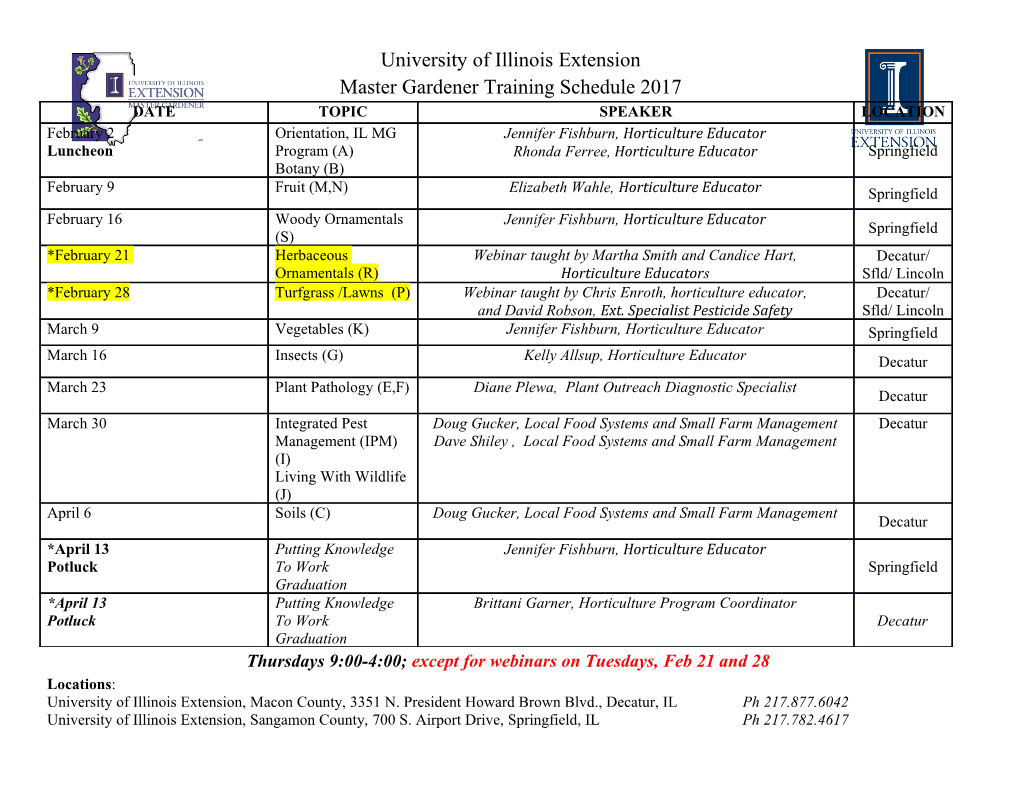
United States Patent Office Patented Mar. 2, 1968 2 3,373,114 In the solution described above, the persulfate reacts DRY COMPOSETIONS FOR DEOXDZNG AND with aluminum, or its alloying elements in the Smut, and DESMUTTING ALUMINUM AND ALUMNUM is reduced to aluminum sulphate. Thus, unlike prior de ALLOYS oxidizing baths, the exhausted solution contains no ob John J. Grunwald, New Haven, Conn., assignor to Mac jectional components which give rise to waste disposal Dermid Incorporated, Waterbury, Conn., a corporation problems. The invention here disclosed differs from that of Connecticut claimed in the aforesaid Patent No. 3, 190,203 in that it No Drawing. Continuation-in-part of application Ser. No. is directed specifically to dry, powder compositions from 313,785, Oct. 4, 1963. This application Jan. 3, 1967, which an oxidizing solution of the type disclosed in the Ser. No. 606,575 0 aforesaid patent may be prepared. The powder composi 4 Claims. (C. 252-136) tions provide advantages over the liquid equivalents in The present invention relates to the surface prepara regard to easier handling and lower shipping weights, but tion of aluminum and alloys for subsequent metal finish more importantly and quite surprisingly produce substan ing operations such as painting, anodizing, plating, bright tial improvement in certain other respects as will more dipping, welding, chromating, etc. This application is a 5 fully appear herein. continuation-in-part of application Ser. No. 313,785 filed One such improvement lies in the greater stability of ct. 4, 1963 now abandoned and of application Ser. No. the powder compositions during storage until sold and 104,816, filed Apr. 24, 1961, now Patent No. 3, 140,203. shipped for use. It is well-known, of course, that the per It is an important procedure in the aluminum finish acids are troublesome, presenting certain definite hazards ing industry, prior to the finishing operations mentioned 20 in respect to explosive decomposition. A concentrated above, to remove the ever-present oxide film which forms sulphuric acid solution of a persulfuric acid salt, for ex on the surface of aluminum alloys on atmospheric ex ample, upon standing for sufficient time as in a ware posure. A typical method employed in the past by which house, can and may deteriorate with the formation of this is achieved involves immersing the previously de Caro's acid (H2SOs), according to the following mecha greased aluminum object in a suitable deoxidizing Solu 25 nism: tion, which usually contains oxidizing agents Such as HSOa--HO->HSO5-H2SO4. chromic acid, chromates or dichromates, nitric acid or a mixture of these materials in well defined proportions. HSO5-HO->HO-H2SO4 Their function is to replace this tenacious oxide film on Thus highly concentrated solutions of persulfuric acid the aluminum alloy by another film more suitable for 30 may become quite dangerous, especially when stored in subsequent treatments. certain metallic containers over extended periods of time, The use of chromic acid or any other chrome base since they favor formation of highly unstable hydrogen deoxidizing solution in the finishing industry creates peroxide. waste disposal difficulties, since these formulations must An additional advantage of the dry powder composi be treated chemically before they can be disposed of tion is realized by avoidance of the hazard involved in without causing pollution problems. Also the use of preparing the treatment bath from the concentrated solu chromic acid in certain finishing shops may cause con tion as commonly supplied for shipment, which hazard tamination of rinsing waters, bright dips, anodizing and arises from the highly exothermic nature of the reaction plating solutions. Furthermore, the use of nitric acid is produced by addition of concentrated sulfuric acid to always accompanied by obnoxious fumes which makes 40 Water. for conditions uncomfortable to personnel and hazardous Another and most significant improvement resulting to their health, as well as causing corrosive action on from the dry powder admixture of the operative com processing equipment and materials. ponents is a most significant and substantial increase in Another procedure frequently used heretofore in the the useful life of a treatment solution prepared from the aluminum finishing industry as a preparatory step, prior powder composition vis-a-vis the liquid equivalents. The to the finishing treatments, consists in etching the alumi improvement noted here is remarkable and quite unex num alloy in a suitable alkaline solution, thereby remov pected, giving expected useful life of a treatment bath ing substantial amounts of surface metal. During this measured in months up to a year or more in some cases, etching process, certain alloying elements of the alumi (providing of course normal replenishment is made for num, which are insoluble in the etching