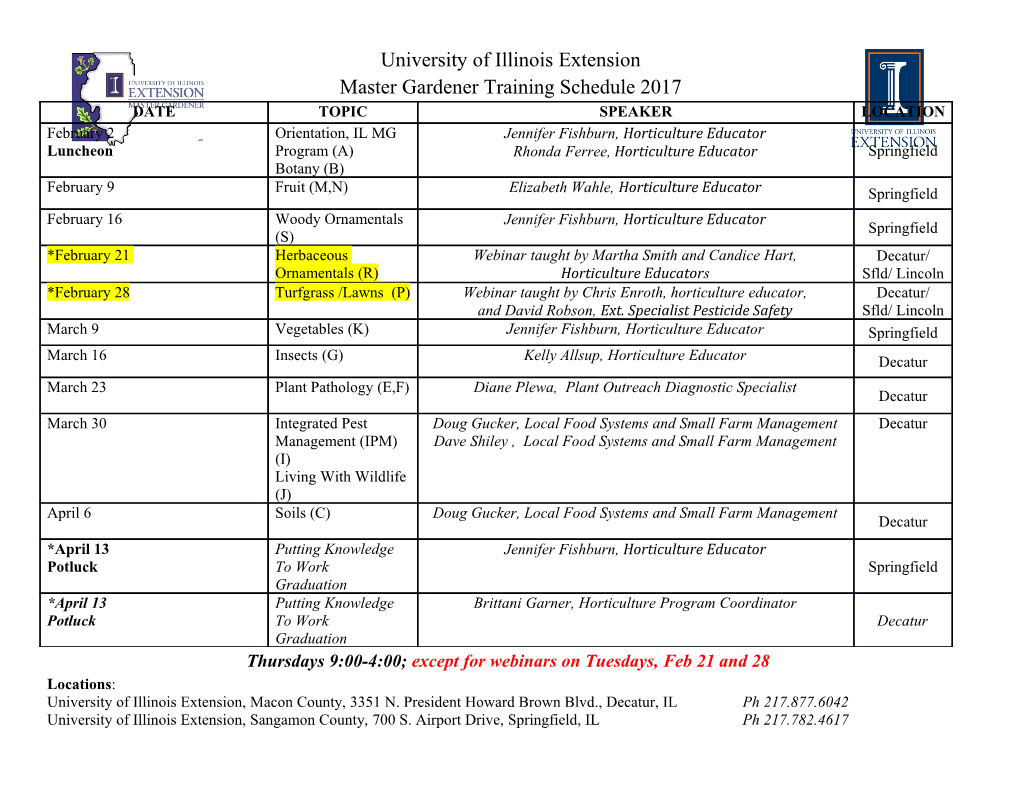
46th International Conference on Environmental Systems ICES-2016-119 10-14 July 2016, Vienna, Austria Versatile Thermal Insulation for Cryogenic Upper Stages M. Moser1 and W. Hoidn2 RUAG Space GmbH, Stachegasse 16, 1120 Vienna, Austria P. Delouard3 RUAG Space AG, Schaffhauserstrasse 580, 8052 Zürich, Switzerland and A. Tvaruzka4, M. Loche5 and U. Lafont6 European Space Agency ESA, Keplerlaan 1, 2201 AZ Noordwijk, The Netherlands Within ESAs future launcher preparatory program RUAG Space has developed a Versatile Thermal Insulation (VTI) system for cryogenic launcher upper-stages. The pneumatically deployable VTI system is self-sustained and mounted via interchangeable segments on the payload interface adapter. At this location the system is protected from environments on the launch pad and aerothermal loads during lift-off. On the interface adapter the VTI is independent from the upper stage, which in turn does not need to be modified for the insulation system. As the insulating VTI segments are adaptable in size the system can be designed to any cryogenic upper stage configuration. VTI is thus a viable upgrade kit for existing- and future launchers. In orbit VTI segments deploy on command through pressurization in a sequence that concludes in an insulating skirt covering the cryogenic stage. The entire deployment process is only controlled by pressure and built-in retainers made of hook/loop fasteners. Apart from the hold-down and release assembly no additional mechanism is needed for deployment. This approach reduces system complexity and leads to a mass below 80kg for a 75m2 covering VTI system. The deployment process has been successfully verified with a full scale, 1.5 meter by 5 meter, demonstrator model of one VTI segment. It was demonstrated that deployment is reliable and reproducible in real size and that stowing in rolled form is compatible with launch loads. Thermal analyses have shown that on a generic 4.4m upper stage the VTI system reduces heat input into the liquid hydrogen tank by more than 90% resulting in a strongly reduced fuel boil-off rate. Nomenclature AIT = Assembly, Integration and Test CAD = Computer Aided Design CFRP = Carbon Fiber Reinforced Plastic 1 Lead Systems Engineer VTI, Thermal Systems, RUAG Space GmbH, Stachegasse 16, A-1120 Vienna, Austria 2 Senior Systems Engineer, Thermal Systems, RUAG Space GmbH, Stachegasse 16, A-1120 Vienna, Austria 3 Senior Thermal Engineer, Launchers, RUAG Space AG, Schaffhauserstrasse 580, CH-8052 Zürich, Switzerland. 4 Mechanisms Engineer, TEC-MSM, Mechanical Engineering Department, ESA/ESTEC, Keplerlaan 1, NL-2201AZ Noordwijk, The Netherlands. 5 Thermal Engineer, TEC-MTT, Mechanical Engineering Department, ESA/ESTEC, Keplerlaan 1, NL-2201AZ Noordwijk, The Netherlands. 