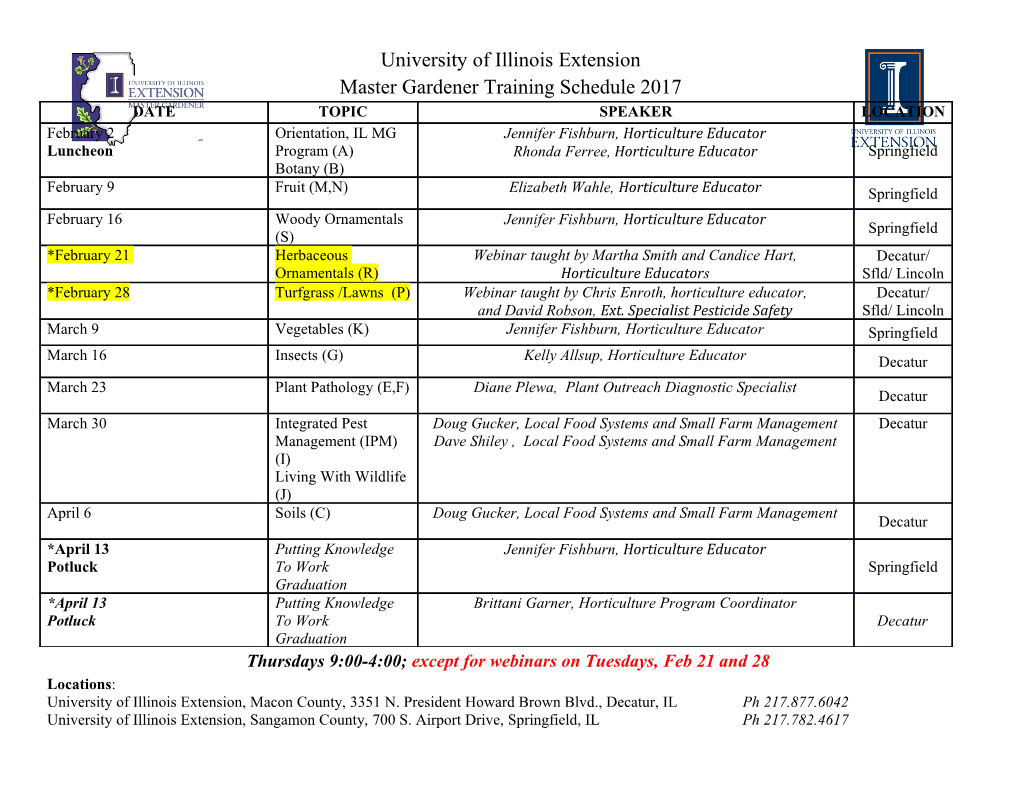
SOLIDIFICATION CRACKING PERFORMANCE AND METALLURGICAL ANALYSIS OF FILLER METAL 82 THESIS Presented in Partial Fulfillment of the Requirements for the Degree Master of Science in the Graduate School of The Ohio State University By Michael Romanoff Orr Graduate Program in Welding Engineering The Ohio State University 2016 Master's Examination Committee: Dr. John Lippold, Graduate Advisor / Faculty Emeritus Dr. Antonio Ramirez, Graduate School Chair / Professor Copyright by Michael Romanoff Orr 2016 ABSTRACT The main objective of this research is to investigate and eventually optimize the solidification cracking resistance of filler metal ERNiCr-3 (FM 82) in thick-section, highly-restrained, hot wire automatic gas tungsten-arc welding (AGTAW-HW) weld deposits used on reactor vessels in the nuclear energy industry. This investigation was achieved with experimental verification of cracking responses of three FM 82 heats using the Cast Pin Tear Test (CPTT), metallurgical/chemical analysis of each heat, and computational analysis. An intentional nitrogen addition study was conducted to observe the effect of increased weld metal N on solidification cracking susceptibility of FM 82. Experimentally, results were considered using the CPTT with varying heats of ERNiCr-3 exhibiting either superior or poor solidification cracking resistance behavior. A verification study was implemented using the CPTT and its designated procedure with three heats of FM 82 that were previously tested. Excellent correlation results showed accuracy and repeatability of the CPTT process. Quantitatively, zero-pin deviations were found at the lower cracking threshold (LCT) of each heat. The LCT is designated as the highest pin length to exhibit 0% and is the main ranking criterion of solidification cracking susceptibility. Qualitatively, the results proved to verify the same ranking of solidification cracking susceptibility as the previous study—this ranking also mimics what is observed in production mockups. Scanning electron microscope (SEM) imaging of fracture surfaces exhibited classic solidification fracture morphology to ensure failure ii mode. Additional work was completed using the CPTT for two dilution studies (10wt% and 25wt %) of a “resistant” heat by a “susceptible” heat. It was observed that 10% dilution of Heat B by Heat A reduced the LCT by one pin-length, whereas 25% dilution reduced it by three pin-lengths. Furthermore, computational thermodynamic software, Thermo-CalcTM, was utilized to determine solidification temperature ranges and terminal phase formations of the FM 82 heat chemistries. This technique constituted a Scheil simulation which estimate alloying segregation behavior during solidification and phase stability after welding. For ease of comparison, one resistant heat (Heat B) was compared against one susceptible heat (Heat A). Heat B was predicted to have a solidification temperature range (STR) of 216°C and 0.1985 volume fraction NbC upon solidification to 99% solid. Heat A was predicted to have a lower STR (203°C) and higher volume fraction NbC (0.2822) upon solidification to 99% solid. Lastly, intentional nitrogen additions were included to see the effects the interstitial has on the susceptibility to solidification cracking of a FM 82 heat. Weldability testing included CPTT of a resistant heat welded with additions of 0.2, 0.4, 1, and 5 vol% N2 in the shielding gas mixture. SEM/EDS techniques were utilized to determine which constituents form based on the nitrogen content of the gas mixture. MX- type precipitates rich in Nb and Ti were found both in grain boundaries and in regions throughout the matrix. Although TEM work was not done to confirm this, the literature determines these MX precipitates to be (Nb,Ti)(C,N). iii DEDICATION This work is dedicated to God, my loving family, and my close friends. A special thank you to my parents, Jonathan and Karin Orr, whose encouragement to think and act independently drive me to live and love life every day. I am thankful for all of their wisdom, generosity, humility, and emotional and financial support throughout my life. Also, an immense feeling of gratitude to my brothers, Benjamin and Matthew Orr, for being my best friends and biggest role models. Michael Romanoff Orr The Ohio State University, 2016 iv ACKNOWLEDGEMENTS I would like to thank: Dr. John Lippold—my graduate advisor, for his constant wisdom and support for my research Frank Argentine—my contact at BWXT, whose passion for his work, and constant support and communication made for a close and enjoyable collaboration between research and industry Ed Pfeifer and Ken Copley—the lab supervisor and technician at OSU, for their timely maintenance and much-appreciated advice with the machinery and technology at the Edison Joining Technology Center My fellow Graduate Research Associate—for teaching me in the labs, discussing metallurgy in the lounge, and making graduate school a fun experience altogether Connor Guarino—my mentee from Metro High School, for his hard work and persistence in the metallurgy lab at OSU preparing samples for testing v VITA June 2010……………..