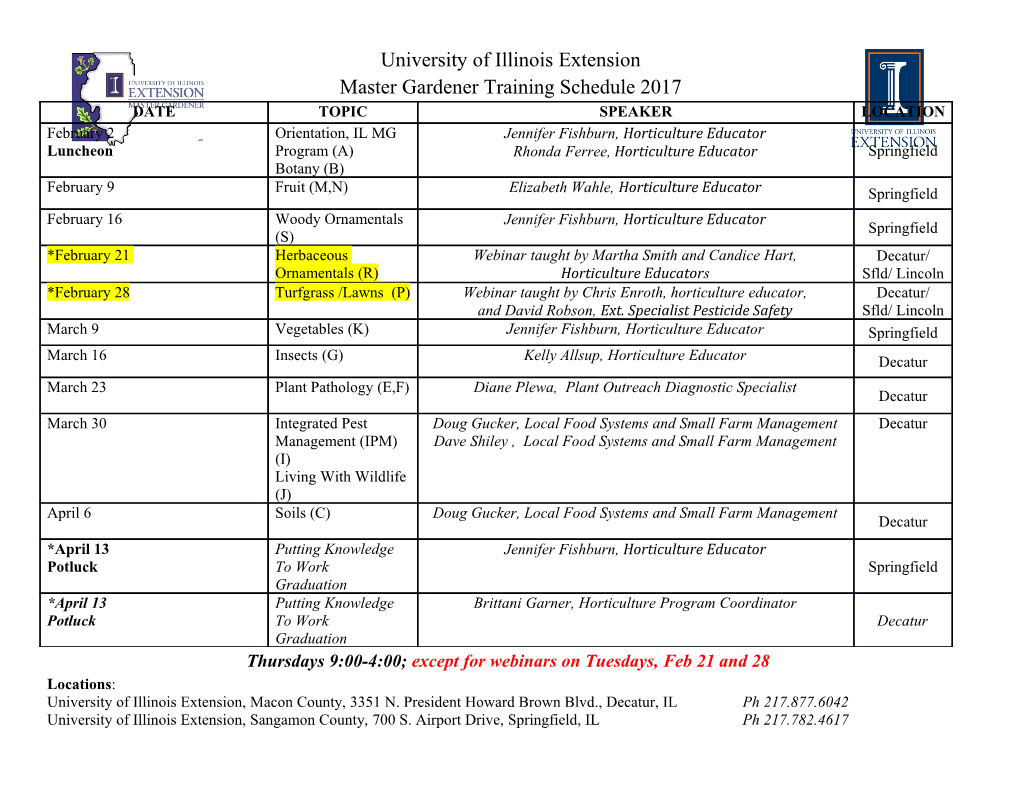
Development of an intelligent system for building product design and manufacturing − Part II: production process planning and scheduling Deyi XUE, Jun SUN, and Douglas H. NORRIE Department of Mechanical and Manufacturing Engineering The University of Calgary, Calgary, Alberta, Canada T2N 1N4 Abstract An intelligent system was developed for modeling the activities in building product design and manufacturing to improve the efficiency of product development. This paper focuses on the production process planning and scheduling aspects of this intelligent system. Manufacturing requirements, including tasks and sequential constraints for accomplishing these tasks, are described using the feature-based product representation scheme. Manufacturing resources, including facilities and persons, are defined as agents, which are coordinated by two mediators: facility mediator and personnel mediator. The optimal production process and its timing parameters for producing the products ordered by customers are identified based upon heuristic search and agent-based negotiation. The intelligent production process planning and scheduling also serve for evaluating the feasibility, cost, and time to manufacture the products ordered by customers. part II of this paper focuses on aspects of 1. Introduction production process planning and scheduling. With the advances in computer technologies, Production process planning is an approach to especially in artificial intelligence (AI) techniques, identify the manufacturing tasks to accomplish the the traditional product development activities, required design. Usually a number of feasible including design and manufacturing, have been processes can be used to produce the desired automated by developing the intelligent design and product. The goal of process planning is to identify manufacturing systems (Kusiak, 1992, Dong, 1994, the optimal one with the least manufacturing Maturana and Norrie, 1996). Despite of the efforts, such as the shortest production time or the progress, the present intelligent design and lowest production cost. manufacturing systems need to be further improved in the following aspects: (1) to integrate knowledge Production scheduling is a process to allocate modeling and product modeling, and (2) to appropriate resources for the required integrated the isolated design and manufacturing manufacturing tasks and to identify the sequence systems into an integrated environment. and timing parameters to accomplish these tasks. Limited resources include facilities, personnel, To solve the problems of the current intelligent materials, and so on. A good schedule can reduce design and manufacturing systems, the research on the efforts in manufacturing, thus improving the developing an integrated design and manufacturing competitiveness of the products. system was carried out in Xue’s previous research (Xue and Dong, 1993, Xue and Dong, 1994, Xue et The research on intelligent planning/scheduling al., 1996, Xue, 1997). This system provides the for solving production problems considering real functions to model product descriptions and product world constraints was initiated by Fox (Fox, 1983). development knowledge, and to identify the optimal In this research, constraints were used for guiding design considering design functional performance the direction of search to identify the feasible and and production costs. the optimal schedules. Since then, many researches on constraint-based scheduling have been carried The research given in this paper presents the out (Zweben and Fox, 1994). The methodologies of experience of the further development of the scheduling are classified into two categories: intelligent design and manufacturing system for constructive approach and repair approach. building product design and manufacturing. The The constructive approach achieves a complete This paper focuses on the improvement of the schedule gradually from a partial schedule using manufacturing aspects. The requirements are constraints as guidance (Fox, 1983, Fox et al., summarized as follows: 1989). The repair-based method, on the other hand, 1. A method to model manufacturing starts with a complete schedule and modifies it requirements and associate these requirements with iteratively towards the optimal solution (Morris, the design descriptions is needed. In the 1990, Zweben et al., 1992). Both approaches aim conventional production planning/scheduling at identifying the optimal schedule considering the systems, manufacturing requirements are given as demanding constraints through iterative search tasks. Each task specifies its resource requirements process. To improve the search efficiency, many including machines and persons. These tasks are not constraint propagation methods, which deduct more associated with the design descriptions