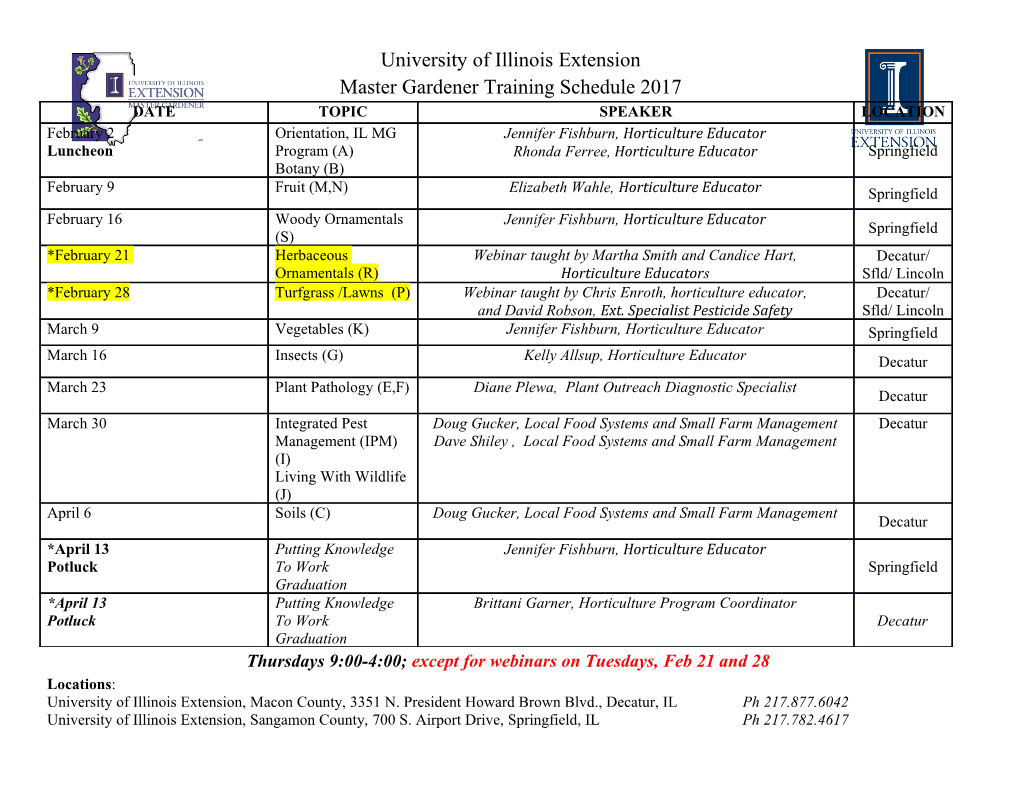
Discrete element modeling— A promising method for refractory microstructure design efractory materials are required to Rkeep their structural stability when subjected to extreme mechanical and chemical environments. Thermal shock spalling, corro- sion, creep, and other complex phenomena may take place while using them. Therefore, mechanical behavior of refractory materials is of great interest. In recent years, researchers reported various technical problems and industrial challenges concerning refractory materials that are Credit: Moreira et al. not easily solved using conventional experimental methods. Thus, numerical computational tools emerged to better understand the physical problems and to analyze such complex conditions. The finite element method (FEM) is one of the most popu- lar approaches for studying thermomechanical problems. It is a numerical method that subdivides a large system into smaller, simpler parts for easier analysis through the use of a mesh, i.e., a geometrical representation of the domain of interest that comprises all elements to be analyzed. This technique is suitable to solve elliptic and parabolic prob- lems, and it is not restricted to linear or isotropic cases. The mesh makes it geometrically flexible and able to model complex domains. Additionally, this technique is easily implemented as computer codes and is also robust because most mathematical problems can be stated as a variational problem where FEM can be applied. However, one of the main disadvantages to FEM is the dif- ficulty of analyzing microscopic situations and material discontinui- ties, as the equations associated with the problem are derived based on a continuous materials assumption.1 Trying to overcome this issue, researchers developed the FEM remeshing technique, which solves complex problems by updating the mesh to consider discontinuities, but this procedure can affect 2 3 By M. H. Moreira, T. M. Cunha, M. G. G. Campos, its performance. Möes et al. developed the extended finite ele- M. F. Santos, T. Santos Jr., D. André, and V. C. Pandolfelli ment method (XFEM) to model fracture and interfacial problems, using discontinuous basis functions on the nodes where cracks may occur. The advantage of this procedure is that it is not necessary to Discrete element modeling is a tool with great potential for update the mesh. Nevertheless, this method also has a high com- putational cost and the study of complex features, e.g., crack initia- modeling refractory materials—if challenges to applying tion at multiple locations, is still an ongoing research.1 DEM for continuous problems are overcome. In contrast to FEM, meshfree methods have been studied, developed, and proposed as an alternative approach. Some examples are the smoothed-particle hydrodynamics (SPH) and 22 www.ceramics.org | American Ceramic Society Bulletin, Vol. 99, No. 2 Capsule summary MODELING DISCONTINUITIES CHALLENGES TO DEM A MANUAL FIX Discrete element modeling, which models DEM faces two challenges modeling continuous A manual calibration using Brazilian and interactions of discrete particles, can model problems: choosing a contact model between uniaxial compression tests results in a DEM microstructures with a large number of discon- particles and finding corresponding microscopic model capable of reproducing the mechanical tinuities, such as refractory materials. parameters that describe a material’s macro- behavior of a continuous problem. scopic behavior. its modified approach (corrective SPH microstructures that have a large number improve the link between the material’s and discontinuous SPH),4 the moving of discontinuities, such as inclusions, microstructure (which has a large number least square (MLS),5 and the element- cracks, debonding, and porosity, which of discontinuities) with their macroscopic free Galerkin method (EFGM).6 These is the case of refractory materials. In properties during application.13 Such techniques aim to study a problem addition, the major advantage of DEM is approach can optimize the processing with a random distribution of nodes the likelihood of investigating both crack and applications of refractory materials, without a mesh or connection between initiation and propagation, as well as the increase their performance, and save time, them. Nevertheless, they are very time- phenomena of coalescence and bifurca- effort, and resources in the industry. consuming and may undergo several tion, which can be used to understand There are two major challenges to numerical issues, such as low accuracy and simulate the macroscopic behavior applying DEM for continuous problems: near the boundaries and difficulties to of the materials9 (Figure 1). the choice of the contact model between impose Dirichlet boundary conditions.1 Various studies used DEM for ceram- the particles and