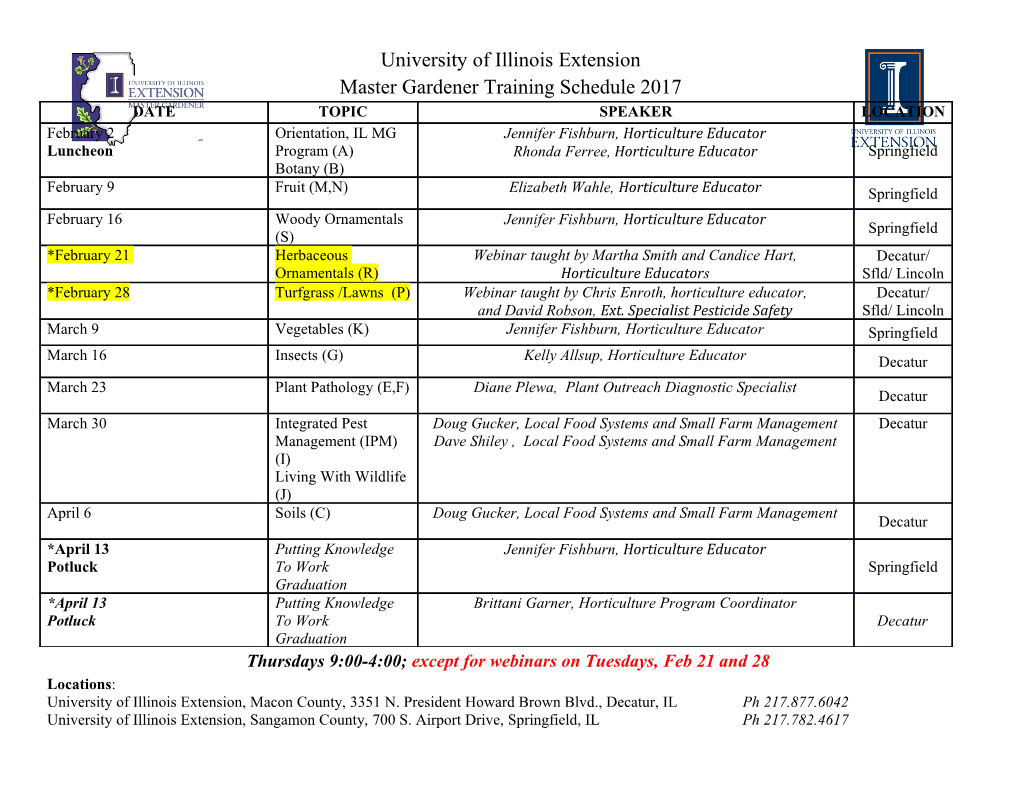
Processing, Characterization and Mechanical Properties of SiAlONs Produced from Low Cost † β-Si3N4 Powder Hasan Mandal1* and Nurcan Calis Acikbas2 1 Materials Science and Engineering Programme, Sabancı University 2 Department of Mechanical and Manufacturing Engineering, Engineering Faculty, Bilecik S.E. University Abstract SiAlON ceramics have been known for many years as prime candidate materials in structural applications at ambient and high temperatures involving superior mechanical and/or chemical processes. In spite of their excellent properties, the utilization of SiAlONs has remained limited till today due to the high cost of raw materials and processing. In order to circumvent this problem, low cost refractory grade, coarse, impure, less sinter active β-Si3N4 powder was used to produce SiAlON ceramics with satisfactory mechanical properties. In this article, the processing challenges in the production of SiAlON ceramics with β-Si3N4 powder were discussed. The process parameters obviously affect the phase assemblage, densification, microstructural and mechanical properties of final SiAlON ceramics. Processed β-Si3N4 powder characteristics are majorly investigated by SEM-EDX, XRD, XRF, laser particle sizer and elemental analyser. The existence of undesirable impurities in theβ-SiAlON crystal structure because of the use of impure Si3N4 powders has been shown to be tolerable by TEM microstructural analysis. Mechanical properties are in general evaluated by Vickers indentation method. Wear behaviour of the cost effective SiAlONs were compared with commercially available ceramic materials which are commonly being used in wear applications. Initially the use of such powders to produce materials for engineering applications proved challenging, however, satisfactory results have been obtained by the optimization of the initial chemical composition and process parameters. Keywords: powder processing, β-Si3N4 powder, particle size, sintering, characterization, wear processing stage has a strong effect on microstruc- 1. Introduction tural development, since ceramic parts are produced SiAlON ceramic materials are very significant by the sintering of initial powder mixtures8-12). Re- with their highly desirable, and proved potential, moval of impurities from the raw powders, initial especially in industrial wear and high temperature particle size distribution, homogeneous dispersion applications1-3). The final mechanical and chemical of sintering additives, and grinding of starting non- properties of these ceramics depend on microstruc- oxide powders are the important parameters in the tural evolution (grain size, grain aspect ratio, poros- microstructural formation of SiAlON materials with ity, intergranular phase, impurities, etc.)4-7). Powder superior mechanical properties13-19). SiAlON produc- tion processes are based on homogenization of raw † Accepted:August 10, 2012 powders α or β-Si3N4 powder, Al2O3, AlN and sin- 1 Orhanli, Tuzla/Istanbul, 34956 Turkey tering additives such as Y2O3, Sm2O3, Er2O3, Dy2O3, 2 Bilecik, 11210, Turkey * CaO, etc. in alcohol or water in order to achieve a Corresponding author: ı E-mail: [email protected] predetermined composition (α:β-SiAlON ratio (α : ı TEL: +90-216-4839666 FAX: +90-216-4839118 β ), a determined intergranular phase chemistry), ⓒ 2013 Hosokawa Powder Technology Foundation 22 KONA Powder and Particle Journal No.30 (2013) followed by drying of slurry, shaping, and sintering. ed β-SiAlON grains to increase fracture toughness). Traditionally, high quality pure α-Si3N4 powder is Si3N4 powders and sintering additives were mixed used instead of β-Si3N4 powder due to its higher sin- with high purity AlN powder (H Type, Tokuyama ter activity. However, fine α-Si3N4 powders are very Corp. Japan, with 1.6wt% O content) and Al2O3 (Alcoa high in cost and this is a key determinant parameter A16-SG Pittsburgh, USA). All of the prepared SiAlON for large scale applications. On the other hand, β compositions with β-Si3N4 powders were milled in -Si3N4 powders can be produced economically with water with 64wt% solid loadings. Tetramethylammoni- combustion synthesis20). Free silicon and iron may um hydroxide (TMAH) was used as a dispersant with originate from milling of the raw β-Si3N4 powder. Re- 2.5 wt%. Milling was performed for a total duration moval of these impurities and/or achieving desired of two hours. The slurry was sieved with 32 µm and final phases including these impurities in the sintered homogenized together with 2 wt % plasticizer (Pri- product is required. Besides milling and sintering mal B60, Rhöm & Haas, Italy), 2 wt % binder (PEG process parameters have crucial effects on micro- 4000, Clariant Produkte GmbH, Germany) and 2 wt% structural evolution. In this respect, SiAlON powder lubricant (Zuzoplast Wem, ZSC Zimmer&Shwarz, processing technology involves a number of know- Germany) in a mixer. The slurries were spray dried how developments to produce materials with supe- (Nubilosa LTC-2 model). The powders were uniaxi- rior properties at low cost. ally pressed at 25 MPa and subsequently cold iso- In this article, the manufacture low cost SiAlON statically pressed at 300 MPa to improve green den- ceramics with satisfactory mechanical properties by sity. Binder burn-out process was carried out at 550 the use of low cost refractory grade, impure, less sin- ℃ for 30 minutes. The pellets were sintered both by ter active β-Si3N4 powder was described. Correlation gas pressure sintering (KCE, FPW 100/150-2200-25 between processed β-Si3N4 powder characteristics type furnace), under 2.2 MPa nitrogen gas in a stan- and process conditions with final phase assemblage, densification, microstructure and mechanical proper- Initial β-Si3N4 Powder ties was determined. Cleaning 2. Experimental Studies (Magnetic cleaning and wet sieving) In this study β-Si3N4 powder manufactured by combustion synthesis (Beijing Chanlian-Dacheng Attrition Milling (in water, 1400 rpm, down to 1, 0.8 and 0.5µm ) Trade Co. Ltd., China) was used as initial Si3N4 pow- der. Attrition milling in water with Si3N4 grinding me- dia (3 mm in diameter) at 1400 rpm was performed to Characterisation of β-Si3N4 Powder (XRD, XRF, SEM-EDX, Laser Particle Sizer) decrease the average particle size of β-Si3N4 starting powder. In order to completely understand correla- tion between processing-structure-property relation- Compositional Design ships, β-Si3N4 powder characteristics were investi- gated by using SEM-EDX, XRD, XRF, laser particle Attrition Milling sizer and elemental analyser. Since αı and βı phases are both stable thermody- namically, it is possible to produce hard and tough Uniaxial Pressing and Cold Isostatic Pressing α-β-SiAlON composites. For this purpose 30α :70β-SiAlON composition was designed and Y-Sm- Debinding Ca multi cation doping system was chosen