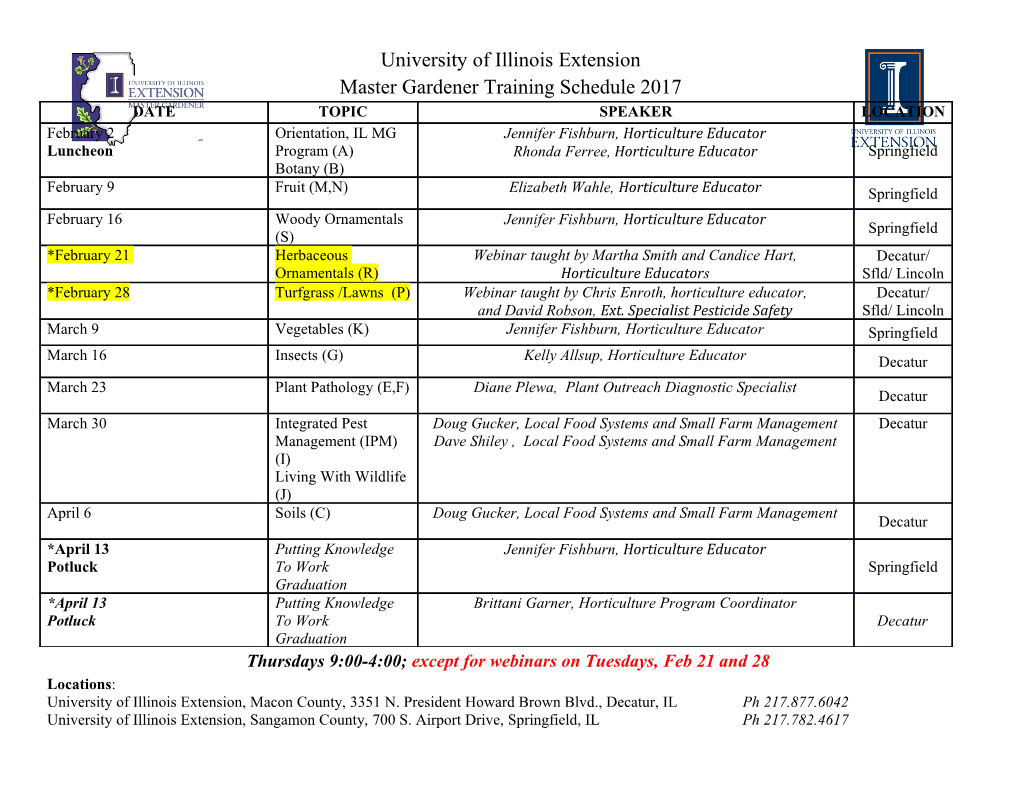
Reflections From Lean Leaders Transcripts from Podcast Interviews with Authors and Thought Leaders Mark Graban This book is for sale at http://leanpub.com/leanpodcast This version was published on 2019-02-18 This is a Leanpub book. Leanpub empowers authors and publishers with the Lean Publishing process. Lean Publishing is the act of publishing an in-progress ebook using lightweight tools and many iterations to get reader feedback, pivot until you have the right book and build traction once you do. © 2006-2019 Mark Graban Tweet This Book! Please help Mark Graban by spreading the word about this book on Twitter! The suggested tweet for this book is: I just bought ”Reflections from #Lean Leaders” by @MarkGraban Also By Mark Graban Best of Lean Blog 2011 Best of Lean Blog 2012 Lean Blog: Sports Measures of Success Practicing Lean Lean Veterinary Practice Management Thanks to all of the amazing guests who have joined me on my podcast since 2006, including Norman Bodek, who shared the idea to do “a radio broadcast” about Lean and Kaizen. Thanks to all who have shared with me and my audience. Contents Introduction - Sample Edition ................. i Podcast #1: Norman Bodek on Kaizen and Continuous Improvement ......................... 1 Podcast #142: Eric Ries on Taiichi Ohno & The Lean Startup 16 Thanks for reading the sample! ................ 22 Updates of the book over time . 22 Introduction - Sample Edition Thank you reading these LeanBlog Podcast transcripts. To listen to all podcasts and for more information about subscribing, please visit [www.LeanCast.org] (http://www.leancast.org). Please visit my websites: • LeanBlog.org¹ • MarkGraban.com² You can follow me on Twitter as @MarkGraban³. This was put together with a combination of computer transcript with a bit of review and editing by me, so there might be some typos or mistakes. If you find any typos or bugs, please email me at [email protected]⁴ and I’ll send you a link to download a free copy of my latest book, Measures of Success: React Less, Lead Better, Improve More⁵ via LeanPub.com. Thanks! Mark Graban ¹http://www.leanblog.org ²http://www.markgraban.com ³http://www.twitter.com/markgraban ⁴mailto:[email protected] ⁵measuresofsuccessbook.com Podcast #1: Norman Bodek on Kaizen and Continuous Improvement July 16, 2006 Podcast Page Link⁶ - MP3 File⁷ Mark Graban: Welcome to the first ever Lean Blog podcast. This is Mark Graban, creator of the Lean Blog. My guest today is Norman Bodek, one of the leading voices in the Lean manufacturing world. I’m very happy to have him here with us. First, a little bit about this podcast. It’s my first attempt, you’ll notice I’m not a professional broadcaster. I’m a Lean consultant, I’ve worked with Lean as an engineer and consultant for about 12 years. I started what was then the Lean Manufacturing Blog, in early 2005 when I was working as an internal Lean change agent for a large manufacturing company. I continued the blog as I moved last August [2005] into a new role as a Lean health care consultant working in hospital settings. The website evolved into, what we call simply the “Lean Blog” because it’s about manufacturing, healthcare, and aspects of Lean that really do apply in any sort of industry. The blog has been really a great learning opportunity for me. I’m hoping that this podcast will expand my learning and I’m hoping ⁶http://www.leanblog.org/1 ⁷https://mgraban.hipcast.com/download/932c3142-5098-ecdc-3e16-4301d25d1e29.mp3 Podcast #1: Norman Bodek on Kaizen and Continuous Improvement 2 that others are going to join me in that learning journey. This is the first of what I hope will be a monthly series of podcasts. Each of them an interview with a leader or an innovator in the Lean world. Today, I start with Norman Bodek. He is the president of PCS Press, a publishing, training, and consulting company based in Vancouver, Washington. He discovered and published the works of the truly great Japanese manufacturing geniuses Dr. Shigeo Shingo and Taiichi Ohno, the inventors of the Toyota Production System. From his numerous trips to Japan, he introduced to the western world the Kaizen Blitz. Single-Minute Exchange of Dies, Total Productive Maintenance, hoshin kanri, poka-yoke, and other new manufacturing method- ology that have helped companies improve their quality and pro- ductivity around the world. Norman’s written countless books, including The Idea Generator: Quick and Easy Kaizen⁸ and his most recent book Kaikaku: The Power and Magic of Lean⁹. You can find more about Norman and his books at his website