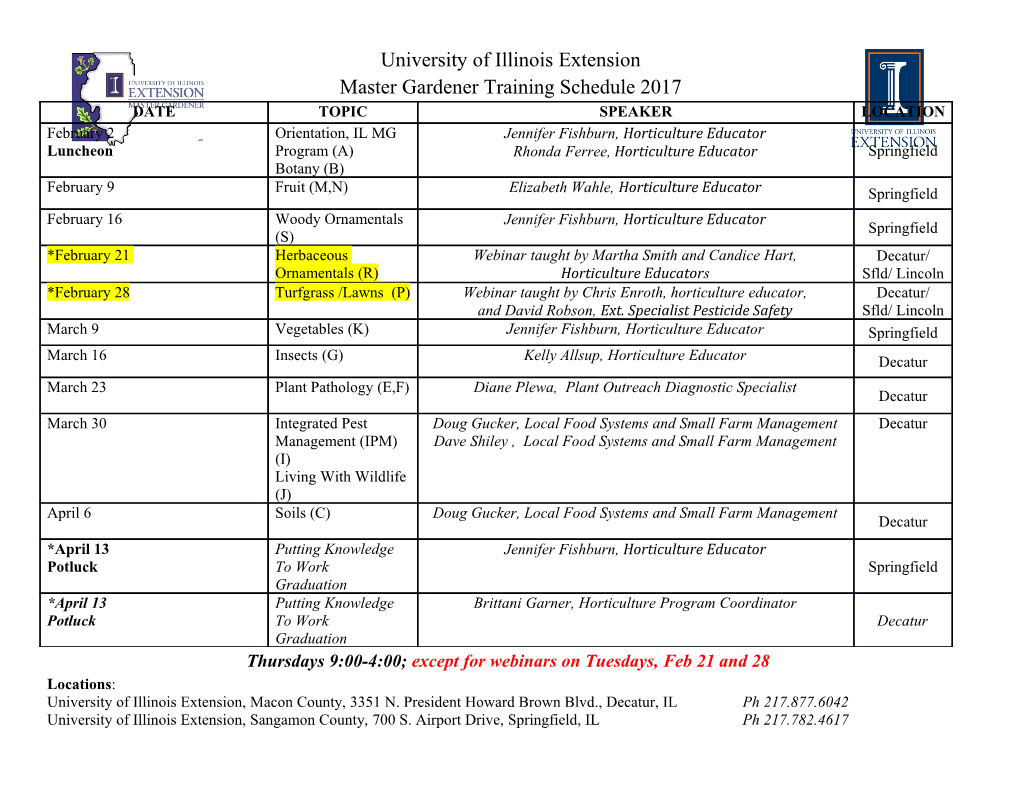
Journal of Power Sources 112 (2002) 130±136 Ultra-low leak rate of hybrid compressive mica seals for solid oxide fuel cells Yeong-Shyung Chou*, Jeffry W. Stevenson, Lawrence A. Chick Paci®c Northwest National Laboratories, Materials Resource Department, 902 Battelle Boulevard, P.O. Box 999, Richland, WA 99352, USA Received 15 May 2002; accepted 13 June 2002 Abstract A novel hybrid compressive mica seal was developed that showed a reduction of leak rate by about 4300 times (compared to simple mica seals) at 800 8C. The hybrid compressive mica seal is composed of 2 compliant glass layers and a mica layer. Three commercially available micas were tested in hybrid compressive seals for solid oxide fuel cell applications. The best results were obtained using Muscovite single crystal mica. The normalized leak rate for this seal at 800 8C was only 1:55 Â 10À4 sccm/cm at a stress of 100 psi and a pressure gradient of 2 psi. Seals based on the other commercial micas (Muscovite and Phlogopite mica papers), also exhibited superior leak rates (0.011 sccm/ cm) compared to simple mica seals without the compliant glass layer (about 6±9 sccm/cm). The microstructure of the mica was examined before and after the 800 8C leak tests using scanning electron microscopy. The cause for the substantial reduction of the leak rate was discussed. In addition, the effect of the compressive stresses was also investigated. # 2002 Elsevier Science B.V. All rights reserved. Keywords: Solid oxide fuel cells; Scanning electron microscopy; Coef®cient of thermal expansion 1. Introduction addition to the challenges in materials development for electrolytes, anodes, and cathodes, most planar SOFC Solid oxide fuel cells (SOFCs) are a new and fundamen- designs require seals between each individual cell to prevent tally different way of making electrical power from a variety (or at least suf®ciently minimize) leaking of gases from the of fuels. The SOFC is an energy conversion device that stack as well as mixing of fuel and oxidant gases. The seal produces electricity through the electrochemical reaction of needs to have long-term stability at the elevated tempera- a fuel (e.g. H2) and an oxidant (e.g. O2). Oxygen is trans- tures and harsh environments (oxidizing, reducing, and ported via the vacancy mechanism through a dense ceramic humid) typical of SOFCs during operation. Also, the seals electrolyte (e.g. fully stabilized zirconia), and then reacted should not cause degradation (e.g. corrosion) of the materi- with hydrogen electrochemically. Because the SOFC con- als with which they are in contact (e.g. stabilized zirconia, verts chemical energy without an intermediate thermal interconnect, and electrodes). Approaches, such as glass energy step, its conversion ef®ciency is not subject to the seals, glass±ceramic seals, cement seals, brazes, and com- Carnot limit. Compared to the conventional power genera- pressive seals have been proposed, though most of the work tion, SOFCs offer several advantages: substantially higher reported has focused on glass seals. Lahl et al. [5] studied energy conversion ef®ciency, modular construction, mini- aluminosilicate glass±ceramics as sealant in SOFC stacks. mal