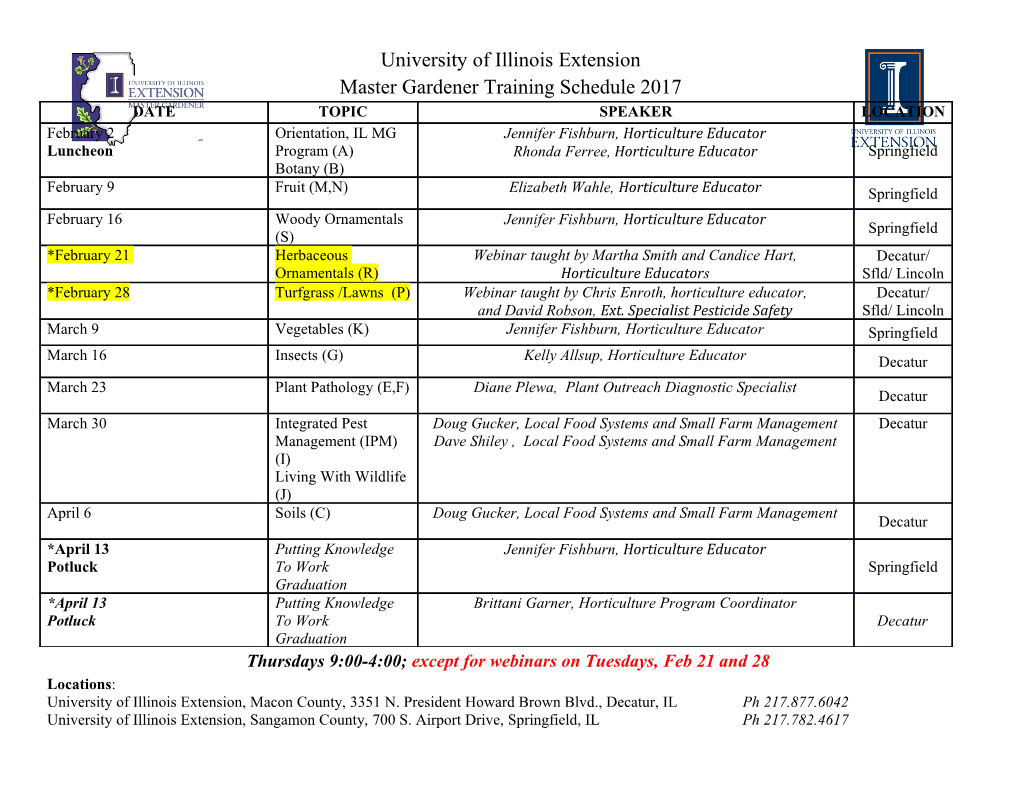
Andrey Shishkin 1. Methods of physical vapor deposition. Thermal evaporation. Adhesion. Role of vacuum. Monitoring of the deposition process. 2. Magnetron and RF-diod sputtering. 3. Electron-beam evaporation. 4. Engineering aspects of physical vapor deposition: vacuum chambers, pumps, cooling systems. 5. Monitoring and control of the deposition processes. 6. MBE based technologies. Physical vapor deposition, PVD Physical vapor deposition (PVD) systems deposit thin films and coatings by a process in which a target material is vaporized, transported in vacuum, and condensed on to a substrate. PVD processes include Sputtering, Electron beam, and Thermal Evaporation. • Thermal evaporation • In-situ control of the film thickness. Estimations of the film uniformity. • Electron-beam physical vapor deposition • Sputtering deposition, magnetron sputtering deposition • Cathodic arc deposition. • Reactive deposition • Laser ablation • Role of vacuum conditions • Vacuum systems for the physical vapor deposition. Pumping systems. • Adhesion of coatings. • Types (modes) of thin film growth. • Several important examples of different coatings. Thermal evaporation Thermal evaporation is realized by thermal heating (usually resistive) of an evaporated material placed in an evaporation source. It is carried out in a vacuum at pressure P<10-5 torr. The thermal evaporation is the most gentle PVD method with evaporated particle energies ~1500 K (0.12 eV). This method is the simplest PVD method and needs comparatively low power consumption. Main types of simple evaporation sources are metallic boats (1,2) and heaters made of refractory wires (3) (Wo, Mo,…) which can be covered by a passive material (2) (Al2O3) More complicated effusion cells with a crucible made of passive material (e.g., boron nitride, BN) and an external heater are used for precision evaporation processes like the molecular beam epitaxy. A simple system for thermal evaporation Vacuum chamber 1 is evacuated to pressure of the order of 10-6 Torr via the pumping line. The pressure is measured by vacuum gauge 2. A material 3 is evaporated from a metal boat 4 heated by an electric current. The current flows through an isolated vacuum tight lead 5, which is usually cooled by water (not shown in Fig.), and grounded lead 6. A substrate 7 is mounted on a holder 8. The holder may have options of rotating around vertical Pumping axis and tilting relative to it. The latter option line corresponds to the so named oblique evaporation. These options help to avoid undesirable shadows. The temperature of the holder may be varied and stabilized in a wide range. The thickness of evaporated film is controlled by a thickness monitor based on a quartz crystal microbalance 9 (QCM). QCM measures variation of a mass on a surface of a quartz crystal resonator. For a high accuracy measurements the crystal should stay at a constant temperature. The evaporation process is controlled by the current through the boat (i.e., the boat temperature) and the shutter 10 position. The shutter is closed till reaching the desired boat temperature and beginning of the material vaporization. It closes at the end of evaporation process. Thickness of deposited films: control and uniformity. I. Thermal evaporation provides the best conditions for in-situ control of the average film thickness. A real – time film thickness monitor can use different sensors: (i) A quartz crystal microbalance, (ii) Reflection high-energy electron diffraction (RHEED) (in the molecular beam epitaxy), (iii) optical methods including ellipsometry. A simplified geometry of the quartz resonator, produced by a cylindrical quartz plate 1 and metallic films 2,3 on opposite sides of the plate. To excite the mechanical oscillations in the plate the ac voltage Vf is applied between films 2 and 3. The resonator is a part of an oscillator which frequency f is determined by the resonant frequency of the mechanical resonator (typical value ~5 MHz). The Q-factor of the mechanical resonance can be as high as 106. Evaporation of a thin film with mass m shifts the resonant frequency by Here f0 nN 0 / D is the resonance frequency without evaporated film, N0 1.661 MHz*mm for the quartz AT cut; n - is an integer numbering different resonant overtones, D-the plate thickness, S- active area of the resonator. 