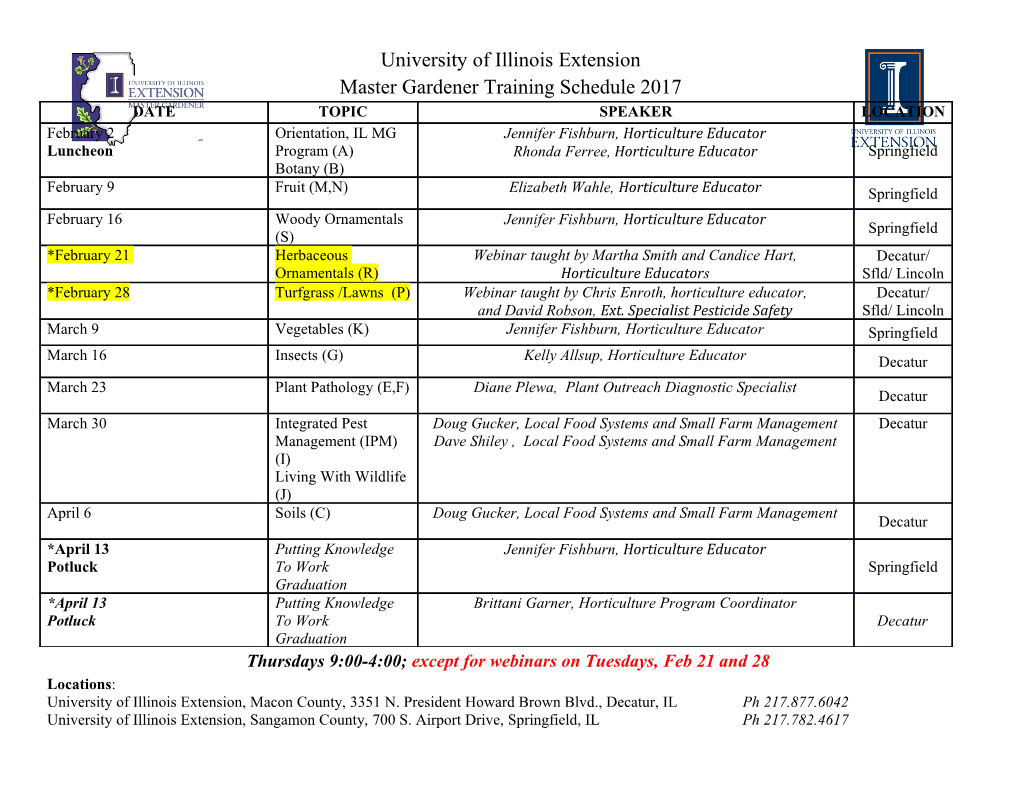
User report Ertron GmbH enhances product Satisfied with the VERSAFLOW 4/55 (from the left): Reinhard Probandt, Managing Director at Ertron GmbH, Thomas Wohlgemuth, quality with VERSAFLOW 4/55 Quality Assurance and Pjotr Cieslak, the man at the machine. Even more agility for the EMS service provider from Erfurt During the GDR era, Erfurt was one of the Mikroelektronik Erfurt with its parent major Eastern German centres for elec- company Funkwerk Erfurt. One of these is tronics manufacturing – a situation which the EMS service provider Ertron, founded has prevailed through to the present day. in 1992, which has quality and flexibility as Today, the spectrum on offer at the tech- part of its company DNA. For THT man- nology site Erfurt covers micro-system ufacturing, Ertron GmbH has now suc- technology and micro-electronics, sen- cessfully put its first selective soldering sor systems and photovoltaic systems. system VERSAFLOW 4/55 from Ersa into Several successful individual companies operation. Author emerged from the former state combine Mark Birl Area Sales Manager Ersa GmbH published in EPP 09/2019 in Germany Ersa informs 2/5 Offline programming or during machine operation: fast and simple preparation of soldering programs with the Editor CAD Assistant 4. In the background: Live process monitoring using the VERSACAM. In answer to the question as to how an This complete package also includes de- electronics manufacturing company velopment and design services. Ertron can survive these days in a high income has the same claim for every project – country like Germany, the terms quali- the aim is always a product that is easy ty and flexibility are always mentioned. to manufacture. “That’s what makes us These two characteristics also describe different from an engineering office,” Ertron GmbH. The EMS service provid- explains Reinhard Probandt, “because er emerged from the former testing their work is finished once development equipment construction department of has been completed. We, on the other Funkwerk. This means that Ertron has hand, always consider the manufac- know-how in the field of electronics turing process during development.” manufacturing as well as knowledge of Common challenges in development metalworking and mechanical process- and manufacturing include components ing. Its main expertise, however, is in the that are too close together, smalls that manufacturing of electronic assemblies are too small or PCB geometries that and components for a wide range of dif- cannot be clamped in product carri- ferent industries: gastronomy, medicine ers. These issues are solved in direct or traffic engineering and mechanical cooperation between the specialist ar- engineering. The company does under- eas. “Because I can only manufacture take unusual projects as well, however a product for a good price and in the – such as the electronics for bowling required quality if I can manufacture it centres or an organ builder. well. This means fewer failures for the customer. His product simply becomes “With 35 employees, we are a small more reliable. A cost advantage not only company with short paths. This means for the customer, but also for us as the we can act very quickly. An advantage manufacturing company,” says Ertron our customers are happy to benefit boss Probandt. from,” says Managing Director Rein- hard Probandt. “If necessary, we can Cooperation between Ertron and the implement projects from one day to Ersa, the soldering specialist from the next.” Batch sizes are between ten Wertheim, began in 2008. Reinhard and several hundred, which are main- Probandt had taken over as Managing ly used in printed circuit board panels. Director at Ertron just the year before. The main business is production of the At that time, there was a wide range of assemblies through to final assembly. different soldering stations from dif- As a service provider, Ertron also offers ferent manufacturers being used in the the respective logistics with compo- manual soldering range. For one thing, nent procurement and storage as well this entailed high costs for reordering as complete quality control with optical consumables and accessories such as and electrical inspection including com- soldering tips. missioning. Ersa informs 3/5 Assembly is clamped in a soldering frame. The company decided to standardise It was thus logical for Ertron that Ersa this “conglomeration”. Following de- should also be included in supplier se- tailed analysis, Ersa was chosen, and lection for the new soldering system today the specialists in the manual sol- and a corresponding inquiry was sent dering department work exclusively with to Mark Birl, the Ersa sales engineer re- i-CON soldering stations. Following the sponsible. The only possible solution for takeover of the electronics manufac- Ertron was a full tunnel wave soldering turer Inlab in 2013 by Ertron GmbH, the system, because the main objective – business relationship between Ersa and apart from the economic factor – was Ertron