operating site restriction, and much lower air pollution They investigated 13 glasses and examined the chemical [1]. interactions at the interface between the sealant and the Currently, there are two basic designs for SOFC applica- SOFC component materials: anode, electrolyte and a metal- tions: tubular and planar [1±4]. While planar designs are lic interconnect. Guidelines for the sealant development believed to potentially offer lower cost and higher power were given. Yamamoto et al. [6] studied the compatibility density per unit volume compared to tubular designs, planar of mica glass±ceramics as gas-sealing materials for SOFC. designs face many challenges that must be overcome. In The mica glass±ceramics were found to be chemically stable to the electrolyte (8YSZ) in that no severe chemical reaction * Corresponding author. Tel.: 1-509-375-2527; fax: 1-509-375-2186. was found at the interface in the temperature range of about E-mail address: [email protected] (Y.-S. Chou). 1000±1300 8C. Other glass systems (B2O3, SiO2, and P2O5) 0378-7753/02/$ ± see front matter # 2002 Elsevier Science B.V. All rights reserved. PII: S 0378-7753(02)00356-7 Y.-S. Chou et al. / Journal of Power Sources 112 (2002) 130±136 131 have also been investigated as potential SOFC seals [7]. interlayers between the mica and the adjacent stack com- Glasses containing high B2O3 showed good results; however ponents. these glasses tend to exhibit extensive volatilization in the SOFC environment. P2O5-based glasses can be tailored to minimize the volatilization; however, the coef®cients of 2. Experimental thermal expansion are too low to match with the other stack components [8]. 2.1. Raw materials In comparison to the rigid glass seals, compressive seals potentially offer several advantages. Since they are not Three commercially available micas were investigated in rigidly bonded to the cells, the need for matching coef®cient this study. Two of them were mica paper: Muscovite paper of thermal expansion (CTE) of all stack components is and Phlogopite paper, each with a thickness of 100 mm. reduced or eliminated. The cells and interconnects are Those papers are composed of large mica ¯akes (<1 mm in allowed to expand and contract freely during thermal cycling diameter, 10 mm thick) and an organic binder. The third and operation, thereby, greatly reducing structural degrada- one is cleaved Muscovite single crystal sheet, also with a tion during thermal cycling and routine operation. Elimina- thickness of 100 mm (the cleaved Muscovite single crystal tion of the need for matching CTE greatly expands the list of sheet is transparent whereas the other two paper-forms are candidate interconnect materials, whether ceramic or metal- not). For the hybrid compressive seal tests, a borosilicate lic. The research in the area of the compressive seals is still glass ®lter paper was used as the compliant layers. The glass in its early stages and very little data is available. Kim and contains 58% SiO2, 9% B2O3, 11% Na2O, 6% Virkar [9] demonstrated the use of compressed mica in a Al2O3, 4% BaO, and ZnO, CaO and K2O. single-cell SOFC set-up; however, the effectiveness was not discussed. Simner and Stevenson [10] studied the compres- 2.2. Leak