EN 15736 reached a total production capacities of 692 Ml/yr. Main feedstocks Sugar and starch from agricultural crops, (sugar cane, cereals, sugar beets); lignocellulosic biomass (forestry residues, agricultural residues, energy crops) Scale of Production Industrial production for first-generation ethanol and pilot-plant/demonstration scale for second generation (cellulosic) ethanol Ethanol Biofuel Fact Sheet Production process EtOH is a naturally widespread chemical, produced by ripe EC-funded projects on ethanol fruits and by wild yeasts or bacteria through fermentation. BIOLYFE - Demonstrating large-scale bioethanol Ethanol from biomass can be produced from any production from lignocellulosic feedstocks feedstock containing appreciable amounts of sugar or NEMO - Novel high-performance enzymes and materials that can be converted into sugar. Fermentation micro-organisms for conversion of lignocellulosic (biotechnology) is the predominate pathway for EtOH biomass to bioethanol production. Biomass can also be converted to EtOH via biotechnological and thermochemical pathways. DISCO - Targeted DISCOvery of novel cellulases and hemicellulases and their reaction mechanisms for Biochemical pathways hydrolysis of lignocellulosic biomass (FP7) The most common raw materials are sugar cane and BABETHANOL - New feedstock and innovative corn, and in temperate climates also sugar beet, wheat transformation process for a more sustainable or potatoes. The overall fermentation process starting development and production of lignocellulosic from glucose is: ethanol C H O 2 C H OH + 2 CO 6 12 6 2 5 2 PROETHANOL2G - Integration of biology and Naturally, the underlying biochemical processes are engineering into an economical and energy- much more complicated. Adapted yeasts, for example efficient 2G bioethanol biorefinery Saccharomyces cerevisiae are used and fermentation can HYPE - High efficiency consolidated bioprocess be carried out with or without the presence of oxygen. technology for lignocellulosic ethanol With oxygen some yeasts are prone to respiration, the conversion of sugars to carbon dioxide and water. As EtOH KACELLE - Demonstrating industrial scale second is a toxin, there is a limit to the maximum concentration generation bioethanol production – Kalundborg cellulosic ethanol plant in the brew produced by the yeasts. This results in a high energy demand for EtOH purification by distillation. FIBREETOH - Bioethanol from paper fibres separated In industrial processes an efficiency of about 90 to 95 % of from solid waste, MSW theoretical yields can be reached. But, unmodified yeast LED - Lignocellulosic ethanol demonstration
Details
-
File Typepdf
-
Upload Time-
-
Content LanguagesEnglish
-
Upload UserAnonymous/Not logged-in
-
File Pages11 Page
-
File Size-