and constraints from the current available constraints, constraints. Therefore, the computer-based design have been introduced to reduce the search space and planning/scheduling systems were developed as (Zweben and Fox, 1994). separated systems. Since the design descriptions Problems of the present intelligent scheduling also influence the requirements of manufacturing systems are summarized as the following two tasks, an integrated scheme for representing product aspects. First, manufacturing tasks and resources in design and manufacturing tasks should be these systems are modeled as constraints. Design developed. descriptions and constraints are not considered in 2. A distributed method to model manufacturing these systems. Second, the production scheduling resources is required. Manufacturing constraints mechanisms in these systems were primarily are modeled as resources, such as facilities and developed based on the centralized control persons. In the past time, these resource databases architecture, in which all the knowledge base and were described at the same place and accessed by a database were described in the same place. This centralized control system. This type of the control architecture has difficulty in handling the database representation method is effective when complex manufacturing systems that require the complexity of the manufacturing system is not knowledge and data in different places. The recent high. With the increase of the manufacturing system research in distributed agent-based technology complexity, manufacturing activities often take provides new approaches to solve the problems place at different locations, thus requiring different caused by centralized scheduling (Parunak, 1996). knowledge bases and databases at different places. This research addresses the following two Therefore, distributed resource modeling approach issues: (1) to generate the optimal schedule is needed. The recent advances in developing agent- considering both of design constraints and based systems provide new approaches to model the manufacturing constraints, and (2) to develop an different knowledge bases and databases, and intelligent planning/scheduling mechanism using associate these knowledge bases and databases in the distributed agent-based technology. problem solving (Parunak, 1996). 3. An efficient method to identify the optimal 2. Requirements for building schedule should be developed. The objective of product manufacturing production process planning and scheduling is to identify the optimal schedule, based upon the Due to the adoption of a computer system for desired goal such as the minimum production time organizing design and production activities, lead- or the minimum cost. In scheduling, all the design times of the product development and and manufacturing constraints should be manufacturing at a local building product considered. The traditional heuristic search is manufacturing company have been reduced effective to identify the optimal solution dramatically. To further improve the product considering the constraints. However, due to the development efficiency, a university-industry large search space, improvement in search project was launched in 1997. This project focuses efficiency, while maintaining the search quality, has on the following two issues: (1) to improve the to be conducted. The recent advances in multi-agent efficiency of product modeling and design, and (2) systems provide distributed methods to improve the to reduce the production time and cost by search efficiency and quality (Parunak, 1996). introducing advanced production process planning and scheduling methods. Feature-based Product Modeling Sub-system Resource Management Sub-system Class Feature Class Browser Features Person Agents P1 Person Instance Feature Instance Personnel P2 Resource Browser Features Mediator Design Engineer … Browser Pm Product Ordering and Scheduling Sub-system F1 O1 Facility Facility F2 Resource Manager Resource Scheduling Scheduling O2 Mediator … Browser Browser Engine … Fn Sales Person Sales Ok Facility Agents Order Agents Figure 1: Manufacturing modules in the system produce the ordered products. When an order to 3. Manufacturing modules in the manufacture a product is created, an order agent is intelligent design and then generated to represent the customer manufacturing system requirements. The order agents negotiate with the resource agents using the corresponding design Manufacturing modules in the intelligent design and constraints and manufacturing requirements, which manufacturing system are shown in Figure 1. These are preserved in the instance features, to identify the modules are organized into 3 sub-systems: feature- optimal
Details
-
File Typepdf
-
Upload Time-
-
Content LanguagesEnglish
-
Upload UserAnonymous/Not logged-in
-
File Pages10 Page
-
File Size-