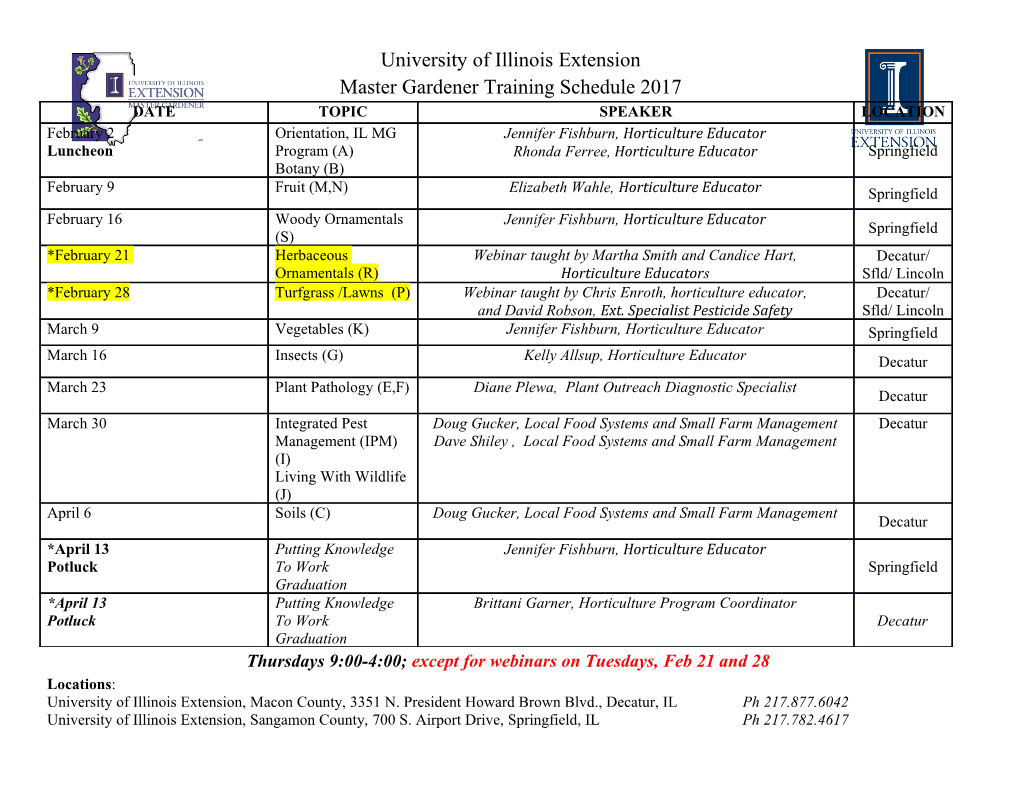
February 2000 • NREL/SR-540-27502 Ignition Assist Systems for Direct-Injected, Diesel Cycle, Medium-Duty Alternative Fuel Engines Final Report Phase I A.K. Chan Caterpillar, Inc. Peoria, Illinois National Renewable Energy Laboratory 1617 Cole Boulevard Golden, Colorado 80401-3393 NREL is a U.S. Department of Energy Laboratory Operated by Midwest Research Institute ! Battelle ! Bechtel Contract No. DE-AC36-99-GO10337 February 2000 • NREL/SR-540-27502 Ignition Assist Systems for Direct-Injected, Diesel Cycle, Medium-Duty Alternative Fuel Engines Final Report Phase I A.K. Chan Caterpillar, Inc. Peoria, Illinois NREL Technical Monitor: Keith Vertin Prepared under Subcontract No. ZAS-7-16609-01 National Renewable Energy Laboratory 1617 Cole Boulevard Golden, Colorado 80401-3393 NREL is a U.S. Department of Energy Laboratory Operated by Midwest Research Institute ! Battelle ! Bechtel Contract No. DE-AC36-99-GO10337 This publication was reproduced from the best available copy Submitted by the subcontractor and received no editorial review at NREL NOTICE This report was prepared as an account of work sponsored by an agency of the United States government. Neither the United States government nor any agency thereof, nor any of their employees, makes any warranty, express or implied, or assumes any legal liability or responsibility for the accuracy, completeness, or usefulness of any information, apparatus, product, or process disclosed, or represents that its use would not infringe privately owned rights. Reference herein to any specific commercial product, process, or service by trade name, trademark, manufacturer, or otherwise does not necessarily constitute or imply its endorsement, recommendation, or favoring by the United States government or any agency thereof. The views and opinions of authors expressed herein do not necessarily state or reflect those of the United States government or any agency thereof. Available electronically at http://www.doe.gov/bridge Available for a processing fee to U.S. Department of Energy and its contractors, in paper, from: U.S. Department of Energy Office of Scientific and Technical Information P.O. Box 62 Oak Ridge, TN 37831-0062 phone: 865.576.8401 fax: 865.576.5728 email: [email protected] Available for sale to the public, in paper, from: U.S. Department of Commerce National Technical Information Service 5285 Port Royal Road Springfield, VA 22161 phone: 800.553.6847 fax: 703.605.6900 email: [email protected] online ordering: http://www.ntis.gov/ordering.htm Printed on paper containing at least 50% wastepaper, including 20% postconsumer waste Acknowledgement This research was sponsored by Stephen Goguen, Program Manager in the Department of Energy’s Office of Heavy Vehicle Technologies. The technical monitor for this project was Keith Vertin, Senior Engineer at the National Renewable Energy Laboratory. Source of Ignition Working Principle Determinant of Ignition Est. Ign. Ignition Volume Est. COV Production Limiting Feature Action Assist Delay Delay (Note 2) (Note 1) (ms) Glow Plug Heat transfer to mixture from external Surface temperature and local 2 - 3 Medium 5 Durability requires 1 hot surface equivalence ratio (Layer near