received a broader basis: Inlab long-term improvement of soldering delivered components for Ersa solder- quality. During the first talks it became ing irons and stations. In other words, apparent that on account of the Erton Ertron was no longer just an Ersa cus- range of components and products, a tomer, but a supplier at the same time, selective soldering system could be the because right up to the present control better choice rather than the POWER- cards for Ersa products such as the FLOW N2 wave soldering plant originally i-CON NANO, i-CON VARIO and the sol- planned. During a visit to the Ersa Appli- dering irons PTC*700 or i-TOOL NANO cation Centre in Wertheim, Mr Probandt are supplied by Ertron. and Mr Wohlgemuth from Erfurt took a close look at both machine options. After the visit, the decision was clear: VALUABLE IMPULSES FROM VERSAFLOW 4/55 with double soldering THE ERSA KNOW-HOW SEMINAR module was the right choice. The se- lective soldering system turned out to In 2017 Ertron had to purchase spare be the better solution for the products parts for its existing wave soldering manufactured by Erton, and it scored system. The plant was getting a bit long in terms of flexibility and the soldering in the tooth and reaching its technical quality achieved during the tests. limits. Preparation and post-treatment of assemblies, such as the masking of components that must not come into LESS THERMAL STRESS contact with solder, or the elimination of FOR ASSEMBLY solder bridges after soldering was bind- ing more and more capacities. This was Thanks to the new selective soldering also true of cleaning the assemblies, system, time-consuming preparatory since the wave soldering system was work that would have been necessary equipped with a foam fluxer. Thomas for the wave soldering process due Wohlgemuth (then responsible for the to the Ertron product spectrum is no wave soldering department) brought longer required. Unlike in the selective back valuable impulses and ideas from soldering process, the assembly moves his visit to the Ersa know-how seminar in a fixed direction – the direction of “Wave and selective soldering”. travel – over the soldering wave in the Ersa informs 4/5 VERSAFLOW 4/55 in batch operation. wave soldering machine. The soldering The user uses PCB data, either CAD wave comes into contact with the en- data such as DXF or ODB++, or graph- tire underside of the PCB in this case. ic files such as GIF or JPG to prepare Areas and components that must not the soldering program with the CAD be wetted with solder are either cov- Assistant 4 – the program editor from ered using special soldering masks or Ersa that has been integrated in the masked as at Ertron. In a selective sys- machine software ERSASOFT 5 since tem, on the other hand, only the com- VERSAFLOW 4. ponents to be soldered are approached and processed by the soldering nozzle. The autorouting function calculates the As an additional benefit, this reduces optimum travel paths for the microdrop the thermal stress for the assembly fluxer and solder pots, while the defini- and has a positive effect on its quality. tion of blocked areas prevents collisions with components. It goes without say- The setting possibilities are also limited ing that the travel paths can be saved with a wave soldering machine, this af- manually as well. Unlike in the wave sol- fects the holding time of the assembly dering system, the solder pots of the above the soldering wave or the solder- VERSAFLOW 4/55 can move under the ing wave tear-off, for example. The sol- PCB in the x and y directions. As a re- dering program always has to use mean sult, connector strips can be processed values. In the VERSAFLOW 4/55 on the according to length, independently of other hand, soldering parameters can their position. This means that the pot be entered individually for each solder- with the soldering nozzle moves past ing spot. Ertron regularly had problems the pins under a connector strip and with bridges formed between compo- thus sets up the solder connections nent pins during the wave soldering one after another – thus minimising process, because connector strips had solder bridges per se. to be routed across the soldering wave due to the PCB layout. Missing or in- sufficient solder passages were also an DOUBLING THROUGHPUT BY issue. PARALLEL OPERATION LONG-TERM IMPROVEMENT THANKS Ertron mainly processes products that TO INDIVIDUALLY DEFINED SOLDERING are soldered in the PCB panel. For this PARAMETERS reason, the VERSAFLOW 4/55 was equipped with a double soldering mod- Long-term improvement has been ule. Thus Ertron achieves double the achieved with the VERSAFLOW 4/55 throughput compared with a single sol- because all the soldering parameters dering module, since two assemblies of including the nozzle to be used for each the PCB are processed simultaneously soldering spot can be defined individu- in parallel operation.
Details
-
File Typepdf
-
Upload Time-
-
Content LanguagesEnglish
-
Upload UserAnonymous/Not logged-in
-
File Pages5 Page
-
File Size-