solution, will 50 unavoidable drag-out and consumption) as compared cover the surface in the form of a loose coating forming to a bath life expectancy of but a few weeks at best when an unsatisfactory base for further treatment, and care using the liquid equivalents when initially preparing the must therefore be taken to see that this loose coating is bath. The reason or mechanism for this unusual stability completely removed. This phenomenon is known in the is not clearly understood, but it is conjectured that the industry as smut formation, and removal of the Smut is 5 5 acid salt (used in place of the liquid acid) functions as commonly referred to by the term "deoxidizing' in prac a diluent making the action of the persulfate more mod tice and is so used in the present specification and ap erate and controlled. pended claims. A still further advantage of the pre-admixed powder composition is that it eliminates weighing-out or meas In the above-mentioned Patent No. 3,140,203, there 60 uring of more than one ingredient, thus further reducing is disclosed a novel aluminum deoxidizing solution com the possibility of faulty make-up. This is of special im prising in combination a strong inorganic acid, more par portance in the present system where the pH of the treat ticularly sulphuric acid, and a soluble persulfate. Am ment solution prepared from the components is critical, monium persulfate or one of the more readily available as previously mentioned. alkali or alkaline earth metal salts of persulfuric acid In general, the powder compositions of this invention are specifically recommended. Providing the acidity of consist in the combination of a persulfate salt that is the solution is maintained at a pH not in excess of 2.0, soluble in water, such salts being selected from the group excellent deoxidation at room temperature is obtained for consisting of ammonium, sodium and potassium persul all alloys of aluminum except those with high silicon fates, together with an acid salt of sulfuric acid likewise content. Even where those alloys do have a high per 70 soluble in water, such acid salt being selected from the centage of silicon, however, they can be handled in such same cation group as in the case of the persulfate, namely system by adding a fluoride anion. ammonium, sodium and potassium. The persulfate and 3,373,114 3. 4. acid sulfate salts are comminuted if necessary simply to Example III preak up any large agglomerations and are thoroughly Aliquot parts of the same powder composition as that admixed to provide a uniform composition. The admix prepared in Example I, namely 50 grams of sodium bi ure is controlled in respect to the amounts of each salt sulfate and 30 grams of ammonium persulfate, were dis in the final composition, whereby the weight ratio of the solved in each instance in different volumes of Water to acid salt of sulfuric acid to that of the persulfate, com show the effect of dilution upon both the solution pH and puted on the basis of mole equivalents of sodium bisul treatment time. The results are tabulated in Table I. fate and ammonium persulfate, respectively, ranges from 1:1 to 10:1. The lower ratio just stated, i.e., equal weights TABLE I of bisulfate and persulfate salt, is a limiting one in order 0 Wolume of Solution pH at Time to Remove that treatment baths prepared therefrom will be more Solution 25° C. Smut (min.) 2 liters------------- 1.35 4. definitely assured of having a maximum pH value not 5 liters------------- 1.65 13% in excess of 2.0 since this, as explained previously, is 10 liters------------ 1.90 25 critical to successful aluminum desmutting. As will be discussed further, such condition will result inherently The foregoing comparison of times to effect desmut when the weight ratios just given are observed upon dis ting are based on identically prepared sample aluminum solving the composition in water to make the treatment alloy panels etched in astandard alkali (sodium hydrox bath. The higher ratio mentioned above, namely 10:1 is ide) etch solution under identical conditions of time limiting in the sense that the persulfate level here is so (2 min.), temperature (160-165 F.) and concentra low that the speed of reaction of the treatment solution 20 tion (75 g./l.) to produce a black oxide on the surface prepared from a mixture of such ratio represents a prac of each. Although it will be noted that treatment time tical minimum for commercial purposes. Optimum mix required increases with greater dilution of the desmutting ture ratios on a gram weight basis are on the order of composition, the pH of the solution remains below 2.0 5:2 to 5:3, bisulfate to persulfate, with the total weight and desmutting still takes place although at greatly re selected to provide about 70 to 80 grams per liter when 25 duced rate.
Details
-
File Typepdf
-
Upload Time-
-
Content LanguagesEnglish
-
Upload UserAnonymous/Not logged-in
-
File Pages3 Page
-
File Size-