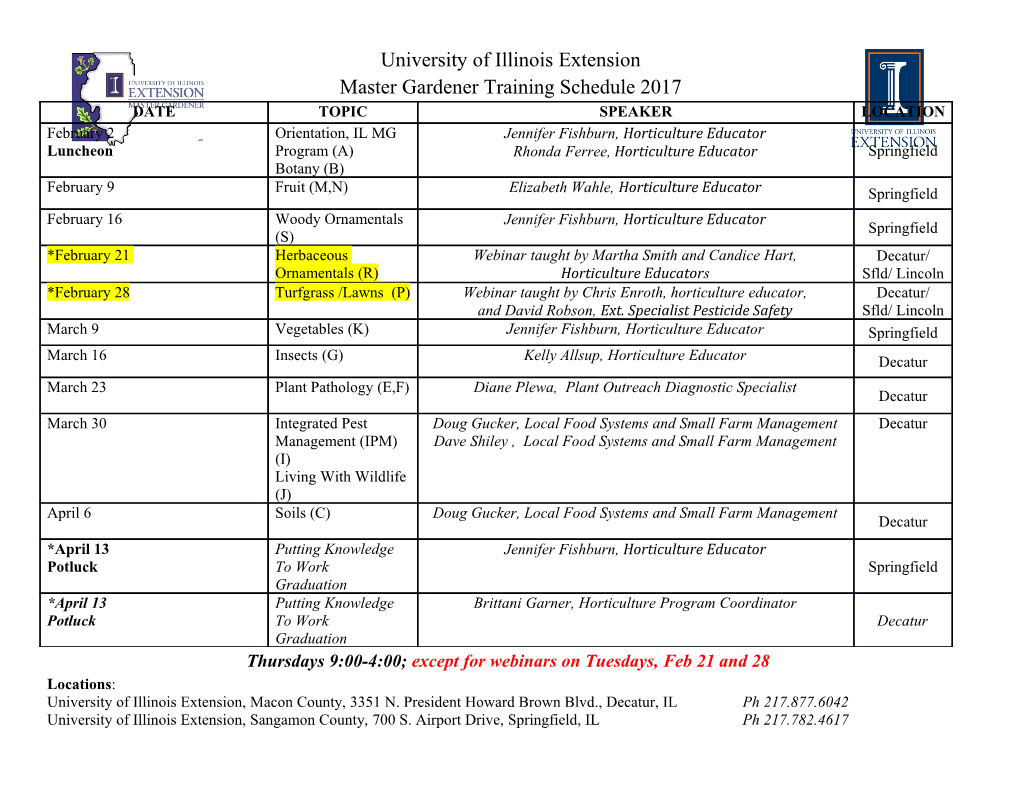
Propulsion Engineering Propulsion Research Work at Marshall Space Flight Center Amy Sivak November 5, 2013 1 ER24: Propulsion Technology Propulsion Engineering and Development Branch Propulsion Research and Development Laboratory NASA - Marshall Space Flight Center Early NEP concept for JIMO mission 2 Space Propulsion Concepts Propulsion Engineering 107 Sails 106 Continuous Fusion Antimatter 105 Pulsed Fusion 104 Electrostatic Electro- Pulsed Fission magnetic 3 Thermal Fission 10 Electrothermal Laser/Solar Thermal Specific Impulse (seconds) Chemical RBCC Chemical Rockets 102 10-5 10-4 10-3 10-2 10-1 1 10 102 Vehicle Acceleration or T/W Ratio (g’s) Unproven Technology (TRL 1-3) Demonstrated Technology (TRL 4-6) Operational Systems (TRL 7-9)3 Types of Electric Propulsion Propulsion Engineering Electric thrusters are generally categorized by their primary acceleration mechanism: • Electrothermal Resistojet – Electrical energy into thermal energy – Large number of all EP systems on-orbit Early Early – Isp 500-1500 s, thrust medium/high – Hot exhaust / high density gas / nozzled expansion • Electrostatic Hall – Applied electric field directly accelerates ions thruster – Growing fraction of all EP systems in space – I 1000-10,000 s, thrust low/medium In Use sp – Low density gas / grid or electrodes to apply E-field / low thrust density Magnetoplasmadynamic • Electromagnetic (Plasma) thruster – Interacting currents and magnetic fields directly accelerate plasma – Isp 1500-6000 s, thrust medium/high R&D Area R&D Area – High density gas / generally compact • MSFC R&D on iodine-fed Hall thrusters, high-power arcjets (1 MW) and high-power pulsed inductive thrusters (PIT). 4 NASA EP Activities – Past & Planned Propulsion Engineering What has been done? • Deep Space 1 technology demonstrator (NSTAR ion engine) • Dawn science mission to asteroid belt (ongoing w/NSTAR ion engine) Asteroid-Retrieval Mission • Capture asteroid and return it to cislunar space by ~2025 • 7-m diameter, 500-1000 t object • ~40 kW (solar) power level Human Exploration – DRM-5 • Power manned transfer vehicle for trip to NEA • 300 kW (solar) power level Planned Solar Electric Propulsion (SEP) Technology Demonstration Mission • Test and validate key technologies required for future exploration elements (i.e. 300-kW solar electric transfer vehicle) by ~2017/2018 • ~15-30 kW solar power level on demonstrator 5 Usage Through the Years As 199419852001of 2010 Propulsion Engineering 6 Recent High-Profile EP Missions Propulsion Engineering ESA’s Smart 1 – PPS1350G Hall thruster (x1) JAXA’s Hayabusa – 10 microwave ion thruster (x4) 2003-2006 (Moon) 2003-2010 (Itokawa – sample return) NASA’s Dawn – NSTAR ion thruster USAF AEHF – BPT-4000 Hall thruster (x4) (x3) 2010 (Geo Orbit – boosted system when bi-prop motor failed) 2007-2015 (Vesta and Ceres) 7 EP at MSFC – Pulsed Inductive Thrusters Propulsion Engineering • High power, high thrust density • Electrodeless (requires high power switches) • Many propellant options • Impulse ~ 0.1 N-s, Isp ~ 2000-s to 10000-s • High impulse maneuvers, primary planetary propulsion • Research level (single shot, t ~ 50% on ammonia) Higher thrust density enables this: Instead of