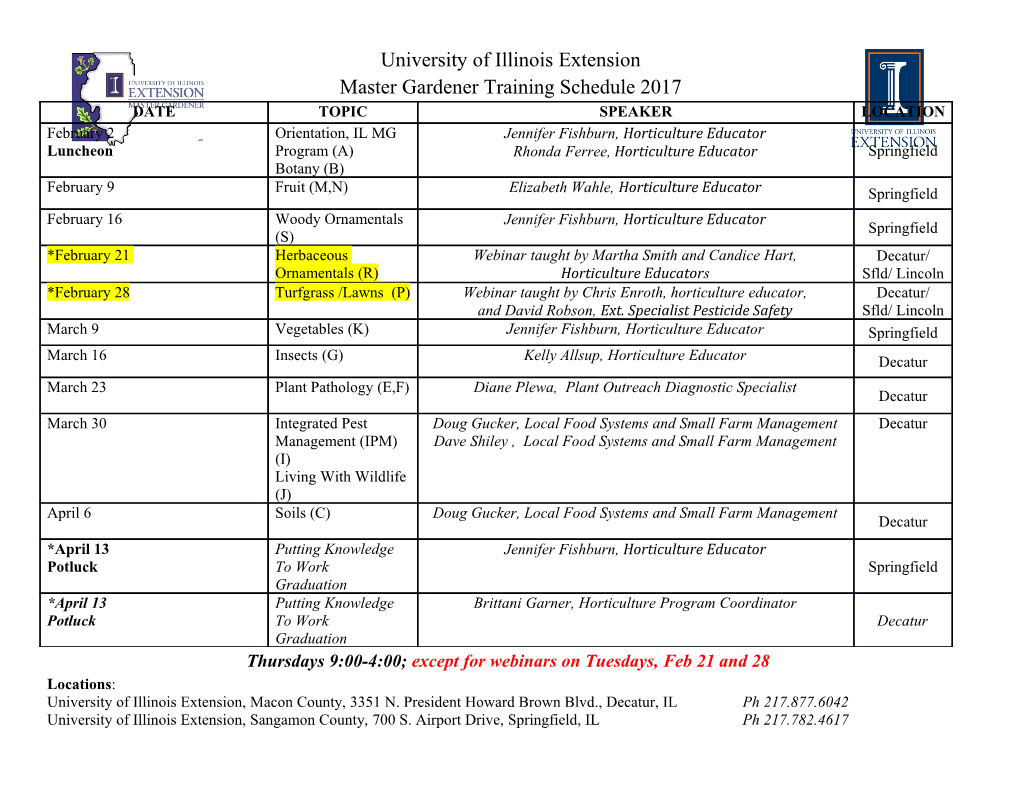
ue to advantages in economics, constructability, and aesthetics, Lessons the construction of mechanically stabilized earth (MSE) walls is Dnow commonplace. An MSE wall consists of Learned soil, reinforcement, and facing to retain earth and support overlying structures (Figure 1). Thirty- to forty-foot high walls are not uncom- problems and solutions mon. Reinforcement often consists of geogrids encountered by practicing or steel reinforcement strips, while the facing structural engineers commonly consists of segmental precast con- crete units, gabion baskets, metallic panels, or geosynthetic facing. There are many different MSE wall construction materials, making it more important for Contractors and design Engineers Figure 1: Typical MSE Wall Cross-Section. to understand how the products work with the ® remainder of the system. afterthought. The plans show a bold black line at For various reasons, some systems fail and require the property line to represent the retaining wall costly repair (Figure 2). Based on lessons learned with the label “retaining wall – to be designed by from case studies, the authors discuss common others,” with a 30-foot grade change from the top pitfalls of MSE wall design and construction, in to the bottom of the wall. The exposed side of Copyrightthe form of a hypothetical the wall will be visible from local neighborhoods case study. and a shopping center. The marsh is just outside Mechanically Stabilized the limit of the retaining wall. It’s Just a The Contractor submits a bid that utilizes an Earth Walls MSE wall, and engages a Fabricator who provides Retaining Wall… proprietary masonry blocks for MSE systems. The Pitfalls in Design Don’t Sweat It! Fabricator works with a design Engineer who is not local to the site, but regularly designs the proprietary and Construction An Owner selects an affordable but complex site MSE system. The Fabricator and his design Engineer to construct a retail outlet with four, one-story assemble their standard design plans using subsur- By Scott J. DiFiore, P.E. and buildings. The multiple-acre site slopes signifi- face information and recommendations from the Bryan P. Strohman, P.E. cantly frommagazine west to east, with more than 40-feet geotechnical report. They do not visit the site, discuss S Tof grade R differential, U and a Cmarsh at Tthe lower U the subsurface R conditions E with the Geotechnical elevations covering less than 10 percent of the site. Engineer, review the site topography and utilities The Owner engages a Geotechnical Engineer to: with the Civil Engineer, or discuss whether soil drill one boring beneath each building, perform backfill will be imported or reused from the site Scott J. DiFiore, P.E. is a soil gradation tests, and prepare a report with development work. The design plans provided to senior project manager at site grading, building foundation, and generic the Contractor contain notes stating that others Simpson Gumpertz & Heger retaining wall recommendations. Site soils, from are responsible to check the bearing capacity below Inc., Waltham, Massachusetts. the limited boring data, vary from clayey sand the wall, the settlement of the wall, and the slope He can be reached at to sandy clay. stability of the wall and retained backfill. [email protected]. The Owner hires a Civil Engineer to layout the The Owner hires the Geotechnical Engineer at roadways, parking lot, buildings, and site utili- the start of construction to perform periodic site Bryan P. Strohman, P.E. is a ties. Site utilities include pressurized waterlines, inspections. However, the Geotechnical Engineer Senior Staff II – Structures at sanitary sewer lines, and a storm drainage pipe was not involved with the project through the Simpson Gumpertz & Heger system to collect runoff from the roadway, parking course of the site or retaining wall design. The Inc., Waltham, Massachusetts. lot, and roof drainage. The retaining wall is an Geotechnical Engineer assigns his recently pro- He can be reached at moted professional engineer (Inspector) to monitor [email protected]. site and retaining wall construction, who has no experience with MSE walls. The Inspector visits the site daily and diligently conducts compaction test- ing on the onsite clayey fill placed in the reinforced zone of the wall. The onsite soils vary significantly as the project progresses, due to the large amount of earthwork required, and the Inspector obtains new laboratory compaction data to correlate with the field-density tests. The Inspector observes water bearing utilities installed in the retained backfill, and storm drain manholes along the top of the wall Figure 2: Costly repairs to failed MSE wall. at the edge of the pavement. The Fabricator and 10 December 2012 STRUCTURE magazine • Settlement: Sands and gravels undergo immediate