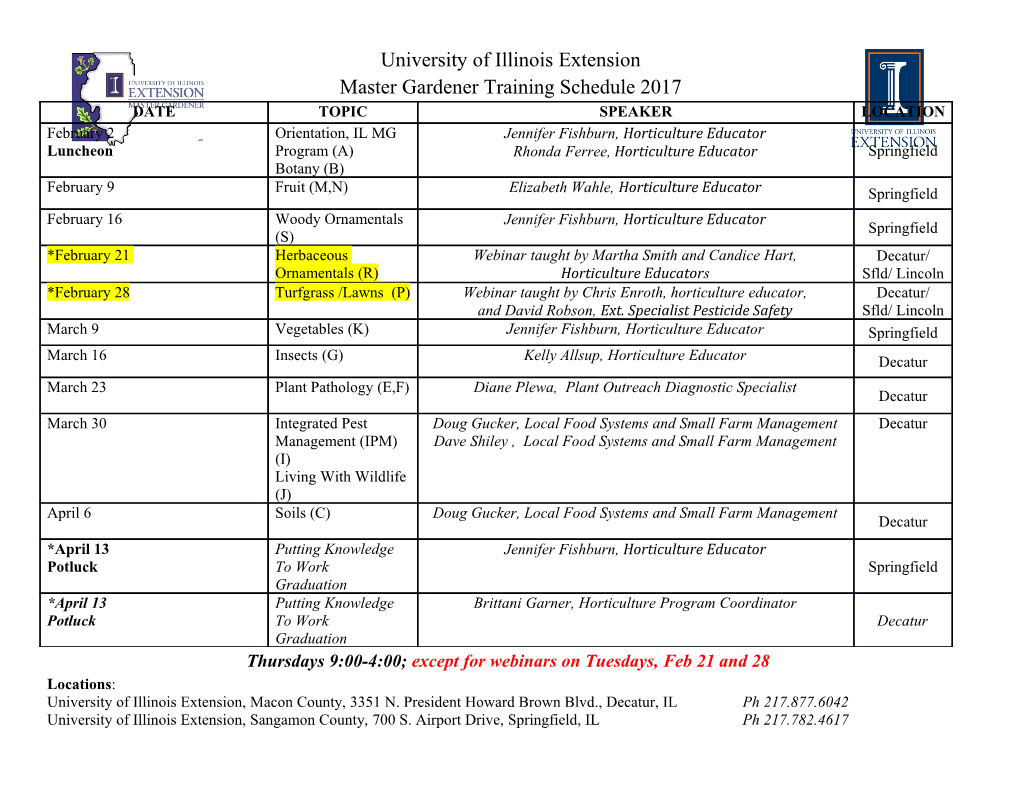
Engineered Wood Products for Structural Purposes Charlotte Bengtsson SP Trätek Växjö University Contents • General about EWP •Productioncontrol • Overview over EWPs •New developments EWP definition • EWP are made from ”pieces” of timber which are arranged or formed for structural purposes. Bonding with adhesives or heat and pressure. • General concept Cut in smaller pieces and re-assemble (reducing defects) Tailor-made structural members •Resulting products more homogeneous less variability (less orthotropic) EWP - general • Overcoming weaknesses of solid wood • Taking advantage of low-quality raw material • Structural members of “any size” • Less variability in material properties – higher design strength Diff. in design value Diff. in mean value Number of beams Strength EWP - general • Strong • Large interval of spans • Made with durable adhesives • Dimensionally stable – Made from dry material Structural Timber Strength [MPa] C24 24 C30 30 Glulam GL32 32 GL36 36 LVL 40-50 EWP - general • Accurate production control is required • Sometimes, 3rd party surveillance is required • Development of Plywood started beginning of 20 century • Glulam was developed early 19th century – C.F. Wiebking (1762-1842) Examples • Glued-laminated timber (glulam) • Laminated Veneer Lumber (LVL) – Kerto™, Microllam™ • Parallel Strand Lumber (PSL) –Parallam™ • Laminated Strand Lumber (LSL) – TimberStrand™ • I-Joists (I-beams) – Masonitebalken™, TJI™ Examples • Oriented Strand Board (OSB) • Plywood • High Density Fibre Board (HDF) –Masonite™ •Particleboard Production control of EWP • Optimised products • Sensible to production errors •Productioncontrol – Quality system – Internal control –Externalaudits • Certification – CE-marking Production control of EWP • Quality system according to a standard –Production place • Ex. requirement on moisture and temperature –Production methods • Description, instructions –Equipment • Description, maintenance –Internal quality control • Visual control • Random control (ex strength) Production control of EWP • External control/audit – Carried out by inspection body – Unannounced visits – Control of the internal quality system (production place, journals etc…) – Sampling for tests by an approved laboratory –Testing Certification and marking • Requirements on products and production are given in a standard • A notified body checks that the requirements are fulfilled • The notified body issues the right to mark the product (CE- marking) • Ex of products that can be CE-marked –Glulam –Panelproducts – I-beams – Stuctural timber Glulam •Low variability in properties •Arbitrary size •Shape stability •Otpimised use of material •Arbitrary shape Manufacturing of glulam • Laminations (spruce) – 40-50 mm thickness (curved: 20-30 mm) – 1.5-5.0 m length –Dry timber (12-15 %MC) – Machine stress graded – Finger joints –Cut to size – Planing Manufacturing of glulam •Beams – Laminations to form cross-section – Apply adhesive, pressure, heat, curing – Planing •Adhesives –PRF, MUF, PUR •Shapesand sizes – Prismatic, curved, single and double tapered – Pot life of adhesives, transport Manufacturing of glulam • High degree of added value •Industrialisedprocess • Stress graded timber (C, L, LS or LD-grades) • Quality control – Finger joints – Delamination of glulam • CE-marking in Europe according to harmonised standard EN 14080 Glulam - characteristics • Lamination effect – Beam bending strength superior to lamination tensile strength • Large beams (deep) – Nominal strength decrease with increasing size (size factor) • Influence of finger joints – 50-75 % of failures in finger joints Glulam - inspiration Parallel Strand Lumber (PSL) • Common in Canada and US • 1986 • Large strands cut from veneers • Defect removal – adhesive – assembly – pressure and curing -trimming –ripping –end product • High density • Characteristic surface • Used for large and small members • Possible to treat with preservatives due to voids in the structure • Fire: comparable to sawn timber PSL - examples Laminated Strand Lumber (LSL) • Common in Canada and US • Early 1990 • Small strands (waste or from fastgrown trees) • Drying of strands – addition of resins – blending – forming - press – sanding - cutting • High density • Characteristic surface • Used for wood framing LSL - examples LVL • Thin veneers (3-5 mm) • Introduced around 1955 • Drying – grading of veneers – adhesive application – hot pressing – trimming – cutting – grading –end product • Same fibre orientation in (almost) all layers • Used for structural framing, I-joist flanges, scaffolding… LVL (KERTO) LVL I-joists • Introduced 1970 •Lowweight •Lowvariabilityin properties •Reliable products • Accurate dimensions • Dimensional stability • ”Squeak-free” floors • Solid wood/LVL flanges • HDF/OSB/Plywood web • Replacing large dimension solid timber I-joists - manufacture • Strength grading of timber, by machine with visual complement (flange) • Fingerjointing to desired length (flange) • Cutting of groove (flange) • Jointing and cutting of tongue for the webmaterial • Jointing of flanges and web to a beam I-joists - manufacture • Manufacturing varies between mills • Strength grading, then cutting • Orientation of the flange Experiences from testing I-joists Failure modes • Tension failure at knot or fingerjoint • Buckling of upper flange • Shear failure very seldom Evaluation - E • Evaluation of E in three different ways • Mid-span deflection, curvature and density of the flanges 1 . 577 E = ρ0 , 12 Variation in beam properties •Data from SP´s quality control (data from 350 I-joists) •Two classes, mentioned ”Class 1” and ”Class 2” Emidspan Ecurvature Edensity Quality Mean Cov Mean Cov Mean Cov [MPa] [%] [MPa] [%] [MPa] [%] Class 1 12500 11 12440 12 12920 9 Class 2 13440 7 13420 8 13780 8 (Requirements 11000 and 13000 MPa) Variation in beam properties Bending Total Depth Flange depth strength Quality 5th Cov Mean Cov Mean Cov perc. [%] [mm] [%] [mm] [%] [MPa] Class 1 26.1 16 299.5 0.2 46.8 1.4 Class 2 30.2 15 249.7 0.2 46.9 1.1 (Requirements 22 and 27 MPa) COV in bending strength for machine strength grading is normally around 20 %. I-joists •New plant (Masonite beams) opened some weeks ago in Rundvik •CE-marking possible by ETA Oriented Strand Board - OSB • Introduced 1970 • Flakes and adhesive formed under heat and pressure to structural panels • Three orthogonal layers • Outer layers parallell to the long axis of the panel, inner layer perpendicular or randomly aligned • Careful production control is required to control the quality Developments • Cross laminated timber • Composites (wood-plastic, alternatives) • Question of formaldehyde emissions (new tough requirements) •??.
Details
-
File Typepdf
-
Upload Time-
-
Content LanguagesEnglish
-
Upload UserAnonymous/Not logged-in
-
File Pages36 Page
-
File Size-