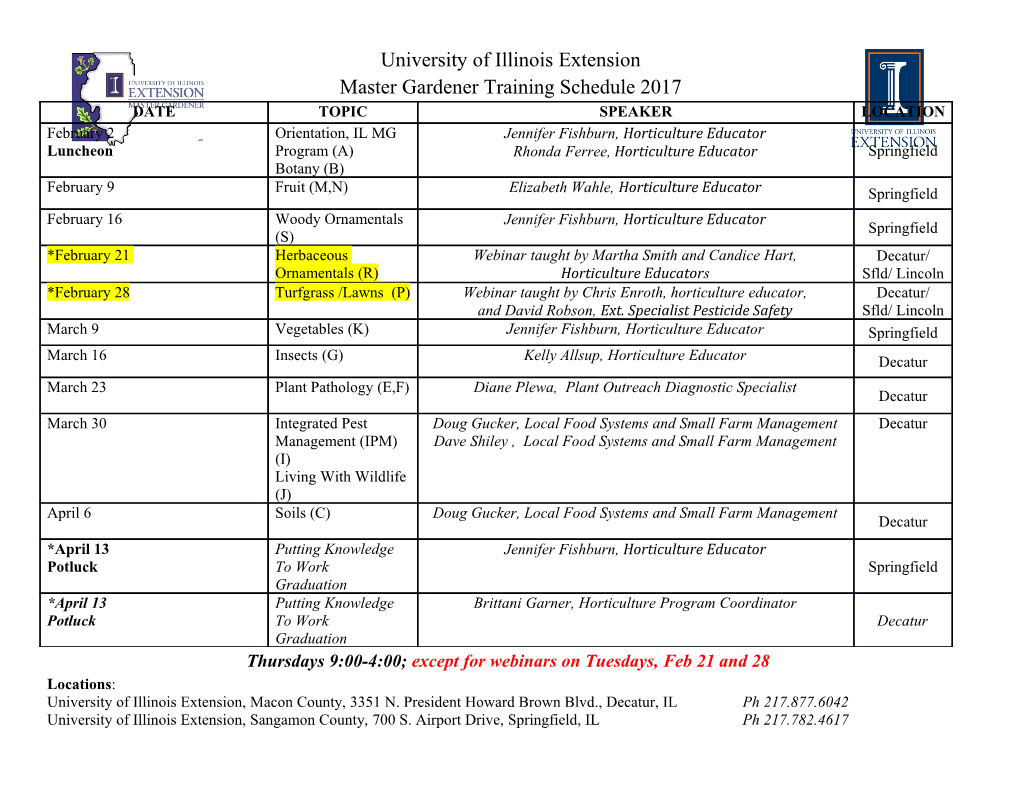
Development of Predictive Gasoline Direct Fuel Injector Model for Improved In-cylinder Combustion Characterization Thesis Presented in Partial Fulfillment of the Requirements for the Degree Master of Science in the Graduate School of The Ohio State University By Mohit Atul Mandokhot Graduate Program in Mechanical Engineering The Ohio State University 2018 Thesis Committee Prof. Shawn Midlam-Mohler, Advisor Prof. Giorgio Rizzoni 1 Copyrighted by Mohit Atul Mandokhot 2018 2 Abstract Gasoline direct fuel injection systems have gained importance due to the increasing level of emissions regulation on SI combustion systems. Direct fuel injection delivery to cylinder provides better atomization and fuel mixing performance, enabling homogenous mixture and better in-cylinder combustion. Increasing focus over the last few decades has been on better characterization of such gasoline direct fuel injection systems. Solenoid powered injectors act as actuators and enable accurate fuel delivery into the cylinder for a combustion event. Characterization of injector’s fuel delivery performance is an important aspect of achieving improved in-cylinder combustion performance. The objective of the current thesis is to develop a numerical physics based fuel injector model that provides a reliable prediction of flow rate and needle lift, in order to be used to improve in-cylinder combustion performance using 3D CFD model methodology. The developed model provides a reliable estimate of flow rate of developed injector, which is experimentally verified against instantaneous flow rate data provided by typical suppliers. In cases where inadequate prediction performance was noted, the errors arise out of lack of high fidelity electromagnetic modeling data, damping characteristics inside model and lack of geometry data to capture performance of highest accuracy. ii Dedication To the pursuit of truth, a journey which I believe is worth undertaking because of the trials it brings and one’s flaws it exposes, in return making oneself stronger. I embarked on this endeavor for my parents and could not have done it without my family and their support. iii Acknowledgments I would like to gratefully acknowledge Prof. Shawn Midlam-Mohler’s confidence in me, his support and guidance throughout this journey. His confidence in me while I navigated through the waters of research, helped me grow immensely. I would also like to acknowledge Prof. Giorgio Rizzoni for lending his expertise as a committee member on my research. I thank him for earnestly delivering his knowledge during my Master’s courses which have helped me explore this new career. I must acknowledge David Hillstrom for being a provider of valuable feedback, a wise soundboard for forming ideas and always being up for coffee at 4pm. In SIMCenter’s coterie of excellent graduate students, people who strive every day to grow themselves, I have been lucky to find a lab full of encouragement and fun. Thanks to Clayton, Aditya, Vivek, Kepin and Ullekh for an environment that fostered growth on wide dimensions while having fun. My final set of thanks are to Dr. Jeeseon Park-Saltzman. SIMCenter, Center for Automotive Research and The Ohio State University have helped me grow in new dimensions. I am grateful to God and the people that have made it happen. iv Vita May 2012…………………………………….B.E (Hons.) Mechanical Engineering, BITS, Pilani – K.K Birla Goa Campus, India 2012 to 2016…………………………………FMC Technologies, Hyderabad, India. 2016 to present………………………………Graduate Research Associate, SIMCenter, The Ohio State University Fields of Study Major Field: Mechanical Engineering v Table of Contents Abstract ............................................................................................................................... ii Dedication .......................................................................................................................... iii Acknowledgments.............................................................................................................. iv Vita ...................................................................................................................................... v List of Tables ................................................................................................................... viii List of Figures .................................................................................................................... ix 1. Introduction ..................................................................................................................... 1 2. Objective and Scope of Thesis ........................................................................................ 9 3. Literature Review .......................................................................................................... 