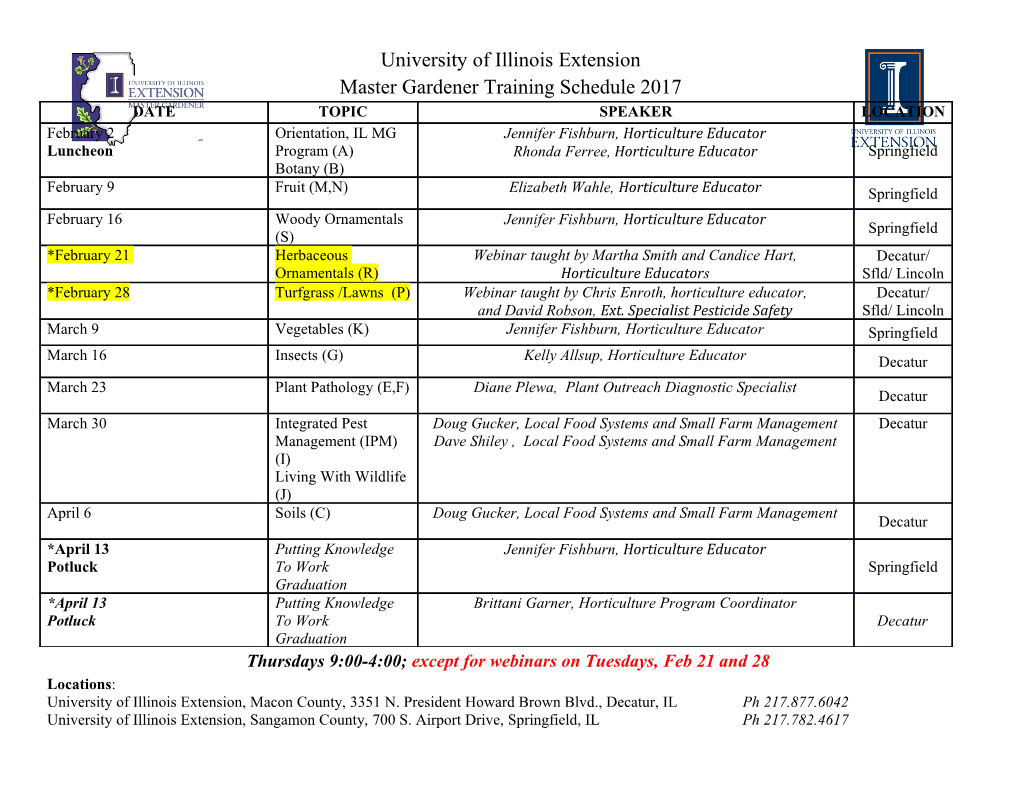
White paper Liquidmetal alloy in automotive applications A broad range of application opportunities. ey Liquidmetal technology process attributes include precision, Kstrength, surface finish, corrosion resistance, hardness, and high elasticity. These attributes result in a broad range of automotive application categories that could benefit from the technology. Among them include engine timing systems, fuel injection, interior and exterior decorative components, passenger safety components, pumps, sensors, severe duty connectors, and many others. Like any manufacturing process, leveraging the full benefits of Liquidmetal technology is achieved by developing application designs intended for the process. While there are many success stories about parts that have been converted from one process to another, experiencing the best economics and performance is always a result of having the part-design freedom. This design liberty is necessary to address all of the requirements of the manufacturing process used to produce them. White paper Finding the right fit Liquidmetal technology has its own set Pick three of characteristics, some of which overlap other metalworking technologies, making it a valuable manufacturing alternative. Hardness, If you need three or more of the attributes scratch & wear High elastic to the right, Liquidmetal technology is resistance limit a likely solution for your automotive application. Strength Non-magnetic Liquidmetal alloy has many notable Surface finish capabilities, but one in particular stands out; dimensional precision and repeatability. Because the process Corrosion Complex shapes generates all of the final material resistance Dimensional characteristics in the molding process step control/ repeatability with little to no shrinkage (0.4%), part geometries are very stable. Additionally, there is no phase change that occurs in the material from its molten state at the beginning of the injection cycle to the material’s solid state in the mold after cooling. Low shrinkage and a lack of phase change allow the material to mimic the mold cavity with high precision and repeatability. 1 2 3 A good Liquidmetal application Potential Applications Brushless DC Drive Strength Surface Surface finish Precision Finish Corrosion Elasticity Key attribute Port Fuel Injection Strength Corrosion Surface Finish Precision Resistance Corrosion Elasticity Key attribute Nozzle Strength Surface Finish Precision Precision Corrosion Elasticity Key attribute Ignition Systems Strength Surface Finish Precision Precision Corrosion Elasticity Key attribute White paper Precision To gain a better understanding of Liquidmetal alloy’s capabilities, a gauge capability study was conducted on a 32-piece sample using a coordinate measuring machine. In the histogram that follows, two dotted lines represent the gauge repeatability for the two dimensions measured, and the solid lines represent six standard deviations for the part dimensions. To summarize the results, the Liquidmetal process may be even more precise than previously thought. The minimal difference between the dotted and solid lines signify that the CMM, with gauge error considered, performs marginally better than the actual part to part variance for the sample. Additionally, no two parts varied more than 2.5 µm for one dimension, and 2.4 µm for the other. These results confirm the incredible precision of the Liquidmetal process, and often beat even the most conservative repeatability ranges for other manufacturing processes, like CNC machining. Dimensional control and precision Automotive applications