www.pcspress.com¹⁰. Norman, I want to thank you very much for being here on the first Lean Blog Podcast. Really is a pleasure to have you here. Norm Bodek: Mark, I want to thank you very much for do this with me. It’s going to be a lot of fun. We’ll talk a lot of management issues. Hopefully, this will stimulate a lot of people out there to focus more on continuous improvement. Why I think it’s the heart of the Toyota Production System. Mark: I was hoping we could start off first, we talk a little bit about the background of Quick and Easy Kaizen, first that’s the title of one of your books. Tell us how you discovered that approach, how that might be different than what other people think of with Kaizen or Kaizen events. ⁸https://amzn.to/2Rd6dLC ⁹https://amzn.to/2R8HGaF ¹⁰http://www.pcspress.com/ Podcast #1: Norman Bodek on Kaizen and Continuous Improvement 3 Norman: Yes, they are distinctly different. Seeing that, whoever the other person was change the name. Originally it was called, “Five day and one night”. I met Ohno’s two chief assistants warden account. They told me they were leaving Toyota and they want to come to America to teach a consultants. I said, “Fine, I’ll bring you over and I’ll run events for you.” And I did. I brought them over and they ran these events called, “Five days and one night.” Then Barnwell changed the name to “The Kaizen Blitz” and it’s not appropriate. Because Kaizen is small incremental improvements. That’s what Kaizen is. Kaizen is change, Kaizen is small continuous improvements. Kaizen Blitz is really Kaikaku, which is the name of my other book. Kaikaku means “Radical change”. That’s what a Kaizen Blitz is, it’s a radical change. What Kaizen is, as I said, it’s small incremental improvements getting everyone in the company involved. The suggestion system I credit it to Kodak back in 1898. The first suggestion was, “Clean the windows.” It’s a wonderful idea. The purpose of a suggestion system was to get ideas, to get all the employees involved, to empower people. To help them participate in a direct way in the organization. Back then in the late 1800’s and early 1900’s people were just doing very simple repetitive tasks and the supervisor would not let the worker do these things. Very often when you do stuff with a suggestion system, people come up with ideas for other people to do things and not them- selves. It went from a suggestion system to a cross-saving system where the average American company that had a system would get one idea every seven years. That’s a statistic that was given by the America suggestion system. Mark: That’s per employee? Podcast #1: Norman Bodek on Kaizen and Continuous Improvement 4 Norman: That’s per employee per year. One idea every seven years. Toyota, who re-looked at this. In studying America management, they re-looked at the America suggestion system and they said, “We want to get all of our employees involved.” We’re doing quality circles, which is putting people in teams, teams are coming up with ideas, but how do we get everybody to come up with ideas? Small, little ideas to make their work easier and more interesting. They adapted it first, the American system, and slowly changed it. The first year I think Toyota started on this, they got one idea per employee for the whole year. After about 10 years, they were up to 46 ideas per employee per year. One per month. One per month implemented idea from an employee. That repre- sented millions of ideas. In fact, I published a book once called 40 Million New Ideas in 20 Years at Toyota. 40 million ideas. Now, it’s astronomical when companies think of this. How can I manage those kinds of ideas? In fact, I gave a lecture out here to company in Oregon, and the manager had 900 people in the plant. I said in Japan, they get two ideas per month per employee. He said no, I have 900 people. I can’t manage 1,800 ideas, and he wouldn’t go forward, so soon. Because you don’t manage it. People manage it themselves. People come up with an idea, and they do it themselves. A lot of people do come up with ideas, and they implement it. But the beautiful part of this system is that it is a system. It’s a process to stimulate and encourage everybody to participate in change, to use their creativity ability. Most people have such boring dead end jobs in factories. Most people just hate to come to work. When I ask the question to audi- ences what day of the week you like, almost everybody says Friday, Saturday, and Sunday.
Details
-
File Typepdf
-
Upload Time-
-
Content LanguagesEnglish
-
Upload UserAnonymous/Not logged-in
-
File Pages30 Page
-
File Size-