test sive mica seals for SOFC applications. They examined micas in paper form as well as the cleaved single crystal Mica samples were cut into 1.5 square inches with a 1/2 in. form. The results showed the cleaved natural mica sheets diameter central hole. The mica squares were then pressed were far superior compared to mica papers; for the mica between an Inconel tube (outer diameter 1:3in.andinner sheets, leak rates about 0.33±0.65 sccm/cm at 800 8C and diameter 1:0 in.) and a dense alumina substrate. For hybrid 100 psi were measured on small test coupons. Though, the compressive seals, two extra glass interlayers were placed allowable leak rates for SOFC stacks at elevated temperature between the Inconel tube/mica and mica/alumina interfaces. remains to be determined, a coupon leak rate of 0.33± For comparison, a test of a glass-only seal was also conducted 0.65 sccm/cm is likely to translate to unacceptably high using a single layer of glass without the mica sheet. Samples leak rates for actual stacks, in which multiple, full size were heated in a clamshell furnace at a heating rate about 2 8C/ components would be stacked together with the mica gas- minto8008C. The load was applied using a universal kets between each component. In this paper, we present a mechanical tester with a constant load control (Model novel hybrid compressive mica-based seal in which the leak 5581, Instron, Canton, MA). The experimental setup is shown rate can be reduced 4300 times by simply adding the glass schematically as in Fig. 1. A large known-volume (370 cm3) Fig. 1. Schematic showing (A) the experimental setup for the leak test and (B) a detail of the hybrid seal test. 132 Y.-S. Chou et al. / Journal of Power Sources 112 (2002) 130±136 reservoir was kept at ambient conditions and connected to the support substrate and the Inconel tube as the top pressing sample via a 1/8 in. Cu tube. By setting up a vacuum in the ram, Fig. 2), it was evident that many defects were present, system (initially as low as 100 mtorr), the leak rate was including long grooves on the metal and the irregular measured by monitoring the pressure change with time. The grooves (voids) on the ceramic substrate. Therefore, it ®nal pressure was about 2 torr. The pressure gradient across seemed likely that the major leaks for the compressive mica the seal therefore, could be considered to be essentially seal occurred through these interfaces. As a result, a constant at 14.7 psi. Assuming the ideal gas law, the leak rate ``hybrid'' compressive seal concept, in which a compliant (L) was calculated by the equation: glass interlayer is placed between the mica/component interfaces (to ®ll or block the surface defects), was devel- Dn n À n p À p V L f i f i oped. The concepts are shown schematically in Fig. 3. The Dt tf À ti RT tf À ti results are reported and discussed in the following sections. where n is the moles of the gas, T the temperature, V the reservoir volume, R the gas constant, t the time, and p the 3.2. Raw materials characterization pressure. Subscripts f and i represent the ®nal and the initial conditions.
Details
-
File Typepdf
-
Upload Time-
-
Content LanguagesEnglish
-
Upload UserAnonymous/Not logged-in
-
File Pages7 Page
-
File Size-