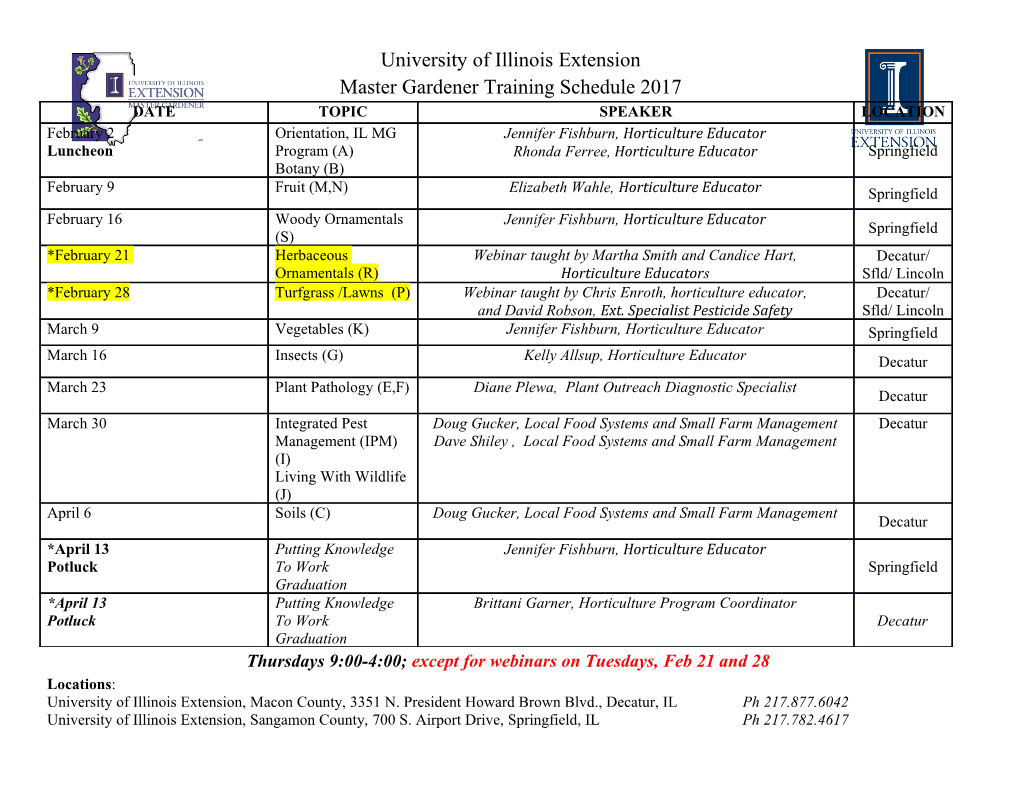
PRECONCENTRATION John Chadwick examines Cutting waste the latest in gravity techniques, ore sorting and magnetic separation to raise separation efficiency and reduce concentration costs “Sensor based automatic ore sorting technology. In bulk tests a very high waste The huge Natalka gold project, owned by Polyus, includes a three-stage gravity circuit; by technologies are used to efficiently remove reject rate of 92.2% was achieved with no gold far the world’s largest – with no less than 52 waste and sub marginal grade material from detected by assay in the waste (98.1% recovery centrifugal gravity concentrators, with sizes up crushed and screened run-of-mine (ROM) ore, assumed based on assay detection limit). As to 42 in. There are multiple concentrators from the two world leaders - FLSmidth’s Knelson producing a coarse (typically 10 mm) upgraded nearly 100% of the gold was recovered, a high > brand and Sepro Mineral Systems’ Falcon preconcentrate at an early stage in the mineral degree of liberation of mineralised quartz reef brand processing circuit. This avoids additional energy from gangue presumably exists at particle sizes intensive downstream processing of this between 25 mm and 60 mm. rejected component of the ROM feed, leading to “The financial modelling confirms robust doubled with ore sorting, from a bulk ROM lower unit operating costs and reduced tailings economics for the project. The base case grade of 0.8 g/t to a mill feed grade of 1.93 g/t disposal volumes.” These are comments from modelling of this potential operation indicates The flow sheet assumes 30% of the crushed and Tony Parry and G van Wyk of Steinert Australia that the grade of plant feed can be more than screened stockpile tonnage prior to sorting is - in their paper Upgrading Low-grade Gold Ore Stockpiles by Preconcentration Using Ore Sorting – an Assessment of the Economic Impact and Viability, presented at the 13th AusIMM Mill Operators’ Conference, October 2016. They reported on test work conducted on bulk low-grade gold ore Bullen stockpile samples from Central Norseman Gold that indicated high gold recoveries as well as high material rejection rates. “A financial model, based on these results, evaluates grade sensitivity and identifies a minimum stockpile grade for adequate financial returns.” The base case modelling estimates that the ex-stockpile grade (including the fines bypassed fraction) can be more than doubled through ore sorting and that the project will be highly viable with strong cash flow generation at stockpile grades as low as 0.7 g/t Au. The modelling enables the company to benchmark ore sorting options against stockpile reclaim and screening operations currently employed. They concluded that the “material is highly Process flow diagram (base case) for gold recovery from Central Norseman Gold’s low-grade gold ore amenable to preconcentration using XRT sorting Bullen stockpile 32 International Mining | MAY 2018 PRECONCENTRATION 25 mm fines which bypasses the sorter. The “Ore sorting technology is plant feed grade uplift, coupled with increasingly being adopted significantly reduced tonnage delivered to the across the gold mining processing plant, results in strong forecast cash industry in Western flow generation for this project and pre-tax Australia, with highly return on capital (IRR) estimated to be 144% encouraging results. over a three year life. The forecast capital Representative samples payback period is approximately six months. collected from the low-grade The financial modelling makes a strong case for stockpile located adjacent to further test work and a potential commercial the portal of the historical operation if stockpile grades of 0.7–0.8 g/t or Rothsay Gold Mine returned higher are confirmed (either through bulk an average stockpile grade mining or selective reclaim of the stockpile).” of 2.5g/t Au. This compares In another Parry-authored paper, with Kai favourably with previous Bartram, Business Development Manager sampling of this stockpile in Mining, Steinert Elektromagnetbau and Luis 2013, which returned results ranging from 2.7 – IMA Engineering Fast Conveyor Analyser (FCA) Loaiza Ampuero of Volcan Compa ia Minera, 4.1g/t Au. More importantly, the results used in sensing coarse primary crushed and/or fine crushed ore before it enters the grinding Upgrading of low grade silver-lead-zincň ore demonstrated that the Steinert Multi-Sensor mills and concentrator. It fast tracks ore grade stockpiles at Volcan Compa ia Minera SAA’s Ore Sorter was able to successfully reject the and type for optimum processing by delivering base metals operations in Peru,ň using sensor- barren ultramafic material located in the immediate feedback based ore sorting, the bulk ore sorting test work hanging wall of Woodley’s Shear.” undertaken on material from low grade Volcan TOMRA introduced its innovative multi- the difficult operating conditions or by ore open pit stockpiles is reviewed. channel laser sorting technology at AIMEX last characteristics. One of the important features of They conclude