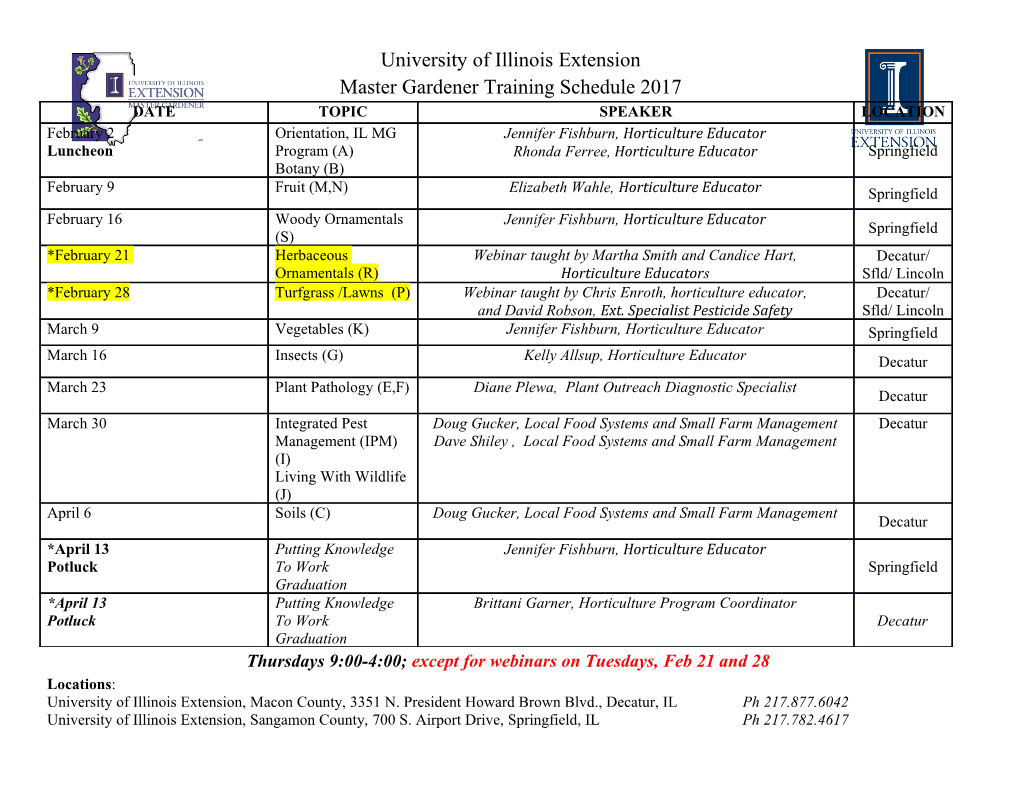
US009 174853B2 (12) United States Patent (10) Patent No.: US 9,174,853 B2 Arkles et al. (45) Date of Patent: Nov. 3, 2015 (54) METHOD FOR PRODUCING HIGH PURITY B01D 2257/304; B01D 2257/406; B01D GERMANE BY A CONTINUOUS OR 53/52; B01D 53/8612; B01D 53/8671; B01D SEM-CONTINUOUS PROCESS 2253/108; B01D 2256/16; B01D 2257/55 (71) Applicant: Gelest Technologies, Inc., Morrisville, USPC .......................................................... 438/685 PA (US) See application file for complete search history. (72) Inventors: Barry C. Arkles, Pipersville, PA (US); (56) References Cited George A. Timberlake, Jr., Gilbertsville, PA (US) U.S. PATENT DOCUMENTS 4,668,502 A 5, 1987 Russotti (73) Assignee: Gelest Technologies, Inc., Morrisville, 7,087,102 B2 8/2006 Withers, Jr. et al. PA (US) (Continued) (*) Notice: Subject to any disclaimer, the term of this patent is extended or adjusted under 35 FOREIGN PATENT DOCUMENTS U.S.C. 154(b) by 0 days. CN 101486444. A T 2009 CN 1023908O8 A 3, 2012 (21) Appl. No.: 14/540,466 WO 2005.005673 A2 1, 2005 (22) Filed: Nov. 13, 2014 OTHER PUBLICATIONS Prior Publication Data Martin et al., “Gas Separation by pressure Swing adsorption' (65) advances in cryogenic engineering, prenum press, NY 1986. US 2015/O158738A1 Jun. 11, 2015 (Continued) Related U.S. Application Data Primary Examiner — Mark A Laurenzi (60) Provisional application No. 61/912,791, filed on Dec. (74) Attorney, Agent, or Firm — Panitch Schwarze Belisario 6, 2013. & Nadel LLP Int. C. (51) ABSTRACT HOIL 2L/214 (2006.01) (57) COIG 7/00 (2006.01) A continuous or semi-continuous process for producing a high purity germane includes (a) preparing a reaction mixture (Continued) containing hydrogen and crude germane and (b) separating (52) U.S. C. the hydrogen from the crude germane by a pressure Swing CPC ............ COIG 17/003 (2013.01); B0ID53/047 adsorption process. The pressure Swing adsorption process (2013.01); B0ID 53/0462 (2013.01); COIB results in a hydrogen-rich product stream and a germane-rich 3/56 (2013.01); COIB 6/06 (2013.01); COIG product stream. The method further includes (c) purifying the 17/00 (2013.01); F25J 3/08 (2013.01); B01D germane-rich product stream by continuous distillation 2253/108 (2013.01); B01D 2256/16 (2013.01); thereof to remove impurities therefrom and to produce a high BOID 2257/55 (2013.01) purity germane containing less than 0.1 Volume percent of (58) Field of Classification Search impurities. CPC ............... B01D 53/46; B01D 2253/10; B01D 2257/00; B01D 2257/20; B01D 2257/204; 13 Claims, 3 Drawing Sheets Refrigerant German to recovery Ret or disposal - A. impurities to Disposal 28 Hydrogen 24 Purge Gas - 20 22 ------------------ --- i regenerable Hydrogen | WacuumCompressor pump with & | AdsorberBalance for Dryer Ho RenovaA. PSA E. 8C y 12 ws s: Crude as Germane-Containing Compressor & g 2 Reaction Mixture refrigeration Digermane s g Drier Cotection Acid Solution 28 BaseSolution 30 Sub-surface diptube High Purity 1. Gerare Aqueous effluent Make Tank 32 US 9,174,853 B2 Page 2 (51) Int. Cl. OTHER PUBLICATIONS BOLD 53/04 (2006.01) Jolly, “The Preparation of the Volatile Hydrides of Groups IV-A and BOLD 53/047 (2006.01) V-A by Means of Aqueous Hydroborate'. Journal of the American F25.3/08 (2006.01) Chemical Society, vol. 83, pp. 335-337 (1961). COIB 3/56 (2006.01) Knaebel, et al., “Pressure Swing Adsorption: Development of an COIB 6/06 (2006.01) Equilibrium Theory for Gas Separations”, Chemical Engineering Science, vol. 40, pp. 2351-2360 (1985). References Cited Sircar et al., “Purification of Hydrogen by Pressure Swing Adsorp (56) tion', Separation Science and Technology, vol. 35, pp. 667-687 U.S. PATENT DOCUMENTS (2000). Int'l Search Report and Written Opinion issued Mar. 6, 2015 in Int’l 2005/019 1854 A1* 9/2005 Withers, Jr. ............. C22B 41.00 Application No. PCT/US2014/066640. 