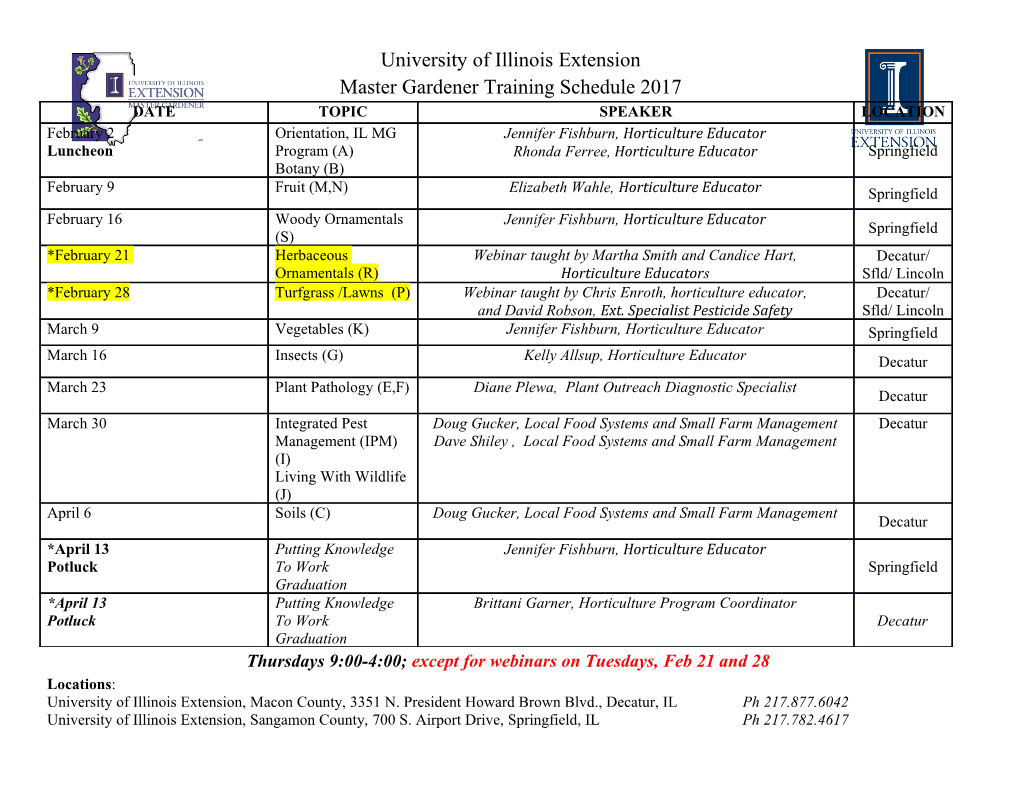
ADEQ ARK ANSAS Department of Environmental Quality Jerry McPherson, Manager ofFacilities Hino Motors Manufacturing 100 Hino Blvd Marion,PJR 72364 Dear Mr. McPherson: The enclosed Pennit No. 2070-PJR-6 is your authority to construct, operate, and maintain the equipment and/or control apparatus as set forth in your application initially received on 1212112009. After considering the facts and requirements ofA.c.A. §8-4-101 et seq., and implementing regulations, I have detennined that Pennit No. 2070-PJR-6 for the construction, operation and maintenance ofan air pollution control system for Hino Motors Manufacturing be issued and effective on the date specified in the pennit, unless a Commission review has been properly requested under Arkansas Department ofPollution Control & Ecology Commission's Administrative Procedures, Regulation 8.603, within thirty (30) days after service ofthis decision. All persons submitting written comments during the thirty (30) day, and all other persons entitled to do so, may request an adjudicatory hearing and Commission review on whether the decision ofthe Director should be reversed or modified. Such a request shall be in the fonn and manner required by Regulation 8.603, including filing a written Request for Hearing with the APC&E Commission Secretary at 101 E. Capitol Ave., Suite 205, Little Rock, Arkansas 72201. Ifyou have any questions about filing the request, please call the Commission at 501-682-7890. Sincerely, Mike Bates Chief, Air Division Enclosure ARKANSAS DEPARTMENT OF ENVIRONMENTAL QUALITY 5301 NORTHSHORE DRIVE / NORTH UTILE ROCK / ARKANSAS 72118-5317 /TELEPHONE 501-682-0744/ FAX 501-682-0880 www.adeq.state.ar.us ADEQ -------------------MINOR--S.OilRCE----------­ AIR PERMIT Permit No. : 2070-AR-6 IS ISSUED TO: Hino Motors Manufacturing 100 Hino Blvd Marion, AR 72364 Crittenden County AFIN: 18-00565 THIS PERMIT IS THE ABOVE REFERENCED PERMITTEE'S AUTHORITY TO CONSTRUCT, MODIFY, OPERATE, AND/OR MAINTAIN THE EQUIPMENT AND/OR FACILITY IN THE MANNER AS SET FORTH IN THE DEPARTMENT'S MINOR SOURCE AIR PERMIT AND THE APPLICATION. THIS PERMIT IS ISSUED PURSUANT TO THE PROVISIONS OF THE ARKANSAS WATER AND AIR POLLUTION CONTROL ACT (ARK. CODE ANN. SEC. 8-4-101 ET SEQ.) AND THE REGULATIONS PROMULGATED THEREUNDER, AND IS SUBJECT TO ALL LIMITS AND CONDITIONS CONTAINED HEREIN. Signed: li~ Mike Bates Date Chief, Air Division Hino Motors Manufacturing Permit #: 2070-AR-6 AFIN: 18-00565 Table ofContents Section I: FACILITY INFORMATION 4 Section II: INTRODUCTION 5 Summary ofPermit Activity 5 Process Description 5 Regulations 8 Total Allowable Emissions 9 Section III: PERMIT HISTORy 10 Section IV: EMISSION UNIT INFORMATION 11 Section V: INSIGNIFICANT ACTIVITIES 17 Section VI: GENERAL CONDITIONS 18 2 Hino Motors Manufacturing Pennit #: 2070-AR-6 AFIN: 18-00565 List ofAcronyms and Abbreviations A.C.A. Arkansas Code Annotated AFIN ADEQ Facility Identification Number CFR Code ofFederal Regulations CO Carbon Monoxide HAP Hazardous Air Pollutant lb/hr Pound Per Hour No. Number NOx Nitrogen Oxide PM Particulate Matter PMIO Particulate Matter Smaller Than Ten Microns S02 Sulfur Dioxide Tpy Tons Per Year UTM Universal Transverse Mercator VOC