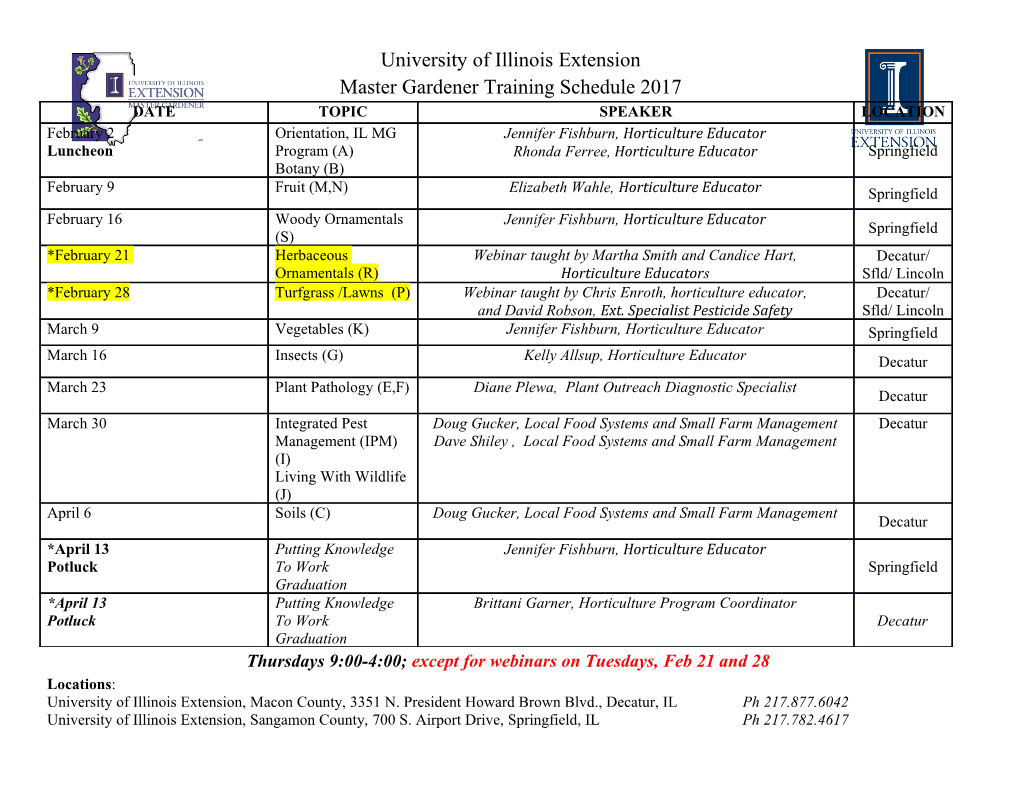
DRILLING DATA RECORDING Mobile Electronic Recording System and Drill-off Data Illustrating Its Use WARREN B. BROOKS MEMBER AIME SOCONY MOBIL OIL CO., INC. JAMES T. DEAN DALLAS, TEX. Downloaded from http://onepetro.org/JPT/article-pdf/15/01/11/2213667/spe-409-pa.pdf by guest on 24 September 2021 WILTON GRAVLEY Abstract Several mechanical and electrical recording systems for drilling variables are now available for rental or purchase. A mobile electronic system has been developed for These systems record from one to six variables. Accuracy, recording drilling variables. Continuous records have been sensitivity, reliability and durability vary considera?ly o.n made, during field tests, of drilling rate, weight on bit, these units. The oscillographic system described m thiS rotary rate, torque, fluid pressure and pump rate. Addi­ paper was designed for improved accuracy and sensitivity. tion~iiy, intermittent recordings have heen made of strains and accelerations in various pieces of drilling-rig equip­ The subject recording equipment has many uses. One ment, and longitudinal, torsional and bending stresses in frequent application has been the obtai~ing."of accur.ate the drill pipe. Transducers are placed on the rig for moni­ drill-off data. In many instances the Lubmski- calculatIOn uring the variables. Cahles connect the transducers through method for drill-off data is sufficiently accurate, However, circuits to an oscillograph. The major electronic compo­ in cases where severe buckling occurs during the drill-off nents of the equipment are housed in a trailer for protec­ or where the wall thickness of the drill pipe has changed tion and portability. due to wear or corrosion, this method can lead to con­ The electronic recording system facilitates taking accu­ siderable error. The technique described in this paper, rate drill-off data in the field. Data are presented on seven utilizing the recording sys:~m, eliminates these inaccuracies. drill-offs taken in San Andres dolomite in Andrews County, Tex., at a depth of about 5,020 ft. In the test interval, Description of the Recording System drilling rate was proportional to weight on hit and to rotary rate raised to the 0.6 power. The mobile monitoring system is durable and versatile. It was designed for use in the field or in the laboratory. Introduction Signals from strain-gauge, p8tentiometric and tachometer­ generator type transducers can be recorded. The frequ~ncy In the drilling research work conducted by Socony response and sensitivity of the circuits used for the vanous Mobil Oil Co., Inc., emphasis has been placed on a study measurements can be varied over wide ranges. of the factors affecting drilling rate, both with conventional In fabricating the circuitry and components, simplicity and new drilling devices. The effects of several inter­ was emphasized. This minimizes electronic problems result­ related variables. have been studied. These include drilling ing from transportation over rough terrain. Normally, sig­ rate, weight on bit, rotary rate, drill-string torque, drilling­ nals are recorded without the use of amplifiers, During fluid pressure and pump rate. early field tests the apparatus was housed in a converted In early field tests standard drilling-rig equipment was seismic-recording