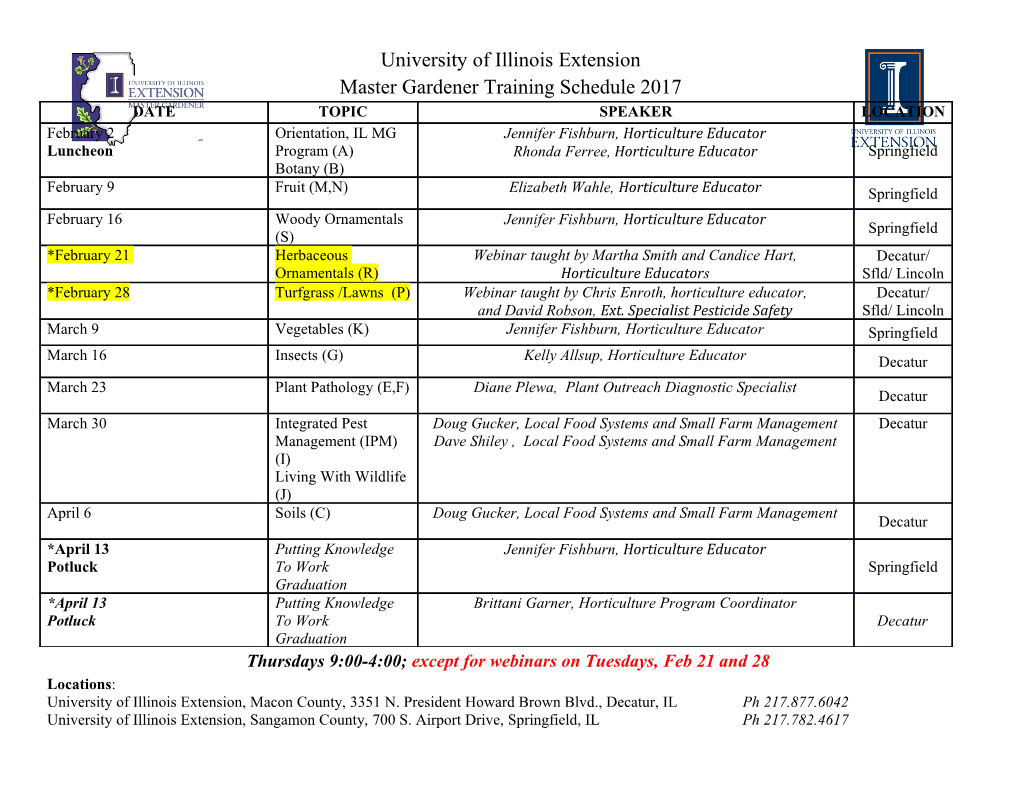
US 2008O166281A1 (19) United States (12) Patent Application Publication (10) Pub. No.: US 2008/0166281 A1 Harms et al. (43) Pub. Date: Jul. 10, 2008 (54) METHODS FOR PRODUCING CESIUM (30) Foreign Application Priority Data HYDROXDE SOLUTIONS Jan. 27, 2005 (DE) ......................... 102005OO3999.5 (76) Inventors: Gerd J. Harms, Goslar (DE); O O Alexander Schiedt, Hahausen Publication Classification (DE); Manfred Bick, Oberursel (51) Int. Cl. (DE); Wolfgang Hildebrandt, BOID LL/00 (2006.01) Langelsheim (DE) (52) U.S. Cl. ........................................................ 423/202 Correspondence Address: (57) ABSTRACT FULBRIGHT & JAWORSKI, LLP 666 FIFTHAVE Methods for producing cesium hydroxide Solutions during NEW YORK, NY 10103-3198 which: cesium-containing ore is disintegrated with Sulfuric acid while forming a cesium aluminum Sulfate hydrate, which (21) Appl. No.: 11/795,855 is poorly soluble at low temperatures; the formed cesium alum is separated away in the form of a solution from the Solid (22) PCT Filed: Jan. 25, 2006 ore residues; the aluminum is precipitated out of the cesium alum solution while forming a cesium sulfate Solution; the (86). PCT No.: PCT/EP2006/OOO634 formed cesium sulfate solution is reacted with barium hydroxide or stontium hydroxide while forming a cesium S371 (c)(1), hydroxide solution, and; the formed cesium hydroxide solu (2), (4) Date: Nov. 1, 2007 tion is concentrated and purified. US 2008/0166281 A1 Jul. 10, 2008 METHODS FOR PRODUCING CESIUM contents of Sulfate and/or barium or has a caesium carbonate HYDROXDE SOLUTIONS Solution as the end product. This process does not give cae sium hydroxide solutions. 0007 Caesium hydroxide solutions have numerous appli 0001. The invention relates to a process for the production cations, e.g. as catalysts, and are used as the starting product of caesium hydroxide solutions. for the production of all neutral and basic caesium salts and of 0002 Current processes for the production of caesium Solid caesium hydroxide and other caesium compounds. compounds are based on caesium-containing ores such as Because a disadvantageous purification of the compounds is pollucite. Thus U.S. Pat. No. 6,015,535 describes a process often not possible or possible only with great expense, a high for the production of concentrated and purified caesium salt purity of the caesium hydroxide solutions is desired. Further solutions. This process includes the digestion of the ore with more, a high concentration of the caesium hydroxide solu a hyperstoichiometric quantity of Sulfuric acid, the purifica tions is aimed for. tion by recrystallisation of the caesium aluminium sulfate 0008. The problem of the present invention is to overcome hydrate obtained in this way, the precipitation of the alu the disadvantages of the prior art and develop a process for the minium with slurried lime Ca(OH) and/or calcium carbon production of an aqueous caesium hydroxide solution which ate and the separation of the precipitate consisting of calcium has a caesium hydroxide concentration of at least 45 wt.