438,685 2008/0299.037 A1 12/2008 Tezock * cited by examiner U.S. Patent Nov. 3, 2015 Sheet 2 of 3 US 9,174,853 B2 U.S. Patent US 9,174,853 B2 JosseuduuOO uunnoe/\ duund US 9,174,853 B2 1. 2 METHOD FOR PRODUCING HGH PURITY BRIEF DESCRIPTION OF THE SEVERAL GERMANEBY A CONTINUOUS OR VIEWS OF THE DRAWINGS SEM-CONTINUOUS PROCESS The following detailed description of preferred embodi CROSS-REFERENCE TO RELATED 5 ments of the present invention will be better understood when APPLICATIONS read in conjunction with the appended drawing. For the pur poses of illustrating the invention, there is shown in the draw This application claims priority to U.S. Provisional Patent ing an embodiment which is presently preferred. It is under Application No. 61/912,791, filed on Dec. 6, 2013, entitled stood, however, that the invention is not limited to the precise “Method for Producing High Purity Germane by a Continu 10 arrangements and instrumentalities shown. In the drawings: FIG. 1 is a schematic flow diagram of the process for ous or Semi-Continuous Process, the entire contents of producing high purity germane in accordance with an which are incorporated by reference herein. embodiment of the present invention; and BACKGROUND OF THE INVENTION FIG. 2A is a schematic flow diagram of the generation and 15 purification steps of a process for producing high purity ger mane in accordance with an embodiment of the present inven This invention involves a method for producing high purity tion, prior to the distillation steps; and germane by a continuous or semi-continuous process. The FIG.2B is a schematic flow diagram of the distillation steps typical preferred commercial method for producing germane of a process for producing high purity germane in accordance is an aqueous borohydride reduction of germanium dioxide, most often using sodium borohydride or potassium borohy with an embodiment of the present invention. dride. Examples of this process may be found in U.S. Pat. No. DETAILED DESCRIPTION OF THE INVENTION 4,668,502 of Russotti; U.S. Pat. No. 7,087,102 of Withers et al.; and U.S. Patent Application Publication No. 2008/ According to the invention, a method is provided for gen O299.037 of TezOck. 25 erating and purifying germane (GeH) by a continuous or Russotti, Withers et al. and Tezock are all directed to the semi-continuous process. yield and purification of germane from germanium dioxide. Referring to FIGS. 1-2B, the method comprises producing In particular, Withers et al. disclose a method for purifying a a germane-containing reaction mixture by reacting one or germane fluid, produced by a cryogenic-trapping technique. more germanium-containing compounds such as, for However, the co-product of the reduction, namely hydrogen 30 example, germanium oxide (also known as germanium diox gas, is not considered or discussed in detail in Russotti. With ide), alkali metal germanates (such as potassium germanate), ers et al. or Tezock. and/or