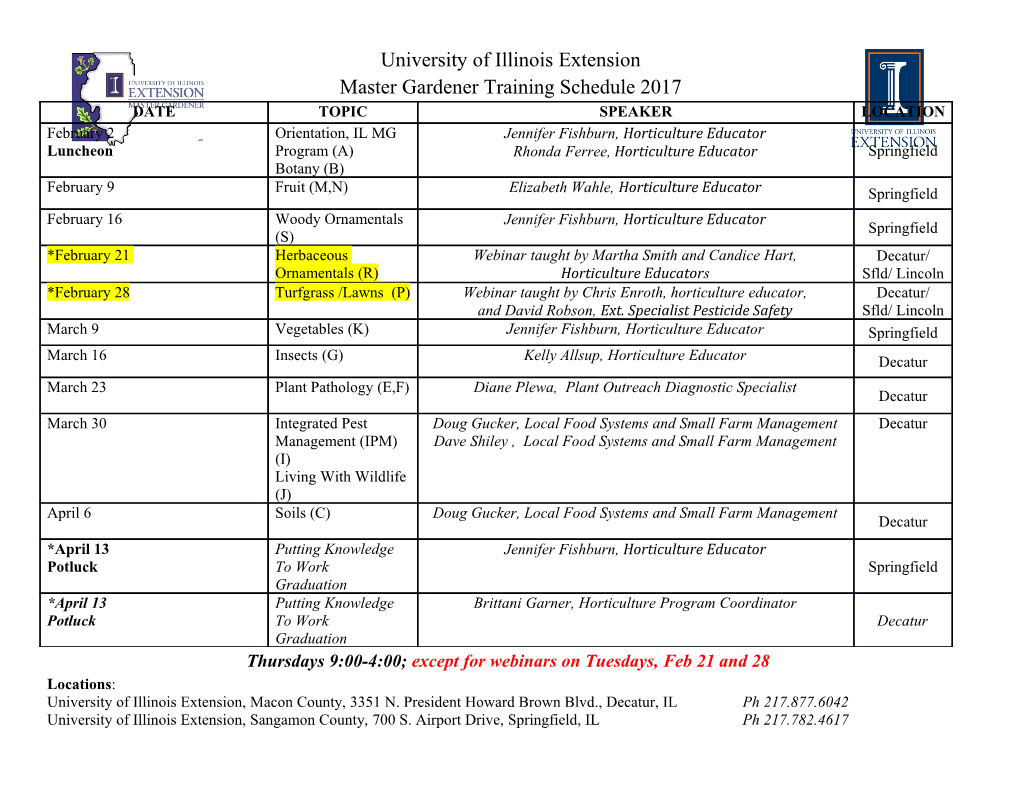
University of Illinois at Urbana-Champaign ECE 445: Senior Design Laboratory Spring 2016 Design Review Electronic Bike Shifting Team 51: Peter Kowalczyk Teaching Assistant: Kevin Luong Katherine O'Kane Matthew Potok Contents 1 Introduction 1 1.1 Statement of Purpose . 1 1.2 Current Competitors . 1 1.3 Objectives . 1 1.3.1 Goals/Benefits . 1 1.3.2 Functions/Features . 1 2 Design 2 2.1 Block Diagram . 2 2.2 Schematics . 3 2.2.1 User Input Subsystem . 3 2.2.2 Shift Subsystem . 4 2.3 Block Description . 5 2.3.1 Summary . 5 2.3.2 User Input Subsystem . 5 2.3.2.1 Microcontroller (ATtiny84) . 5 2.3.2.2 Battery (Sparkfun Polymer Lithium Ion) . 5 2.3.2.3 User Input (Buttons) . 5 2.3.2.4 Bluetooth Module (RN-42) . 6 2.3.3 Shifting Subsystem . 6 2.3.3.1 Microcontroller (ATtiny84) . 6 2.3.3.2 Battery (EC Tech YN-025) . 7 2.3.3.3 Servo (JX-Servo 5512MG) . 7 2.3.3.4 Accelerometer (Memsic 2125) . 7 2.3.3.5 Bluetooth Module (RN-42) . 7 2.3.3.6 Cable . 8 2.3.3.7 Derailleur . 8 2.4 Hardware . 8 2.5 Software . 11 2.5.1 User input subsystem . 11 2.5.2 Shift subsystem . 12 2.6 Calculations, Simulations, and Experiments . 12 2.6.1 Power Consumption . 12 2.6.1.1 User Input Subsystem . 12 2.6.1.2 Shift System . 12 2.6.2 Accelerometer Experiment on Test Bike . 13 3 Requirements and Verifications 14 3.1 User Input Subsystem . 14 3.1.1 Microcontroller [2.5 points] . 14 3.1.2 Battery [2.5 points] . 15 3.1.3 Bluetooth Module [6 points] . 16 3.2 Shifting Subsystem . 17 3.2.1 Microcontroller [5 points] . 17 3.2.2 Battery [5 points] . 17 3.2.3 Servo [17 points] . 18 i 3.2.4 Accelerometer [6 points] . 18 3.2.5 Bluetooth Module [6 points] . 19 4 Tolerance Analysis 19 5 Cost and Schedule 21 5.1 Cost Analysis . 21 5.1.1 Labor . 21 5.1.2 Parts . 21 5.1.3 Total . 21 5.2 Schedule . 22 6 Safety Statement 22 6.1 Battery Safety . 23 7 Ethics 23 References 24 List of Figures 1 Block diagram . 2 2 User input subsystem schematic . 3 3 Shift subsystem schematic . 4 4 Servo mount in isometric view . 9 5 Servo mount in exploded view . 9 6 Servo mount from bottom view . 10 7 Servo mount location . 10 8 Direct rear derailleur drive mechanism . 11 9 Plot of accelerometer experiment with x-axis perpendicular . 13 10 Plot of accelerometer experiment with x-axis parallel . 14 11 Lever arm length . 20 List of Tables 1 User input microcontroller I/O . 5 2 User input Bluetooth I/O . 6 3 Shift microcontroller I/O . 6 4 Shift accelerometer I/O . 7 5 Shift Bluetooth I/O . 8 6 User input subsystem battery specs . 12 7 Power consumption of user input subsystem . 12 8 Shift subsystem battery specs . 12 9 Power consumption of shift subsystem . 13 Assorted requirements and verifications tables . 14 10 Cost of labor . 21 11 Cost of parts . 21 12 Total cost . 21 ii 13 Schedule . 22 iii 1 Introduction 1.1 Statement of Purpose Electronic gear shifting systems have long been an expensive upgrade to their older mechanical counterparts. Currently, only professional racing cyclists have the funds to invest in electronic gear shifting, which have significant advantages compared to mechanical shifting. For example, programming can compensate for poor adjustment and ensure better shift quality. The system can self-calibrate, so there would be fewer adjustments. The electronics, when sealed, are not affected by the elements; whereas mechanical systems rely on cables that must remain exposed. Electronic systems age at a slower rate too, since firmware can be simply updated. Also, wireless communication allows users to have multiple shift points to increase ergonomics. Despite these advantages, currently no retrofittable high-performance economical wireless pack- age exists. With our product, both casual cyclists and serious athletes without sponsor funding will be able to enjoy reliable biking without the hassle of maintenance. 