% Sulfate hydrate (gypsum) and aluminium hydroxide from the and is marked by as low as possible a content of multivalent caesium sulfate solution. There follows a reaction of this cations in general and alkaline earth cations in particular, and Solution with a calcium hydroxide slurry and an acid, main low contents of Sulfate and carbonate. taining a pH of 7 to 8. Separation of the residue consisting of 0009. The problem is resolved by a process for the pro calcium sulfate from the caesium salt solution determined by duction of caesium hydroxide solutions in which the anion of the acid then takes place. Purification of the 0010 caesium-containing ore is digested, forming a caesium salt Solution takes place by a multi-stage “polishing caesium aluminium Sulfate hydrate (caesium alum), in which the solution is rendered alkaline with barium poorly soluble when cold, with sulfuric acid, hydroxide and then mixed with carbon dioxide or carbonate, 0.011 the caesium alum formed is separated off as a alkaline earths and Sulfate being precipitated and separated solution from the solid ore residues, off. The by then highly dilute caesium salt solution is finally 0012 the aluminium is precipitated out from the cae concentrated by evaporation, wherein concentration can con sium alum Solution, forming a caesium Sulfate solution, tinue until a solid is obtained. 0013 the caesium sulfate solution formed is reacted 0003 Patent DE4313 480C1 describes the production of with barium hydroxide or strontium hydroxide, forming a caesium hydroxide Solution by reacting caesium aluminium a caesium hydroxide solution (this process step is Sulfate hydrate or a caesium Sulfate Solution with calcium described as “causticisation') and hydroxide in accordance with the equations 0.014 the caesium hydroxide solution formed is con centrated and purified. 2CaSO (1) 0015. In the reaction of the caesium sulfate solution formed to the caesium hydroxide solution, the use of barium Cs-SO+Ca(OH)->2CsOH+CaSO (2) hydroxide is preferred. 0004. The yields achieved, however, are very unsatisfac 0016. Any caesium-containing ore or material can be used tory. U.S. patent application 2002/0143209 A1 attempts to as caesium-containing ore. However, pollucite is preferably remedy this by repeating the reaction according to equation used. A preferred pollucite has a caesium content of 20 to 24 (2) several times, the caesium hydroxide produced and wt.%. The particle size of the ore used is preferably 90 wt.%. present in a mixture with caesium sulfate in each case being <100 um and is optionally achieved by grinding the ore. neutralised with the desired acid. 0017. The following reaction equation can be given for the 0005. Due to the comparatively better solubility of the digestion reaction: hydroxide of the barium but very low solubility of the sulfate, the reaction 0018 Digestion is preferably carried out with a hypersto is virtually completely displaced towards the caesium ichio-metric quantity of Sulfuric acid (relative to the quantity hydroxide. U.S. Pat. No. 3,207,571 describes the reaction of of ore used). The mixture ratio of caesium-containing ore a caesium Sulfate solution with an aqueous barium hydroxide (with a Cs content of 20 to 24 wt.