compounds formed in situ from germanium tetrachlo In general, in Such reductions, impure germane leaves the ride, germanium or various germanides, with one or more primary process reactor entrained in a hydrogen gas stream at hydrogen-containing reducing agents in a reactor 10 to pro a volume concentration of approximately 2% to 20%. The 35 vide a reaction mixture. Preferably, the hydrogen-containing presence of the co-product hydrogen gas presents enormous reducing agent is a borohydride. Examples of reducing agents difficulties for high Volume production of germane, particu that may be used include Sodium borohydride, potassium larly if the purification is completed in a batch-wise low borohydride, lithium borohydride. The various components temperature condensation of the germane out of the hydrogen may be mixed together in ratios known in conventional reac stream. An article by W. Jolly published in the Journal of the 40 tion methods. Also, the various components may be added American Chemical Society discusses the formation of directly to the reactor 10 with good turbulent mixing or, hydrogen and removal of the germane from the hydrogen gas alternatively, may be fed through a static mixer (not shown) stream by cryogenic trapping (W. Jolly, JAm. Chem. Soc., V. before entering the reactor 10. 83, p. 335 (1961)). The reaction is preferably conducted in an aqueous While methods for removal of the hydrogen gas, such as 45 medium under conventional temperature and pressure condi membrane separation and absorption, are alternatives which tions. However, it will be understood that the reaction may may potentially allow for continuous purification of the ger instead be conducted in a non-aqueous medium, Such as an mane, such methods have not to date been reduced to practice. organic solvent, or utilizing a combination of aqueous and Accordingly, a method for producing high purity germane on non-aqueous media. Preferably, the method comprises pro a semi-continuous basis without the need for low temperature 50 ducing a germane-containing reaction mixture by borohy process conditions, such as those required for cryogenic trap dride reduction of germanium oxide or its hydrate germanium ping processes, would be desirable. hydroxide in an aqueous solution. However, it will be under stood by those skilled in the art that any known processes for BRIEF SUMMARY OF THE INVENTION producing germane-containing mixtures may be utilized. 55 The reaction mixture primarily contains germane (GeH) One aspect of the present invention is directed to a method and hydrogen (H), as well as carbon dioxide (CO), water for producing high purity germane containing less than 0.1 vapor (H2O), digeonane (GeH) and possibly other trace Volume percent of impurities. The method comprises: (a) gases and impurities. More particularly, in one embodiment, preparing a reaction mixture containing hydrogen and crude the reaction mixture contains 80% or greater, and more pref germane; (b) separating the hydrogen from the crude ger 60 erably 80% to 98% by volume hydrogen gas with the balance mane by a pressure Swing adsorption process, the pressure being germane, carbon dioxide, water vapor, digermane and Swing adsorption process resulting in a hydrogen-rich prod other trace gases and impurities.
Details
-
File Typepdf
-
Upload Time-
-
Content LanguagesEnglish
-
Upload UserAnonymous/Not logged-in
-
File Pages9 Page
-
File Size-