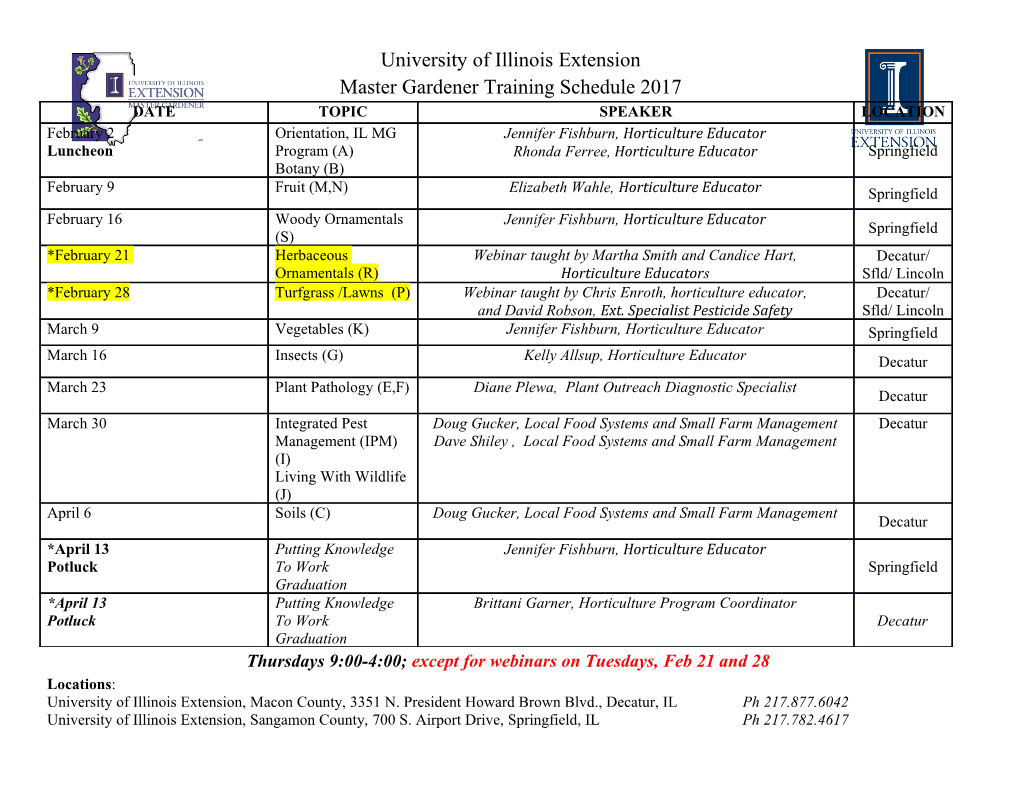
Article citation info: 87 Krol O, Sokolov V. Research of modified gear drive for multioperational machine with increased load capacity. Diagnostyka. 2020; 21(3):87-93. https://doi.org/10.29354/diag/126026 ISSN 1641-6414 DIAGNOSTYKA, 2020, Vol. 21, No. 3 e-ISSN 2449-5220 DOI: 10.29354/diag/126026 RESEARCH OF MODIFIED GEAR DRIVE FOR MULTIOPERATIONAL MACHINE WITH INCREASED LOAD CAPACITY Oleg KROL, Volodymyr SOKOLOV Volodymyr Dahl East Ukrainian National University, Department of Machinery Engineering and Applied Mechanics, 59-a Central pr., Severodonetsk, 93400 e-mail: [email protected] Abstract The presented work is devoted to the improvement of spur gears of the reduction drive for metal-cutting machines according to the criterion of load capacity. A feature of this article is the creation of such a constructive solution, which is aimed at finding a compromise between reducing contact loads in the engagement zone and increasing the complexity and labour intensity of the manufacturing gears process. A procedure for accelerated creation of 3D models of a gear drive and its components using the specialized software application “Shafts and Mechanical Transmissions-3D” in the environment of integrated CAD system KOMPAS-3D is proposed. A study of a new cylindrical gear transmission design with a longitudinal generatrix of axoids, confirmed by the corresponding patent solution is realized. A calculation form for the practical design and manufacture of a new design cylindrical gear is proposed. Keywords: cylindrical gear transmission, machine gear drive, axoid generatrix, 3D model, load capacity 1. INTRODUCTION involves the use of conventional two-stage and planetary gears. Based on the aggregate-modular principle, The competitiveness of multioperational multioperational machine tools (MT) of various machines is primarily associated with factors: layouts are created [1-3]. At the same time, a productivity, reliability and accuracy. At the same limited group of normalized nodes is developed and time, reliability is one of the main requirements specialized multioperational machines are built made by consumers and often serves as the main from them, which most fully correspond to criterion for assessing quality. technological tasks. The layout of the machines is Productivity and reliability of machine drives distinguished by the location of the spindle, the are often limited by the smooth operation of pinion main motion drive in space, the relative position of and gears. Therefore, the issues of improving the the main nodes. reliability, load capacity of the gears of the The main motion drive occupies a special machine's main motion drive due to the position in the structure of MT. They should improvement of design and technological solutions provide a high-productivity performance of various are relevant. operations when changing the rotation frequency in a wide range [4, 5]. In machine tools, a spindle with 2. LITERATURE REVIEW a cone of 40 – 5000 ... 7000 min-1 and the engine power of the main drive is associated with the In [7-9], it is noted that, at the initial stages of dimensions of the table. In medium-sized machines the research, it is necessary to implement a search with a table width of 500 ... 800 mm is 11 ... 15 for the toolkit to describe the contour of the teeth kW. Moreover, the speed of the working feed lateral surface of spur and bevel gears. Such a reaches 8000 ... 10000 mm/min, the speed of fast description will be the basis for obtaining optimized movements 10 ... 12 m/min [6]. contact conditions in a wide range of gear One of the most common options for the main transmission. Important parameters include groove motion drive of machines is an option with an profile parameters, which are largely determined by alternating current motor equipped with a frequency the longitudinal generatrix shape of the pinion and converter and gearbox based on 2-3 mechanical wheel axoid. gears (various types of gears), to increase the range It is also important to equip the production of of rotational speeds and torque. This type of gears with appropriate software for CAM systems. reduction drive provides high torque during Promising in this regard is the software Gleason 5- roughing and retains the possibility of high-speed axis Gear Studio (G5S) [7] company Gleason processing at speeds of about 104 rpm. The standard Corporation. These specialized programs are configuration for most machines with a 40th cone intended for profiling the tooth lateral surface, 88 DIAGNOSTYKA, Vol. 21, No. 3 (2020) Krol O, Sokolov V.: Research of modified gear drive for multioperational machine with increased load capacity evaluating the contact pattern and preparing the Based on the analysis of the problem under corresponding control programs for 5-axis CNC consideration, improving the efficiency of various machines and machining centres. To make this types of gears, we statement of the problem: technology truly practical, each operator, in just a To develop a modernized gear design of the few simple steps and minimal knowledge