Volatile Organic Compound --~-- -- -~ ~----------- ----~~--~~-~~---~-~------ ------- ~----- -~_ .. ~--~~--- 3 Hino Motors Manufacturing Permit #: 2070-AR-6 AFIN: 18-00565 Section I: FACILITY INFORMATION PERMITTEE: Hino Motors Manufacturing AFIN: 18-00565 PERMIT NUMBER: 2070-AR-6 FACILITY ADDRESS: 100 Hino Blvd Marion, AR 72364 MAILING ADDRESS: 100 Hino Blvd Marion, AR 72364 COUNTY: Crittenden County CONTACT NAME: Jerry McPherson CONTACT POSITION: Manager ofFacilities TELEPHONE NUMBER: 870-702-3037 REVIEWING ENGINEER: Amanda Leamons UTM North South (Y): Zone 15: 3895975.56 m UTM East West (X): Zone 15: 749657.00 m 4 Hino Motors Manufacturing Permit #: 2070-AR-6 AFIN: 18-00565 Section II: INTRODUCTION Summary ofPermit Activity Hino Motors Manufacturing U.S.A., Inc (Hino) operates an auto parts production facility located in Marion, Arkansas. With this de minimis modification application, Hino Motors is requesting permission to remove the thermal oxidizer associated with SN-02 and to redesign the dryer section ofSN-02 to reduce the heat rated capacity from 6.0 MMBTUIhr to 3.0 MMBTUIhr. Furthermore, Hino is requesting to transition to a new electrodeposition (ED) coating at SN-01 which is a lower VOC containing coating than previously used. As a result ofthese modifications, the net annual permitted emissions increased 0.8 tons ofmethyl isobutyl ketone and decreased for PMlPMIO, VOC, NOx, and CO. The predominant emission from the facility is VOC emissions resulting from various coatings applications at 45.3 tpy. Other emissions include particulate (PMIPMIO) emissions from grinding and welding operations, various emissions resulting from natural gas combustion at the coating dryers, and HAP emissions resulting mostly from the coating applications. Process Description The scheduled manufacturing operating time and production to meet the annual production goals is two (2) eight-hour (8-hour) shifts, five (5) days per week. Within a shift, the production operating time is 7.75 hours. This design production basis establishes the average hourly production and materials consumption rates for this application. For periods to catch up on production or to meet client demand shortfalls, it may be necessary to operate three (3) shifts per day and six (6) days per week. The potential 100% capacity operating time is considered to be the equivalent of24 hours per day, 365 days per year or 8,760 hour per year. There are no limits on annual hours ofoperation. Truck Parts Electro Deposition Coating Line Miscellaneous truck axle parts fabricated off-site will be cleaned, surface treated and painted in ·---------an-Etecuo Deposition Coating (ED Coating) line (SN-Ot).lne--degreasing and pretreamrent---­ operations utilize aqueous dip and rinse tanks with degreasers, surface conditioner, zinc­ phosphate treatment and inorganic toner solutions. There are no regulated emissions from these process steps. They are listed collectively in the insignificant activities list as Degreasing Operations (See Section V). After degreasing, the parts are ready for coating. The Electro Deposition Coating (painting) uses a two-component water borne coating of pigments and resin diluted with water in the coating dip tank. There the parts are coated