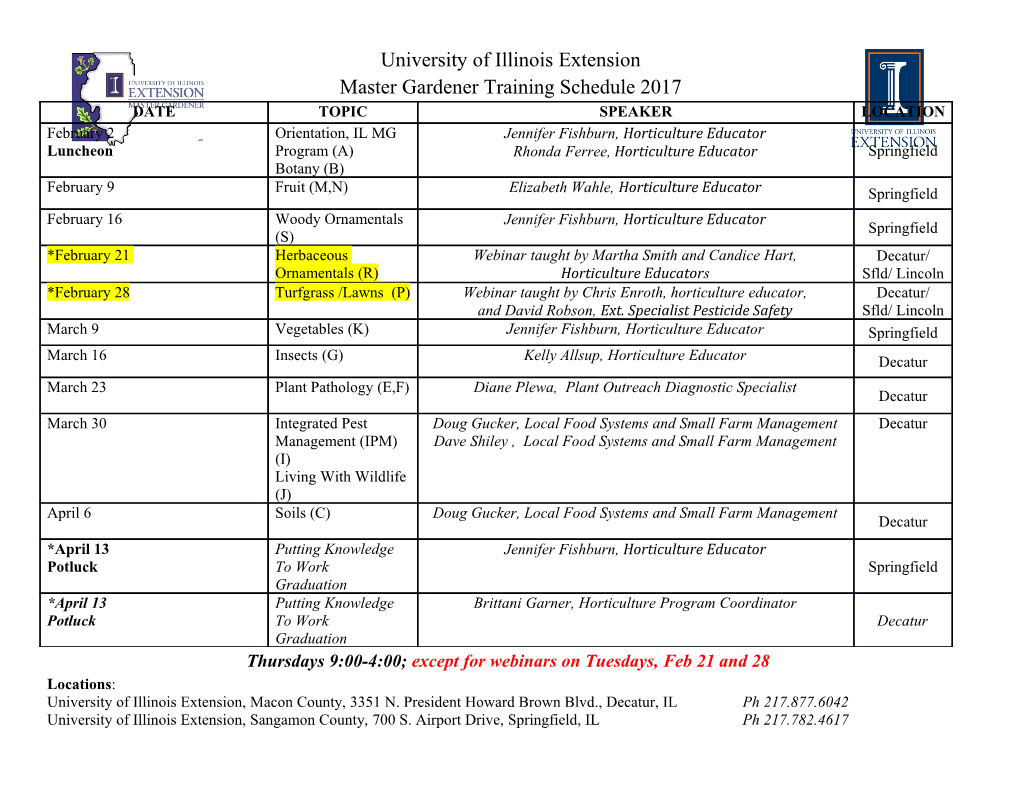
Planar structures with automatically generated bevel joints The MIT Faculty has made this article openly available. Please share how this access benefits you. Your story matters. Citation Zhilong Sua, et al., "Planar structures with automatically generated bevel joints." Computers & Graphics 72 (2018): p. 98-105. doi: 10.1016/j.cag.2018.02.005 ©2018 Author(s) As Published 10.1016/j.cag.2018.02.005 Publisher Elsevier Version Author's final manuscript Citable link https://hdl.handle.net/1721.1/124169 Terms of Use Creative Commons Attribution-NonCommercial-NoDerivs License Detailed Terms http://creativecommons.org/licenses/by-nc-nd/4.0/ ARTICLE IN PRESS JID: CAG [m5G; February 27, 2018;2:49 ] Computers & Graphics xxx (2018) xxx–xxx Contents lists available at ScienceDirect Computers & Graphics journal homepage: www.elsevier.com/locate/cag Technical Section Planar structures with automatically generated bevel joints ∗ ∗∗ Q1 Zhilong Su a, Lujie Chen b, , Xiaoyuan He a, , Fujun Yang a, Lawrence Sass c a Southeast University, Nanjing, 2 Si Pai Lou, Nanjing, China b Singapore University of Technology and Design, 8 Somapah Road, Singapore c Massachusetts Institute of Technology, MA, USA a r t i c l e i n f o a b s t r a c t Article history: A generative method based on computer algorithms is proposed to automatically produce parts of planar Received 31 August 2017 structures ready for fabrication. The parts resemble surface patches of the digital model of a structure. Revised 29 January 2018 Each part is generated with bevel joints on the edges so that part-to-part connection is enabled by fric- Accepted 13 February 2018 tion of the joints. The shape of a bevel joint is determined by the interior angle between two parts, and Available online xxx is modelled by a number of parameters, including the thickness of a planar material in use. The bevel Keywords: joints consist of slanted planes, and in principle when they are assembled, no gap exists on the surface Planar structures of the physical structure. Due to the slanted planes, the joints cannot be fabricated by a laser cutter Bevel joint that can only produce vertical cuts. We experimented the fabrication with a three-axis CNC router and a Digital fabrication 3D printer; both produced accurate and robust parts; however, there is limitation in using a CNC cutter, CNC cutting which is discussed in details. 3D printing ©2018 Elsevier Ltd. All rights reserved. 1 1. Introduction For large-scale prototyping [8] , i.e. practically any dimension 23 that is beyond one meter, planar structures are one of the most 24 2 Creative design is inevitably influenced by the capability of adopted approaches [9] . They have long been used in architecture, 25 3 production. Many years of research has led designers to recognize construction, and ship building. A typical work process starts from 26 4 that physical artefacts, either in the form of low-fidelity prototypes a digital 3D model; create a representation of the model by 2D 27 5 or high-quality products, give valuable feedback on a conceptual planes in Computer-Aided Design (CAD) software; materialize 28 6 idea and are critical to the success of an iterative design pro- the planes by assigning a thickness; generate slots and joints for 29 7 cess [1] . Methods of rapid physical production are therefore connecting