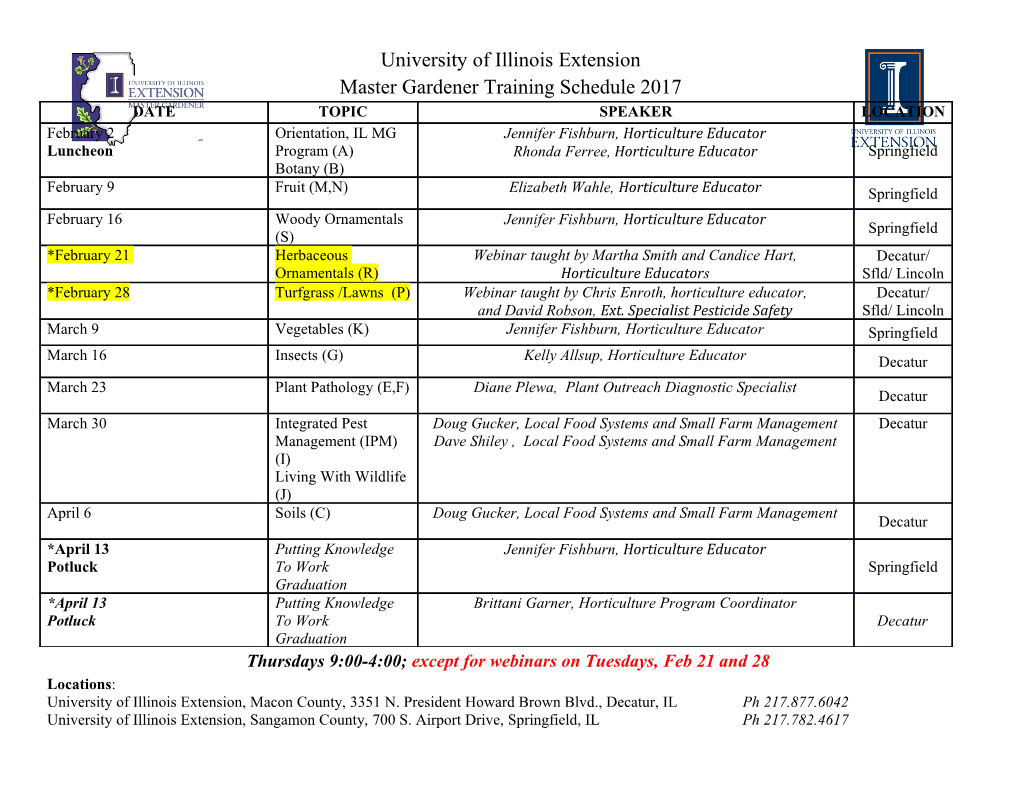
Materials Capturing and sequestering large quantities of CO2 in recycled concrete Accelerated re-carbonation of concrete Recycling concrete: an obligation Recybéton® is the name of a French national project With two tons per person and per launched in 2012 and extending over a 5 years per- year, concrete is the manufactu- iod. It brings together contractors, material manu- red material most consumed facturers and construction industries as well as worldwide. The bulk of conc- research centres such as Ifsttar, among others. The rete is made up of aggregates project aims at increasing the re-use of concrete representing some two thirds generated by deconstruction, in new concrete struc- of the total mass. At this stage tures. in time, the concrete manufac- A number of technical limitations remain however. turing process uses up approxi- Aggregates produced by crushing recycled conc- mately 40% of the total aggregate rete are of rather poor quality: they are more porous store available. However, not only is than natural aggregates; also, their mechanical pro- this resource not renewable, it is also more and more perties are lower. Also, a major obstacle is the fact difficult to procure. The Greater Paris Region - the Ile that they absorb too much water (from 5 to 10% de France area - imports nearly half of all the aggre- more) and more slowly (about 20 minutes). The wor- gates it consumes (approximately 13 million tons kability of concrete made in the usual way and using per year1) and forecasts are showing an increase in mixed recycled aggregates drops during its transport consumption by an additional 5 million tons per year2 in a concrete mixer lorry, to the point that it could because of the «Greater Paris» metropolis planning become improper for use on reaching final destina- project. The question is therefore how to produce tion. concrete whilst saving on the use of aggregates? At the same time, the volume of de-constructed Carbonation in all its stages material from buildings and infrastructures is increa- To produce cement, limestone (CaCO3) is heated sing and will become even more prevalent in the with silica at a high temperature (1,500°C). This pro- coming years. Indeed, buildings built during the duces lime (CaO) and most of the CO2 contained in Reconstruction period of the 1950s' have run their the limestone is released: it is called de-carbona- course. The volumes of concrete to be recycled will tion of limestone. Lime then recombines with silica increase considerably. to form clinker: it is then crushed and supplemented At present, such material is processed in two ways: to produce cement in powder form. It is estimated a) it is buried in a landfill, or b) it is recycled in road that this process (heating energy plus de-carbona- earthworks, as low added value backfill. tion) accounts for approximately 7% of the global Unfortunately, there are limits to the road industry's CO2 emissions. recycling capacities and if nothing is done, the cost of processing deconstructed material could increase drastically. Photo : Concrete from deconstruction 1 Livre blanc UNPG 2011 (White Book) 2 Source DRIEE Ile de France (Regional and InterDepartment Agency for Environment and Energy) When concrete is made, cement reacts with water: manufacturing processes for the new constructions silica and calcium hydrates are produced.These made of concrete. The objective therefore, is deve- hydrates govern the concrete's mechanical resis- loping a process to be used by the industry, and tance. However, hydrate molecules do not remain contributing to the development of a sunrise