with the aim to produce self reinforcement microstructures. Y2O3 (>99.9%, H.C. Starck Berlin, Germany), Sm2O3 Sintering (GPS and PLS) (>99.9%, Stanford Materials Corp., USA), CaCO3 (>99.75%, Reidel-de Haen, Germany) were used as sintering additives. CaO was used to avoid α to β Si- Characterisation (XRD, SEM) AlON transformation, Y O and/or Re O (where Z Hardness and Toughness Measurement 2 3 2 3 Re Sand blast wear test ≥62)) to increase the stability and hardness of α-Si- AlON and Sm2O3 (where ZRe<62) to develop elongat- Fig. 1 Flow chart of the manufacturing process. KONA Powder and Particle Journal No.30 (2013) 23 Table 1 Sand blast test conditions 1.6 Cleaned β Pressure 6 bar 1.4 Asreceived β Particle composition Alumina 1.2 y β Particle size of alumina 0.5-1 mm it 1 Alumina content 2 kg 0.8 β 2 ve Intens 0.6 Si 2 Sample dimensions 24.5 × 7 mm ti Si β FeSi 0.4 Fe Test duration 10 min. Rela 0.2 Distance to nozzle 10 mm 0 Impact angle 50° 23 25 27 29 31 33 35 37 39 2 theta Fig. 2 An XRD analysis of cleaned and as-received β-Si3N4 powders. dard manner and by pressureless sintering (Thermal Technology, 1000-4560-FP2000 model furnace). Post sintering heat treatment was performed at 1900℃ for 3 hours under 0.1 MPa nitrogen gas. Flow chart of the manufacturing process is given in Fig. 1. α:β phase ratio and phase composition of the in- tergranular phase were determined by X-ray diffrac- tion (Rigaku 2000 Rint, Japan). Polished surfaces of the sintered samples were gold coated prior to exami- nation in a Zeiss VP50-Supra type scanning electron Fig. 3 Schematic illustration of iron and silicon remov- microscope (SEM) by using back-scattered electron ing processes. imaging mode. Analytical TEM investigations were achieved by using 200 kV field emission TEM (JEOL contains Fe, Si, Fe2Si and FeSi2 as impurities. Iron JEM-2100F). contamination was believed to cause from the milling Hardness and fracture toughness measurements process of starting Si powder involving use of steel were carried out by Vickers indentation technique by grinding media. applying 10 kg load for 10 seconds. At least 5 inden- In order to remove iron, magnetic cleaning pro- tations were made for each sample. The sand blast cess was applied as shown in Fig. 3. Initial β-Si3N4 wear tests were further performed at Röchling Leripa powder was mixed in mixer with isopropyl alcohol GmbH (Austria). The test conditions were given in and Fe impurities were collected with a magnet. This Table 1. The erosion rates of the nozzles are defined process was repeated until iron impurities were to- as the nozzle mass loss divided by the nozzle density tally removed. To remove silicon impurities, obtained and so volume of the erodent abrasive particles (wear slurry after magnetic cleaning process were passed volume) is found. under 75 µm sieves to separate coarser silicon par- ticles. Subsequently slurry was dried in rotary evapo- rator. A phase comprises of as-received and cleaned 3. Results and Discussion β-Si3N4 powder is given in Fig. 2. XRD analysis 3.1 Powder processing challenges and solutions showed that this cleaning process is effective, since Widespread use of SiAlON parts is limited at pres- there were no silicon or iron/iron containing impuri- ent due to high cost of raw materials and of process- ties detected.
Details
-
File Typepdf
-
Upload Time-
-
Content LanguagesEnglish
-
Upload UserAnonymous/Not logged-in
-
File Pages9 Page
-
File Size-