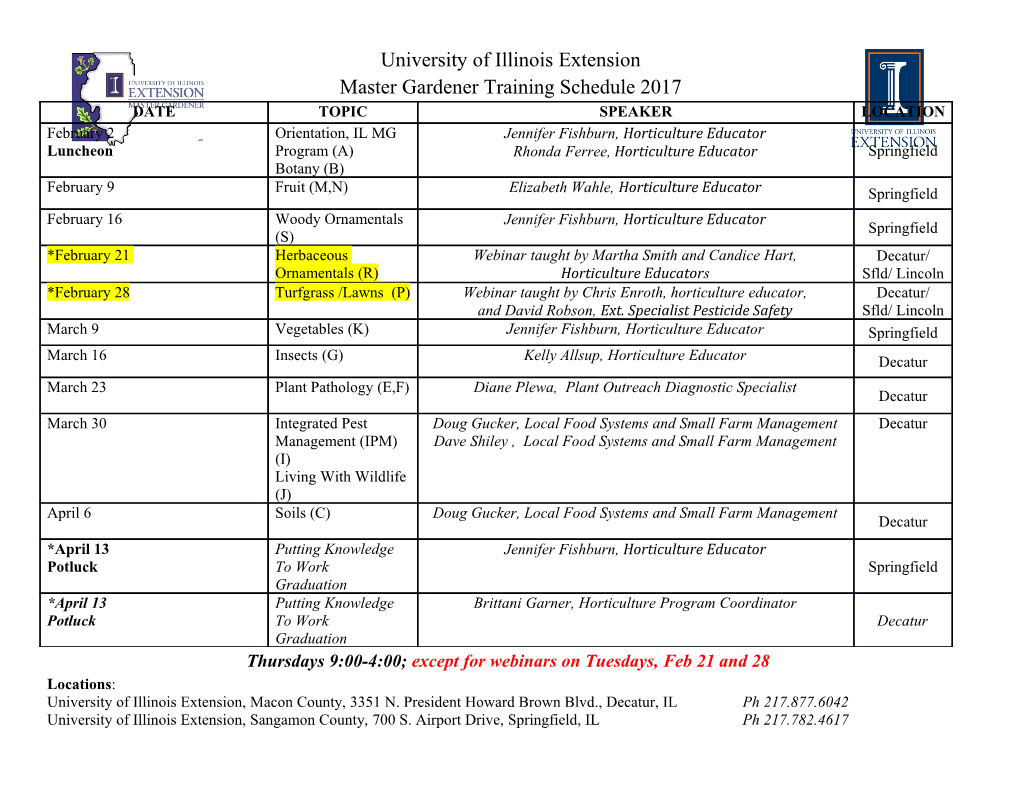
United States Department of Agriculture Rough Mill Improvement Forest Service Guide for Managers and Northeastern Research Station Supervisors General Technical Report NE-329 Philip H. Mitchell Jan Wiedenbeck Bobby Ammerman Abstract Wood products manufacturers require an efficient recovery of product from lumber to remain profitable. A company’s ability to obtain the best yield in lumber cut-up operations (i.e., the rough mill) varies according to the raw material, product, processing equipment, processing environment, and knowledge and skill of the rough mill’s employees. This book discusses several key principles that can help manufacturers understand and solve yield and production problems. Our publication was inspired by the 1981 publication “Rough Mill Operator’s Guide” written by Edward K. Pepke and Michael J. Kroon. Computer-based technologies and new rough mill layouts and equipment are prevalent in today’s rough mills, therefore, they are given considerable emphasis in this contemporary version of the Pepke-Kroon guide. The Authors PHILIP H. MITCHELL is a wood products extension specialist at North Carolina State University in Raleigh, NC. JAN WIEDENBECK is a Project Leader with the USDA Forest Service, Northeastern Research Station in Princeton, WV. BOBBY AMMERMAN is an extension associate at the University of Kentucky in Quicksand, KY. Manuscript received in publications 12 September 2003 Published by: For additional copies: USDA FOREST SERVICE USDA Forest Service 11 CAMPUS BLVD SUITE 200 Publications Distribution NEWTOWN SQUARE PA 19073-3294 359 Main Road Delaware, OH 43015-8640 June 2005 Fax: (740)368-0152 Visit our homepage at: http://www.fs.fed.us/ne Foreword Wood product companies require an effi cient recovery of product from lumber to remain profi table. A company’s ability to obtain the best yield in lumber cut-up operations (i.e., the rough mill) varies according to the raw material, product, processing equipment, processing environment, and knowledge and skill of the rough mill’s employees. This book discusses several key principles that can help manufacturers contemplate and solve yield and production problems. In 1981, Edward K. Pepke and Michael J. Kroon published Rough Mill Operator’s Guide, which has gone out of print. Since that time, the proliferation of computer technology has changed the way many rough mills operate. With advanced technology, there is a need to educate operators and managers. Without education and training, the technology is often ineffective, or worse, it is detrimental to the goal of improving rough mill performance. Clearly, there is a need for a contemporary version of the guide. However, many of the principles presented by Pepke and Kroon are still valid. Both the newer technologies and processing strategies and the long-established methods that still apply are discussed in this publication “Rough Mill Improvement Guide for Managers and Supervisors,” and a future companion publication, “The Rough Mill Operator’s Guide.” Our initial goal was to update the “Operator’s Guide.” However, in preparing for rough mill improvement workshops, we realized there also was a lack of updated educational materials for managers and supervisors. This book is a compilation of material the authors generated to teach the workshops. The “Operator’s Guide” will be published separately, and together with this publication, will provide a pair of useful educational resources for rough mill owners and operators. This book is divided into three sections. The fi rst section covers the importance of product yield as it relates to value, the impact of lumber grade and quality characteristics on yield, and the use of part grades and scheduling in the rough mill. The second section reviews both traditional and modern cut-up operations in the rough mill, focusing on the major processes of ripping and crosscutting lumber. The third section presents additional issues and operations that impact yield, such as the lay- up of edge-glued panels, fi ngerjointing, and moulders. Both this publication and the operator’s guide were inspired by the earlier work of Pepke and Kroon. Their 1981 operator’s guide has been in great demand for many years. We thank them for the information they assembled and conveyed in that publication and for the good sense they demonstrated in developing a guide that targets the rough mill operator. Technology development will surely continue at a rapid pace. However, it is our hope that the principles discussed in this book will remain valid over many years as have the principles that originally were conveyed by Pepke and Kroon. i Contents Foreword ........................................................................................................................i Table of Figures ........................................................................................................... iv Section 1: Product Yield, Value, and Quality Requirements ..................................1 Lumber Processing Effi ciency, Yield, and Value .......................................................2 Impact of Lumber on Yield and Value ......................................................................8 Part Grades and Rough Mill Scheduling ................................................................13 Section 2: Traditional and Modern Cut-up Systems ..............................................17 Optimizing Operations on a Manual Crosscut Saw ...............................................24 Yield Improvement in Manual Ripsaw Operations in the Crosscut-fi rst Rough Mill .........................................................................................................31 Gang Ripsaw Practices in the Rip-First Rough Mill ..............................................37 Optimizing Crosscut and Chop Saw Operations ...................................................43 Section 3: The Panel Lay-up, Fingerjointing, and Moulding Operations ...........49 Panel Lay-up Operations ........................................................................................50 Improving Rough Mill Yield by Fingerjointing ......................................................55 Improving Rough Mill Yield at the Moulder ..........................................................57 iii Table of Figures Figure 1.—Where do the dollars go in rough mill manufacturing? (Wood Component Manufacturers Association 1999.) .....................................................................................2 Figure 2.—Producer price indices for hardwood lumber and household furniture, adjusted to 1982=100. ......................................................................................................2 Figure 3.—Approximate value increase of 1 board foot of lumber as it is processed by each operation through the rough mill (adapted in 2000 from Pepke and Kroon 1981 by applying an infl ation factor of 1.8). .....................................................................3 Figure 4.—Annual part cost savings from a 1 percent yield improvement for the rough mill processing 12 Mbf per day with 16 employees (dotted lines indicate a 10 percent increase in throughput, or 13.2 Mbf processed per day, with no increase in labor cost). ....................................................................................................................7 Figure 5.—Steps in a small-scale, fi ve-board, rough mill yield study -- rip-fi rst example. .......8 Figure 6.—A screen image of the main menu of the ROMI 3.0 cut-up simulation program. .........................................................................................................................10 Figure 7.—FAS grade lumber, pictured at the top, typically is signifi cantly wider than Selects grade lumber, pictured at the bottom. ..................................................................12 Figure 8.—Split, stain, and wane defects that run for some distance along the length of the board are best removed in a rip-fi rst operation. ......................................................20 Figure 9.—Defect clusters and large defects that occupy a signifi cant cross-section of the board are best removed in a crosscut-fi rst operation. ..................................................20 Figure 10.—Forms of lumber warpage — sidebend, also known as crook, is the most prevalent form encountered in hardwood processing operations. ............................21 Figure 11.—The initial end trim at the crosscut saw can be minimized with the use of a mirror. ......................................................................................................................24 Figure 12.—Long end splits usually should be removed at the ripsaw rather than at the crosscut saw. ..............................................................................................................25 Figure 13.—Removal of wane and knots using crosscuts, rips, and salvage cuts; full-width dashed lines show the fi rst crosscut, horizontal dashed lines show rip cuts performed on the shorter pieces, light vertical lines show chop cuts made on the already crosscut and ripped strips. ...............................................................................................25 Figure 14.—Large defects and those extending across the board width should be removed at the crosscut saw: A) Cuts should be made to remove spike knots and fuzzy grain; B) Solid line indicates patterns to be cut at band saw, thus eliminating knot. ..................26 Figure 15.—The manual cut-off saw’s basic layout. The backgauge
Details
-
File Typepdf
-
Upload Time-
-
Content LanguagesEnglish
-
Upload UserAnonymous/Not logged-in
-
File Pages69 Page
-
File Size-