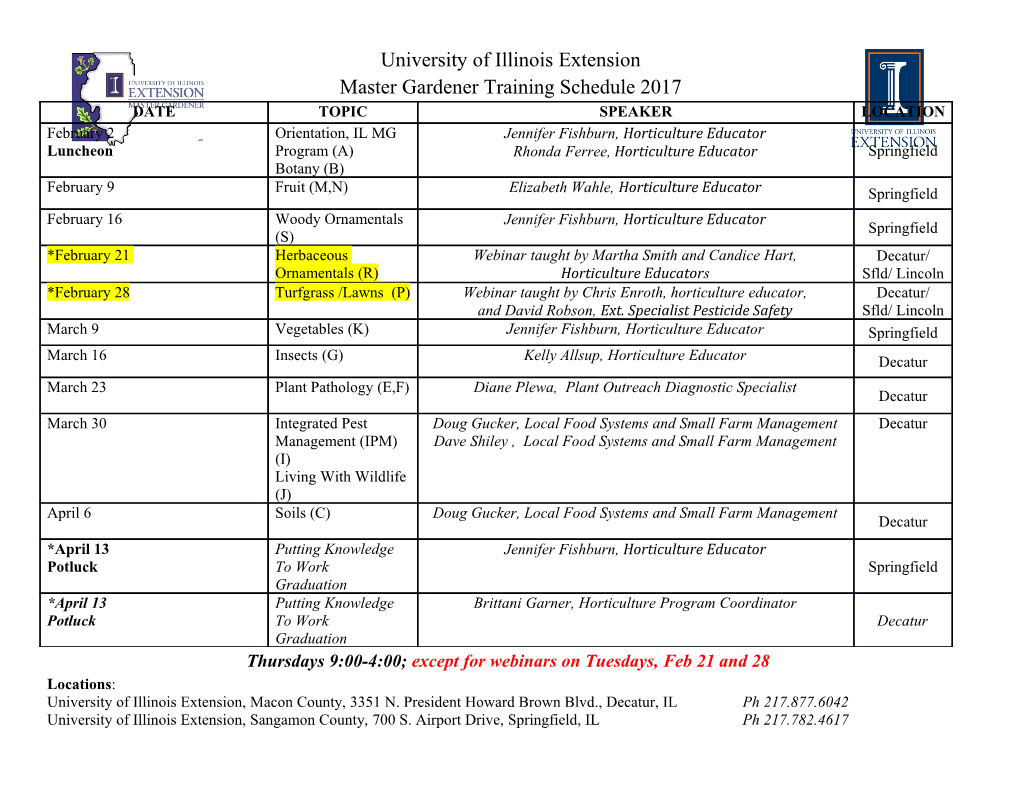
SP2020_00068 LUMEN – DESIGN OF THE REGENERATIVE COOLING SYSTEM FOR AN EXPANDER BLEED CYCLE ENGINE USING METHANE Jan Haemisch(1), Dmitry Suslov(2), Günther Waxenegger-Wilfing(3), Kai Dresia(4), Michael Oschwald(5) (1)-(5) Institute of Space Propulsion, DLR Lampoldshausen, Langer Grund, D-74239 Hardthausen, [email protected], [email protected], [email protected], [email protected], [email protected] KEYWORDS: LUMEN, HARCC, regenerative cool- 1 INTRODUCTION ing, machine learning, design optimization The regenerative cooling system for the LUMEN engine faces two major features: 1. Methane ABSTRACT as coolant. 2. Usage of the coolant in an ex- pander bleed system architecture. Methane has a much higher density, compared to hydrogen and The regenerative cooling still is one of the most cru- can therefore be stored in smaller, lighter tanks. Due cial parts in designing a liquid rocket engine. The to the higher density the turbopumps demand sig- goal of an effective design is a trade-off between nificantly less power. Additionally insulation can be a sufficient cooling of the structure and a low pres- saved due to a higher boiling point. Major drawback sure drop in the cooling channels. For an expander is a reduction of the specific impuls. Nevertheless type cycle a third requirement arises: A sufficient multiple LOX/CH or LOX/LNG engines are currently enthalpy increase of the cooling fluid for the turbop- 4 under development [4, 16, 3]. umps to operate effectively. To prevent the combus- Methane as coolant in regenerative cooling sys- tion chamber from melting, the regenerative cooling tems is a critical topic and a major concern for using has to be designed with a sufficient margin to re- methane as fuel for rocket engines. Methane has spect all uncertainties. A neural network based sur- a higher density and a lower specific heat at con- rogate model is used to study the robustness of the stant pressure c , compared to hydrogen. The main cooling channel design for other load points of the p different however is the vicinity to the critical point engine. that may lead to heat transfer deterioration (HTD) In this paper, the design of the regenerative cool- [13, 15, 23]. ing system and the manufacturing of a subscale The main goal of a common cooling channel de- combustion chamber will be discussed. sign is to maximize the cooling efficiency in other words to reach the minimal hot gas side wall temper- ature with a minimal pressure loss. The lower the NOMENCLATURE hot gas side wall temperature, the better the cool- ing performance since a temperature decrease of dT = 40K doubles the engine life time [10]. For α heat transfer coefficient [W=m=K] the cooling channel design of an expander-type en- gine a third goal arises: A sufficient increase of the cP specific heat capacity at constant pressure [J=kg=K] coolant enthalpy to drive the turbopumps. This goal h enthalpy [kJ=kg] is in opposite to the maximal cooling since a large temperature increase of the coolant goes along a ks roughness [m] L combustion chamber length [mm] high wall temperature. The enthalpy increase of the m_ mass flow [kg=s] coolant is the reason why expander-type engines n number of cooling channels [-] typical display a long cylindrical combustion cham- P pressure [bar] ber part [1]. Pcc combustion chamber pressure [bar] Pin inlet pressure [bar] 1.1 LUMEN Engine P outlet pressure [bar] out THE LUMEN (Liquide Upper Stage deMonstator ∆P pressure drop [bar] ENgine) is a Nozzle-Expander-Bleed (NEB) engine q_ wall heat flux [W=m2] w that uses methane as fuel and therefore also as T fluid inlet temperature [K] in coolant. The flow direction is counterflow for the T fluid outlet temperature [K] out nozzle and combustion chamber and coflow for the nozzle extension. Computational Fluid Dynamics 1 parameter unit value These goals are not independent since a higher enthalpy increase would increase the turbopump T [K] out > 400 performance and enlarge the allowed pressure T [K] w < 900 drop. The other way around, a lower pressure drop ∆p [bar] channel < 25 could potentially allow a lower enthalpy increase. Since the turbopump is not part of the calculation, the goals are set to be fixed. In future versions of Table 1: Goals for the cooling system design. the calculation, the feedback of the turbomachinery might be added. parameter unit value Due to manufacturing and structural reasons the cooling channel width [mm] ≥ 1 width of the cooling channel is at least 1 mm and width between cooling channels [mm] ≥ 1 the distance between the cooling channels has to distance to hot gas side [mm] 1 be at least 1 mm. The number of cooling channels number of cooling channels [−] ≤ 86 is a consequence of these constraints in the noz- zle throat. For the hot gas side wall temperature, the optimum is a constant temperature slightly be- Table 2: Constraints due to manufacturing and low the temperature limit. structural reasons. 