truck. The system was later installed in used in obtaining data. Because of the encouraging results a house trailer. This instrument trailer is shown on the obtained in these tests, an oscillographic recording system lower right in Fig. I, together with the I Y2 -ton truck used was fabricated. This mobile electronic recording equipment to transport the trailer. Hidden by the trailer is a portable has been used successfully in the field and in the Socony 5-kw AC generator utilized for power. Mobil Field Research Laboratory for four years. In addi­ Fig. 2 is a block diagram of the transducers, recorder tion 10 the mentioned variables, strains and accelerations and control equipment. Each transducer is connected to in the drill string and in various rig components have the control circuitry by a shielded four-conductor cable. been recorded and analyzed on several occasions. One such application occurred during Project Mohole, Phase 1. Fig. 3 shows the electronic equipment mounted in the Longitudinal, torsional and bending strains in the drill trailer. The oscillograph recorder is located on the table string were recorded while drilling in about 11,700 ft of at the left. The left relay rack contains an intercom system, water at the Guadalupe Island site.' control circuits for the transducers and a power supply. The right relay rack contains AC monitoring meters, a DC Original manuscript received in Society of Petroleum Engineers office voltmeter, an oscilloscope and a voltage regulator. Aug. 18. 1962. Revi,:;,ed manuscript received Dec. 6, 1962. Paper presented Recorde~ at 37th Annual Fall Meeting of SPE. Oct. 7-10, UJ62, in Los Angeles. lReferences givt:.:n at end of paper. The oscillograph recorder is a la-channel, general- JA:\I'ARY, 1963 SPE 409 11 purpose type. * A mercury-vapor lamp of high intensity TABLE l-VARIABLES RECORDED ON A DRILLING RIG AND TYPES OF TRANSDUCERS USED is used as the light source for the galvanometers. The Variable Recorded Type of Transducer recording paper is sensitive to ultra-violet light and devel­ Drilling rote Potentiometer ops under ordinary lighting without the use of fluids or Hook load (weight on bit) Strain-gauge pressure cell or stroj,n-gauge sub Rotary rate Tachometer-generator a dark room. Therefore, the record can be observed imme­ Torque Strain-gauge pressure ceJl or strain-gauge sub Fluid pressure Strain-gouge pressure cell diately and continuously. The records are not permanent; Pump rate Tachometer-generator however, they do not fade for a few weeks under fluores­ cent lighting. Permanent records are made by photostating or fixing (with a chemical solution) the original records Transducers at a later date. The types of transducers utilized for the six conven­ The paper drive on the recorder has eight different tional drilling variables are shown in Table 1. All of the speeds in increments between 1 ft/hr and 2 ft/sec. This transducers are connected and placed in operation without versatility permits recording high-frequency signals in any interruption of rig operation, with the exception of detail, and also makes possible recording signals con­ the torque transducer. The installation of this equipment tinuously for long periods of time. requires about one-half hour downtime on the rig. The frequency response of each trace depends on the Drilling Rate