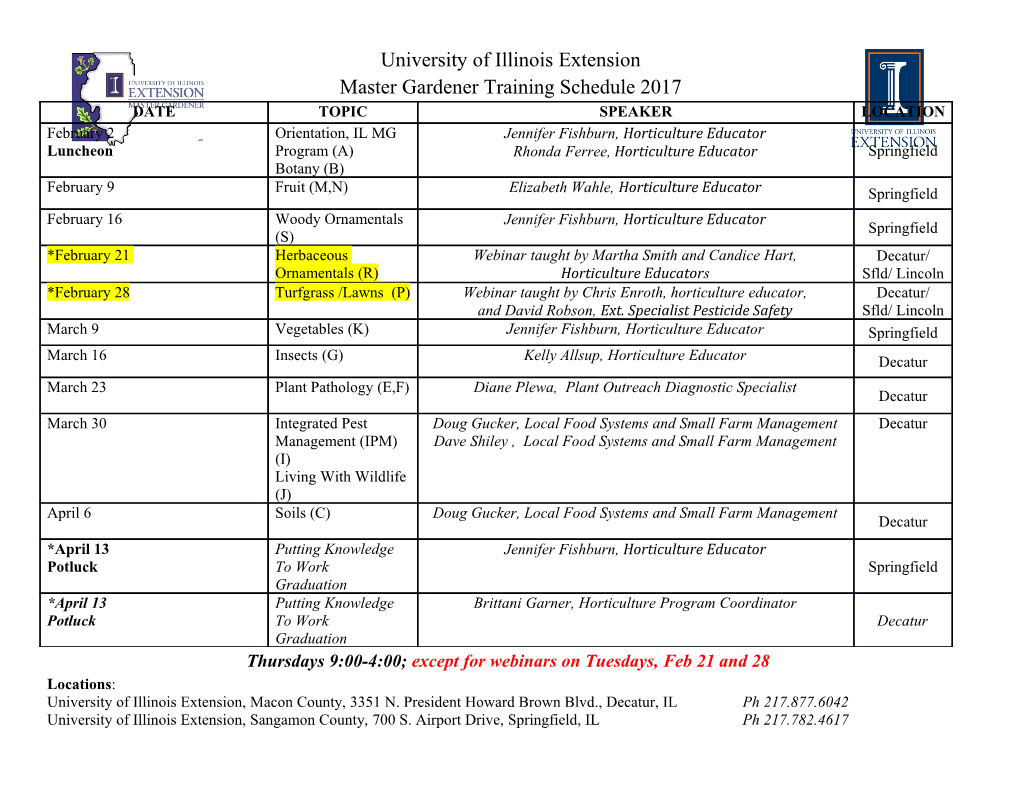
28 West Yorkshire: 1500-1830 Iron and coal Iron wrought-iron, was the result. There is documentary evidence for the existence of an iron In the Middle Ages the iron industry, in common with industry in West Yorkshire by the twelfth century, although other craft industries, was not particularly capital intensive, it is certain that ironstone was being extracted and smelted most extracting and smelting operations being carried out long before then. 1 In the Middle Ages the ore, which occurs on a limited scale. This situation was encouraged by the fact in quantity in the shales of both the Millstone Grit and the that most licences for mining and smelting were, because of Coal Measures, was mined where it outcropped. The usual the destructive effects of the industry on both the land method of extraction was the digging of bell pits. Essentially surface and woods, of a short duration. small scale workings, each bell pit employed only a handful As a result of the nature of the industry in this period it of men, the ironstone being obtained by the miners first was possible for individuals to take out the necessary licence sinking a shaft to the ore-bearing level, and then working and work on their own account. There are also, however, a outwards from the base of the shaft in every direction until number of examples of entrepreneurs who employed the roof of the workings was judged to be no longer safe. miners, charcoal burners, and smiths to work on their When that point was reached the pit would be abandoned behalf. The best documented case of entrepreneurial and back-filled, the latter frequently being one of the involvement in the medieval iron industry of West conditions upon which the mining lease was granted. Fields Yorkshire is that of John Culpon of Sowerby. In the early of these ironstone bell pits can still be seen in a number of fourteenth century Culpon engaged smiths to work iron at a places in West Yorkshire, the best examples being those at number of sites scattered over central and western areas of Bentley Grange and Emley Woodhouse (both in Emley) the manor ofWakefield. 2 (see Pls 13, 14). This method of mining was still being practised in the late sixteenth century, the period from Probably the most important single group to have been which the Emley Woodhouse workings date, and probably involved in the iron industry of the county during the later. Middle Ages were the monks of the Cistercian order. In the twelfth century a number of Cistercian monastic houses Ore was also extracted from the ground by means of adit were founded in the north of England; four of these, Byland and gallery mines. In the former type of mine a tunnel was Abbey, Fountains Abbey, Kirkstall Abbey and Rievaulx driven into the side of a hill at the point at which the ore Abbey, were, before the end of the century, directly outcropped, whilst in the latter a shaft was sunk and tunnels involved in the iron industry of West Yorkshire. then excavated outwards from its base. In the fourteenth century the monks of these abbeys Ironstone was mined wherever it occurred irrespective of ceased to work the iron on their granges and, instead, began existing land use, whether in woodland, common, or open to grant leases for mining and smelting to private field. Once the ore had been brought to the surface it was individuals. Among those who took advantage of the transported to the site of the smelting furnaces, these being available leases was Matthew Wentworth of Bretton Hall. usually located as near to the mine workings as possible. In 1503 Monk Bretton Priory granted him a lease to mine The fuel for the reduction process was charcoal, the wood ironstone for his smithies (furnaces) at West Bretton. from which it was made being cut and burnt by gangs of charcoal burners or 'colliers'. With the dissolution of the larger religious houses in 1539 The simple furnaces, or 'bloomeries', in which the ore monastic interests in the iron industry of West Yorkshire was reduced were constructed of fire-resistant clay, or came to an end. The sale of the lands previously held by the stones bonded with clay. These were charged with charcoal Cistercian abbeys resulted in the valuable mineral rights and iron ore, fired, and the temperature within raised to the passing completely into private hands, often those of the required level by use of hand- or foot-operated bellows. local gentry. These men, in their turn, often seem to have After a number of hours, when the ore was judged to be been content to lease sites rather than work them reduced, the furnace was broken open and a piece of iron themselves. removed. This was then reheated and beaten with hammers The Middle Ages witnessed the introduction of to remove slag and consolidate the metal. The finished technological