this! *From NASA CR-191155, by C.L. Dailey and R.H. Lovberg, 1993 8 Pulsed Inductive Thruster Characteristics Propulsion Engineering • High voltage (15 kV) and energy (4 kJ/pulse) • Separate ionization and acceleration • Complexity (18 capacitors, 18 switches) mechanisms • Stringent switching requirements • Simultaneous closing of 18 switches • Preionization lowers energy/voltage required • High voltage holdoff, high current to operate switching • ~100 J/pulse vs. 4 kJ/pulse • Presently spark gap switched • All other advantages of inductive acceleration Difficult to scale to small size Easier to scale to small size 9 Thruster Development Propulsion Engineering Flat-plate geometry Conical geometry 10 Critical Issues - Preionization Propulsion Engineering Helicon discharge (~1000 W) 13.56 MHz Microwave-driven ECR discharge (~1 kW) 2.45 GHz Inductively-coupled discharge (35-50 W) ~600-900 MHz 11 Critical Issues - Continued Propulsion Engineering Switching • High voltage holdoff (multiple kV) • High current conduction (10s of kA) • Fast (> 100 kA/s rise time) • Repetition rate (> 100 Hz for high power) • Fast turn off / reset for next pulse Pulsed Gas Injection Power systems • Fast open and close (1-3 ms total) • Transform spacecraft bus power to • Low latency in propellant lines current / voltage needed by thruster • Low leak rate (0.001 sccs GHe) • DC / AC input power • Lifetime (108-109 pulses) • Repetitive capacitor charging to multiple kV • Charging rate commensurate with capacitor switching capabilities • Operate in environment (vacuum) • Remove / dissipate heat in system 12 Measurement at MSFC Propulsion Engineering High-fidelity thrust stand • Thrust levels ~1 mN – 1 N (50 N resolution) • Impulsive resolution below 1 mN-s * • Steady-state or pulsed in-situ calibration *Rev. Sci. Instrum., by Wong, Toftul, Polzin, Pearson, Feb. 2012 13 Second Capacitor PIT Design Propulsion Engineering • Traditionally, the PIT uses one capacitor with a switch to send current to the thruster coil. • Addition of a capacitor – Increases current rise rate (a) Schematic of a traditional PIT circuit through the inductive coil with one capacitor. – Better ionizes the propellant – May eliminate the need for pre-ionization • Numerical Analysis of the two capacitor case was performed. • Paper on the two capacitor case: (b) Schematic of the PIT circuit with “Pulse Inductive Plasma Accelerator Effect of a a second capacitor. Second, Parallel Capacitor on the Performance,” Polzin, Sivak, and Balla. 2011. 14 Nuclear Thermal Rocket Element Environmental Simulator (NTREES) Propulsion Engineering A key technology element in Nuclear Thermal Propulsion is the development of fuel materials and components which can withstand extremely high temperatures while being exposed to flowing hydrogen. NTREES provides a cost effective method for rapidly screening of candidate fuel components with regard to their viability for use in NTR systems 15 Nuclear Thermal Rocket Element Environmental Simulator (NTREES) Propulsion Engineering • The NTREES is designed to mimic the conditions (minus the radiation) to which nuclear rocket fuel elements and other components would be subjected to during reactor operation. • The NTREES consists of a water cooled