2 3 11 g/cm s - shear modulus for the AT cut 0 2.648 g/cm – density of the quartz , 0 2.947 *10 of a quartz crystal. Quartz crystal microbalance For Au ( =19.3 g/cm3) film, one monolayer (d~3A) corresponds to f=33 Hz. Temperature stabilization is important condition for precise measurements! Equation (Q1) is valid for f / f0 0.03 For a wide frequency range ( f/f0<~0.3) a more complicated equation is used: f f m N 0 0 0 arctg Ztg S Zf f0 Here Z 0 0 and are the density and shear modulus of evaporated film. Difficulties and ways to overcome them: 1. All geometries of evaporators are unique. Also we can have different positions of the substrate – the sensor needs often calibration. 2. Heating of the quartz resonator – we need cooling system which makes the system more complex. 3. Deposition of different materials on the same sensor – it can be eliminated by the use of several sensors: one for each material. Estimate for the thermal evaporation rate , ma dm / dt P(Tev ) 2kTev Here dm/dt – the mass rate of evaporation from a unit area, ma – mass of evaporated particle, P(Tev) – the vapor pressure at evaporation temperature Tev . This formula is equivalent to the well known equation of the molecular kinetic theory for the particle flow Ns /t on a unit flat area: Ns /t=nV av /4 where n is the particle density and 1/2 Vav=(8kT/ma) is the average particle velocity determined from the Maxwell‘s distribution. P(T) is usually described by the Clausius–Clapeyron equation Q is the specific latent heat of the phase transition (vaporization) V i s the specific volume change of the phase transition (the difference of specific volumes of a liquid and vapor). dP PQ Q ln P A A B / T For an ideal gas and dQ/dT=0 2 which gives (Q2) dT T R TR Temperature dependence of the vapor pressure Temperature dependences of the vapor pressure P on the temperature T (horizontal scale is inversely proportional to T) for Au and Ti. Solid lines were calculated in accordance with Eq. (Q2) with the use of parameters 4 AAu=20.84 and BAu=4.26x10 K (liquid-vapor). 4 ATi=23.81 and Bti=5.67x10 K (solid-vapor). The solid signs are taken from handbook “Physical quantitites” edited by Grigor’eva and Meilikhov (1991). The melting points Tm are marked by vertical by arrows. Equilibrium vapor pressures of selected materials. The slashes indicate the melting points (MPs). Typical for the thermal deposition value of the vapor pressure 10-2 Torr is marked by the horizontal arrow. Some of the materials are evaporated and some are sublimated. Sublimation of metals is possible by their direct heating by passed current (e.g., Ti). Angular distribution of atomic flow A general geometry of evaporation. is the angle between the normal to the surface element dS1 of the evaporator and a direction R to the surface element dS2 of the substrate. R is a distance between these elements. The angle between R and a normal to dS2 is Projection of the dS2 on the plane normal to R is dS0= dS2cos( A part dw of a total flux w from a flat source into a small solid angle d in the direction determined by angle is given by equation dw=(w/) cos( )d . This relation is the result of the maxwellian distribution and an analog of the Lambert law in the optics. For evaporated mass m, the film thickness is d= m cos( )cos( /R2 If the source is spherical, dw=(w/4) d and d= m cos( /4R2 Coordinate dependence of the thickness of the deposited films substrate Consider thermal vapor deposition from a small flat source on parallel substrate . This corresponds to = , cos =H/(H2+X2)1/2 , R2=H2+X2. m 2 m 1 d ( X ) H d (H 2 X 2 )2 max H 2 Flat source m H m 1 d ( X ) 2 2 3 / 2 d max Spherical source 4 (H X ) 4 H 2 source Thickness distribution along the substrate for a small flat (black 1.0 Spherical sourc(ea) lines) and spherical (red lines) sources. Panel b shows initial part of 0.8 x 0.6 panel a. ma These data show that condition of thickness uniformity leads to d/d 0.4 requirement of a large distance between the source and the substrate, 0.2 Flat source 0.0 0.0 0.2 0.4 0.6 0.8 1.0 1.2 1.4 i.e., to a large size of a vacuum system. 1.1 (b) Theoretical calculations may be inaccurate due to a finite size of the 1.0 x source and redistribution of the temperature along it. However some a 0.9 m d/d of these factors may even lead to a better film uniformity. In fact, in 0.8 practice the optimal conditions are chosen empirically and 0.7 0.0 0.2 0.4 reproduced from one evaporation cycle to another. X/H Advantages of the thermal evaporation method • The most gentle PVD method, due to the lowest possible energy of evaporated particles (~1500 K~0.12 eV). • Atomic or molecular deposition from the vapor. • Appropriate for deposition of a large number of materials. • Appropriate for ultra-high vacuum conditions. • In-situ control of the deposited layer thickness.
Details
-
File Typepdf
-
Upload Time-
-
Content LanguagesEnglish
-
Upload UserAnonymous/Not logged-in
-
File Pages82 Page
-
File Size-