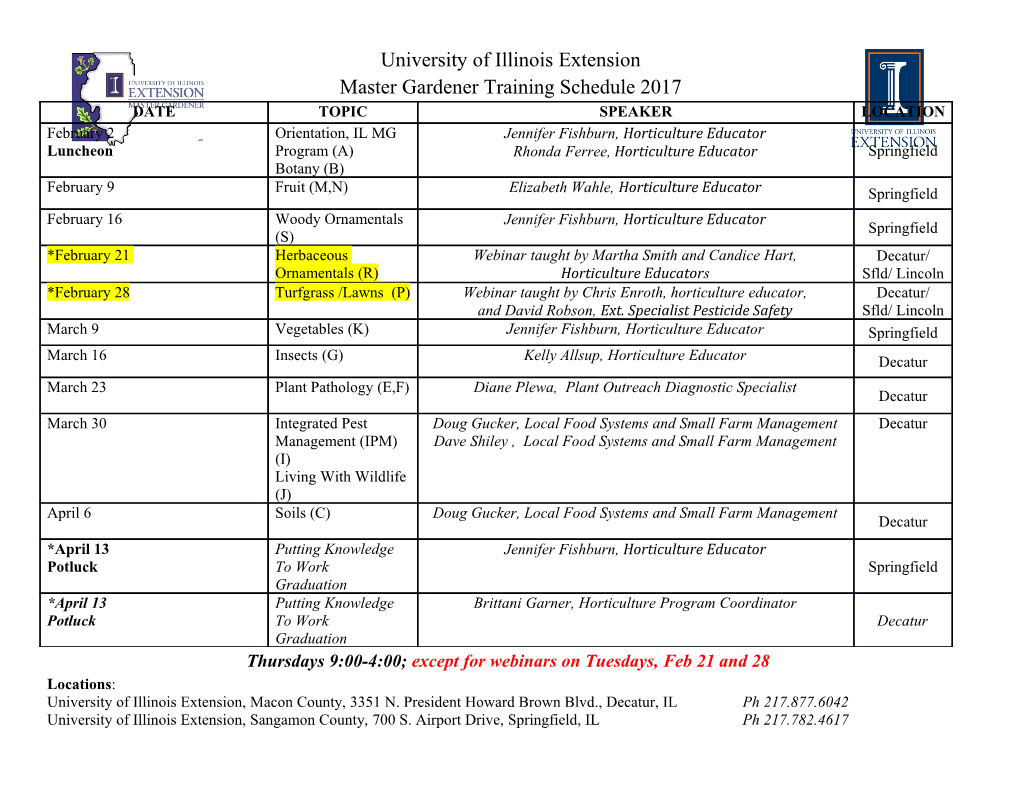
minerals Article Concentration of Rare Earth Elements (Sc, Y, La, Ce, Nd, Sm) in Bauxite Residue (Red Mud) Obtained by Water and Alkali Leaching of Bauxite Sintering Dust Leonid Chaikin 1, Andrei Shoppert 1,*, Dmitry Valeev 2,3 , Irina Loginova 1 and Julia Napol’skikh 1 1 Department of Non-Ferrous Metals Metallurgy, Ural Federal University Named after the First President of Russia B.N. Yeltsin, 620002 Yekaterinburg, Russia; [email protected] (L.C.); [email protected] (I.L.); [email protected] (J.N.) 2 Laboratory of New Metallurgical Processes (#24), A.A. Baikov Institute of Metallurgy and Materials Science, Russian Academy of Sciences, 49, Leninsky Prospect, 119334 Moscow, Russia; [email protected] 3 Scientific Research Centre “Thermochemistry of Materials”, National University of Science & Technology “MISIS”, 4, Leninsky Prospect, 119049 Moscow, Russia * Correspondence: [email protected]; Tel.: +7-922-024-3963 Received: 31 March 2020; Accepted: 28 May 2020; Published: 30 May 2020 Abstract: One of the potential sources of rare-earth elements (REE) is the industrial waste known as red mud (bauxite residue), in which the majority of REE from the initial bauxite are concentrated via the Bayer process. Therefore, the studies of the subject, both in Russia and outside, focus almost exclusively on red mud processing. This article looks into the possibility of REE concentration into red mud by leaching an intermediate product of the bauxite sintering process at Russian alumina refineries, namely electrostatic precipitator (ESP) dust. The experimental works were performed by X-ray diffraction (XRD)and electron probe microanalysis (EPMA) of the sinter and sinter dust. The determination of major and rare-earth elements in the sinter from the rotary kilns and in the ESP dust before and after leaching was carried out by X-ray fluorescence (XRF) and plasma mass spectrometry (ICP-MS). The study showed that it is possible to obtain red mud that contains three times more REE than traditional waste red mud after two-stage leaching ESP dust in the water at 95 ◦C followed by leaching in an alkaline-aluminate liquor at 240 ◦C. The shrinking core model was used to study the kinetics of leaching of the original ESP dust and water-treated dust in alkaline-aluminate liquor. The study showed the change in the limiting stage of the alkaline leaching process after water treatment, with the activation energy growing from 24.98 to 33.19 kJ/mol. Keywords: rare-earth elements; scandium; alumina production; sinter processes; red mud; electrostatic precipitation dust; alkali leaching; kinetics 1. Introduction The volumes of production/consumption of rare and rare-earth metals, which are critical for modern industries, are steadily increasing [1–4]. In this group of metals—scandium, yttrium, lanthanum, and lanthanides—scandium is the most scarce and commercially attractive one. The increased interest in scandium is associated with its application in various industries [5–7]. Small amounts of scandium are found in ores of aluminum, cobalt, iron, molybdenum, nickel, phosphate, titanium, tungsten, uranium, and others [8–16]. At the moment, phosphogypsum—waste from the processing of apatite concentrates [17,18]—and red mud (bauxite residue) are considered to be the most promising sources of scandium [19–24]. Phosphogypsum is also considered to be the most promising source of other rare earth metals [6], Minerals 2020, 