about the machine reduction drive which implements a design of the gearbox, will be able to automatically compromise between increased reliability and generate the optimal program for machining parts sophisticated manufacturing technology on modern and 3D models of gears, based on which a control CNC machines. program for processing them is developed. To achieve this goal, the following tasks are According to [8], one of the main goals is to proposed: create a working 3D model for analyzing contact 1. To develop 3D models of the main motion drive geometry, visual identification, and evaluating the for multi-operational machines in the KOMPAS- relationships between the set of tooth geometric 3D CAD environment using the specialized parameters. The toolkit of the designer’s tools application program “Shafts and Mechanical should include a method for creating a three- Transmissions-3D”. dimensional model of the gear in the corresponding 2. Explore and create a new design of the gear integrated CAD systems [8-10]. transmission with a modified shape of the At the same time, the increase in reliability longitudinal axoids generatrix of the pinion and achieved by constructive methods often conflicts wheel. with technological improvements. Thus, within the confines of the JSME RC-268 committee, a new 3. METHOD OF 3D MODELING Invo-Planar [11] bevel gear was developed, the MULTIOPERATIONAL TOOLS tooth flank of which is flat, whose transverse tooth GEARBOXES DRIVE profile is a straight line. Processing the simplified contour of the tooth As the object of research, a multi-operational lateral surface by grinding in one pass allows you to milling-drilling-boring machine with a six-spindle reduce machine time for a standard gear contour by turret was selected. Increasing the level of more than 10 times. Moreover, the lateral surface of complexity of projects in machine tool the tooth is much smoother than the curved lateral manufacture, the creation of competitive designs surface of the tooth formed by many trajectories of involves the widespread use of various computer- the tool cutting blades. On the other hand, the aided design systems. In the technology of the progress of machine equipment, 5 coordinate design process, the procedures for constructing 3D centres makes it possible to accelerate the models and parametric representations of parts and production of complex contours of the tooth lateral assembly units are important. surface. So, on the 5-axis Gleason Heller machine, The research of the main structural with the help of the CAM “Heller uP-Gear [7], characteristics of the machine drive is provided by gears are machined with the optimal geometry of the corresponding 3D modeling toolkit in integrated the tooth flank and the contact pattern. As a cutting CAD/CAM/CAE KOMPAS-3D [14-18], in which a tool, insert disk knives are used for roughing, semi- three-dimensional model of the machine reduction finishing and final gear cutting operations. drive has been developed (Fig. 1). Another aspect, from the standpoint of the In the process of creating this model, the latest criterion of contact stresses, and therefore functionalities of CAD KOMPAS and specialized reliability, it is rational to increase the length of the applications were used. When developing such teeth working contact, which gives an increase in complex parts as the bed housing with a gear drive the load capacity of the gear transmission. The (speed gearbox) and the housing of a six-spindle problem of the operational aspect associated with a turret, specialized CAD application libraries were decrease in the process of working the contact used. It is significantly improved the process of length of the teeth in the longitudinal direction geometric modeling. Using the Artisan Rendering (especially at high cutting speeds) drew attention photorealistic image module integrated into [12]. This phenomenon leads to a decrease in the KOMPAS forms the corresponding design and length of the loaded tooth region and, as a result, to understanding of the machine design [19]. the risk of excessive contact stress. The author The machine under consideration belongs to the considers compensation methods for these class of specialized machines of the 2nd standard mechanical deviations so that the load on the gear size, which are used in small-scale and series wheel surface is evenly distributed under normal production and are intended for multi-operation operating conditions. A generatrix of the single or machining of complex profile products from steel, double helix type is proposed for describing the cast iron, light and non-ferrous metals. The side surface of a wheel tooth to increase the contact machine is equipped with an automatic tool length. Another constructive option for increasing changer, which is carried out by turning the six- energy efficiency by the example of differential spindle turret to the desired position according to mechanisms was proposed in [13].
Details
-
File Typepdf
-
Upload Time-
-
Content LanguagesEnglish
-
Upload UserAnonymous/Not logged-in
-
File Pages7 Page
-
File Size-