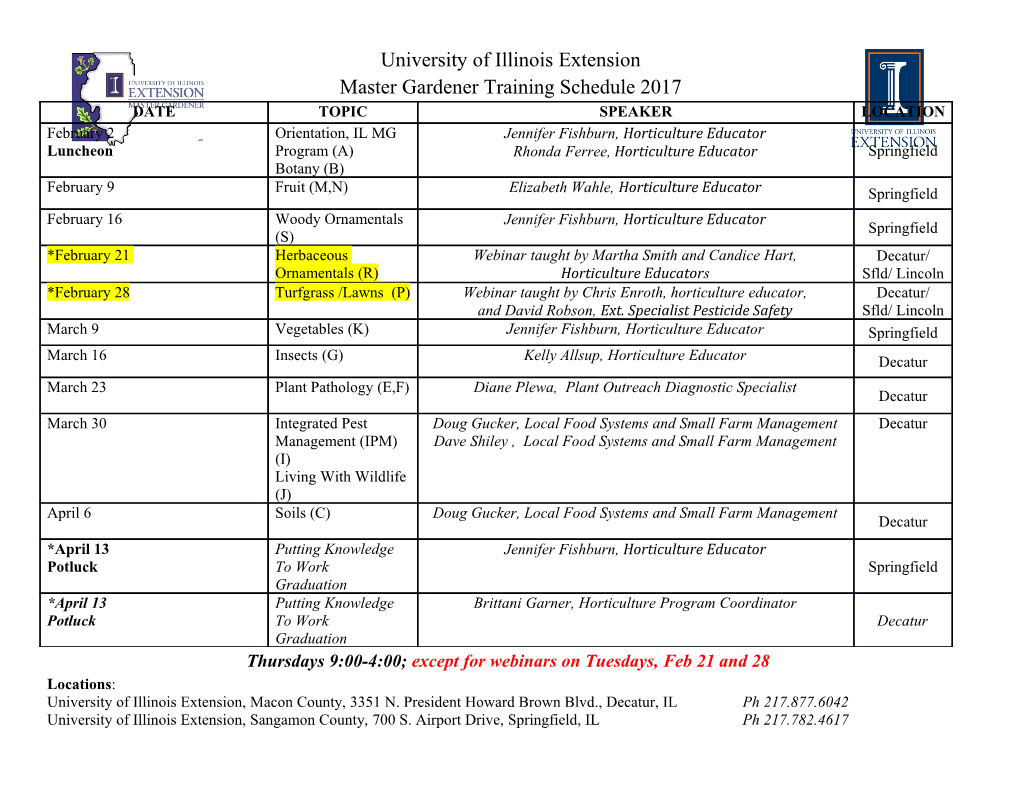
Modelica library for the systems engineering of railway brakes Marc Ehret Institute of System Dynamics and Control, German Aerospace Center, Germany, [email protected] Abstract content of electronic and software components, systems engineering has become a wide spread and important pro- This work outlines the role of system simulation for the cedure in product development (INCOSE, 2015). development process of railway brakes. The principles of In the context of systems engineering, computer based systems engineering motivate the use of computer based system simulation is a powerful tool since it supports de- simulation in order to enhance the understanding of sys- signers to understand the behavior of systems in design tems and to verify the behavior of systems in early de- stages where an experimental analysis is not feasible. Fur- sign phases. For this reason, the Modelica library "Vir- thermore, it allows engineers to check their own thinking, tual Train Brakes" is presented which enables engineers to to analyze alternatives and capabilities of the system and generate simulation models of railway brakes and to per- to communicate their concept to others (INCOSE, 2015) form system simulations during different phases of the de- (Mittal et al., 2017). Modelica is a well suitable modeling velopment process. By modeling and simulating the brake language to generate models of multi-physical technical systems of a passenger and a freight train, the capability of systems, such as railway brake systems and to study their the library is demonstrated and further investigations are physical behavior. motivated. Keywords: Railway Brakes, Systems Engineering, Multi- The goal of this work is to develop the concept of a Level Models, Variant Models, Generic Models Modelica library which provides an environment for the application of system simulation throughout the entire de- 1 Introduction velopment process of railway brakes. As shown in Fig- ure 2, the main tasks of the library are: Railway brakes are complex technical systems that fulfill high requirements concerning safety, availability and reli- ability. These systems are constructed to be deployed in support dimensioning a difficult operational environment, characterized by large • temperature ranges and heavy dynamic loads during long analyze and optimize system behavior utilization times. Furthermore, a huge amount of kinetic • energy needs to be converted during a single brake appli- cation which requires that brake discs are able to absorb support integration up to 30 MJ of energy (Breuer, 2006). Beside severe op- • erational conditions, the diversity of railway vehicles and brake types demands to design individual adapted brake support system test and commissioning systems which leads to a high variety and individuality • of the developed systems. This individuality and the cor- responding variety of brake systems is in contrast to the Initially, this work introduces railway brake systems comparatively low number of items that is usually deliv- and the role of systems engineering in the scope of their ered (Anton, 2010). In order to reduce technical as well as design. Subsequently, use cases of system simulation dur- economical risks the application of systems engineering is ing the development process are discussed which are the indispensable for of the development process of railway basis for the structure and implementation of the library brakes. with Modelica in Dymola. Varying requirements concern- Systems engineering is an approach that enforces sys- ing the accuracy and the computational effort of the mod- tem architects to deduce physical solutions by identifying els are considered and the generic composition and di- stakeholders, specifying their requirements and map them verse configuration variants of railway brake systems are by system functions. Thereby, an interdisciplinary and respected. After the presentation of the library it is applied holistic view of the desired system is generated, which is to model and simulate the brake systems of a passenger deepened throughout the design process. By this means, and a freight train. The development of the library is an mistakes are identified and eliminated in early design ongoing work. This paper is primarily meant to motivate phases before costly changes during the implementation its usage and to present the modeling concept. An outlook are necessary. Due to the increasing complexity and func- is given which states the current limits of the library and tionality of technical systems arising from the increasing motivates further investigations. 