sector stable over time - they are described as «metasta- of circular economy. ble», i.e. when encountering atmospheric CO2, they And there is more! In addition, the laboratory has naturally re-carbonate by slowly reabsorbing CO2, discovered a definite improvement of the mechani- and re-transform into calcium and silica gel. The cal quality of re-carbonated aggregates. Water mineral cycle has gone full circle. absorption is both more limited and quicker than in non re-carbonated recycled aggregates: An additio- Drawing an advantage out of a problem nal advantage that will help turn into a reality the Manufacturers have always feared carbonation. It recycling of concrete inside concrete. increases concrete acidity (lowering the pH) and results in irreversible corrosion of the metal structu- Considerable potential res reinforcing the concrete. Fortunately, this natu- In France, material recovered from building and ral chemical reaction is very slow acting: in an public works deconstruction represents close to 300 outdoor structure in use, only 2 to 3 cm in depth are million tons per year. 36% of this is concrete-based re-carbonated after 50 years! Ifsttar's objective has material. At present, it is estimated that only half of been to speed up this reaction in recycled conc- it is recycled to produce fresh concrete. By genera- rete.The process under study focuses on bringing in lising recycling and by applying this new technique contact crushed aggregates from de-construction of accelerated re-carbonation to nearly 100 million and CO2 from the air, under very high concentration tons of aggregates per year, this should make it pos- and pressure, using a fairly conservative supply of sible to capture and sequester from 10 and 15 million energy. tons of CO2 per year, i.e. the equivalent of over 10% Using this natural phenomenon to capture and of all GHG emissions produced by the transportation sequester atmospheric CO2 in the cement matrix of sector. de-construction aggregates will improve considera- bly on the environmental balance of concrete as a Moving on to demonstrators material. The first laboratory tests demonstrated that In increasing number of studies is being carried out using 1 ton of recycled concrete potentially led to in laboratories. Demonstrators will soon be built with the capture and sequestering of 150 kg of CO2 That interested contractors, i.e. buildings built in re-car- was without counting on the sparing of 650 kg of bonated recycled concrete. Ifsttar is already in natural quarry aggregates, as those would not be contact with recyclers, the pre-cast industry and buil- required. To be added to that, there are the net ding contractors. savings in CO2 that are possible when using new A coloured pH indicator is used to make carbonation visible. Since carbonation lowers pH, the indicator turns pink where- ver the material has not undergone carbonation. On the left, aggregates of recycled concrete have been carbonated at natu- ral speed (carbonation only over a few millimetres from the surface). On the right, the same aggregates have been carbonated using the accelerated method (thorough mass carbonation). Champs-sur-Marne • Lille / Villeneuve d’Ascq • Lyon / Bron • Marseille / Salon de Provence • Nantes / Bouguenais • Versailles / Satory Ifsttar Head Office 14-20, boulevard Newton Cité Descartes, Champs-sur-Marne 77447 Marne-la-Vallée Cedex 2 French institute of science and technology for transport, www.ifsttar.fr development and networks [email protected].
Details
-
File Typepdf
-
Upload Time-
-
Content LanguagesEnglish
-
Upload UserAnonymous/Not logged-in
-
File Pages2 Page
-
File Size-