2.2 optimization parameters (CFD) is a commonly used tool for the calculation of To reach the goals with the given boundary condi- heat transfer in cooling channels [26, 22, 15]. How- tions the geometry of the cooling channel can be ever most of the validation data is for hydrogen as varied. That includes the width and height along cooling fluid. Data for methane as coolant is rare the cooling channel length, a varying length of the [12, 14, 27, 20]. In addition to that, the physical cylindrical part of the combustion chamber and the properties rapidly change in the vicinity of the crit- number of cooling channels. The nozzle geometry ical point. These two points lead to significant de- remains fixed. Despite the geometry, the coolant viations of the CFD simulations, especially close to mass flow can be used as another parameter. The the critical point [15]. This has to be kept in mind LUMEN system architecture allows to vary the mass when discussing sufficient margin for the analysis. flow for the cooling channels within a certain range. The paper is divided into three parts: In the first The roughness is assumed to be constant. part a method is described and used to find the opti- Due to simplification and manufacturing reasons, mal cooling channel geometry for an expander type the cooling channel geometry can be changed at 5 engine. In the second part, a neural network model characteristic positions along the combustion cham- is presented and used to validate the found solu- ber length. In between the values are interpolated tion for different load points. The third part gives an linearly. Fig. 1 shows the positions depending on overview of the manufacturing process of the sub- the assumed heat flux profile. The characteristic scale combustion chamber. positions are the begin and end of the decreasing heat flux in the cylindrical part, the nozzle and the beginning and end of the combustion chamber. Ad- 2 PART I: OPTIMIZATION OF COOLING CHAN- ditionally the length of the cylindrical part (between NEL GEOMETRY h2 and h3) can be varied. Based on the boundary conditions and constrains, that are defined by a system analysis for the whole 2.3 Boundary conditions LUMEN engine, CFD simulations with varying ge- ometry were performed to optimize the cooling The main boundary conditions for the cooling chan- channel geometry. An optimization algorithm is nel design are the assumed heat flux profile, the used to change the height, width and length of the maximal mass flow and the assumed roughness in cooling channels to find the solution that addresses the channels. all three goals: sufficient cooling, low pressure drop, The LUMEN engine is designed to work for load large increase of coolant temperature. points between a combustion chamber pressure be- tween Pcc = 35 bar and Pcc = 80 bar and the mixture ratio (ROF) between 3 and 3.8. 2.1 goals for the design The geometry optimization will be performed for The optimal design features a wall temperature the nominal point, that is: Pcc = 60 bar and below the allowed limit of 900K, an enthalpy in- ROF = 3:4. The boundary conditions for the CFD crease of the coolant to get an outlet temperature of simulation for this load point can be found in Tab. 3. Tout > 400 K, and the lowest pressure drop possible When a solution for this load point is found, the per- (at least dP < 25 bar). The goals are summarized in formance for the other load points will be verified. Tab. 1. The constraints due to manufacturing rea- The heat flux profile is the result of a ROCFLAM III sons are summarized in Tab. 2. simulation [19, 21]. 2 h5 m CH4 parameter unit value h1 h2 h3 h4 L [mm] 247.2 60 h1 [mm] 8.2 h2 [mm] 4.0 50 h3 [mm] 4.0 40 h4 [mm] 1.8 [MW/m²] 30 h5 [mm] 4.1 nchannel [−] 86 20 m_ CH4 [−] 2.35 heat flux 10 0 -350 -300 -250 -200 -150 -100 -50 0 50 100 150 Table 4: Geometry parameter for the final design. 89 mm 60 mm 119 mm L [mm] length 2.4 The numerical setup Figure 1: Positions at which the cooling channel ge- RANS simulations were performed with the com- ometry is optimized. mercial software ANSYS CFX [2]. The SST turbu- lence model was used. The used mesh is adapted parameter unit value to each iteration step so that the cell width and heights remain constant to get comparable results. q_ [MW=m2] Fig. 2 w The the y+-value is <1. More details for the numeri- T [K] 120 ein cal setup can also be found in [15].
Details
-
File Typepdf
-
Upload Time-
-
Content LanguagesEnglish
-
Upload UserAnonymous/Not logged-in
-
File Pages10 Page
-
File Size-