10, 500; doi:10.3390/min10060500 www.mdpi.com/journal/minerals Minerals 2020, 10, 500 2 of 13 Minerals 2020, 10, x FOR PEER REVIEW 2 of 14 astons. it mayHowever, contain despite up to the 1% large of rare number earth of elements works devoted in total to [25 the]. processing More than of 250 phosphogypsum, million tons of phosphogypsumthere is still no hascommercially been accumulated viable technology in Russia [26 for] with its anprocessing annual increase [27], which by over is 14 explained million tons. by However,isomorphic despite co-crystallization the large number of REE of with works gypsum, devoted and to thetherefore processing the need of phosphogypsum, for its complete thererelease is still[28]. no commercially viable technology for its processing [27], which is explained by isomorphic co-crystallizationBauxite residue of REE generated with gypsum, in the and recovery therefore and the needprocessing for its complete of bauxites release is [28a ].source of environmentalBauxite residue pollution generated [29,30] in theon recoverythe one hand and processing and a promising of bauxites object is a sourcefor obtaining of environmental valuable pollutionelements [31] [29, 30on] the on theother one hand. hand Bauxite and a residue promising contains object a forhigh obtaining amount of valuable scandium elements (70–260 [31 ppm)] on thethat otheris close hand. to its Bauxiteprimary residueresources contains [32]. Large a high amounts amount of this of scandium waste form (70–260 what may ppm) be thatcalled is man- close tomade its primarydeposits, resourceswhich can [ 32be]. recycl Largeed amountsinto building of this materials, waste form pigm whatents, coagulants may be called for wastewater man-made deposits,treatment, which and which can be can recycled be used into to building re-extract materials, alumina, pigments, extract iron coagulants concentrates, for wastewater titanium, treatment, rare and andrare whichearth metals can be [33–35]. used to In re-extract the industrial alumina, production extract iron of alumina, concentrates, almost titanium, all Sc is concentrated rare and rare in earth red metalsmud. According [33–35]. Into theavailable industrial estimates, production the global of alumina, reserves almostof scandium all Sc in is the concentrated industrial waste in red range mud. Accordingfrom 1 to 3 to million available tons, estimates, with 70–80% the global of it reservesbeing contained of scandium in bauxite in the industrialprocessing waste waste range [36]. from The 1full to 3processing million tons, of the with bauxite 70–80% residue of it being currently contained genera in bauxiteted makes processing it possible waste to [extract36]. The 6600–20,400 full processing t of ofscandium the bauxite per residueyear. Therefore, currently a generatedlarge number makes of stud it possibleies have to been extract dedicated 6600–20,400 to the t recovery of scandium of rare- per year.earth Therefore,metals from a largevarious number types ofof studiesbauxite have residue been [37] dedicated obtained to by the processing recovery ofvarious rare-earth bauxites metals in fromthe Bayer various method types and of bauxite its variations. residue [However,37] obtained the by low processing content of various scandium bauxites in the in red the mud, Bayer the method high andcontent its variations. of alkali and However, alkaline the earth low metals, content and of scandium the simultaneous in the red recovery