10 3.1 Review of 1D-3D Engine Research ........................................................................ 10 3.2 Review of Injector Modeling .................................................................................. 13 References ......................................................................................................................... 20 4. Proposed Technique for Injector Characterization ....................................................... 21 5. Model Development ...................................................................................................... 24 5.1 Injector Driver Circuit ............................................................................................. 27 5.2 Injector Electromagnetic Circuit ............................................................................. 35 5.3 Mechanical Circuit of Injector ................................................................................ 48 5.4 Fluid Flow Circuit ................................................................................................... 56 6. Post-Processing of Model Results ................................................................................ 76 6.1 Need for Combined Model ..................................................................................... 76 6.2 Structure of Models for Combination ..................................................................... 81 6.3 Post-Processing Algorithm for Combination of Results ......................................... 82 7. Results ........................................................................................................................... 86 7.1 Experimental Results .............................................................................................. 86 7.2 Simulation Results .................................................................................................. 91 vi 8. Error Analysis ............................................................................................................. 102 8.1 Metrics .................................................................................................................. 102 9. Conclusion .................................................................................................................. 115 Bibliography ................................................................................................................... 116 vii List of Tables Table 1 – Parameters, Injector Driver Controller, Gasoline Direct Injector ..................... 34 Table 2 - Parameters, Electromagnetic Circuit, Gasoline Direct Injector ........................ 47 Table 3 - Parameters, Mechanical Circuit, Gasoline Direct Injector ................................ 54 Table 4 - Parameters, Flow Circuit, Gasoline Direct Injector .......................................... 66 Table 5 - Parameters, Core Damping, Gasoline Direct Injector ....................................... 72 Table 6 – List of Elements for multi-domain physics in Injector Model .......................... 73 Table 7 – Operating Conditions of Injector Model ........................................................... 91 Table 8 – Relative RMS Error % per Zones for Cases ................................................... 114 viii List of Figures Figure 1. Gasoline Direct Fuel Injector interface with Cylinder, as shown in [8] .............. 3 Figure 2: Direct Fuel Injection system with Rail and Low Pressure Fuel System, as shown in [8] ........................................................................................................................ 4 Figure 3 - Gasoline direct injection rail architecture representation. .................................. 5 Figure 4 - Injector, I/O Diagram ......................................................................................... 6 Figure 5 – Sample Trapezoidal Instantaneous Flow Rate from Injection Event. ............. 12 Figure 6 – Silicon moulds used for dimensional analysis in nozzle sac area, as seen in [3] ........................................................................................................................................... 17 Figure 7 – Dimensional analysis and orientation of silicon moulds of nozzle holes of Gasoline Direct Injector, under SEM, as seen in [3] ........................................................ 18 Figure 8 – Proposed rate shaping of fuel injection using fast response actuator, as seen in [4] ...................................................................................................................................... 19 Figure 9 – Feed Forward simplistic fuel injection control command architecture in ECU
Details
-
File Typepdf
-
Upload Time-
-
Content LanguagesEnglish
-
Upload UserAnonymous/Not logged-in
-
File Pages129 Page
-
File Size-