with a 5 Hino Motors Manufacturing Permit #: 2070-AR-6 AFIN: 18-00565 low VQC, non-HAP coating. The coated parts then enter a natural gas-fired drying oven (SN-02 A, B, C) to complete the drying process. Upon exiting the oven, finished parts are ready for shipping. The oven has a heat input capacity of3.0 MMBTU/hr. Machining and Welding Processes The facility will manufacture front and rear differentials, front and rear axles and suspension parts (upper and lower, front and rear knuckle arms). The factory floor will have multiple lines and stations for machining, welding, treating, cleaning and assembly ofthe parts. Only the Welding Activities (SN-04) have any quantifiable emissions. Machining offront and rear knuckle parts is carried out in enclosed grinding machines using water with soluble cutting/polishing oil and additives. Manufacture ofa knuckle can involve machining, preparation, welding and assembly ofabout fifteen (15) different parts that go into a knuckle assembly. All welding stations are closed or hooded and connected to the welding exhaust system. The rear axle shaft process involves machining and heat treating. Enclosed machining prevents cutting solution mist that might be generated in the machine from being released into the work room. The heat treating operation is electric high frequency treating and quench with no emission release. The differential case lines involve enclosed machining. One line includes electric heat treating. The differential case and parts come together at the differential assembly line. Parts washed in the several aqueous washing machines are air dried after the hot water wash. There are two (2) rear axle housing lines involving machining and arc welding activities. The axle fabrication involves welding together the cast upper steel upper and lower halves ofthe housing and the attached parts and performing necessary machining ofsurfaces. The rear axle housing, shaft and differential come together in the rear axle assembly station. The axle painting activity is in this area. The welding activities carried out on the rear axle housing and the upper and lower, front and rear suspension arms are the only source of quantifiable emissions from these truck parts fabrication areas. All welding stations are in exhausted cabinets or utilize hoods connected to the plant welding exhaust system. This exhaust system will use two (2) fans located outside the southwest comer ofthe building to exhaust all ofthe welding stations in the plant. Welding uses gas metal arc welding wire with carbon dioxide and argon shielding gases. Rear Axle Paint Line After assembly ofthe rear axle housing, shafts, differential and other components, the assembled rear axle is prepared for painting on a conveyerized Axle Coating Line, and painted in two booths (SN-05a & SN-05b). For painting, the axles are hung on an overhead conveyor line to 6 Hino Motors Manufacturing Permit #: 2070-AR-6 AFIN: 18-00565 pass through the spray coating booths and the gas fired curing oven. All axles are painted using only one (l) black, waterborne coating. Paint application will be
Details
-
File Typepdf
-
Upload Time-
-
Content LanguagesEnglish
-
Upload UserAnonymous/Not logged-in
-
File Pages26 Page
-
File Size-