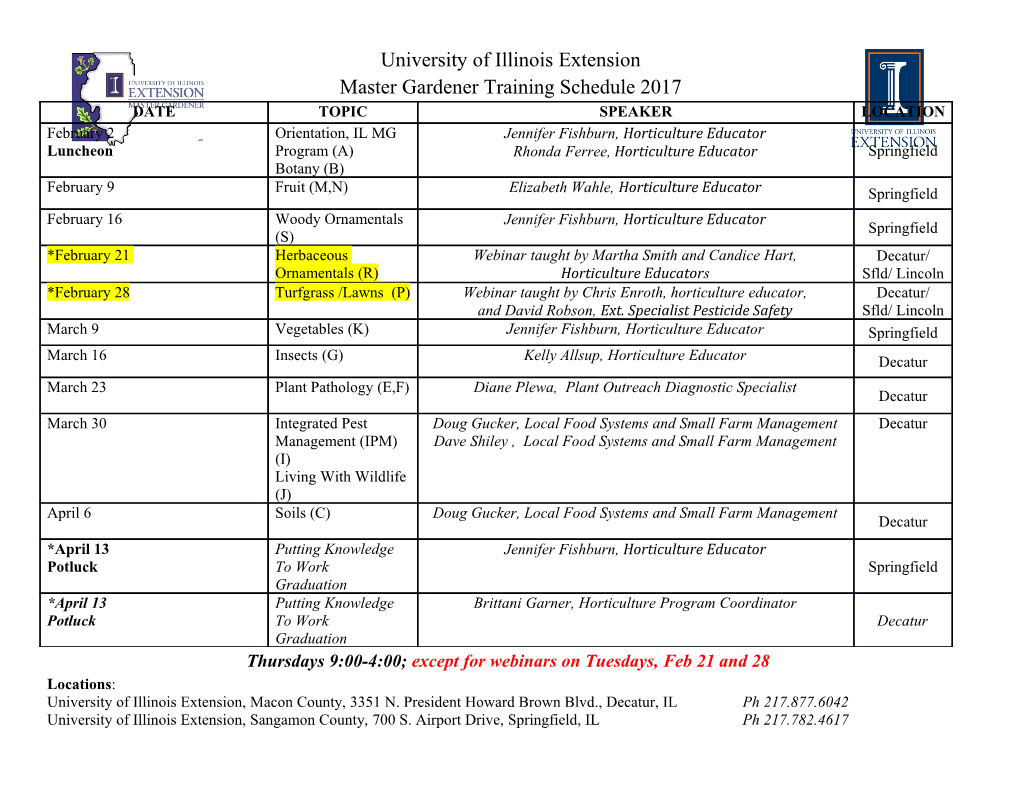
Development of the Cylindrical Jun Qu Wire Electrical Discharge Research Assistant Machining Process, Part 2: Albert J. Shih Associate Professor Surface Integrity and Roundness Department of Mechanical and Aerospace Engineering, This study investigates the surface integrity and roundness of parts created by the cylin- North Carolina State University, drical wire EDM process. A mathematical model for the arithmetic average surface Raleigh, NC 27695 roughness on the ideal surface of a cylindrical wire EDM workpiece is first derived. Effects of wire feed rate and part rotational speed on the surface finish and roundness for brass and carbide work-materials at high material removal rates are investigated. The Ronald O. Scattergood pulse on-time and wire feed rate are varied to explore the best possible surface finish and Professor, roundness achievable by the cylindrical wire EDM process. This study has demonstrated Department of Materials Science and that, for carbide parts, an arithmetic average surface roughness and roundness as low as Engineering, 0.68 and 1.7 m, respectively, can be achieved. Surfaces of the cylindrical EDM parts North Carolina State University, were examined using Scanning Electron Microscopy (SEM) to identify the macro-ridges Raleigh, NC 27695 and craters on the surface. Cross-sections of the EDM parts are examined using the SEM to quantify the sub-surface recast layers and heat-affected zones under various process parameters. This study has demonstrated that the cylindrical wire EDM process param- eters can be adjusted to achieve either high material removal rate or good surface integ- rity and roundness. [DOI: 10.1115/1.1475989] 1 Introduction Scanning Electron Microscopy ͑SEM͒ has been a common tool to examine EDM surfaces ͓4,7͔. The EDM surface consists of The wire Electrical Discharge Machining ͑EDM͒ process re- small craters created by electrical sparks ͓1͔. To improve the EDM moves the work-material by a series of electrical sparks between surface integrity, the size of craters needs to be small. This study the workpiece and wire electrode. These sparks generate craters uses the SEM to examine and estimate the sizes of craters. Sub- on the surface and the recast layer and heat-affected zone on the surface depths of the recast layer and heat-affected zone are two sub-surface of the EDM workpiece. The surface integrity de- other important characteristics of the EDM surface integrity. The scribes the mechanical, metallurgical, topological, and chemical SEM is used to examine the polished cross-section of EDM sur- conditions of the surface region. EDM surfaces are complicated. A faces to quantify and compare subsurface damage for various comprehensive description of the surface integrity on EDM sur- EDM process parameters and material removal rates. faces involves the measurement of surface roughness, depth of In this paper, a mathematical model of the arithmetic surface heat-affected zone, micro-hardness, size of surface crater, residual roughness of an ideal cylindrical wire EDM surface is introduced stresses, and endurance