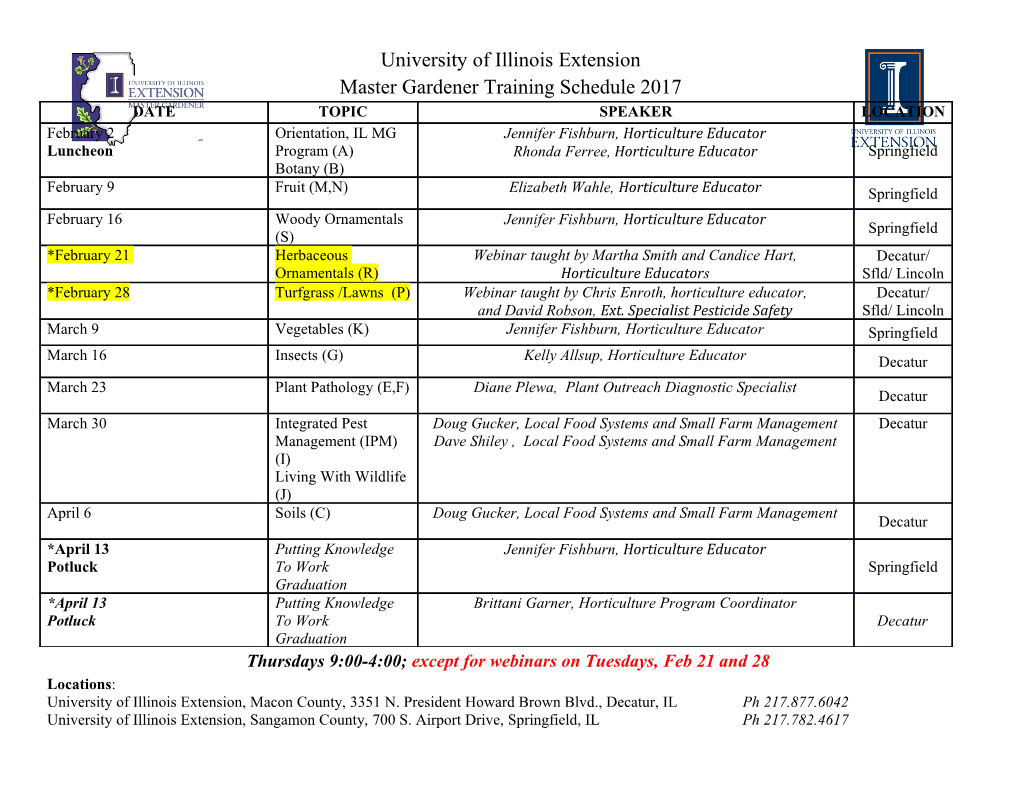
www.musictrades.com FEBRUARY 2018 $3.00 The Perfect Pairing Buffet Crampon ’s acquisition of Powell Flutes creates benefits for two companies with a similar artist-focused approach to the market. Buffet Crampon gains a leading position in the professional flute market, while Powell gains access to a global marketing team. POWELL FLUTES THE PERFECT Buffet Crampon’s acquisition of Powell Flutes creates benefits for two compa - Pnies withA a similar arItist-focRused approIach to Nthe market. BG uffet Crampon gains a leading position in the professional flute market, while Powell gains access to a global marketing team. f conventional marriages have a failure rate of around 50%, corporate tie-ups probably fare even worse. In the music products industry, the frequency of failed acquisitions has led some to sarcastically define “corporate synergy” as 2+2=3. However, if there ever was a proverbial “match made in heaven,” it was Buffet Crampon’s 2016 acquisition of the storied Verne Q. Powell Flute Company of Boston. For Buffet Cram - pon, the transaction immediately filled a large gap in its product offering with Ian acclaimed line of high-quality flutes and piccolos. The deal also brought together two companies with a similar focus on serving artists with instru - ments of uncompromising quality. Buffet Crampon clarinets are the choice of an overwhelming majority of the world’s most discerning clarinetists, A handmade just as Powell flutes can be found anywhere serious music is being made. Powell solid silver flute For Powell, the benefits were equally significant: access to a potent global (right) and a distribution network, a corporate parent with a deep understanding of how Sonaré to simultaneously maintain the integrity of an instrument, and fiscal sol - model with a vency. proprietary François Kloc, President of Buffet Crampon USA, who was involved Aurumite in every step of the acquisition process, describes Powell as the perfect headjoint. complement to Buffet Crampon’s other venerable brands, including the namesake woodwinds, founded 1825, Besson brass, founded 1837, B&S brass, founded in the early 19th century, Antoine Courtois Paris brass, founded 1789, Hans Hoyer French Horns, founded in the early 19th century, Julius Keilwerth saxophones, founded 1925, Melton Meinl Weston low brass, founded in the early to mid-19th century, J. Scherzer rotary trumpets, founded 1900, and W. Schreiber bassoons, POWELL FLUTES The Powell Flute team in front of the Maynard factory. (l-r) Christina Cobas, director of marketing; Hannah Liuzzo, Powell Sonaré product specialist; Alfredo Munoz, customer service representative; Francois Kloc, president, Buffet Crampon USA; Mark Spuria, general manager; Kaitlyn Mix, office manager; Kristyn Moore, sales specialist; and Heidi Derven, senior accountant. founded 1946. “We work best with instruments that have a Custom Instruments series of price-is-no-object, no-compro - great tradition,” he adds. “The mentality at Powell is the same mise flutes that are the choice of leading artists; the Conser - as the mentality at Buffet Crampon: We’re both never satisfied vatory line, a more “value-oriented” handmade instrument; the and always trying to make things better. It felt good working Signature line of intermediate professional flutes; and the hy - together from the very start.” brid Sonaré line, which has become a favorite among students At Powell, this quest for continual improvement is reflected as well as professional wind players who occasionally double in a long tradition of innovation. Although founder Verne Q. on flute. What has changed is the sales process. The special - Powell can’t claim to have invented the modern Boehm flute, ized team at Powell continues to handle sales of the Custom he and his successors can take credit for numerous improve - instruments, which often entails specifying dozens of key and ments. In 1928, he crafted the first 14-karat gold flute. A headjoint options to tailor an instrument to the needs of a single decade later, he made the first all-platinum flute. In 1974, Pow - musician. However, responsibility for the sales of Conserva - ell was the first company to introduce instruments based on tory and Sonaré instruments has been shifted to the Buffet the Cooper scale, which provides enhanced intonation and er - Crampon organization. Mark Spuria, Powell’s general manager gonomics, and in 1987 it introduced Aurumite, a proprietary and longstanding team member, says the new arrangement has gold and silver composite material with its own distinctive already had a positive impact. “Our instruments are being ex - tonal qualities. In 2002, the company pioneered the concept of posed to more potential buyers than ever before,” he says. “The a “hybrid” flute, combining Chinese-fabricated key work with benefits have been immediate.” a U.S.