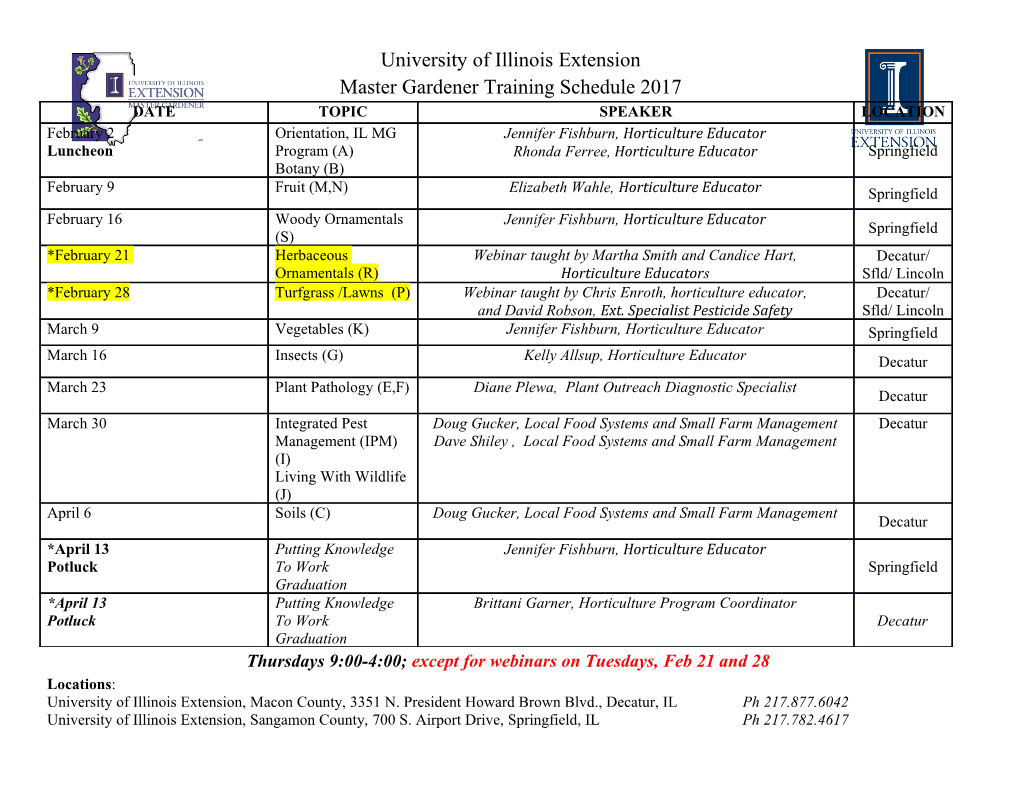
Korea-Australia Rheology Journal, 29(4), 317-323 (November 2017) www.springer.com/13367 DOI: 10.1007/s13367-017-0031-1 Process viscometry in flows of non-Newtonian fluids using an anchor agitator Hae Jin Jo1, Hye Kyeong Jang1, Young Ju Kim2,† and Wook Ryol Hwang1,* 1School of Mechanical Engineering, Gyeongsang National University, Jinju 52828, Republic of Korea 2Exploration System Research Department, Korea Institute of Geoscience and Mineral Resources, Pohang 37559, Republic of Korea (Received Octrober 18, 2017; final revision received November 5, 2017; accepted November 13, 2017) In this work, we present a viscosity measurement technique for inelastic non-Newtonian fluids directly in flows of anchor agitators that are commonly used in highly viscous fluid mixing particularly with yield stress. A two-blade anchor impeller is chosen as a model flow system and Carbopol 940 solutions and Xan- than gum solutions with various concentrations are investigated as test materials. Following the Metzner- Otto correlation, the effective shear rate constant and the energy dissipation rate constant have been esti- mated experimentally by establishing (i) the relationship between the power number and the Reynolds num- ber using a reference Newtonian fluid and (ii) the proportionality between the effective shear rate and the impeller speed with a reference non-Newtonian fluid. The effective viscosity that reproduces the same amount of the energy dissipation rate, corresponding to that of Newtonian fluid, has been obtained by mea- suring torques for various impeller speeds and the accuracy in the viscosity prediction as a function of the shear rate has been compared with the rheological measurement. We report that the process viscometry with the anchor impeller yields viscosity estimation within the relative error of 20% with highly shear-thinning fluids. Keywords: agitators, process viscometry, torque measurement, Metzner-Otto correlation, non-Newtonian fluids 1. Introduction measurement on the shaft. The Metzner-Otto method is a heuristic approach in quantifying the total energy dissipa- Mechanical agitation involving physical or chemical tion rate in non-Newtonian flows in an agitator by intro- changes in a stirred vessel is commonly encountered in a ducing the effective shear rate concept (Metzner and Otto, wide variety of process industries such as food, plastics, 1957). It is popular in the mixing community and indeed rubbers, mining and waste water treatment (Paul et al., is considered as a ‘single major practical technique for 2003). Among others, fluid mixing in a laminar regime is incorporating non-Newtonian effect’ in agitator analyses. considered as a difficult operation particularly with highly It has been mainly used in the field of mixing for non- viscous yield stress fluids such as gels, slurries and drill- Newtonian fluids relating to power requirement, heat ing muds, due to the formation of nearly unyielding region transfer, blend time and viscosity measurement (Doraiswamy away from the rotating impeller. In this particular case, the et al., 1994). anchor-type impeller with close clearance between impel- As was indicated by Doraiswamy et al. (1994), the ler blades and vessel walls is frequently employed in spite Metzner-Otto method has been frequently used in quan- of its poor mixing performance, as it minimizes unyield- tifying the energy dissipation rate as a function of the ing region over the entire vessel (Pedrosa and Nunhez, Reynolds number and a representative (effective) shear 2000). Process characterization and monitoring are neces- rate in non-Newtonian fluid flows inside an agitator. sary to control the mixing process in agitator system espe- Nagata et al. (1971) studied the power consumption of cially with rheologically complex fluids in a laminar shear-thinning liquids with various impellers using the regime and the process viscosity measurement would be a Metzner-Otto correlation. Similar works were reported in right choice in this purpose. literatures: The power consumption with thixotropic liq- In this work, we present an experimental method to uids (Edwards et al., 1976); the power requirement pre- measure the process viscosity for a flow in an anchor agi- diction from experimental data with a helical ribbon tator with non-Newtonian fluids. The present work fol- impeller (Shamlou and Edwards, 1985); analytical mod- lows the Metzner-Otto correlation in estimating the eling the energy dissipation rate with a helical ribbon viscosity of rheologically complex fluids using the torque impeller and effects of fluid viscoelasticity on the power characterization (Carreau et al., 1993); the power con- sumption with the anchor impeller by 3D numerical sim- *Corresponding author; E-mail: [email protected] †Co-corresponding author; E-mail: [email