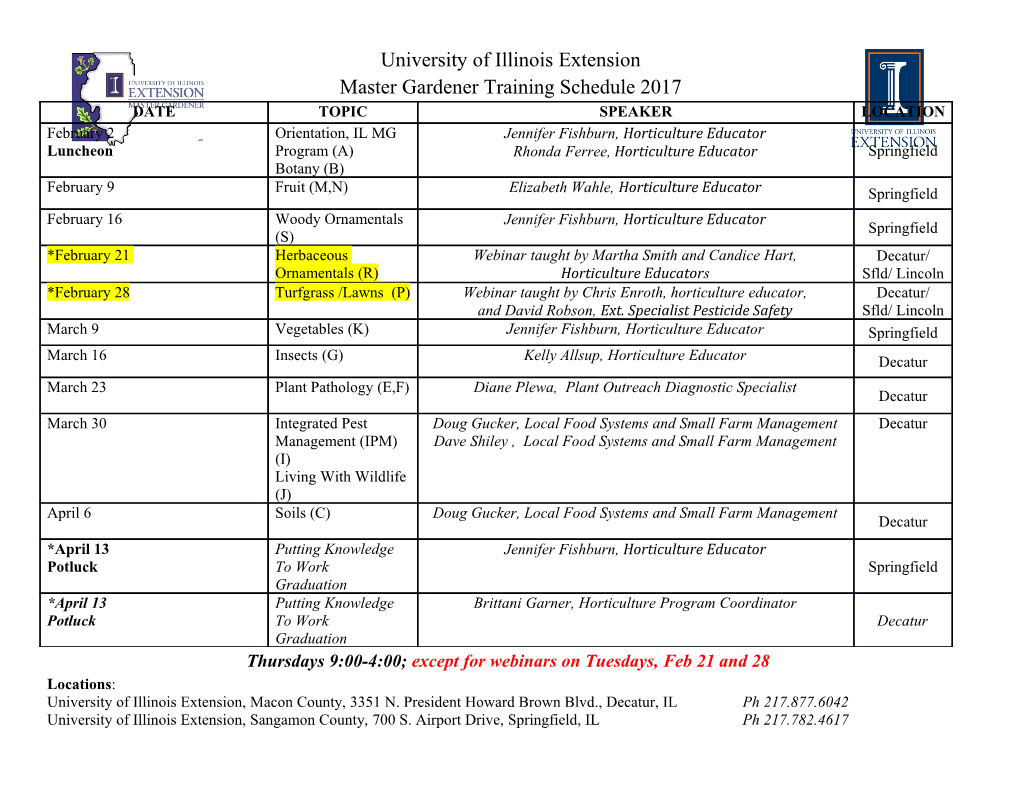
ANSI/AWS C5.4-93 An American National Standard Recommended Practices for Stud Welding Keywords — arc stud welding, discharge, ferrule, ANSI/AWS C5.4-93 stud welding, troubleshooting An American National Standard Approved by American National Standards Institute June 28,1993 Recommended Practices for Stud Welding Superseding AWS C5.4-84 Prepared by AWS Committee on Arc Welding and Cutting Under the Direction of AWS Technical Activities Committee Approved by AWS Board of Directors Abstract These recommended practices for stud welding, prepared by the Subcommittee on Stud Welding of the AWS Committee on Arc Welding and Cutting, are intended to serve as a basic guide for those interested in attaching fasteners by arc and capacitor discharge stud welding. The variations of the process, stud design, equipment, welding procedures, quality control, and safety precautions are discussed. The information presented will guide the designer and the shop in the utilization of studs in many fields including automotive manufacture, boiler and building construction, farm and industrial equipment, railroads and shipbuilding, aircraft and aerospace, metal furniture, and other metal working industries. American Welding Society 550 N.W. LeJeune Road, P.O. Box 351040, Miami, Florida 33135 Table of Contents Page No. Personnel iii Foreword iv List of Tables vii List of Figures viii 1. Process Description 1 1.1 Arc Stud Welding 1 1.2 Capacitor Discharge Stud Welding 3 2. Selection of Method 4 2.1 Fastener Size 5 2.2 Base Metal Thickness 5 2.3 Base Metal Composition 5 2.4 Capacitor Discharge (CD) Method 5 3. Designing for Stud Welding 6 3.1 Base Metal 6 3.2 Stud Design Ratio 7 4. Considerations for Stud Selection 7 4.1 Arc Stud Welding 7 4.2 Capacitor Discharge Studs 11 4.3 Stud Tensile and Torque Strengths 12 5. Equipment for Stud Welding 12 5.1 Arc Stud Welding Equipment 12 5.2 Capacitor Discharge Stud Welding Equipment 17 5.3 Automatic Feed Systems 17 6. Stud Welding Low Carbon and Austenitic Stainless Steels 17 6.1 Base Metal Preparation 17 6.2 Welding Requirements 18 6.3 Welding Technique for Steels 18 7. Stud Welding Aluminum Alloys 20 7.1 Base Metal Preparation 20 7.2 Shielding Gas 20 7.3 Welding Requirements 20 7.4 Welding Technique for Aluminum 20 8. Stud Locating Techniques 23 8.1 Locating with Templates 23 8.2 Locating with Spacers 23 8.3 Fixed Guns 24 8.4 Methods of Ensuring Perpendicularity 24 8.5 Special Accessories 28 9. Quality Control and Inspection 28 9.1 Steel Studs 28 9.2 Aluminum Studs 30 Page No. 10. Weld Troubleshooting 31 10.1 Cold Welds 31 10.2 Hot Welds 31 10.3 Stud Hang-Up 31 11. Safety Precautions 32 11.1 General 32 11.2 Electrical 32 11.3 Fire Protection , /. 