6 Materials Engineer, TEC-QTE, Product Assurance & Safety Department, ESA/ESTEC, Keplerlaan 1, NL-2201AZ Noordwijk, The Netherlands. CUS = Cryogenic Upper Stage ESA = European Space Agency FLPP = Future Launcher Preparatory Program GEO = Geostationary Orbit GH2 = Gaseous Hydrogen GHe = Gaseous Helium GN2 = Gaseous Nitrogen GMM = Geometrical Mathematical Model GSE = Ground Support Equipment GTO = Geostationary Tranfer Orbit HDRM = Hold Down and Release Mechanism LH2 = Liquid Hydrogen LOx = Liquid Oxygen MLI = Multilayer Insulation MMOD = Micro Meteorite or Orbital Debris PET = Polyethylene terephthalate SLI = Single Layer Insulation TMM = Thermal Mathematical Model TRL = Technology Readiness Level ULA = United Launch Alliance VDA = Vacuum Deposited Aluminum VTI = Versatile Thermal Insulation I. Introduction EDUCTION of propellant boil-off allows cryogenic upper stages to perform longer coasting phases with R multiple engine re-ignitions and thus improvement of overall launcher performance and payload orbital insertion flexibility. MLI has been shown to be an excellent barrier against incident thermal energy and in consequence an extremely effective thermal insulation system on cryogenic tanks. Several systems have been developed in recent years to further improve MLI performance at cryogenic temperatures allowing for increased- or even long duration storage of cryogenic propellants in orbit.1-4 However, MLI cannot be built robust enough to survive aerodynamic loads appearing during typical rocket launches. As a consequence it is common practice that thick layers of foam insulation are sprayed onto the external walls of launch vehicle cryogenic stages. These foams offer good environmental protection on ground but worse thermal performance than MLI in orbit and also tend to degrade upon launch vehicle ascent resulting in high fuel boil-off rates and strong restrictions in cryogenic upper stage (CUS) mission duration and utilisation flexibility. It is thus from highest interest to develop a system that supports increasing CUS performance by maintaining its properties during launch and ascent and in addition features the excellent insulation properties of MLI in orbit. As this increased performance is not needed on all missions, designing a stage to always comply with these long coasting or multi-ignition mission scenarios would result in reduced overall launcher performance due to increased mass penalty. Consequently, the main goal of the FLPP VTI project was the development of an add-on CUS insulation system which is to be applied only in cases required. The insulation shall be versatile in terms of applicability, adaptability to stage- or payload configuration and AIT constraints. The overall footprint i.e. the number of interfacing areas on the stage shall be minimal. With its expertise in developing advanced insulation products RUAG Space has been involved in studying VTI concepts since 2009. Based on a detailed requirements definition with industry three general approaches were identified for further investigation: Aerothermal Shroud Mechanically Deployable Cover Pneumatically Deployable System In course of a trade-off process, both, the Aerothermal Shroud and Mechanically Deployable Cover were discarded as they revealed major technical challenges and performance drawbacks. The former, a cylindrical shroud which covers MLI during launch, was shown to have high mass and that its thermal performance benefit largely depends on a compromise between mechanical stability and attachment design. The Mechanically Deployable Cover 2 International Conference on Environmental Systems would deploy in orbit but with the help of mechanisms