limit, etc. ͓1͔. This study investigates the in Section 2. Results of surface roughness and roundness measure- surface integrity and roundness of cylindrical wire EDM parts and ments for two sets of experiments intended to produce for high explores possible ways to adjust process parameters to achieve material removal rate and fine surface roughness, respectively, are better surface integrity and roundness. presented in Section 3. SEM micrographs of the surfaces and Investigations have been carried out to analyze and improve the cross-sections of the sub-surfaces of cylindrical wire EDM car- surface integrity of parts created by die-sinking EDM ͓2–5͔ and bide and brass parts are illustrated and discussed in Section 4. wire EDM ͓6–9͔. In representative studies, the arithmetic average surface roughness, Ra , of the wire EDM processed workpiece ͓ ͔ was about 0.2 to 0.4 m for tool steels 6 and 1.4 to 3.9 m for 2 Surface Finish Modeling metal matrix ceramic composites ͓9͔. For the die-sinking EDM process, better surface finish has been reported. The Ra values The cross-section of an ideal surface produced by the cylindri- could be achieved as low as 0.014 m on silicon components ͓5͔ cal wire EDM process consists of a series of circular arcs, as and 0.6 m on titanium carbide parts ͓4͔. Researchers have dem- shown in Fig. 1. The real EDM surface is the combination of this onstrated that better surface integrity can be achieved by optimiz- ideal geometry and craters generated by sparks on the surface. The ing the EDM process parameters ͓2,4,6,8,9͔. For the cylindrical radius of the circular arc in the ideal surface, re , is equal to the wire EDM process, effects of the new process parameters, such as radius of the wire, rw , plus the gap between wire and workpiece. part rotational speed, on the surface integrity and roundness are The same cross-section geometry can be found on surfaces ma- ͓ not known. A set of preliminary experiments was conducted to chined by turning with a radius tool and by ball-end milling 10– ͔ identify key process parameters that significantly affect the mate- 16 . The peak to valley surface roughness, Rt , of the ideal surface ͓ ͔ rial removal rate and surface roughness. Two sets of experiments, with circular arcs has been studied 12,13,15,16 . However, the in which these parameters are varied, were conducted to investi- closed-form analytical expression of the commonly used arith- gate their effects on material removal rate, surface integrity, and metic average surface roughness, Ra , could not be found in lit- roundness of cylindrical wire EDM carbide and brass parts. erature. Only the approximation solution, which replaced the cir- cular arc by a section of the parabolic curve, is available ͓15,16͔. The closed-form representation of the arithmetic average surface Contributed by the Manufacturing Engineering Division for publication in the JOURNAL OF MANUFACTURING SCIENCE AND ENGINEERING. Manuscript received roughness, Ra , for an ideal surface consisting of circular arcs is May 2001; revised December 2001. Associate Editor: Y. L. Yao. derived in this study. 