settlement, whereas fine-grained soils (clays and silts) are susceptible to long- term settlement (consolidation). The Geotechnical Engineer did not perform consolidation tests, and no one predicted the amount of wall settlement. If the wall settles over the long-term, the pavement, utilities, Figure 3: Water collecting in clay backfill buildings, and other site features will immediately behind MSE wall facing. go along for the ride. • Geogrid-Soil Interaction: The geogrids his design Engineer provided no specific wall interact with the soil through friction. drainage systems in the design. The Contractor Together, the geogrids and soil act constructs the wall from the specified modular as a gravity structure. Geogrid and ® blocks and geogrid reinforcement, and the reinforcing manufacturers regularly clayey site soils. test for interface friction with sand and The project team is primarily focused on the gravel backfill, but not always for silts building, utility, and pavement construction. and clays, which have different behavior. After all, the project is a retail center. But, as the The reinforcing could also be more project developed, the MSE wall became its own susceptibleCopyright to creep in clayey soils. significant construction project. It is up to 30-feet • Compaction: Fine-grained soils require high, next to an established neighborhood, with - For Advertiser ADVERTISEMENT Information, visit special attention to compaction water sources in the wall backfill, supports build- methods and moisture content, more ing foundations and a parking lot. Treating the so than sands and gravels which are MSE wall as “incidental” to the project could easier to compact. Poor compaction be disastrous. Is the project team giving the wall results in weaker soils, reducing soil- its due consideration? reinforcement interface friction and The Imperfect Site increasing wall pressures. • Soil Migration: As water flows through Much of the easily-developed land has already soil, it collects fine-grained particles been taken; this site has its development chal- magazineand transports them. If the wall www.STRUCTUREmag.org lenges. The primary developmentS consistsT of Rdesign U did not includeC filter T fabric orU R E four, simple one-story retail structures. Just other protective measures against soil bring the site to grade, install spread footings migration and erosion, the soil mass will and pavement, and the development is off and lose volume and strength, resulting in running. What has the project team neglected additional wall pressures and settlement. that could come back to haunt them? • Water Retention: Compared to sands Subsurface Data and gravels, fine-grained soils are orders of magnitude less permeable. By performing only four borings over a multi- Water readily collects on and within acre site, the team focused on the buildings, fine-grained soils Figure( 3), which, but neglected ancillary development which (a) introduces groundwater and includes significant earthworks and soil reuse. seepage forces, (b) reduces soil strength Retaining wall construction is near the edge (increasing wall pressures), (c) reduces of the marsh, which likely consists of unsuit- interface friction between backfill able compressible soils. Could unsuitable soils and reinforcing, and (d) in colder extend beyond the marsh and into the MSE environments introduces freeze-thaw wall area? Backfilling over the unsuitable soils cycles in soils at and below ground will result in settlement. What about other surface and just behind the facing, unclassified soils outside the building foot- which can create frost-jacking pressures. prints? Incomplete soil characterization could cause construction problems or project delays. Water, Enemy of the Wall Soil Backfill Water comes from a variety of sources (Figure Clayey soils dominate the site, which are 4 ), including precipitation, leaky utilities, intended for reuse. MSE walls ideally use irrigation in landscaped areas, and ground- sand and gravel backfill in the reinforced zone. water. Unless actively managed by the project How do clayey soils impact MSE wall design team, all sources can have detrimental effects and construction? on MSE walls. continued on next page STRUCTURE magazine11 December 2012 Open landscape areas are often located immediately at the top of the wall behind a curb line, or perhaps in islands set back from the wall. Irrigation lines and sprinkler systems, just like other water bearing utilities, Figure 4: Water sources include: (A) groundwater, are susceptible to leakage. (B) pressurized water lines, (C) storm drain • Infiltration: Rainwater and snow melt systems, (D) infiltration through open landscape infiltrate the ground through
Details
-
File Typepdf
-
Upload Time-
-
Content LanguagesEnglish
-
Upload UserAnonymous/Not logged-in
-
File Pages4 Page
-
File Size-