32 11.4 Vision Protection 32 11.5 Hearing Protection 32 11.6 Protective Clothing 32 11.7 Ventilation 33 11.8 Other 33 11.9 Maintenance 33 11.10 References 33 Annex—Commonly Used Metric Conversions 35 Document List (Inside Back Cover) VI List of Tables Table Page No. 1 Stud Welding Method Selection Chart 5 2 Typical Combinations of Base and Stud Metals for Stud Welding 6 3 Recommended Minimum Base Metal Thickness of Steel and Aluminum for Arc Stud Welding 8 4 Typical Length Reductions of Studs in Arc Stud Welding 9 5 Weld Flash Clearance for Arc Welded Full Base Studs 12 6 Standard Arc Welding Studs — Tensile/Torque Strengths 14 7 Approximate Tensile and Torque Strengths of Capacitor Discharge Welded Studs 15 8 Typical Stud Welding Conditions for Joining Low Carbon and Stainless Steel Studs to Similar Base Metals 19 9 Comparable Rectangular and Round Studs 21 10 Typical Welding Conditions for Arc Stud Welding of Aluminum Alloys 23 11 Minimum Required Torque Valves and Tension Loads for Arc Stud Welding 31 vn List of Figures Figure Page No. 1A Equipment Setup for Arc Stud Welding of Steel 2 IB Power-Control Type Power Source Setup for Arc Stud Welding of Steel 2 2 Steps in Arc Stud Welding 3 3 Steps in Contact Capacitor Discharge Stud Welding 4 4 Steps in Gap Capacitor Discharge Stud Welding 4 5 Steps in Drawn-Arc Capacitor Discharge Stud Welding 4 6 Commonly Used Studs and Fastening Devices for Arc Stud Welding 8 7 Typical Stud Welds with Shrink Fissures in the Upper Portion of the Weld Flash 10 8 Stud Flash May be Accommodated by Use of Oversized Clearance Holes, Use of Gasket Material, and Use of a Dog or Hold-Down Clip 12 9 Commonly Used Studs for Capacitor Discharge Stud Welding 13 10 Oscillograph Traces of Current and Voltages in Arc Stud Welding 15 11 Arc Stud Welding Capacity for DC Power Sources 16 12 Effect of Cable Size and Length on Available Welding Current from a 2000A Power Source 17 13 Portable Arc Stud Welding Equipment 18 14 Recommended Orientation for Welding Rectangular Studs to a Vertical Surface 19 15 Satisfactory and Unsatisfactory Arc Stud Welds 20 16 Arc Stud Weld with Proper Flash Indicative of a Good Weld 21 17 Examples of Satisfactory and Unsatisfactory Capacitor Discharge Stud Welds 22 18 Equipment Setup for Arc Stud Welding of Aluminum 22 19 Simple Template Used to Locate Studs Within ±1/32 in. (0.8 mm) 24 20 Simple Template for Capacitor Discharge Welds 24 21 Template with Hardened and Ground Bushing and Welding Gun Adaptor 24 22 Locating with Spacer 25 23 Locating from Adjacent Studs 25 24 Locating from Nearby Surface and Previous Stud 25 25 Mounting Gun in a Fixed Position 25 26 Bipod Foot Plate Assembly for 1/2 in. (12.7 mm) Diameter and Smaller Studs 25 27 Bipod Foot for 1/2 in. (12.7 mm) Diameter and Larger Shear Connector Studs 25 28 Bipods for Unusual Surface Contours 26 29 Typical Ferrule Tube Extension Application 27 30 Typical Offset Assembly 27 31 Ferrule Foot Plate 27 32 Typical Extension Assembly 28 33 Stud Hang-Up 28 34 Cold Weld 29 35 Hot Weld 29 36 Bend Test for Welded Studs to Determine Acceptable Welding Procedures 30 37 Method of Applying a Tensile Load to a Welded Stud Using Torque — a Bolt Can Be Used for an Internal Thread 30 vui Recommended Practices for Stud Welding 1. Process Description source of dc welding current. Typical arc stud welding equipment connections are shown in Figures 1A and IB. Stud welding is a general term for joining