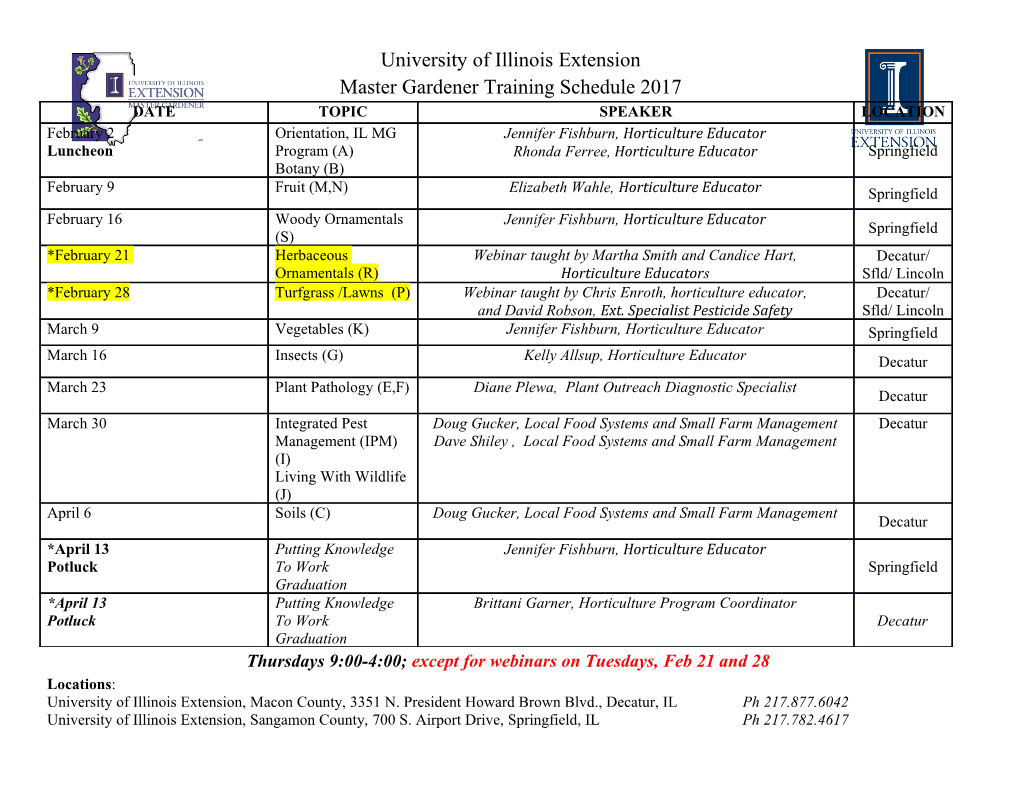
Turning Scrap into New Steel So long as there is a ready supply of scrap steel and enough electrical power, an electric arc furnace can be located anywhere RAYMOND R. SHEPARD In this, the third of a four-part series, the author provides an overview of the electric arc furnace (EAF) process and how it is used to make low-carbon and specialty steels. The capital required to start a traditional, comprehensive steel mill is extraordinary. Because of the economics facing the steel industry today and the fact EAFs can directly accept scrap, electric arc furnaces are emerging as a potential solution for steel production in the United States. Inspectors will benefit from a basic understanding of this process. The next issue will detail the continuous casting process and the rolling of steel. tilization of the electric arc furnace (EAF) for steel pro - duction has dramatically increased during the last thirty Uyears. Although we may think of the process as new, it has been in existence about one hundred years. Initially, factors such as cost, availability of electricity, and technological issues relegated the process to small batches of steel or for the pro - duction of specialty steels. After sixty years, the process and economics evolved to where it was economically feasible to use EAFs on a large scale. The early 1970s saw the EAF process take hold, and the proportion of steel produced by this process has continuously increased. At age 23, Paul Louis Heroult became famous as the codis - coverer of the electrolytic process for aluminum production. Fig. 1 — Sorted scrap is used to charge EAFs. Some furnaces Aluminum had been a very expensive metal to produce, but the are able to accept 100% scrap, making EAFs efficient recyclers. new process made it available on an industrial scale for the first Small scrap is usually used first to protect the refractory material time. Heroult’s work with the electrolytic process laid the foun - from damage by larger pieces. dation for experiments he performed to develop the electric arc furnace, and a few years later, around 1900, the first EAF was Today, EAFs recycle millions of pounds of scrap steel in the pro - produced. The first furnaces were very small, having no more duction of low-carbon steel and high-quality alloy steel and stain - than a few yards capacity. Heroult eventually came to the United less steels. States and worked to establish a few EAFs here. He saw great potential for this process and worked diligently in an attempt to Steelmaking with an Electric Arc Furnace see it gain a foothold in the steelmaking industry. Due to eco - nomic factors, he never saw his dream of massive EAF steel pro - The EAF is a stout, round vessel. Large carbon electrodes duction come to fruition during his lifetime and his discovery of are lowered from above the vessel until they almost touch the the electrolytic process for aluminum overshadowed his work in metal. An electric arc is then initiated that delivers significant steel until after his death. heat input. Operating at voltages in the range of 100–600 volts, The EAF process was ahead of its time. However, economics and 20–80 kA (AC furnaces), an EAF consumes enough elec - change. Enormous capital is required to start a conventional, tricity to power a small town. integrated ironworks for producing pig iron and the manual To put the amperage (heat) in perspective, it is roughly the labor necessary is staggering. The EAF gained a foothold equivalent of 670 welders, using E7018 electrodes, striking arcs in because of its lower labor costs and ability to process scrap the same place at the same time. In fact, the process is similar to a directly. Processing scrap meant an EAF did not have to be shielded metal arc welding power source set up to perform air car - located near a blast furnace for the delivery of pig iron but bon arc gouging, albeit on a much more massive scale. The trans - instead could be located anywhere that had a supply of scrap former produces high amperage that is delivered via cables to the and the proper electrical generating capacity. The term “mini carbon electrode. The electrode melts the steel it contacts, but mill” was coined to describe small EAFs that started to appear instead of blowing the steel away as in air carbon arc gouging, the in areas that were not traditional steel production regions. furnace holds and controls the molten steel. RAYMOND R. SHEPARD ( [email protected] ) is Quality Specialist/Training Coordinator, Kakivik Asset Management, Anchorage, Alaska. SPRING 2004 • 27 assembly are then moved back into place. Actuation may be accomplished through the use of hydraulics or electric motors and cables. Charging the furnace may take several buckets of scrap — Figs. 1, 2. To reduce downtime, several processes have