protected] ulation and experimental validation (Tanguy et al., 1996). © 2017 The Korean Society of Rheology and Springer pISSN 1226-119X eISSN 2093-7660 317 Hae Jin Jo, Hye Kyeong Jang, Young Ju Kim and Wook Ryol Hwang 3 5 Literatures on the application of the Metzner-Otto method Np = P/ρN D (2) to the viscosity measurement using the agitator are rela- tively rare compared to the power characterization. Brito with ρ and D being the fluid density and the impeller De La Fuente et al. (1998) measured the process viscosity diameter, respectively. The flow regime can be identified using the helical ribbon impellers experimentally and with the Reynolds number and it is defined as Re = ρND2/ reported highly accuracy viscosity measurements with μ conventionally in the mixing community. In case of a complex fluids. Similar studies on food materials with laminar flow (Re≤10 )of a Newtonian fluid with a viscos- helical ribbon impellers were investigated by Eriksson et ity μ, the torque on the shaft and the power draw scale al. (2002). with μND3 and μN2D3, respectively, and therefore the In this work, we present an experimental process vis- power number Np appears reciprocal to the Reynolds num- cometry based on the Metzner-Otto correlation for flows ber Re with a constant Kp: in anchor agitators with inelastic non-Newtonian fluids. A Np = Kp/Re.(3) two-blade anchor impeller is chosen as a model flow sys- tem and Carbopol 940 solutions and Xanthan gum solu- The symbol Kp is the energy dissipation rate constant, tions are investigated as test fluid materials. Following the which is a function of flow geometries only and measures Metzner-Otto correlation, the effective shear rate constant the amount of the rotational drag on the impeller. From 3 and the energy dissipation rate constant have been esti- Eq. (3) the torque on the shaft becomes KpμND /2π inside mated experimentally by establishing (i) the relationship the agitator in a laminar regime. between the power number and the Reynolds number and The Metzner-Otto correlation claims that the reciprocal (ii) the proportionality between the effective shear rate and relationship between the power number and the Reynolds the impeller speed. The effective viscosity has been number (Eq. (3)) can be reproduced even for non-New- obtained by measuring torques for various impeller speeds tonian fluids with the same constant Kp, if the Reynolds and the accuracy in the viscosity measurement as a func- number is properly corrected (Metzner and Otto, 1957). tion of the shear rate has been compared with the rheo- The corrected Reynolds number is the effective Reynolds logical measurement. number Reeff, defined with the effective viscosity μeff; and the effective viscosity μeff is the viscosity at the effective · 2. The Metzner-Otto Method shear rate γeff , which was defined in Eq. (1). That is, 2 · Np = Kp/Reeff, Reeff = ρND /μeff , and μeff = μ()γeff .(4) In this section, we briefly review the Metzner-Otto method for the completeness of the present work. Flow in Once the two flow constants Kp and Ks are known, one an agitator is complex and highly non-uniform even in a can predict the viscosity as a function of the flow rate by laminar regime due to the rotation of impellers of non- measuring the torque in a complex flow like an agitator trivial shapes such as the anchor or helical ribbon impel- system as follows. Firstly, for a given set of the torque and lers particular for highly viscous fluids (Paul et al., 2003) the impeller speed, one can determine the power number and the complexity in the flow field becomes much con- Np as well as the corresponding effective Reynolds num- siderable with the presence of non-Newtonian fluids. ber. Then the effective viscosity is determined directly Metzner and Otto (1957) proposed a constant factor to from the effective Reynolds number and, plotting the define a representative (or effective) shear rate, multiplied effective viscosity as a function of the effective shear rate by the impeller speed N in characterizing the power draw (Eq. (1)), the flow curve of a non-Newtonian fluid is then for a flow in an agitator: obtained. The above procedures can be easily imple- · mented experimentally. γ eff = Ks N .(1) The effective shear rate constant Ks is hypothesized to 3. Experimental Methods depend on impeller shapes and tank geometries only, inde- pendent of rheological behaviors of fluids. In fact, Ks has In this work, we employed an anchor impeller in a flat turned out to be ‘nearly’ a constant for a given agitator bottomed vessel and a motor-driven stirrer with the torque geometry, primarily with the impeller type and there are a measurement unit as a model viscosity measurement sys- couple of known constants
Details
-
File Typepdf
-
Upload Time-
-
Content LanguagesEnglish
-
Upload UserAnonymous/Not logged-in
-
File Pages7 Page
-
File Size-