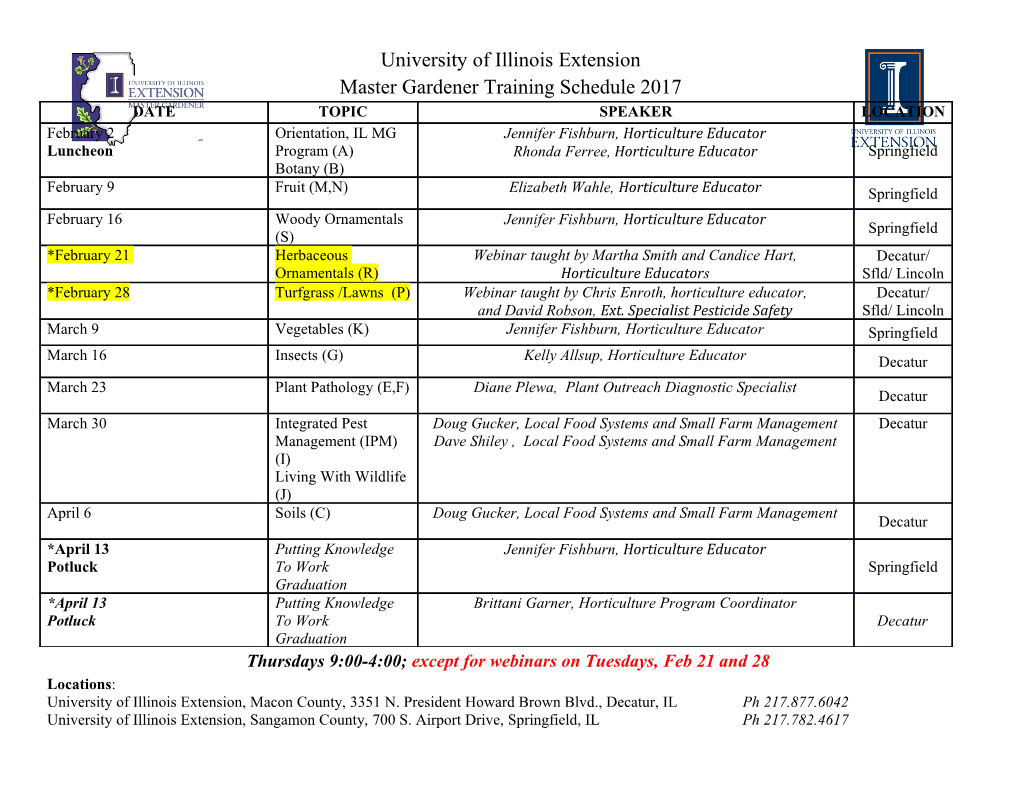
Sevil Yeşilpınar Analysis of the Performance of Sewing Dokuz Eylul University Threads Manufactured from Conventional Department of Textile Engineering 35100 Bornova, İzmir, Turkey E-mail: [email protected] and Compact Ring-spun Yarns Abstract The compact spinning system produces a yarn structure which is different from the structure of conventional spun yarn as the result of the elimination of the spinning triangle. New perspectives introduced by compact spinning have proved their worth in all textile processes, from yarn production to the finishing stages. In this study, the seam strengths of sewing threads produced by conventional and compact spun-ring systems were investigated together with strength tests before and after washing. The results were evaluated with SPSS software. It was found out that the difference between the seam strength of sewing threads produced from conventional ring and compact yarns were not of major statistical significance, and nor was the difference in seem strength before and after washing. Additionally, the effect of the gassing process on compact sewing threads was established. The results allow us to recommende that the gassing process should not be applied to sewing threads made of compact yarns. Key words: seam strength, compact yarn, sewing thread, gassing. distinctive features of compact yarns. In the compact spinning system, elimi- The basic alteration in the compact spin- nating the spinning triangle almost en- ning system, which is the modified form tirely in the yarn formation zone allows of the ring spinning system, is that the even very short fibres to contribute to drawing system of compact spinning ma- strength in this zone where fibres have chine finishes with a condensation zone no twist. In this way, the spinning ten- formed with the aid of air suction. In this sion existing in this zone is received by way, the spinning triangle is eliminated, all fibres. Thus breakages during yarn which is at the same time the strongest production decrease, and therefore the and weakest feature of ring spinning spinning stability increases [9]. with regard to other systems; thus a better orientation of fibres in the yarn When working with compact yarns, the is achieved. Various machine suppliers size amount necessary for warp prepa- use different designs of the condensation ration or weaving performance can be zone as a result of the elimination of the decreased by 50% in comparison to spinning triangle [1- 3]. ring yarns with the same properties [5, 9 - 11]. A decrease in size amount as a The first advantage that comes to mind result of the usage of compact yarns also with the usage of compact spinning decreases the cost of the desizing proc- system is the decrease in raw material ess, besides the cost advantage achieved costs. The utilisation ratio of fibre fe- in the sizing process [5]. atures of compact yarns is higher than conventional ring yarns from the view- A high performance of compact yarns on point of important yarn features such as weaving and knitting machines is very strength and hairiness. When producers important for more economic production consider profiting from raw material’s of woven and knitted fabrics. Compact cost advantage without aiming to inc- yarns, which have high strength and rease the yarn quality, it is possible to low hairiness, cause fewer fibre flys achieve such a cost advantage by using and yarn breakages. In this way, weav- low-quality raw material [4]. ing and knitting machines can be kept clean. Compact yarns enable the finished It is possible to produce compact yarns textile products to have higher strength, n Introduction with the same strength as the ring yarns a brighter appearance and better handle. by decreasing the twist amount by The tendency to pill decreases as a result The compact spinning system produces 20-25%, because of the high utilisation of much lower hairiness [12, 13]. a yarn structure which is different from ratio of the fibre features of compact the structure of yarn spun by the conven- yarns [5-8]. Decreasing the twist amount New perspectives introduced by compact tional spinning system yarn structure as allows the production of yarns with the spinning have proved their worth in all a result of the elimination of the spin- same strength as ring yarns with softer textile processes from yarn production ning triangle. High strength, decreased handle, and also directly increases the until the finishing stage. However, the hairiness and high elongation values are yarn production speed [5]. use of compact yarns as sewing threads 20 FIBRES & TEXTILES