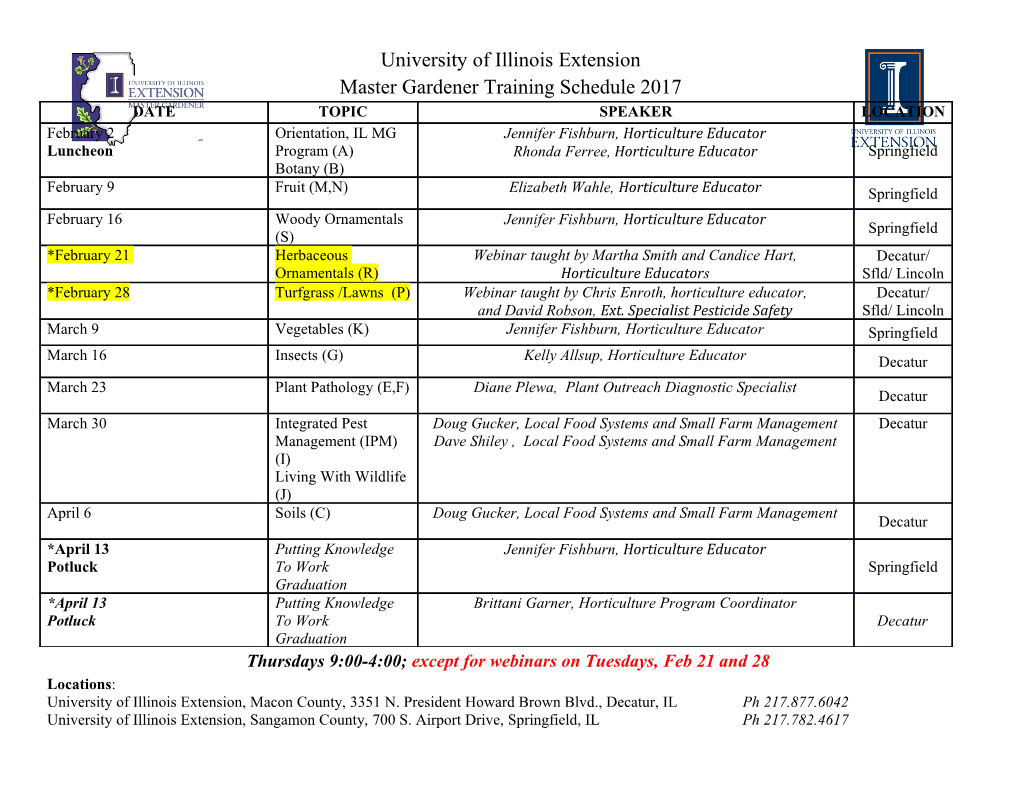
Lin et al. Biotechnol Biofuels (2015) 8:168 DOI 10.1186/s13068-015-0352-6 RESEARCH Open Access Bio‑butanol production from glycerol with Clostridium pasteurianum CH4: the effects of butyrate addition and in situ butanol removal via membrane distillation De‑Shun Lin1, Hong‑Wei Yen2, Wei‑Chen Kao1, Chieh‑Lun Cheng1, Wen‑Ming Chen3, Chieh‑Chen Huang4 and Jo‑Shu Chang1,4,5* Abstract Background: Clostridium pasteurianum CH4 was used to produce butanol from glycerol. The performance of butanol fermentation was improved by adding butyrate as the precursor to trigger the metabolic pathway toward butanol production, and by combining this with in situ butanol removal via vacuum membrane distillation (VMD) to avoid the product inhibition arising from a high butanol concentration. 1 Results: Adding 6 g L− butyrate as precursor led to an increase in the butanol yield from 0.24 to 0.34 mol butanol 1 (mol glycerol)− . Combining VMD and butyrate addition strategies could further enhance the maximum effective 1 1 butanol concentration to 29.8 g L− , while the yield was also improved to 0.39 mol butanol (mol glycerol)− . The butanol concentration in the permeate of VMD was nearly five times higher than that in the feeding solution. Conclusions: The proposed butyrate addition and VMD in situ butanol removal strategies are very effective in enhancing both butanol titer and butanol yield. This would significantly enhance the economic feasibility of fermen‑ tative production of butanol. The VMD-based technology not only alleviates the inhibitory effect of butanol, but also markedly increases butanol concentration in the permeate after condensation, thereby making downstream process‑ ing easier and more cost-effective. Keywords: Bio-butanol, Clostridium pasteurianum, Vacuum membrane distillation (VMD), Butyrate addition, Glycerol Background Butanol is not only a key chemical in many industrial Glycerol is the principal byproduct of the biodiesel pro- processes, but also an alternative fuel. It has several duction process [1, 2], with production of ten gallons of advantages over ethanol as a biofuel, in terms of energy biodiesel resulting in one gallon of glycerol byproducts. content, volatility, hygroscopicity and the ease with Since the biodiesel industry has been expanding rapidly which it mixes with gasoline in any proportion. Clostridia in recent years, a large amount of glycerol has been pro- fermentation is known for its ability to produce butanol duced, leading to a significant fall in its market price. The [3–5]. Acetone–butanol–ethanol (ABE) fermentation of reutilization of glycerol by converting it into higher value sugars by Clostridium acetobutylicum is a well-known products is thus of great interest. One of the options is bio-butanol producing process and has been widely used using glycerol as a carbon source to produce butanol in industry since the early 20th century. There are also through fermentation processes. several studies in the literature reporting reutilization of glycerol, a waste product of biodiesel manufacturing pro- *Correspondence: [email protected] cess, as the carbon source to produce butanol with the 1 Department of Chemical Engineering, National Cheng Kung University, Clostridium pasteurianum strain [6–9]. Tainan, Taiwan Full list of author information is available at the end of the article © 2015 Lin et al. This article is