1.2 Current Competitors In traditional mechanical systems, it has been found that slightly overshooting the targeted gear and returning results in the best quality shift. Unfortunately, due to mechanical limitations in the ratchets found in all modern shifter units, this overshoot-return technique can only be applied in one direction. Mechanical systems also rely on springs, and using cables to counter the natural rest state of these springs. This becomes particularly problematic with large tooth count drops in front shifting. In essence, when shifting from the large front chainring to the small front chain ring, a large length of chain is released. The rear derailleur uses a spring to wind back its pulley cage to \soak" up this excess chain length in an effort to restore tension to the chain. The spring often pulls very hard and ends up \throwing" the chain off the front chainrings. At least in the Shimano Di2 system, the entire derailleur is motorized; there is no dependence on cables. Motors can be effortlessly configured to apply this overshoot-return technique in both directions. Furthermore, the rear derailleur pulley cage spring is replaced with a motor to gently (instead of suddenly) restore tension to the chain. The Di2 system also permits the addition of extra shift buttons to be placed in convenient places, such for sprinting and for climbing. Of the main three competitors of shifting componentry, Shimano, Campagnolo, and SRAM, only SRAM has released a wireless version. 1.3 Objectives 1.3.1 Goals/Benefits • Little to no maintenance/adjustments required, especially in adverse conditions • Equal or better shift quality to average mechanical system • Improved ergonomics • Reliable performance 1.3.2 Functions/Features • Automatic trimming: the derailleur cage adjusts automatically to prevent chain rub against the cage, but still maintain the desired gear ratio 1 2.1 Block Diagram 2 Design ) • • • • • 42) - Shifter buttons only affect user's ownBattery bike level and not indicator any otherAt nearby least electronic shifting 100 systems hoursRetrofittable of package: battery the life, system whichuntil will is a work comparable shift with to is most competitorsSuccessful determined existing shift to derailleurs be confirmation successful system: using a closed feedback loop, the derailleur will move Power Sparkfun Polymer (RN ( Lithium Ion Bluetooth module module Bluetooth Power Connection Input/Output Connection Bluetooth Mechanical Connection User InputSystem (ATtiny84) (Buttons) User Input Microcontroller Figure 1: Block diagram 2 ) ) Servo Servo 551MG ADXL362 Cable - ( (ATtiny84) JX Derailleur ( Accelerometer Microcontroller stem (Rear Derailleur) (Rear stem ) 42) - 025 - Power EC Tech (RN YN ( Shifting Sy Bluetooth module module Bluetooth 2.2 Schematics 2.2.1 User Input Subsystem Figure 2: Circuit schematic for user input subsystem 3 2.2.2 Shift Subsystem Figure 3: Circuit schematic for shift subsystem 4 2.3 Block Description 2.3.1 Summary Our system will be split into two parts: a user input subsystem and a shifting subsystem. The former subsystem will handle user input and transmit it wirelessly via Bluetooth. The latter subsystem will receive the Bluetooth packets and control a servo to shift the rear derailleur. Each subsystem will be powered by its own separate battery. More details on the individual subsystems and their parts can be found below. 2.3.2 User Input Subsystem 2.3.2.1 Microcontroller (ATtiny84) The microcontroller collects user input through button presses and forwards the data to the Bluetooth module. It will also incorporate a small circuit to measure the voltage of the battery and set three LEDs' statuses accordingly. The microcontroller can be powered anywhere from 2.7 V to 5.5 V. [1] The current iteration of the circuit schematic assumes that the microcontroller will be powered with 5 V; however, if during testing it is found that 3.3 V is sufficient, then the design will changed appropriately. This will eliminate the need to include the level shifting circuits between the Bluetooth module and the microcontroller. Pin # Function Connection 1 VCC +5 V 2 TX, serial.
Details
-
File Typepdf
-
Upload Time-
-
Content LanguagesEnglish
-
Upload UserAnonymous/Not logged-in
-
File Pages28 Page
-
File Size-