innovations which not only were to increase product, kn::>wn as a 'bloom', was wrought-iron. the efficiency and the capacity of the industry, but also to Occasionally, if the furnace became too hot, the iron took change completely its character. One of the first of these too much carbon from the charcoal; cast-iron, a product for was the application of mechancial power to the working of which the medieval iron industry had little use, rather than forge hammers and furnace bellows, the source of power, as Iron and coal 29 Plate 13. Bell pits, Bentley Grange, Emley in the case of the textile industry of the period, being The blast furnace was a larger and more permanent provided by water. The first known reference to a structure than the bloomery, and, unlike the bloomery mechanically operated forge hammer in England is to one which was broken open after each firing, the smelting located in Warley township in West Yorkshire. This process was a continuous one, charcoal, ironstone and hammer, or 'oliver' as it was referred to, was already in use limestone being fed in at the top, and molten slag and iron by 1349/50. 3 tapped out at the bottom. The volume of air required to provide an effective blast for furnaces of this size could only The next and most important single development in the be provided by a mechanical power source, which until the history of the iron industry was the invention of the blast eighteenth century meant water. This reliance upon water furnace. The blast furnace, first used in Flanders in the late power restricted the location of furnaces, as it did woollen fourteenth century, seems to have been introduced into the mills, to those sites where an adequate supply of water was south of England in the fifteenth century. available. Plate 14. Bell pit, Bentley Grange, Emley 30 West Yorkshire: 1500-1830 The introduction of the blast furnace made possible a Yorkshire) in 1650. Through marriage and settlements John considerable increase in the industry's output of iron. Even became part owner of the furnace; subsequently his son and the earliest of these furnaces were capable of producing a grandson, through both marriage and business ton of iron every twenty-four hours of the period of time partnerships, acquired interests in a number of furnaces and they remained in blast. The traditional bloomeries, on the forges in both West and South Yorkshire. other hand, usually produced 'blooms' weighing no more In 1696 John Spencer and. his partner Thomas Dicken than a few pounds, and also had the added disadvantage of entered into an agreement with a group of iron masters from having to be rebuilt after each firing. Cheshire, Nottinghamshire and South Yorkshire 'for the better and more profitable working and managing the· several furnaces and smithyes in their or any of their []Possession] ... ' these to be' ... held used wrought and enjoyed in partnership amongst the said parties'. 5 Between them the members of the partnership owned or had interests in: the several ffurnaces and smithyes with the Dam Goites sluices and appurties thereunto belonging called Chappell ffurnace Rockley ffurnace Barnby ffurnace Upper bank ffurnace Nether bank ffurnace and Stainbrough smithyes all in the said County of York.6 Of the furnaces mentioned in the agreement only two were in West Yorkshire, those at Nether and Upper Bank (Midgley in Shitlington), both of which were owned by Spencer and Dicken. The furnaces, located close to the site of Byland Abbey's monastic ironworking grange at Bentley, are now only commemorated by the name Furnace Hill. Plate 15. Bretton furnace watercourse Other ironworking sites were later brought into partnership, these including forges at Colnebridge and Another important difference between the bloomery and Kirks tall (both monastic foundations) and a blast furnace at the blast furnace was that whereas the former produced West Bretton. The watercourse and spoil heaps of Bretton directly-reduced wrought iron, the latter could only furnace are still visible, these constituting the only surviving produce cast iron. Because there were still few uses to which remains of a charcoal blast furnace in West Yorkshire (see cast-iron could be put, a secondary process was necessary to Pl. 15). convert it into wrought-iron. In order to do this the cast-iron By bringing together both furnaces and forges in a single was reheated in a finery until molten and stirred with a bar working partnership a degree of vertical integration was whilst a blast of air was played over its surface; the oxygen in achieved which, theoretically at least, benefitted all the the blast combined with carbon in the iron and gradually parties concerned.
Details
-
File Typepdf
-
Upload Time-
-
Content LanguagesEnglish
-
Upload UserAnonymous/Not logged-in
-
File Pages9 Page
-
File Size-