distributed under the terms of the Creative Commons Attribution 4.0 International License (http:// creativecommons.org/licenses/by/4.0/), which permits unrestricted use, distribution, and reproduction in any medium, provided you give appropriate credit to the original author(s) and the source, provide a link to the Creative Commons license, and indicate if changes were made. The Creative Commons Public Domain Dedication waiver (http://creativecommons.org/publicdomain/ zero/1.0/) applies to the data made available in this article, unless otherwise stated. Lin et al. Biotechnol Biofuels (2015) 8:168 Page 2 of 12 Most butanol fermentation processes are inhibited Results and discussion by the accumulation of butanol in the fermentation Butanol separation performance with a vacuum broth, commonly known as “end-product inhibition” membrane distillation process [10, 11]. The final butanol concentration in the fer- To identify the selectivity of VMD on the separation of mentation broth is thus limited to a threshold (inhibi- the main products of butanol fermentation (i.e., butanol tory) level. The inhibitory concentration of butanol is and ethanol, denoted as BE), the rate of BE removal about 17 g L−1 for C. pasteurianum and 11–12 g L−1 under the fermentation conditions was determined using for C. acetobutylicum [6, 12]. This is the primary fac- prepared model solutions of B at a concentrations of tor impeding commercial acceptance of butanol pro- 15.0 g L−1 and E at a concentration of 3.0 g L−1, respec- duction from renewable feedstock. Several separation tively. The VMD system was used at 37 °C for the experi- techniques have thus been integrated with butanol fer- ment. As shown in Fig. 1, with the VMD operating for mentation processes for in situ solvent removal during 27 h the butanol concentration in the model solution batch and continuous butanol fermentation, and these decreased from 15 to 1.51 g L−1, while the ethanol con- include distillation, liquid–liquid extraction, adsorp- centration decreased from 3.0 to 0.47 (Fig. 1a). The effect tion by molecular sieves, and membrane separation of the feeding butanol and ethanol concentration on the [13–15]. To make butanol competitive with fossil fuels, rate of removal of butanol and ethanol was also investi- the production costs must be reduced. Selective and gated. Figure 1b shows that increasing the concentration continuous butanol removal from fermentation broth of butanol in the feeding solution means increasing the with a separation process can enhance the conversion mole fraction of butanol in the solution (or increasing the rates, and consequently the economic feasibility of partial pressure of butanol), thereby leading to a higher the butanol fermentation process [14]. The advantages butanol removal rate. The butanol flux with the VMD of membrane separation methods, such as membrane was 72 g h−1 m−2 at an initial butanol concentration of distillation and pervaporation, include low energy 15 g L−1. The effect of varying the ethanol concentration demand, no removal of nutrients and substrates, no on the flux of ethanol removal was also investigated. As need for an entrainer, and a low possibility of contami- shown in Fig. 1c, the ethanol flux increased along with the nation [16–18]. concentration of ethanol. The ethanol flux with the VMD This study was undertaken to examine the efficiency was 12.7 g h−1 m−2 when the ethanol feeding