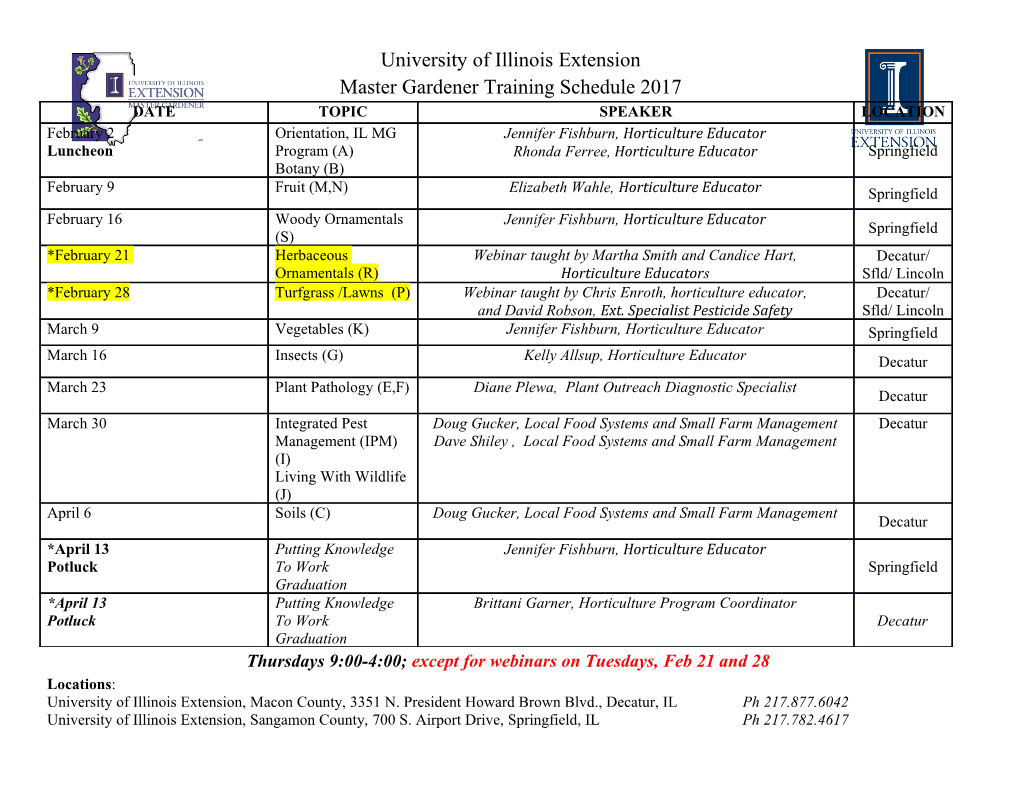
,.. Technology Programme /’ ‘, -’& /.. , f--“><d“-’2’3 v-“““\,,,. SULA2 “:;;’-:’’””“Fi; A?’‘.$’:.-,.,(‘~~-J ..’++Energy in Steel and Base Metal Production .,-’-4 .,> $9 4$m, Q7 Final Report Association of Finnish Steel and Metal Producers TECHNOLOGY DEVELOPMENT CENTER FINLAND ,, ;, ‘,1 ,,, +’”; ,. :! ‘:’f ‘,! DISCLAIMER Portions of this document may be illegible in electronic image products. Images are produced from the best available original document. , ,,“, 4, 1 Technology Programme SULA 2 Energy in Steel and Base Metal Production Final report Association of Finnish Steel and Metal Producers TECHNOLOGY DEVELOPMENT CENTRE Helsinki 1998 ISSN 1237-8941 ISBN 95 I -817-690-6 Cover picture Freddi.com Page Iayow DTPage Oy Printers: Tammer-Paino Oy, 1998 Foreword Ever since the 1970’s efilcient use and conservation of energy has been one of the most essential elements in the pursued energy policy. The advantage for the economy of both the nation and its industry and commerce through savings in the use of energy has been the fundamental motive and starting point. Recent years also indicate an emphasis in the efforts to improve the environment’s state and in the prevention of changes in the climatic conditions. New research data and technology have proved to be key factors in the search for more effective ways to save energy. Supporting research in order to find these ways has been a matter that is politically neutral and easily acceptable to all parties involved. The starting point in the research for energy savings in the national level was rather simple: the largest saving potential can be found in the most energy intensive industries. Many of the worst shortcomings in the use of energy have been adjusted already during the 1980’s. Furthermore, it was noticed on the way that necessary knowledge and know-how of technology and processes have been improved, and that it could also be a notable opportunity as regards entrepreneurial activity and exports for equipment suppliers in the energy intensive process industry. Based on this observation two programmed were started in the process industxy. One is called SUSTAINABLE PAPER that concerns energy economical manufacture of paper and board, and the other being SULA 2 that deals with energy economical pro- duction methods and technology for steel and metals. The goals in the SULA 2 programme concentrate on improving the competitiveness of metal producing companies in their own production units by using new energy and process technology. Flash smelting of copper and nickel, production of fer- rochrome and stainless steel, blast furnace automation and expert system in a cokhg plant are examples on the studied technologies within the programme, as well as examples of cases where the results of the programme have given notable support to sales of equipment and export of technology. The results of the six- year-programme, costs being little over 130 million FIM, can be considered suc- cessful, as the value of energy saved alone in the production units of the companies involved has been over 45 million FIM annually. The final report has been edited by the director of the programme, Hiikan Hakulin, of the Association of Finnish Steel and Metal Producers. In this final report have been presented the most central results of 50 research and development projects. The programme has been evaluated as a part of the international evaluation of all energy programmed. The international part has been published in a separate eva- luation repofi. Helsinki, August 1998 TEKES, Technology Development Center Finland 3 Abstract SULA 2 is the energy research programme of the The total research costs are ca. 130 million FIM. “ steel and metal producing industry. Central steel The major part of costs is carried by the participat- ‘t ,., and metal producing companies are Outokumpu, ing companies, 62 % and by public funding (Min- 3 ‘,,, ,, Rautaruukki, Imatra Steel and Fundia Wire which istry of Trade and Industry, TEKES, The Academy is a subsidiary of Rautaruukki. of Finland) 36 9Z0. ,: ;, The general objectives of the SULA 2 programme In six projects the objective of research was study- ing and inventing new production processes or ,.’ are: f., ● .!