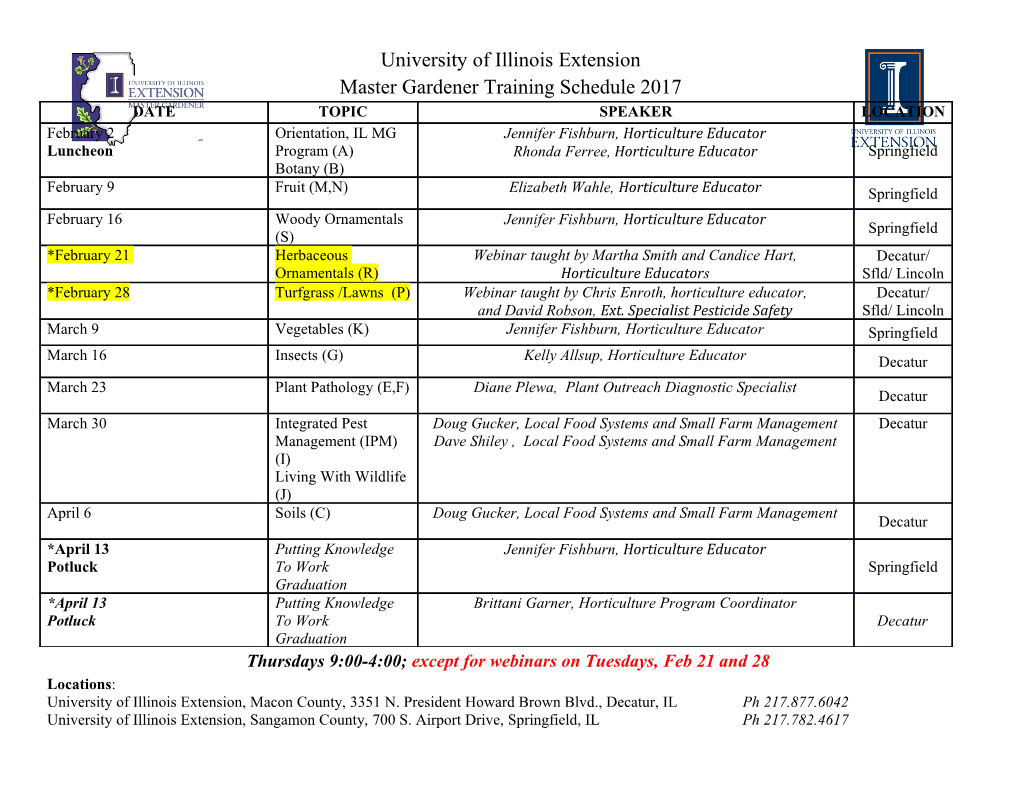
AIAA 2003-4912 Technology Investigation for High Area Ratio Nozzle Concepts G. Hagemann, A. Preuss, F. Grauer, and J. Kretschmer EADS Space Transportation GmbH, Propulsion & Equipments, Munich, Germany M. Frey and R. Ryden Volvo Aero Corporation, Space Propulsion Division, Trollhättan, Sweden R. Stark and D. Zerjeski DLR Lampoldshausen, Institute for Space Propulsion, Hardthausen, Germany 39th AIAA/ASME/SAE/ASEE Joint Propulsion Conference & Exhibit 20 – 23 July 2003 / Huntsville, Alabama For permission to copy or republish, contact the American Institute of Aeronautics and Astronautics 1801 Alexander Bell Drive, Suite 500, Reston, VA 20191 Technology Investigation for High Area Ratio Nozzle Concepts Gerald Hagemann, Axel Preuss, Frank Grauer, and Joachim Kretschmer, EADS Space Transportation GmbH, Munich 81663, Germany Manuel Frey, and Roland Ryden, Volvo Aero Corporation, Trollhättan 46181, Sweden Ralf Stark, and David Zerjeski, DLR Lampoldshausen, Hardthausen 74219, Germany Bell-type nozzle concepts are state -of-the-art technology for expanding gases towards high exhaust velocities. Alternative nozzle concepts have been investigated, although none of them has achieved full-scale flight hardware status. These concepts include altitude adaptive concepts for first stage application, and concepts with reduced length for upper stage application. Both applications have the common requirement that for the thrust chamber design, accurate prediction models for the wall pressure evolution, the wall heat transfer, and the side-load characteristic are of importance. To enhance corresponding design models, the need of well tailored subscale tests at elevated thrust levels has been identified and expressed by the three partners EADS Space Transportation (former Astrium, Space Infrastructure), DLR Lampoldshausen, and Volvo Aero Corporation. Consequently, a joint programme has been formulated, the Calorimeter Nozzle Programme. Within the frame of this Calorimeter Nozzle Programme, three different thrust chamber configurations including actively cooled and film-cooled nozzle extensions are build, tested, and analyzed. Tests are performed with hydrogen-oxygen propellant combination at mixture ratios between 5 and 7.5, and at elevated combustion chamber pressures up to 130 bars. benefits such as in performance or launcher Nomenclature integration compared to the classical bell nozzles. However, each of these concepts comprises also Symbols specific shortcomings which have to be carefully A area analyzed prior to any full-scale realization. e area ratio o/f mixture ratio expansion- p pressure deflection x, y, z coordinates thrust chamber extendible nozzle plug nozzle Subscripts (RL-10, Vinci) (“Aerospike”) a ambient dual-bell c feeding chamber nozzle e exit classical bell nozzle extendible nozzle (Vulcain, SSME, LE-7) Introduction Fig. 1: Rocket nozzle concepts for first and The key demand on future space transportation upper stage application. systems is the continuous reduction of earth-to- Figure 1 illustrates existing and flight-proven orbit launch costs and increase in launcher concepts vs. the above referred advanced nozzle - or reliability and operational efficiency. Meeting these thrust chamber concepts. The application for either demands strongly depend on new engines that first or upper stage integration imposes specific deliver high performance with low system demands.2 For first stage application, stable and complexity. Depending on the engine integration in controlled operation on ground without the first or upper stage of a launch vehicle, high uncontrolled flow separation, and high vacuum thrust levels and / or high vacuum performance are performance are key requirements. Among these required. For both applications, practically all of concepts for first stage application there are three today’s rocket engines use classical bell-type altitude adaptive concepts: nozzle extensions to expand the exhaust gases into the ambience. - The dual-bell nozzle concept, with single step altitude adaptation; Different advanced nozzle concepts have been frequently discussed in the literature.1, 2 Based on - The extendible nozzle concept, with single experimental and analytical analyses it could be step altitude adaptation, and shown that all of these concepts own certain 1 - The clustered plug nozzle concept, with are of importance. Especially with regard to future continuous altitude adaptation up to its advanced nozzle concepts with actively cooled and/ geometric area ratio. or film-cooled nozzle extensions (which may For upper stage application, any nozzle concept additionally foresee devices for active or passive will feature instant full flowing during ignition into flow separation control) the further understanding vacuum. Therefore, flow separation may only of physical