ASME code stamped pressure vessel and its associated control hardware and instrumentation coupled with inductive heaters to simulate the heat provided by the fission process. • The current NTREES upgrade will increase the induction heating capacity by a factor of 30 over the previous configuration (now 1.2 MW) • In addition to the power upgrade, there will be numerous enhancements to the data acquisition and control system 16 Description of NTREES Upgrade Activities Propulsion Engineering • Much of the NTREES system is being relocated on top of a platform to conserve space and increase safety • NTREES induction power supply is being upgraded to 1.2 MW • Water cooling system is being upgraded to remove 100% of the heat generated during testing • Data acquisition system is being upgraded to detect the release of radioactive particles and provide addition system performance data • The H2 / N2 mixer is being upgraded to handle increased heat loads of up to 5 MW 17 Current View of the NTREES Facility Propulsion Engineering 18 NTREES Upgrade to 1.2 MW Propulsion Engineering • Water cooling system • Construction the H2/N2 mixer • Test article induction coil • Induction heater power bussbar and feedthrough installation • Installation of the nitrogen line is complete and pressure certification activities • Exhaust line installation • Induction heater power connections • Data acquisition and control system activities 19 New NTREES System Layout Propulsion Engineering Power Feedthrough 20 NTREES H2 / N2 Mixer Assembly Propulsion Engineering H2 / N2 Mixer Installed on Main Chamber 21 NTREES Coil and Feedthrough Propulsion Engineering Coil and Feedthrough Assembly Coil New Coil is Heavily Insulated and Rugged Cooling Chamber Old Coil was Uninsulated and Somewhat Fragile Electrical Connection 22 Test Run of NTREES Propulsion Engineering 23 Pyroelectric Microthruster Propulsion Engineering • Prior scientific experiment • Use on microsatellites preformed using pyroelectric – Low thrust technology Lithium Tantalate Crystal – Utilizes solar heating and a • Design is driven by a Pyroelectric Lithium Tantalate pyroelectric crystal, Lithium Crystal for power source. Tantalate, which produces an electric field when subjected to a temperature cycle. • Electric field ionizes surrounding deuterium gas which hits an Erbium Dideuteride/ Tritiate Water target to produce a small amount of neutrons. • Low level neutrons produced, Observation of Nuclear Fusion Driven by a just above background. Pyroelectric Crystal. Naranjo, B., J.K. Gimzewski, and S. Putterman. s.l. : Nature, Apr. 2005, Vol. 434 D + D -> 3He (820 keV) + n (2.45 MeV) 24 Pyroelectric Microthruster Test Setup Propulsion Engineering 25 Results Comparable to Literature Propulsion Engineering 1.40 0.14 Current Current ~ 10 s Average & Excursions Removed 1.20 dT/dt 0.12 1.00 0.10 0.80 0.08 C/sec) 0.60 0.06 ° Current (nA) dT/dt ( 0.40 0.04 0.20 0.02 0.00 0.00 0 100 200 300 400 500 600 700 -0.20 -0.02 Elapsed Time (s) Current and dT/dt During Heating Observation of Nuclear Fusion Driven by a Pyroelectric Crystal. Naranjo, B., J.K. Gimzewski,
Details
-
File Typepdf
-
Upload Time-
-
Content LanguagesEnglish
-
Upload UserAnonymous/Not logged-in
-
File Pages50 Page
-
File Size-