glow plug surface) development AC Spark Plug Long duration high frequency spark Local equivalence ratio, spark 1 - 2 Small 3 Power supply and controls 2 initiated early in compression stroke duration and spark energy (Spark plug gap) require development SDHP Plug Short duration high power spark Local equivalence ratio and 1 - 2 Small 4 Durability and electronics 2 spark energy (Spark plug gap) unproven SmartFire Spark Multiple sparks with feedback control Local equivalence ratio and 1 - 2 Small 3 Durability and electronics 2 Plug spark energy (Spark plug gap) unproven Plasma Jet Ignitor Plasma generated and propelled into Plasma energy and plume < 1 Large 2 Durability requires 4 cylinder volume (Plasma plume volume) development Heated Pre-chamber Heat transfer to mixture from internal Surface Temperature and local 2 - 3 Medium 5 Durability requires 4 hot surface equivalence ratio (Layer at pre-chamber wall) development Fuel Preheating Fuel raised to ignition temperature Initial fuel temperature < 1 Large 1 Injector and power supply 5 prior to or during injection (Injection plume) require development Laser Excitation Excitation of fuel molecules in laser Laser energy and local fuel 1 - 2 Small 4 Cost and component durability 4 focal volume by laser wavelength concentration (Laser focal volume) far from production Laser Plasma Gases in laser focal volume ionized by Laser energy and local 1 - 2 Small 4 Cost and component durability 4 intense thermal heating equivalence ratio (Laser focal volume) far from production Inlet Air Heating Inlet air heating and increased Inlet air temperature and 2 - 3 Large 2 Power requirement and 5 compression ratio of engine to induce compression ratio (Injection plume) emissions issues autoignition Micropilot Injection Small quantity of high cetane fluid Fuel pilot cetane number and 1 - 2 Large 2 Pilot fuel consumption issues 3 injected with natural gas quantity (Injection plume) Fuel Additives Addition of ethane to natural gas to Fuel additive concentration 2 - 3 Large 3 Fuel supply problems 5 aid autoignition and autoignition temperature (Injection plume) Stratified Charge Early injection of fuel through plasma Plasma energy and plume < 1 Large 2 Requires extensive 4 Plasma Ignition jet ignitor volume development Note 1: '1' - Continue development. '2' - Initiate development. '3' - Perform concept study. '4' - Monitor outside research. '5' - Will reevaluate if encounter new development. Note 2: COV = Coefficient of Variation. Scale: 5 - high, 1 - low Table 1: Direct Injection Natural Gas Engine Ignition Options Survey Figure 1: Constant volume high pressure chamber -17- Predicted Breakdown Voltage vs Pressure 'Uniform-Field' Electrodes 300 predicted curve & point - 1.5 mm gap predicted curve & point - 1.0 mm gap 250 predicted curve & point - 0.5 mm gap 200 150 100 Breakdown Voltage (kV) 50 0 100 200 300 400 500 600 700 800 900 1000 1100 Pressure (psig) Figure 2: Predicted Breakdown Voltage vs Pressure by Paschen’s law -19- Figure 3: 60 Hz AC power supply Figure 4: Electrode mounting fixture -21- Breakdown Voltage vs Pressure Flat-Flat Electrodes 200 data point - 1.5 mm gap data point - 1.0 mm gap data point - 0.5 mm gap 150 best fit curve - 1.5 mm gap best fit curve - 1.0 mm gap best fit curve - 0.5 mm gap 100 50 Breakdown Voltage (kV) 0 100 200 300 400 500 600 700 800 900 1000 1100 Pressure (psig) Figure 5: Breakdown Voltage vs Pressure for Flat-Flat electrodes -23- Breakdown Voltage vs Pressure Flat-Round Electrodes 200 data point - 1.0 mm gap data point - 0.5 mm gap best fit curve - 1.0 mm gap 150 best fit curve - 0.5 mm gap 100 50 Breakdown Voltage (kV) 0 100 200 300 400 500 600 700 800 900 1000 1100 Pressure (psig) Figure 6: Breakdown Voltage vs Pressure for Flat-Round electrodes Breakdown Voltage vs Pressure Flat-Point Electrodes 200 data point - 0.5 mm gap best fit curve - 0.5 mm gap 150 100 50 Breakdown Voltage (kV) 0 100 200 300 400 500 600 700 800 900 1000 1100 Pressure (psig) Figure 7: Breakdown Voltage vs Pressure for Flat-Point electrodes -26- Breakdown Voltage vs Pressure 0.5 mm Gap 200 predicted curve & point - Paschen's Law best fit curve & predicted point - Flat-Round electrodes best fit curve & predicted point - Flat-Flat electrodes 150 100 50 Breakdown Voltage (kV) 0 100 200 300 400 500 600 700 800 900 1000 1100 Pressure (psig) Figure 8: Comparison of breakdown voltages for a 0.5 mm gap Breakdown Voltage vs Pressure 1.0 mm Gap 300 predicted curve & point - Paschen's Law best fit curve & predicted point - Flat-Round electrodes 250 best fit curve & predicted point - Flat-Flat electrodes best fit curve & predicted point - Flat-Point electrodes 200 150 100 Breakdown Voltage (kV) 50 0 100 200 300 400 500 600 700 800 900 1000 1100 Pressure (psig) Figure 9: Comparison of breakdown voltages for a 1.0 mm gap -27- Figure 10: High frequency AC power supply -29- DC Power Supply 15 to 20 Volts 20 amps 108 Volts 5 Volt 12 Volt 1 Amp Regulator Regulator Continuous 1 Amp 1 Amp 17 Amp surge Adjustable High Frequency Generator Low Voltage Logic Adjustable to High Voltage "H" Bridge Spark Duration Circuit Circuitry Control Interface Adjustable Enable Spark Repetition Switch Rate Control Disable External single Ignition coil spark control Spark Plug in Power and Ground Pressure Chamber Signal Line Figure 11: Schematic diagram of the high frequency AC power supply -30- Figure 12: EIS (electronic ignition system) Figure 13: SDHP (short duration high power) ignition system -35- 'Open Circuit' Voltage Coil made by Adrenaline Research Inc. 10 0 -10 -20 -30 Output Voltage (kV) -40 -50 0 20 40 60 80 100 120 140 160 Time (micro-seconds) Figure 14: Voltage Output vs Time Figure 15: Adrenaline plugs made by Champion -37- Figure 16: ‘S martFire’ ignition system -38- Figure 17: Spark plug after bench testing with the Adrenaline System (0.46 mm gap) Figure 18: Spark plug after bench testing with the Adrenaline System (0.51 mm gap) -40- Figure 19: Spark plug after bench testing with the Adrenaline System (1.02 mm gap) Figure 20: Spark plug after bench testing with the Adrenaline System (1.27 mm gap) -41- Figure 21: Ceramic disk sandwiched in the portable oil tester Figure 22: Ceramic disk sandwiched in the portable oil tester submerged the oil bath -45- Figure 23: Disks showing original coatings Figure 24: Disks showing modified coatings
Details
-
File Typepdf
-
Upload Time-
-
Content LanguagesEnglish
-
Upload UserAnonymous/Not logged-in
-
File Pages78 Page
-
File Size-