how to find the cor- Another approach to modeling dis- ics applications (continuous problems), responding microscopic parameters continuous problems is through discrete regarding problems related to compres- that describe the macroscopic behavior methods, such as molecular dynamics sion tests,10 crack initiation and propaga- of the material (the calibration step). (MD)7 and the discrete element method tion in alumina,11 and the effect of aver- The present work is based on previous (DEM).8 These methods differ from FEM age grain size on the toughness of alumi- research that proposed a straightforward because the body is not represented by a na ceramics.12 André et al.13 studied the approach to overcome such challenges.9 continuous mesh where constitutive laws Young’s Modulus of a borosilicate glass The aim of this study was to explore are obeyed but rather by a set of discrete matrix with alumina inclusion affected by the possibilities of applying discrete ele- bodies or particles that interact with its microcracks. Wang14 analyzed the fracture ment modeling as a tool for analyzing neighbors following contact or distant propagation in concrete to evaluate the mechanical tests of refractories. The interaction laws at the microscale. difference in strength due to aggregates results attained can lead to models that in Such interactions create emergent and aggregate/mortar interfacial transi- the future could help global key players properties that can be measured on a tion zone (ITZ), yielding insights concern- to overcome, for example, the challenges macroscale as an apparent property that ing the effect of the microstructure on its of evaluating the mechanical and thermal results from the multiple interactions at mechanical behavior. damage in steel plant installations, which the microscale. This possibility enables Nevertheless, DEM has not been are not easily developed experimentally. DEM to be a tool with great potential extensively applied to model commer- Thus, an alumina castable considering for modelling cracks and representing cial refractory materials, although it can Alfred’s grain size distribution was studied Credit: Moreira et al. Figure 1. (a) Schematic representation of features of a refractory material and its connection with DEM, (b) SEM micrograph of a spinel containing alumina castable refractory showing all multiple phases, pores, and microcracks. (TA: tabular alumina; CA6: CaO.12Al2O3; MA: MgAl2O4) American Ceramic Society Bulletin, Vol. 99, No. 2 | www.ceramics.org 23 Discrete element modeling—A promising method for refractory microstructure design FEM. Instead of considering the Each bond model is characterized by regions of interest as a continu- a set of variables, which are commonly um media, where known consti- referenced as micro (or local) param- tutive laws describe its behavior eters. Because the mechanical behavior in a grid (the domain’s mesh in of the whole structure is an emergent FEM), in DEM the domain of property that arises from the interaction interest is expressed by a set of of each element, two distinct scales are rigid spherical bodies that inter- separately considered: the macroscopic act following specific laws.1 (the scale of the material sample that will For the representation of be simulated and is represented in the Credit: Moreira et al. mechanical phenomena, DEM, model) and the microscopic (the discrete Figure 2. Schematic representation of the most common which originated as a tool for element scale), as seen in Figure 3a. cohesive bond models. Recreated from Reference 1. simulating naturally discrete The physical features of the whole problems such as granular sample are referenced as macroscopic with GranOO, an opensource discrete flow, powder compaction, and related properties, whereas the quantities related 15 element workbench. The calibration problems, can be of great benefit to the bonds and individual elements are process was carried out by an automatic when specifying laws of bonding the already mentioned microparameters. 9 algorithm developed by Andreá et al. and between elements.16 Although studies were conducted in by a manual calibration accomplished The bond between particles can be order to propose analytical relationships using the Brazilian and uniaxial compres- based on distinct models. The most com- between the set of micro- and macro- sion tests. The three-point bending test mon ones are the contact bond (simple parameters,17,18 there are no direct laws was used in a further validation step. spring) model, the dual spring model, that correlate the set of microparameters the parallel bond and flat joint models,16 and the experimentally measured proper- Materials and methods and the recently developed
Details
-
File Typepdf
-
Upload Time-
-
Content LanguagesEnglish
-
Upload UserAnonymous/Not logged-in
-
File Pages7 Page
-
File Size-