requiring dimensional tolerances common to CNC machining are candidates for the Liquidmetal process. There are a number of components in a broad range of assemblies that meet this criteria, such as fuel injection components, engine timing and variable valve applications, fluid control valves, and sensors. White paper Corrosion and Surface Finish Combining excellent corrosion resistance, brilliant surface finish, and high hardness, Liquidmetal alloy is an excellent solution for decorative components. This is particularly true for high-end automobile applications where the look and feel of chrome plated plastic does not match that of a real metal surface. Testing has shown Liquidmetal alloys can outperform 316 stainless steel in highly corrosive environments. Figure 6. 3600 SS-316 500 250 100 0 0 0 0 1N HCl 1N H2 SO4 NaOH pH13 Seawater As-molded surface finish for Liquidmetal alloy is comparable to lapping and superfinishing polishing techniques. This capability allows for reduced post processing cost on cosmetic surfaces of decorative components. Ra µm 50 25 12.5 6.4 3.2 1.6 .8 .4 .2 .1 .05 .025 .012 CASTING Liquidmetal Less Frequent MIM Common Die Casting Investment Casting Sand Casting ABRASIVE Superfinishing Lapping Polishing METAL CUTTING Grinding Turning Milling 2000 1000 500 250 125 64 32 16 8 4 2 1 .5 Ra µIn White paper Applications such as instrument bezels, nameplates, key fobs, handles, and other touch points where the feel of metal exhibits high quality are all great candidates. They will especially benefit from the processes’ unique ability to provide fine surface finish and corrosion resistance. Elasticity The unusually high elastic limit of Liquidmetal alloys provides a particularly good alternative to 17-4 PH and 316 stainless steel for pressure sensors. These common materials used in pressure sensors are subject to physical deformation, embrittlement, and property changes over time. Burst failure, caused by pressure spikes, along with corrosion are common causes of failure with these alloys. Stainless steels also have to protect electronics from the damaging effects of exposure to the liquids and/or gases for which they are monitoring. Both are challenging requirements because these materials experience cyclical stress, which can lead to micro-fractures thus allowing fluids and gases to penetrate the sensing device. White paper A well built pressure sensor requires the mechanical properties of its diaphragm to be maintained over hundreds of millions of cycles and decades of use to achieve accurate results over the lifetime of the sensor. Membranes made from Liquidmetal alloy are extremely stable, exhibiting consistent elastic deflection with extensive use, thus making the alloy a great candidate for sensors. 17-4PH 0.51% Condition H 900 316L 0.52% Annealed 0.69% lasticity (% of original shape) Titanium Ti-6Al-4 1.% Conclusion The automotive application possibilities are endless. High precision, corrosion resistance, surface finish, strength hardness, elasticity, and the other characteristics of Liquidmetal alloy are all achieved by a single step molding process. No post processing, such as heat treating, is required to achieve final material properties. Wondering how Liquidmetal alloys might work for your application? We Talk to the invite you to download our design guide and speak with Liquidmetal scientists and engineers. We are challenging experts. everything you know about metal parts processing. Why not challenge us? (949) 635-2100 liquidmetal.com .
Details
-
File Typepdf
-
Upload Time-
-
Content LanguagesEnglish
-
Upload UserAnonymous/Not logged-in
-
File Pages8 Page
-
File Size-