a metal stud The mechanics of the process are illustrated in Figure 2. or similar part to a workpiece.1 Welding can be done by a The stud is loaded into the chuck, the ferrule (also known number of welding processes including arc, resistance, as an arc shield) is placed in position over the end of the friction, and percussion. The arc stud welding process stud, and the gun is properly positioned for welding, (SW), including capacitor discharge methods, will be Figure 2(A). The trigger is then depressed, starting the covered in this document. automatic welding cycle. In arc stud welding, the base (end) of the stud is joined A solenoid coil within the body of the gun is energized. to the other work part by heating them with an arc drawn This lifts the stud off the work and, at the same time, between the two. When the surfaces to be joined are creates an arc, Figure 2(B). The end of the stud and part properly heated, they are brought together under pressure. of the workpiece are melted by the arc. When the preset Stud welding guns are used to hold the studs and move arc period is completed, the welding current is auto- them in proper sequence during welding. There are two matically shut off and the solenoid de-energized by the basic power supplies used to create the arc for welding control unit. The mainspring of the gun plunges the stud studs. One type uses dc power sources similar to those used into the molten pool on the work to complete the weld, for shielded metal arc welding. The other type uses a Figure 2(C). The gun is then lifted from the stud and the capacitor storage bank to supply the arc power. ferrule is broken off, Figure 2(D). The arc stud welding processes using these power The time required to complete a weld varies with the sources are commonly known as arc stud welding and cross-sectional area of the stud. For example, weld time capacitor discharge stud welding respectively. typically would be about 0.13 seconds for a 10 gage 1.1 Arc Stud Welding. The arc stud welding process (0.134 in. [2.6 mm]) stud, and 0.92 seconds for a 7/8 in. involves the same basic principles as any other arc weld- (22 mm) diameter stud. Application rates vary with the ing process. Application of the process consists of two size of the stud and other factors such as working condi- steps: tions. An average rate is approximately six studs per (1) Welding heat is developed with an arc between the minute, although a rate of fifteen studs per minute is stud and the plate (work). common in many applications. (2) The two pieces are brought into intimate contact The equipment involved in stud welding compares with when the proper temperature is reached. that of manual shielded metal arc welding with regard to The equipment consists of the stud gun, a control unit portability and ease of operation. The initial cost of such (timing device), studs and ferrules, and an available equipment varies with the size of the studs to be welded.
Details
-
File Typepdf
-
Upload Time-
-
Content LanguagesEnglish
-
Upload UserAnonymous/Not logged-in
-
File Pages7 Page
-
File Size-