the planar parts; fabricate and assemble the parts to 30 8 valuable to designers of various industries. Automobile, marine produce a physical artefact. Although the process involves a lot of 31 9 and air plane designers make mockups to study the aesthetics, manual work such as drafting in CAD software, it offers a designer 32 10 dynamics, and mechanics of their products [2–4] . Architects make great flexibility in materialize his design. Designers also see oppor- 33 11 scaled models to understand the interaction between a building tunities to automate part of the process and come up with creative 34 12 and an environment [5] . From a designer’s point of view, physical solutions. Sass [10,11] proposed a shape grammar to streamline 35 13 prototypes are best to be created with low cost, in a short time, the generation of interlocking planar parts to produce house 36 14 while having good fidelity and strength because they are supposed models. He used computer-numerically controlled (CNC) machines 37 15 to be used for just-in-time evaluation [6] . The two-sided expec- to fabricate the parts. This work demonstrated preliminary idea on 38 16 tation on prototypes has motivated research in rapid prototyping automation of planar structures, while a shape grammar is not a 39 17 across multi-disciplines. 3D printing as a highly automated rapid computer program but rule sets to guide manual drafting. 40 18 prototyping method has been widely used [7] . A printed artefact Researchers in computer graphics started to look into direct 41 19 obtains a solid surface that closely resembles the original digital physical production in 2006 [12] , where direct means that the 42 20 model. However, 3D printing has limitations, such as low speed parts of a physical artefact are directly generated from a digital 43 21 and limited build volume. In areas where these limitations are model with little human intervention in modeling (drafting). This 44 22 unacceptable, other methods are applied instead. approach also relies on CNC machining but its impact is sub- 45 stantial: Computer algorithms can independently extract relevant 46 shape information to produce the drawings of parts, which are 47 later fabricated using CNC machines. As a result, human error is 48 Q2 ∗ Corresponding author . ∗∗ 49 Corresponding author . largely eliminated from modeling and fabrication. Since then, new E-mail address: [email protected] (L. Chen). ideas in automating the production of planar structures have been 50 https://doi.org/10.1016/j.cag.2018.02.005 0097-8493/© 2018 Elsevier Ltd. All rights reserved. Please cite this article as: Z. Su et al., Planar structures with automatically generated bevel joints, Computers & Graphics (2018), https://doi.org/10.1016/j.cag.2018.02.005 ARTICLE IN PRESS JID: CAG [m5G; February 27, 2018;2:49 ] 2 Z. Su et al. / Computers & Graphics xxx (2018) xxx–xxx 51 flourished. They address various questions such as improving slots 52 and joints for complex models [13] , differentiating importance 53 of planar parts [14,15] , chair-design system [16] , parametric de- 54 sign system [17] , unequally spaced slots [18] , non-perpendicular 55 parts [19] , and bendable parts [20] . 56 2. Related work Fig. 1. (a) Finger joints of a watertight structured achieved in [25] . (b) Bevel joints 57 This paper is concerned with a type of planar structures of a planar structure. (c) An exploded view of the bevel joints in (b). 