…………..…………………………….Woodridge High School 2015…………………………….…..B.S Welding Engineering, Ohio State University 2016………………………………...M.S Welding Engineering, Ohio State University Field of Study Major Field: Welding Engineering vi TABLE OF CONTENTS ABSTRACT ....................................................................................................................... ii DEDICATION ................................................................................................................. iv ACKNOWLEDGEMENTS ............................................................................................. v VITA ................................................................................................................................. vi LIST OF TABLES ........................................................................................................... xi LIST OF FIGURES ....................................................................................................... xiii CHAPTER 1: INTRODUCTION .................................................................................... 1 CHAPTER 2: BACKGROUND ...................................................................................... 4 2.1 Welding Metallurgy .................................................................................................. 5 2.1.1 Solidification Subgrain Boundaries (SSGBs)..................................................... 7 2.1.2 Solidification Grain Boundaries (SGBs) ............................................................ 7 2.1.3 Solute Redistribution .......................................................................................... 8 2.2 Solidification ............................................................................................................. 9 2.2.1 Solidification of Fusion Welds ......................................................................... 10 2.2.2 Solidification in Castings .................................................................................. 12 vii 2.3 Weldability .............................................................................................................. 16 2.3.1 Solidification Cracking ..................................................................................... 17 2.3.2 Avoiding Solidification Cracking ..................................................................... 29 2.4 Weldability Testing ................................................................................................. 32 2.4.1 Original Cast Pin Tear Test Method ................................................................. 32 2.4.2 OSU Second Generation Cast Pin Tear Test Method....................................... 35 2.4.3 OSU Third Generation Cast Pin Tear Test Method ......................................... 37 2.5 Nitrogen Effects on Ni-based alloys ....................................................................... 38 2.5.1 Investigation on the use of Nitrogen in Shielding Gas during Welding of Ni- based Alloys and Materials with Austenitic Microstructures .................................... 41 2.5.2 Effects of Nitrogen on Microstructure and Mechanical Properties .................. 43 2.5.3 Internal Nitridation of Ni-based Alloys ............................................................ 47 2.5.4 Nitrogen Effects on Solidification Cracking in Ni-based Alloys ..................... 49 CHAPTER 3: OBJECTIVES ........................................................................................ 53 3.1 Cast Pin Tear Test ................................................................................................... 53 3.2 Solidification Cracking Performance and Metallurgical Analysis of FM 82.......... 54 CHAPTER 4: MATERIAL AND EXPERIMENTAL PROCEDURE ...................... 55 4.1 Material ................................................................................................................... 55 4.2 Weldability Testing Procedure ................................................................................ 56 viii 4.2.1 Material Preparation ......................................................................................... 57 4.2.2 Button-Melting ................................................................................................. 59 4.2.3 Cast Pin Tear Testing ......................................................................................
Details
-
File Typepdf
-
Upload Time-
-
Content LanguagesEnglish
-
Upload UserAnonymous/Not logged-in
-
File Pages177 Page
-
File Size-