%): water : concentrated Solution. A dilute caesium hydroxide Solution which is sepa sulfuric acid is preferably=1.0:(1.0 to 1.8):(1.0 to 1.8), par rated from the solid barium sulfate, is obtained. This solution ticularly preferably 1.0:(1.2 to 1.6):(1.2 to 1.6) and especially can be converted directly with acid to the corresponding preferably 1.0:(1.3 to 1.5):(1.3 to 1.5). caesium salt Solution, or a carbonate Solution is produced 0019 Digestion is preferably carried out in such away that from this solution by addition of CO., wherein excess barium the mixture of caesium-containing ore, water and Sulfuric can be precipitated from this as barium carbonate by concen acid is heated for a period of at least 2 hours at a temperature trating and separated. of>90°C. A digestion time of at least 3 hours is preferred. The 0006. The processes described have a number of disadvan preferred minimum temperature is 100° C., particularly pref tages. According to the route proposed in U.S. patent appli erably 120° C. A preferred maximum temperature corre cation 2002/0143209 A1, caesium hydroxide can only be sponds to the boiling point of the reaction mixture. Potentially produced in mixture with other caesium salts. The production evaporating water is preferably replaced. The reaction can method stated in U.S. Pat. No. 3,207,571 leads to highly also be carried out at excess pressure, e.g. at 0.5 to 6 bar dilute caesium hydroxide Solutions with high, not defined, excess pressure, preferably 1 to 6 bar excess pressure. US 2008/0166281 A1 Jul. 10, 2008 0020 Should the caesium-containing ore also not have a 0029. The caesium alum is thereby dissolved with heating high enough aluminium content or should not enough alu in a quantity of water sufficient to dissolve all of the salt and minium be digested during digestion and pass into Solution, in then cooled to approx. 20°C., the Supernatant mother liquor a preferred embodiment of the process aluminium can be being separated off and optionally used again at another point added in the form of aluminium sulfate during or after diges in the process. This recrystallisation is preferably carried out tion, so that a sufficiently high quantity of aluminium is several times. The first recrystallisations can thereby be car available for the formation of the caesium alum. Without a ried out with mother liquors and the other recrystallisations Sufficient quantity of aluminium, yield losses could occur, but with water, preferably deionised water (DI water). performance of the process as Such is not affected by an 0030) Surprisingly it was found that with e.g. six recrys insufficient quantity of aluminium. The molar ratio of Alto Cs tallisations and the use of the mother liquors in the 1, 2" and is preferably at least 1:1. A slight aluminium excess is par 3' recrystallisations and carrying out the 4, 5' and 6' ticularly preferably used, the Al:Cs molar ratio being up to recrystallisation with deionised water (DIwater), the contents 1.5:1. of for example Rb can be reduced to <1.0 ppm, based on the 0021. At the end of the digestion reaction and cooling of content of caesium alum calculated as caesium hydroxide. the reaction mixture, a caesium aluminium Sulfate hydrate Preferably, based on the ore charge, 3 to 4 parts by weight DI heavily contaminated by other alkali elements crystallises water are used in the corresponding recrystallisation step. out. Water or process Solutions from later process steps (e.g.
Details
-
File Typepdf
-
Upload Time-
-
Content LanguagesEnglish
-
Upload UserAnonymous/Not logged-in
-
File Pages6 Page
-
File Size-