processes involved near the separation impose a constraint in case of a firing during the line is of importance. very first phase of stage separation. This, however, Despite the different cold gas experiments is not the case for civil launchers such as Ariane 4 carried out within the framework of the European and 5. Key requirement here is again a high Flow Separation Control Device Programme, vacuum performance. The only practical limit to FSCD, until 2002,3 hot gas tests are needed for the reach highest performance values with long nozzle characterization of the heat transfer, flow separation extensions is the available storage compartment, and side-load behavior in actively and film-cooled and thus a geometric constraint. For classical bell- nozzle extensions.* Furthermore, the experimental type nozzles, the above referred extendible nozzle data base to be established will be needed for concept is therefore here already realized, e.g. with enhancement of engineering models and also for the American RL-10 and the future European Vinci CFD validation. LOX/LH2-engines. Fundamental difference to first This need has been identified and expressed by stage application is that the deployment occurs the three partners Astrium, DLR Lampoldshausen, prior to engine ignition. and Volvo Aero Corporation. Consequently, a joint programme has been formulated, the “Calorimeter L L Nozzle Programme”, see Ref. 4 for a detailed L L description of the programme set-up. Within the framework of this calorimeter nozzle programme, expansion-deflection three different thrust chamber configurations, conical nozzle bell-shaped nozzle truncated plug nozzle nozzle TC length = 100 % TC length » 80 % TC length » 50 % TC length » 50 % including actively cooled and film-cooled nozzle diameter = 100 % diameter = 100 % diameter = 104 % diameter = 102 % extensions, are built, tested, and analyzed. Tests are Fig. 2: Comparison of different thrust chamber performed with a hydrogen-oxy gen propellant concepts featuring equal vacuum performance. combination at mixture ratios between 5 and 7, and For upper stage application, advanced concepts at combustion chamber pressures up to 130 bars. allowing for a significant reduction in geometric Key objectives of this experimental research size without any moving parts being in closer programme are the following: investigation are the: - Characterization of heat transfer, flow - Expansion-deflection thrust chamber separation, and side load behavior in concept, and also actively and film-cooled nozzles. - The plug nozzle concept. - Data base for development / validation of The reduced geometric size of above referred CFD tools and engineering models. thrust chamber concepts is emphasized in Fig.2, - Demonstration of mechanical integrity of sketched for equal vacuum performance values. All nozzle design. above referred nozzle concepts are currently The status of the calorimeter nozzle programme explored by space industry and institutes in Europe, (abbreviated as “Calo” in the following) is see e.g. Ref.1-3. The investigations concentrate on described in this paper. It contributes to the the European FSCD programme. - aerodynamic design, including wall pressure evolution at given back pressures Calo Programme Overview and in vacuum, - thermal analysis for the cooling layout, The Calo programme consists of three - mechanical design studies, campaigns with different nozzle hardwares. All - manufacturing studies, and three campaigns use a water-cooled copper - proof-of-concept by subscale tests, either combustion chamber manufactured by EADS ST. with cold- and hot firing tests. To this combustion chamber, which also includes For the design of a new rocket engine thrust the nozzle throat and the divergent portion up to an chamber, accurate prediction models for a) the wall pressure evolution, including the * The FSCD Programme investigates flow effect of flow separation at back pressures separation and side-load origins in advanced high by the ambiance, area ratio nozzles by means of experiments and b) the wall heat transfer for attached and numerical analyses, with the following partners separated flow condition, and involved: European industry (EADS Space Transportation, Snecma, Volvo Aero) and institutes c) the side-load characteristic, (Cnes, ESA ESTEC, DLR, Onera, LEA Poitiers). 2 area ratio of e = 4.1, the base nozzle (up to e = 11.1) Calo P8 Test Campaign and the nozzle extension is attached as follows: Hardware Description - Campaign A: Actively cooled nozzle For the contour design, a truncated ideal profile without film injection; EADS ST-built was selected; see also Ref. 4 for further details: water-cooled copper base nozzle and nozzle extension, see Fig.
Details
-
File Typepdf
-
Upload Time-
-
Content LanguagesEnglish
-
Upload UserAnonymous/Not logged-in
-
File Pages8 Page
-
File Size-