- :’ Lowest possible specific energy consumption equipment. Results so far are a new production ● Harmful emissions in air and water must not process for the Tomio stainless steel plant and a exceed internationally agreed standards new design of ore concentrate rotary dryer, which ● Best possible utilization of raw materials has been commercialized. The electric energy con- ● Best possible utilization of by-products and sumption of the melting shop in Tomio has de- waste heat creased by 25 1%0, and the production capacity has ● Reducing the amount of process waste and util- increased accordingly. izing this waste, economic aspects permitting The objective of all the other projects is improving The priorities of the SULA 2 programme are in the production processes used by the involved com- process development. Worthwhile areas of concen- panies. In 12 projects the process fundamentals tration in energy research by Finland include the have been investigated and in 32 projects the aim following: has been direct applications. -, . Iron and steel production . Zinc production Considerable savings in production process energy . The production of ferrochromium and stainless consumption, estimable from production reports steel have been achieved in several projects. The total ● The pyrometallurgical production of copper and amount of estimable saving in specific energy con- .’ nickel sumption is about 900 TJ/y (fuels and reductants) } . Rolling and heat treatment of steel plus 80 Gwh/y (electric energy) with a value of about FIM 45 million. Most energy has been saved addition to the steel and metal producers the in Rautaruukki Steel’s coking plant and blast fur- ,, In following companies participate in some projects: naces, in Outokumpu Steel’s ferrochrome plant and Kuusakoski, Kumera, Fiskars Tools and BET- stainless steel melting shop, as well as in Imatra { KER. Research work is performed in the following Steel’s melting shop. universities and research centers: Helsinki Univer- sity of Technology, OuhI University, ~bo Akademi Reduced production costs, not directly related to University, Tampere University of Technology, energy, in the order of FIM 10 million/y are VTT Energy and VTT Building Technology. achieved both in Rautaruukki Steel’s blast furnace plant by increased oil injection and in the steel plant The total number of projects in SULA 2 pro.- by better yield in the desulphurizing process. , gramme is 51. Of these 20 are research institute projects, 21 are company R & D projects and 10 It is thus estimated that the direct annual cost are energy conservation projects funded by Minis- reduction is about FIM 72 million. Six projects ‘: try of Trade and Industry. have addhionally contributed to a substantial in- 5 . crease in production capacity. There are also pro- the SULA 2 programme. This network combines jects of which the impact is difficult to be meas- expertise from the SULA 2 and LIEKKI 2 pro- ured, and some projects with results that have not grammed. so far been implemented in the production proc- esses at all. Therefore, the actual economical result Through the programme it has been possible to do is better than the measurable result. more research work on metallurgical processes in the technical universities. A centre of competence As a result oft wo projects the air pollution at Imatra in the blast furnace process has been created at the Steel plant in Imatra has been eliminated and sub- University of Oulu in the course of the programme, stantially reduced at Koverhar steel plant. The sub- and HUT has founded a CFD technology applica- stituting of coke for high sulphur residual fuel oil tion centre at the Laboratory of Materials Process- at Rautaruukki’s and Koverhar’s blast furnaces is ing. The programme has generated three doctoral also environmentally important. dissertations, nine licentiate’s theses and 63 mas- ter’s theses. Two further doctoral theses will be A new cross-disciplinary network focusing on finished this year. blast furnace oil injection has been created within 6 Contents “ Foreword . 3 Abstract . 5 , ,, I GENERALVIEW . 9 Background, Objectives and Participants. ...9 Funding . ...10 Programme organization and Management Groups . II 2PROJECTREPORTS . 13 iron and Steel Production . 13 New Technologies and Raw Materials for lronand Steelmaking . 15 improvement of High Temperature Properties of iron Ore Agglomerate . ...21 Utilization of Dust . ...34 The New Coke Oven Battery Heating Control Systems at Rautaruukki Steel.. 39 The Blast Furnace Process Research at the Universityof Oulu . ..48 System foBlast Furnace Superti~on and Process Operator ~d(SPO) . 58 Burden Control by Artficial intelligence . ...60 lnterpremtion and Control of Blast Furnace Wall Tempemtures and Heat Loads. 64 Modelling and Prediction of Pig h-on Variables in the Blast Furnace . 69 Modelling ofTurbulent Combustion Blast Furnace Raceway . ...73 High Oil injection Rate in Blast Furnace Process . ...77 Changing from 100 %Sinter Burdento 100 %Pellets in Koverhar . 82 Suitability of Plastic Waste for Blast Furnace Fuel . ...89 Neural Networks Modelling for Blast Furnace Process . ...97 Slags in Steelmaking . ...105 Consim Program for BOF-Control . ...114 Post Combustion in Converter Process . ...127 The EAFMelting Shop Projector lmatra Steel, lmatra Steelworks. 128
Details
-
File Typepdf
-
Upload Time-
-
Content LanguagesEnglish
-
Upload UserAnonymous/Not logged-in
-
File Pages256 Page
-
File Size-