that “initial ore sorting test August. It said then that this new laser sorting ROM sorting technology is the major material work and subsequent bulk sorting trials have technology “will enable quartz and gold handling infrastructure required. The capital provided data to indicate that the Cerro de processes to achieve higher recovery, better expenditure can be substantial requiring good Pasco low grade stockpile is amenable to quality and more consistent sorting of quartz understanding of the sortability curve (grade- upgrade using XRT ore sorting. Although there material than can be secured using other sensor recovery curve) behaviour of the ore.” are additional significant losses to waste in the technologies. More detail on this was included The paper discusses one industrial case, ore sorting process, the financial analysis in IM’s annual gold recovery article in the where substantial amount of data measured confirms that the major reduction in total feed August 2017 issue. from the ore feed belt has been obtained. This tonnages to the concentrator and the lift in In the diamond sector, a TOMRA X-Ray data was then analysed for the grade recovery metal value per tonne of feed achieved by Transmission machine has been commissioned curves obtainable from that ore with sorting. introducing ore sorting transforms what would at its mine by Australia's Merlin Diamonds. By The XRF measurement used was the FCA be a marginal project into a highly profitable using this technology, it is expected that larger device from IMA Engineering. It is a specially project. The indicated capital payback is diamonds will be recovered than previously built version of XRF designed to operate with approximately six months and the ore sorting possible, as well as recovering low luminescing coarse material. The measurement was taken at project generates a forecast IRR of 207%, while diamonds. It replaces the conventional the main belt conveyor taking ore from the achieving a significant reduction in wet tailings concentrator and detects all diamonds including primary crusher to the stockpile. The crushed tonnages and environmental impact. This coated and low-luminescent as well as ore was about 80% -300 mm at a capacity of suggests that the company’s decision to build and preventing the crushing of larger diamonds. The 1,100-1,200 t/h. Measurement times were varied commission the ore sorting plant is a sound one.” Ector kimberlite pipe will be processed using from 30 seconds to a minute. Measurements There is a lot of this ore sorting test work the TOMRA XRT machine initially due to its high were obtained over several months. going on in Australia. EganStreet Resources proportion of large diamonds. The authors conclude that “the measured announces that it has identified an opportunity At this year’s SME conference, K. Heiskanen grade recovery curves between ore types and to optimise and significantly enhance the et al (colleagues from Outotec and IMA blasted block locations had different signatures. financial outcomes of its 100%-owned Rothsay Engineering) presented Developing real grade- Waste rock could always be detected from both Gold Project, located 300 km north-east of Perth recovery curves for sorting noting that “sorting high- and low-grade ores. High-grade ores in Western Australia, through the application of technology has advanced rapidly recently. Of the benefited from sorting but some disseminated state-of-the-art ore sorting technology. The two possibilities particle sorting has advanced low-grade ores were not amenable for sorting. Company has received highly favourable initial especially in introducing new sensors and the The results clearly point towards the benefits of results from ore sorting testwork completed on use of multiple sensors. The analysing and measuring the coarse mill feed for longer a low-grade stockpile from the historical computing lead times have also shortened. This periods of time at high sampling frequency underground mine at Rothsay, with the key has made it a viable technology option for many before the final technical and economic outcome that the use of a Steinert Multi-Sensor applications but not for the most important assessment of sorting can be made at any mine. Ore Sorter provides an opportunity to increase sorting task at a mine; the ROM ore. Bulk In the studied case there is a possibility to underground mine production (being fed to a sorting, however, has advanced in smaller steps, increase the metal stream to the products up to similar-sized process plant), reduce the impact even if the technology has the capability to 2-3%. It may well be, that the measurement of dilution from the main ore-hosting structure tackle the ROM ore and offers a high potential alone without sorting can give substantial at Rothsay, reduce life-of-mine processing costs to bring mines substantial economic benefits. operational improvements by enabling better and substantially enhance project economics.
Details
-
File Typepdf
-
Upload Time-
-
Content LanguagesEnglish
-
Upload UserAnonymous/Not logged-in
-
File Pages8 Page
-
File Size-