58 that is a watertight representation of a digital model. Methods 59 aforementioned produce openly sliced models that are not suit- 60 able for certain applications; for instance, be used as mold for 61 casting. Watertight planar structures are physical models as a 62 complete volume, as opposed to sets of overlapping slices. There 63 is sparse exploration of this method of model production. Chen 64 et al. [21] developed a multiplanar modeler that subdivided a 65 digital model into several planar surfaces. Interior connectors were 66 used to join the planar parts. Due to the connectors, fabrication 67 of a model requires two separate processes, one for the planar 68 parts and the other for the connectors. Song et al. [22] described a 69 coarse-to-fine prototyping system, where the interior of a model is 70 made of low-fidelity planar structures and the exterior is made of 71 high-fidelity 3D printed parts. The complete model is an assembly 72 of 3D printed parts onto the planar structures. 73 While the above ideas from the computer graphics field have 74 accomplished watertight representation of a model, explorations 75 in architecture have found real-world applications of these struc- Fig. 2. Overview of the production system for planar structures bevel joints. 76 tures. Robeller et al. [23] created interlocking planar structures 77 with dovetail joints. The structures were strong and could be used 78 as pavilion in an architecture scale. Dovetail joints are widely We have made an interesting observation based on the work 115 79 used in conventional woodwork, the intellectual contribution of in [25] : Adding one more constraint to a watertight structure, we 116 80 [23] lies in a computational method to calculate the angle of a would get a planar structure without surface gaps. Fig. 1 shows 117 81 dovetail joint from the geometry of adjacent planar parts. The the difference in finger joints between the former achieved in 118 82 authors also applied robotic machining to fabricate the parts using [25] and a type of the latter. Clearly, the latter is more elegant 119 83 bevel cutting to accurately produce the joints along the edges. This and structurally robust. Note that the dovetail joints in [23] are 120 84 process greatly simplifies the production of self-interlocking planar different from those in Fig. 1 (b), which hold an object by friction, 121 85 structures, in which no additional connectors are needed; all parts just like those in Fig. 1 (a). Dovetail joints require much more 122 86 are held together by an interlocking mechanism and friction. complicated fabrication, assembly, and disassembly processes 123 87 Howe [24] applied watertight structures made of finger joints because they rely more on intricate shape for interlocking than 124 88 on concrete casting. He showed feasibility of casting large-scale friction between joints. 125 89 concrete structures that have curves, and demonstrated that form- This paper extends the algorithms developed in [25] to a new 126 90 work (mold) production can be a potential industry application of production system that generates structures without surface gaps 127 91 watertight structures.
Details
-
File Typepdf
-
Upload Time-
-
Content LanguagesEnglish
-
Upload UserAnonymous/Not logged-in
-
File Pages9 Page
-
File Size-