in Eastern Europe April / Juni 2006, Vol. 14, No. 2 (56) FIBRES & TEXTILES in Eastern Europe April / Juni 2006, Vol. 14, No. 2 (56) 21 has not been encountered in the literature noted to determine the effect of the gas- The significant level α was taken as 0.05 we have investigated. The purpose of this sing process on the sewing threads made for these evaluations. The variance analy- study is to investigate and compare the of compact yarns. A Juki DDL-8500-7 sis results of seam strengths of fabrics cut performances of sewing threads as pro- electronic lock stitch machine was used in the warp and weft directions are given duced by conventional ring and compact as the sewing machine. A circular fabric in Tables 3 and 4 respectively. When yarns. In this study, seam strengths of band of 25 cm width and 1.5 m length Tables 3 and 4 are examined, the seam sewing threads produced by both meth- was prepared on the machine. Yarn strength results in the warp and weft di- ods will be measured, and the difference breakages were noted as 20 m of fabric rections are seen to be in agreement with in seam strengths will be statistically was sewn at 4500 needle penetrations each other. In the factorial experiments analysed. The effect of the washing proc- per minute. 50 repetitions were made for (3×3), the difference in the seam strengths ess on the seam strength will also be ob- each type of sewing thread. The results of stitch types was found to be statistically served. Another purpose of this research obtained were evaluated on a computer important, whereas the difference in the is to determine the effect of the gassing with the aid of SPSS software. seam strengths of different sewing thread process on the sewing thread made of types was insignificant. It is well-known compact yarns. n Results that the seam strength changes according to the stitching type [16, 17]. The goal of n Material and method The test results of seam strength deter- this study is to determine the effect of the mined for three different types of sewing sewing threads produced by conventio- In this research, Giza 70 type cotton was thread and three different types of stitch nal ring and compact yarns on the seam used as the raw material for the sewing are given in Table 2. Each seam strength strength. According to the results of the thread. Single ply yarn was produced average consists of five repetition values. variance analysis, the difference in the from the cotton according to convention- The seam strength values were statistically seam strengths of sewing threads made al ring and compact spinning systems. evaluated with the aid of SPSS software. of conventional ring and compact yarns Then, the single ply yarn was shaped into sewing thread by passing it through the Table 1. Test results of sewing threads production methods used in various production production steps (rewinding-doubling- stages. twisting-gassing-mercerising-bleaching- dyeing-finishing) of a sewing thread. In Single ply After twisting Sewing cone Compact order to observe the effect of the gassing Parameter Conven- Conven- Conven- Compact Compact Compact without tional ring tional ring tional ring gassed process, half of the sewing thread pro- gassing duced from compact yarns was subjected Yarn count(tex) 15 15 45 45 45 45 45 to this process. The test results obtained Cotton type Giza 70 Giza 70 Giza 70 Giza 70 Giza 70 Giza 70 Giza 70 during production of the sewing thread Size CV% 0.52 1.20 0.94 0.31 0.95 0.33 0.32 used in this research are given in Table 1. Twist S/Z, t/m 996 S 1020 S 729 Z 711 Z The right fabric for the count of the sew- Force, cN 364 363 1275 1202 1492 1446 1434 ing thread was selected to investigate the Force CV, % 7.47 6.91 3.27 4.54 5.12 5.98 4.58 seam strength of the sewing thread pro- Tenacity, cN/Tex 24.33 24.84 27.85 26.87 35.78 35.44 34.14 duced. For this purpose, we used trouser Elongation, % 4.90 5.66 6.94 7.29 4.83 5.03 4.75 fabric with a mixture of 50% viscose and CV, % 11.57 11.01 6.45 6.22 6.29 6.12 4.61 2 50% polyester, and 245 g/m in weight. Thin-%50 0 0 0 0 The seam strength test was performed on Thick+%50 9 9 0 0 an Instron 4411 device according to the Neps+%200 48 21 1 1 ISO 13935-2 standard [14]. The speed of S3 hairiness 2793 600 165 33 20.33 5.83 190 the device was 100 mm/min. Samples were Hairiness index 1070 217 39 5 6.33 0.5 66 cut to the dimensions of 100 ×150 mm. Two samples were sewn together on the short side by putting one right above the Table 2. Seam strength test results.
Details
-
File Typepdf
-
Upload Time-
-
Content LanguagesEnglish
-
Upload UserAnonymous/Not logged-in
-
File Pages4 Page
-
File Size-