mud, the of high iron content together of alkaliwith REE and alkaline[38] or low earth extraction metals, efficiency and the simultaneous [39,40] render recovery the existing of iron methods together for with extracting REE [38 scandium] or low extraction from this etypefficiency of industrial [39,40] renderwaste non-viable. the existing methods for extracting scandium from this type of industrial wasteIt non-viable.should be noted that most studies of the separation of REE from alumina products have focusedIt should on the be processing noted that of most red studiesmud. In of this the article, separation we made of REE an from attempt alumina to study products the possibility have focused of onobtaining the processing the REE of concentrate red mud. In from this article,electrostatic we made precipitator an attempt (ESP) to study dust, the which possibility is an intermediate of obtaining theproduct REE concentrateof kiln sintering from electrostaticin alumina precipitatorproduction. (ESP)The dust dust, is which generated is an intermediatein a rotary kiln product (Figure of kiln 1), sinteringwhere low-quality in alumina bauxite production. (the mass The ratio dust of is Al generated2O3 to SiO in2 a(silicon rotary modulus) kiln (Figure is 1less), where than 7) low-quality is sintered with soda ash in order to convert the alumina-containing mineral into a water-soluble sodium bauxite (the mass ratio of Al2O3 to SiO2 (silicon modulus) is less than 7) is sintered with soda ash in orderaluminate. to convert Iron and the silicon-containing alumina-containing minerals mineral reac intot similarly a water-soluble with soda sodium to form aluminate. ferrite and Iron sodium and silicon-containingsilicate, respectively. minerals The technological react similarly process, with sodaespecially to form at ferritethe drying and sodiumand decarbonization silicate, respectively. stages, Thegenerates technological a large number process, of especiallyfine particles at theless dryingthan 100 and μm decarbonization (25–40% of the charge), stages, generateswhich are acarried large numberaway with of finethe exhaust particles gases. less than To clean 100 µ them (25–40% exhaust ofgases the charge),of kilns from which dust are particles, carried away a three-stage with the exhaustcapture gases.system To is cleanused. the The exhaust first stage gases is of kilnsthe dust from chamber dust particles, where amost three-stage coarse capture dust particles system isprecipitate; used. The the first second stage stage is the is dust cyclones, chamber where where medium most coarsedust particles dust particles are removed precipitate; from the the exhaust second stagegases isthrough cyclones, vortex where separation; medium dust and particles the final are stag removede is electrostatic from the exhaust precipitator. gases throughThe last vortex stage separation;captures the and finest the finalparticle stage fraction is electrostatic (less than precipitator. 20 μm) using The the last force stage of captures an induced the finest electrostatic particle fractioncharge. (less than 20 µm) using the force of an induced electrostatic charge. Figure 1. Flow chart of the sintering process on the RUSAL-Kamensk-Uralsky alumina refinery. Figure 1. Flow chart of the sintering process on the RUSAL-Kamensk-Uralsky alumina refinery.
Details
-
File Typepdf
-
Upload Time-
-
Content LanguagesEnglish
-
Upload UserAnonymous/Not logged-in
-
File Pages13 Page
-
File Size-