concentra- of in situ butanol removal using vacuum membrane tion was 3.0 g L−1. Using VMD, the butanol concentra- distillation (VMD) during the cultivation of Clostrid- tion in the permeate was up to five times higher than ium pasteurianum CH4, using glycerol as the carbon that in the feeding solution (Fig. 1d). The high concentra- source. VMD is a promising technology for treating tion of butanol obtained in the permeate would facilitate the aqueous solutions. The applications of VMD can the butanol recovery process. Overall, the results of the be classified into three main fields: the single compo- model solution clearly indicate that using the VMD sys- nent transport process, the binary component trans- tem could efficiently remove butanol from the fermenter port process and the multi-components transport broth, thus greatly reducing the product inhibition that process, such as the desalination process and extrac- occurred in the ABE fermentation process. tion of organic and dissolved gas from water. VMD has the potential of competing with other well-established Effects of butyrate addition on batch butanol fermentation separation technologies in terms of economic and Anaerobic fermentation has the potential to produce safety considerations [19]. The relatively high energy sustainable liquid and gaseous energy products from demand required for the distillation is the major con- renewable feedstock. In this study, butanol and hydro- cern in the VMD operation. A possible solution to gen were produced from glycerol with C. pasteurianum reduce the total energy consumption is to combine CH4 isolated from the effluent of a2 H -producing biore- VMD operation with a heat recovery facility or to actor. In our preliminary work, response surface meth- use renewable energy (such as solar energy) as part of odology (RSM) was adopted to investigate the optimum energy supply. fermentation conditions, including the parameters such In addition, the effect of adding butyrate at the begin- as culture pH, glycerol concentration and the added ning of fermentation (acting as a precursor in the butanol concentration of butyric acid. RSM is a useful tool to metabolism) on butanol production was also evaluated optimize a desired response when many factors and [20]. Finally, the combination of an in situ VMD module interactions are involved with the main advantage of with the addition of butyrate was used to further enhance reducing the number of experiments needed to evaluate butanol production efficiency and obtain a higher glyc- multiple parameters and their interactions. Therefore, erol utilization yield. this tool is suitable for improving fermentation systems Lin et al. Biotechnol Biofuels (2015) 8:168 Page 3 of 12 a b 80 Butanol 60 ) 2 40 Flux (g/h/m 20 0 246810121416 Butanol concentration (g/L) c d 80 ) Butanol 70 60 50 40 30 20 Permeate concentration (g/L 10 246810 12 14 16 Butanol concentration in the feed (g/L) Fig. 1 Removal of butanol and ethanol using the model BE solution. a The residual butanol and ethanol concentrations in the model BE solutions, b flux of butanol at various butanol concentrations, c flux of ethanol at various ethanol concentrations, and d performance of concentrated butanol concentration in the filtrate of vacuum membrane distillation (VMD).
Details
-
File Typepdf
-
Upload Time-
-
Content LanguagesEnglish
-
Upload UserAnonymous/Not logged-in
-
File Pages12 Page
-
File Size-