-made headjoint to deliver a superior value to aspiring Kloc began his career at the Mignot Oboe factory in France students. The resulting Sonaré line has since been widely before joining Rigoutat Oboes, where he learned the art of key copied. Powell even has the distinction of sending the first making and finishing. After a year working at a music store in flute into outer space. In 2011, NASA astronaut Cady Coleman the Grenoble area (Bertet Music), Kloc came back to Paris to took her Powell with her on a mission to the International work for Loree oboes and later was immersed in product de - Space Station. velopment at Buffet Crampon. He explains that the difference The Powell Flute line remains unchanged following the Buf - between a mediocre instrument and a superlative one often fet Crampon acquisition and includes the flagship Handmade comes down to a host of easily overlooked details. The small POWELL FLUTES Powell flutes are truly “handmade.” A team of 50 at the Maynard plant use hand tools to polish, finish, and fit all flute compo - nents, with the kind of care and precision associated with fine watchmaking. things really do count, he explains, and for that reason, Buffet than other musical instrument factories. The production Crampon management has taken a “light touch” approach with process begins in a caged raw materials storage area where the Powell production process. “This is not something that the 14-karat gold, sterling silver, or Aurumite that will become needs to be fixed,” he adds. “And there is probably more flute a flute is placed in felt-lined wooden trays to make “kits.” Be - making expertise in this building than anywhere else in the fore leaving the storage area, each piece of metal is weighed world.” to the last gram. At each stage of the manufacturing, the shav - Powell’s manufacturing operations occupy the top floor of a ings and leftover scraps are carefully collected from the fac - four-story, 130-year-old former textile mill located 20 miles tory floor and re-weighed. The plant manager carefully west of Boston in the town of Maynard. The evolution of the monitors the ratio of scrap to finished flutes to keep wastage mill building, which overlooks the scenic Assabet River, in to a minimum. These kinds of controls are required when the some ways reflects the convergence of tradition and technol - unprocessed raw materials for a single flute can cost upwards ogy in the Powell production process. In the 1890s, the mill of $10,000. housed water-powered wool looms but by 1990 had been gut - The flute making process starts in the body department with ted and converted into a computer factory for the Digital raw tubing. For Powell’s Custom handmade flutes, raised tone Equipment Company. There’s a similar contrast at Powell, holes are painstakingly soldered into place. For the Conserva - where computer-controlled metal shaping equipment is em - tory models, they are drawn. Once the holes are in place, ribs ployed alongside skilled craftspeople who shape the critical and posts are fitted and soldered to the body. From there, the tone hole with hand tools identical to those used by Verne Pow - body goes to a stringing operation where key assemblies are ell decades ago. The common thread that unites these diverse fitted to the posts. Final assembly involves installing pads, operations is an overriding concern with perfection. springs, and corks, and adjusting the action of the all the keys. From the careful handling of precious metal raw materials to Separately, in perhaps the most critical operation in the entire the fabrication of tiny key components, the Powell flute fac - process, skilled artisans shave small bits of silver, undercutting tory probably has more in common with a jewelry operation or overcutting the embouchure in the headjoint. It’s a time- POWELL FLUTES consuming process that can take up - wards of an hour for a single headjoint, but is critical to the performance of the finished instrument. At each step of the production process, craftspeople working with a magnifying lens and small chisels and scraping tools spend an inordinate amount of time re - moving small metal burrs and smooth - ing out nearly imperceptible imperfections. This extensive handwork is necessary to create a smoothly func - tioning key assembly. Just as impor - tantly, it gives each flute the elegance and beauty typically associated with a fine piece of jewelry. Kloc says, “The flute is the most unfor - giving of all wind instruments. There is Key sets and bodies move through the production process in felt-lined trays to avoid no give, the keys and pads either fit per - scratching. fectly or it won’t work at all.” This is why a craftsperson can spend as much as 20 minutes inserting paper shims of varying thicknesses under a pad to en - sure that it provides a perfect seal. At a minimum of $13,500 for a silver hand- made flute—gold models can run three times as much—a Powell flute is un - questionably expensive.
Details
-
File Typepdf
-
Upload Time-
-
Content LanguagesEnglish
-
Upload UserAnonymous/Not logged-in
-
File Pages6 Page
-
File Size-