type of galvanometer and corresponding control circuit The drilling-rate transducer senses the linear displace­ used. The galvanometers have frequency responses ranging ment of the drilling cable on a sheave of the crown block from 24 to 2,000 cycles/sec. Galvanometer sensitivity (usually the "fast" sheave). The movement of the drilling Downloaded from http://onepetro.org/JPT/article-pdf/15/01/11/2213667/spe-409-pa.pdf by guest on 24 September 2021 varies inversely with frequency response. During most tests line is proportional to the movement of the traveling low-frequency, high-sensitivity galvanometers have been block. The transducer includes a wheel approximately 9 in. used. in diameter that is held against the cable on a sheave. Keyed to the wheel is a potentiometer. Movement of the "Heiland Model 906A Visicorder. cable on the sheave turns the wheel and the potentiom­ eter. The resistance change in the potentiometer is sensed by the control circuit and transmitted to the recorder. The signal recorded is proportional to displacement of the drilling line and the kelly. Since it is recorded vs time, the slope of the trace on the record is proportional to drilling rate or to other movement of the drill string. Hook Load (Weight on Bit) The hook load has been sensed by the following two methods. 1. Modified Commercial Unit-The hook load has been sensed by a strain-gauge type of pressure transducer in­ serted in a standard weight-indicator system. This standard system measures tension in the deadline (proportional to hook load) with a diaphragm unit on the deadline tie­ down. The diaphragm is connected to the weight-indicator gauge (a pressure gauge) by a liquid-filled line. A pressure transducer is connected to this line, thereby giving a signal proportional to hook load. Weight on bit is the difference between the hook-load values when the bit is just off­ bottom and Oil-bottom. 2. Strain Gauges Mounted on a Sub in the Drill String-The hook load (the reading is actually hook load Fig. I-Mobile electronic recording system on drilling rig. DRILLING RATE HOOK LOAD ROTARY RATE CONTROL TORQUE EQU IPMENT FLUID PRESSURE PUMP RATE IOTHER VARIABLES r · Fig. 2---'Block diagram of recording equipment. Fig. 3-Recording equipment inside the instrument trailer. 12 JOURNAL OF PETROLEUM :rECH!'iOLOGY minus the weight of the kelly and swivel) has been sensed wheel of the torque unit. The speed of the idler wheel IS during some studies by a strain-gauge bridge mounted on proportional to the rotation rate of the rotary table. a sub placed immediately below the kelly. A cable attached to the bridge enters the interior of the sub through a Torque special seal, traverses the interior of the kelly and then Torque has been sensed by the following two methods. returns through a seal to the outside above the kelly. The 1. Modified Commercial Unit-One torque transducer cable is connected to a set of slip rings. A separate cable is a modified Martin-Decker Hydro-Mech unit. The device connected to the brushes on the rings transmits the signal consists of an idler wheel which is forced against the tight to the oscillograph. This system has greater accuracy and side of the rotary drive chain.
Details
-
File Typepdf
-
Upload Time-
-
Content LanguagesEnglish
-
Upload UserAnonymous/Not logged-in
-
File Pages6 Page
-
File Size-