708 Õ Vol. 124, AUGUST 2002 Copyright © 2002 by ASME Transactions of the ASME 1 p/2 ¯yϭ ͵ ydx (4b) p Ϫp/2 Defines S(x) as follows: 1 1 x ͑ ͒ϭ ͵ ϭ Ϫ ͱ 2Ϫ 2Ϫ 2 ͩ ͪ S x ydx rex x re x re arcsin (5) 2 2 re Using S(x), ¯y can be expressed as: 2 p/2 2 p 2 p ¯yϭ ͵ ydxϭ ͫSͩ ͪ ϪS͑0͒ͬϭ Sͩ ͪ (6) p 0 p 2 p 2 Define another parameter xc as the x coordinate where y(xc) ϭ¯y. Fig. 1 Cross-section view of an ideal cylindrical wire EDM sur- ϭͱ Ϫ 2 face and the key parameters and coordinate system for math- xc 2re¯y ¯y (7) ematical modeling The analytical expression of arithmetic average roughness, Ra , can be expressed as: 2 xc p/2 ϭ ͑ Ϫ ͒ ϩ ͑ Ϫ ͒ As shown in Fig. 1, after defining an XY coordinate system, Ra ͫ ͵ ¯y y dx ͵ y ¯y dxͬ p 0 x one of the circular arcs on the surface can be expressed as: c 2ϩ͑ Ϫ ͒2ϭ 2 2 p p x y re re (1) ϭ ͫSͩ ͪ Ϫ2 S͑x ͒Ϫͩ Ϫ2x ͪ ¯yͬ (8) p 2 • c 2 c • where 3 Experiments on Surface Finish and Roundness p p Ϫ рxр (1a) Cylindrical wire EDM experiments were conducted to investi- 2 2 gate the surface finish and roundness generated under different cos ␣ process parameters and to verify the surface finish model. The ϭ f p (1b) same work-materials, brass and carbide, as in the previous paper ͓17͔ are used in this study. The pitch, p, as shown in Fig. 1, is a function of wire feed rate, Two sets of experiments, designated as Experiments I and II, ␣ f , workpiece rotation speed, , and wire traversing direction, were designed. In Experiment I, the Material Removal Rate ͓ ͔ 17 . The peak-to-valley surface roughness, Rt , of the ideal sur- ͑MRR͒ was high. The wire feed rate and part rotational speed face shown in Fig. 1 has been derived ͓15͔. were varied to achieve different levels of surface roughness to verify the proposed surface finish model. In Experiment II, the p2 R ϭr Ϫͱr2Ϫ (2) goal was to adjust EDM process parameters to achieve the best t e e 4 possible surface finish and roundness. After conducting prelimi- nary cylindrical wire EDM experiments, two process parameters, The arithmetic average surface finish, Ra , of the ideal surface is defined by the following formula: the pulse on-time and wire feed rate, were identified to have sig- nificant effects on surface finish. Also, compared to Experiment I, 1 p/2 the material removal rates were reduced significantly in Experi- ϭ ͵ ͉ Ϫ ͉ Ra y ¯y dx (3) ment II to achieve good surface finish and roundness. Key process p Ϫ p/2 parameters for Experiments I and II are listed in Table 1. The where ¯y is the least squares mean line of the ideal profile, which other process parameters remain the same as in the previous paper is the reference mean line of surface roughness as defined in ͓17͔. Table 2 summarizes the MRR under different process param- ASME B46.1-1995 ͓18͔. Based on the definition of least squares eters in Experiments I and II. mean line, In Experiment I, four part rotation speeds and three wire feed p/2 rates were tested for cylindrical wire EDM of brass and carbide. yϪ¯y ͒2dx In total, 24 experiments were conducted.
Details
-
File Typepdf
-
Upload Time-
-
Content LanguagesEnglish
-
Upload UserAnonymous/Not logged-in
-
File Pages7 Page
-
File Size-