236 PROCEEDINGS OF THE 1ST AMERICAN MODELICA CONFERENCE DOI OCTOBER 9-10, 2018, CAMBRIDGE, MASSACHUSETTS, USA 10.3384/ECP18154236 2 Systems engineering of railway brakes 2.1 Introduction to railway brakes The main functions of railway brake systems are (i) the conversion of kinetic energy in order to reduce the veloc- ity of the train, (ii) to counteract the downhill-slope force in order to keep the velocity of the train and (iii) to prevent a stationary train of moving due to gradients or other ex- ternal forces, for instance caused by wind (Knorr-Bremse, 2003). The basic safety requirements demand that all types of railway vehicles have an automatic, continuous and inex- Figure 1. Classification of railway brakes according to (Knorr- haustible brake system. This means that the brake sys- Bremse, 2003) tems of all cars of a railway vehicle are controlled by a through signal line (continuity) and that in case of an error in this signal line caused by leakage or cutoff, each of the tread and disc brakes, which are mostly activated by com- cars of the vehicle stops automatically. Inexhaustibility pressed air except for trams which use hydraulic media requires that the performance of the brake system is still due to the limited available space in these vehicles. Ad- available, although there have been repeated brake appli- ditional brake systems, e.g., electro-dynamic brakes in cations before (DIN EN 14198, 2005)(DIN EN 15734-1, electrically driven vehicles and hydro-dynamic brakes in 2013). The brake distance in case of emergency brak- diesel-hydraulic vehicles, are applied to serve as service ing is the major performance requirement brake systems brakes and to support the frictional brakes in order to min- have to meet. The maximum brake distances of loco- imize wear and thus extend the technical lifetime of brake motives and passenger trains required by (Commission systems. Non-adhesion dependent systems, for instance Regulation (EU) No 1302/2014, 2014) is shown in Ta- track-brakes, are not limited by the maximum transferable ble 1 relating to different velocities. Additionally, the force between rail and wheel. They are deployed to min- mean value of the corresponding deceleration is given as- imize the braking distance in case of an emergency. The suming a constant deceleration. This value does not in- faultless cooperation and redundancy of the diverse sub- clude the delay and response time of the brakes as well as systems is an important aspect for the safe, secure and re- the velocity-dependent adhesion between wheel and rail liable operation of trains. limiting the maximum feasible deceleration described in chapter 4.2.4.5.2 and 4.2.4.6.1 in (Commission Regulation 2.2 Systems engineering (EU) No 1302/2014, 2014). Depending on the type of system there are different process models which determine the design procedure Table 1. Brake distance requirements for emergency braking of systems. Haberfellner and Daenzer differentiate be- of locomotives and passenger trains relating to different ini- tween plan-driven methods, such as the "V-Model" or the tial velocities according to (Commission Regulation (EU) No 1302/2014, 2014) "Waterfall-Model" and agile methods, such as "Scrum" or the "Spiral-Model" (Haberfellner and Daenzer, 2002). The latter methods are commonly used for software engi- Initial Mean km Required m neering in which flexible and less sequential frameworks velocity brake distance [m] deceleration h s2 are preferred due to the dynamic and changing environ- ment throughout the development process. In contrast, 350 5360 0.88 plan-driven methods are characterized by fixed steps and 300 3650 0.95 defined sequences during the development process. This 250 2430 0.99 is essential for the design of large multi-physical systems 200 1500 1.03 which are subject to high requirements regarding safety and reliability, such as railway brake systems. In order to fulfill these requirements and functions rail- The most common plan driven method is the "V- way vehicles are equipped with different types of brake Model", as shown in Figure 2. The basic idea is to fol- systems, shown in Figure 1, depending on the type of ve- low a structured top-down development process. At first hicle (passenger cars, freight cars, locomotives) and its op- the stakeholders are identified, who are the source of the erating modes (service brake, emergency brake, parking system requirements from which in turn the system spec- brake, holding brake). ifications are deduced (Haberfellner and Daenzer, 2002) Due to its high level of safety all railway vehicles are (INCOSE, 2015). During the top-down development pro- at least equipped with frictional brake systems, such as cess the specifications of the system are disassembled into DOI PROCEEDINGS OF THE 1ST AMERICAN MODELICA CONFERENCE 237 10.3384/ECP18154236 OCTOBER 9-10, 2018, CAMBRIDGE, MASSACHUSETTS, USA Figure 2. "V-Model" as development process of railway brake
Details
-
File Typepdf
-
Upload Time-
-
Content LanguagesEnglish
-
Upload UserAnonymous/Not logged-in
-
File Pages10 Page
-
File Size-