and mechanical actuators. This deployment approach would thus result in large system complexity, and depending on the deployment method chosen, high mass penalty. Further, both systems require a number of interfaces which permanently have to be foreseen on the upper stage. The Pneumatically Deployable System on the other hand offers a number of advantages: it can be built with a low number of mechanisms and mechanical components it is of lightest weight of the investigated systems it can be stowed within a small volume. In combination, this results in a system with low complexity in transport, handling and integration and, based on the exceptional packing efficiency, provides the stage architect with a high degree of freedom for placement of the system on the CUS.5 These facts have also been recognized by ULA who have developed a sun shield for an Atlas CUS in cooperation with ILC Dover.4 There straight beams are stowed in an accordion pattern and pneumatically deployed using rigid end-fittings. Based on the above trade-off we have focused on the Pneumatically Deployable VTI System, which has been designed and developed in the frame of an ESA FLPP study since 2012. II. The VTI System A. Overview The Pneumatically Deployable VTI System was developed for a generic cryogenic upper stage with ø4.4m diameter and LH2 and LOx tanks. VTI was required to only cover the hydrogen tank. VTI consists of several segments of a deployable insulation which are attached on the external side of the payload interface adapter Versatile Thermal Insulation between payload and upper-stage cryogenic deployed tanks. For on-ground-operations, launch and ascent the system is protected against environmental hazards and aerothermal loads by encapsulation under the fairing. Upon fairing jettison and when the CUS has reached a stable coasting phase VTI is deployed pneumatically over the LH2 tank and Payload is, in its baseline configuration, designed to keep full functionality for up to 10 hours. With Cryogenic Stage further upgrades the system may however be designed for longer mission durations and utilized for solar sails, orbital propellant depots Figure 1. Illustration of VTI in Orbit or telescope sun shields. A principle illustration of the deployed VTI system covering the generic upper stage LH2 tank is presented in Figure 1. For the ø4.4m stage configuration 10 VTI segments, each 1.5m wide, are circumferentially attached to the payload adapter and are divided in groups of 5 so-called “inner” segments and 5 ”outer” segments. Outer segments, are mounted to the payload adapter an elevated (+Z, i.e. flight direction) position with respect to the inner segments. The VTI assembly in stowed configuration, mounted on the payload adapter, is shown in the CAD image Figure 2. Designed with a modular layout, each segment is self-contained, interchangeable and is composed of two major sub-systems: 1. Storage and Deployment Support System, which itself is composed of a. Storage and Release Subsystem it retains a VTI segment during launch and early orbital phases in rolled form of app. 200mm diameter.
Details
-
File Typepdf
-
Upload Time-
-
Content LanguagesEnglish
-
Upload UserAnonymous/Not logged-in
-
File Pages11 Page
-
File Size-