been developed where scrap is fed to the furnace continuously or in increments, eliminating the need for bucket charging. These systems save money as there is no off-time during which the furnace is not producing steel. In the Consteel Process, scrap is fed to the EAF though a conveyor. The off-gas from the furnace is directed over a sealed portion of the conveyor. This off-gas preheats the scrap and increases the efficiency of the EAF process. Initiating the Arc When the arc is first initiated, there is an explosion of sound. The arc is initially unstable as it dances around the assorted scrap. Scrap in direct contact with the arc is instantly melted into liquid that runs through the scrap to the bottom of the furnace. The electrodes are slowly lowered through the scrap, melting a hole as they go, a step called the bore-in period. Once a suffi - cient pool of molten steel has formed beneath the electrodes, the arc stabilizes above the liquid bath. Operators then may increase the current applied to the furnace. The remaining scrap melts as it contacts the ever-increasing molten bath. The arc between the electrode and the molten metal can reach as high as 15,000°C at its hottest region. Depending on the current applied and the arc hold-off length, the arc may be Fig. 2 — As shown here, molten pig iron can also be used to up to approximately six inches across and one foot long. The charge electric arc furnaces. EAF vessel is liquid cooled. Heat is introduced to the furnace at such a fast rate the differential expansion rates of the refractory material and the external steel structure would cause premature Supplying Power failure of the refractory material. The outside skin of the vessel is made of segmented steel panels. At points where heat damage Primary power from electrical utilities is generated in three would be severely detrimental, water-cooled copper panels are phases. This means there are three conductors, 120 degrees out used instead. Water cooling removes heat content from the fur - of phase with each other, providing electricity to the EAF. nace, but reduces expansion of the EAF. This reduction in Electricity moves through the grid at a high voltage and low expansion and contraction during furnace cycles increases the amperage. Amperage for this process is synonymous with heat. life of the refractory material and the frame. A power system designed to carry high amperage would have to One might initially think an electric furnace solely derives its use massive conductors and would not be cost effective. The heat energy from electricity; but that is not correct. An EAF fur - EAF must convert high-voltage, low-amperage power into high- nace derives its energy from a complex interaction of electrical amperage, low-voltage power. This is done in the transformer and chemical energy. An oxygen lance may be a part of the EAF room adjacent to the EAF. process. The introduction of oxygen over the heat allows carbon A step-up transformer changes the low amperage to high- in the molten steel to combine, forming CO. This exothermic amperage power. A transformer is actually a simple electrical reaction adds heat to the melt and helps reduce the required device consisting of a coil of a number of predetermined turns current supplied to the furnace. Since a high level of low-carbon and an inner iron core that may be moved up or down the inte - scrap steel is utilized in the charging of the furnace, carbon may rior of the coil. Power is transferred from the coil to the core via actually be added to the melt. The use of oxygen at levels high - induction. The higher the number of coils, the higher the er than necessary for oxidation to occur significantly reduces amperage output. Thus, the heat input of all three electrodes the amount of current supplied to the furnace. High oxygen lev - can be independently controlled. els do have a side effect though. Carbon monoxide and nitrous Typically there are three transformers, one for each leg of oxide are created, and these gases must be collected and treat - power. The high-amperage current is brought to the EAF ed through a fume system before being released as a benign gas through three massive, liquid-cooled cables. These cables or into the environment. bus bars carry the current out of the transformer room and Electrodes are made of graphite (carbon) and are typically across a movable arm to the top of the oven. The arm assembly more than 20 inches in diameter. The electrode is consumed can weigh up to 20 tons. Care must be taken to not induce cur - through sublimation at the electrode tip, and through oxidation rents in adjacent structural support members, as the intense along its heated sides.
Details
-
File Typepdf
-
Upload Time-
-
Content LanguagesEnglish
-
Upload UserAnonymous/Not logged-in
-
File Pages3 Page
-
File Size-