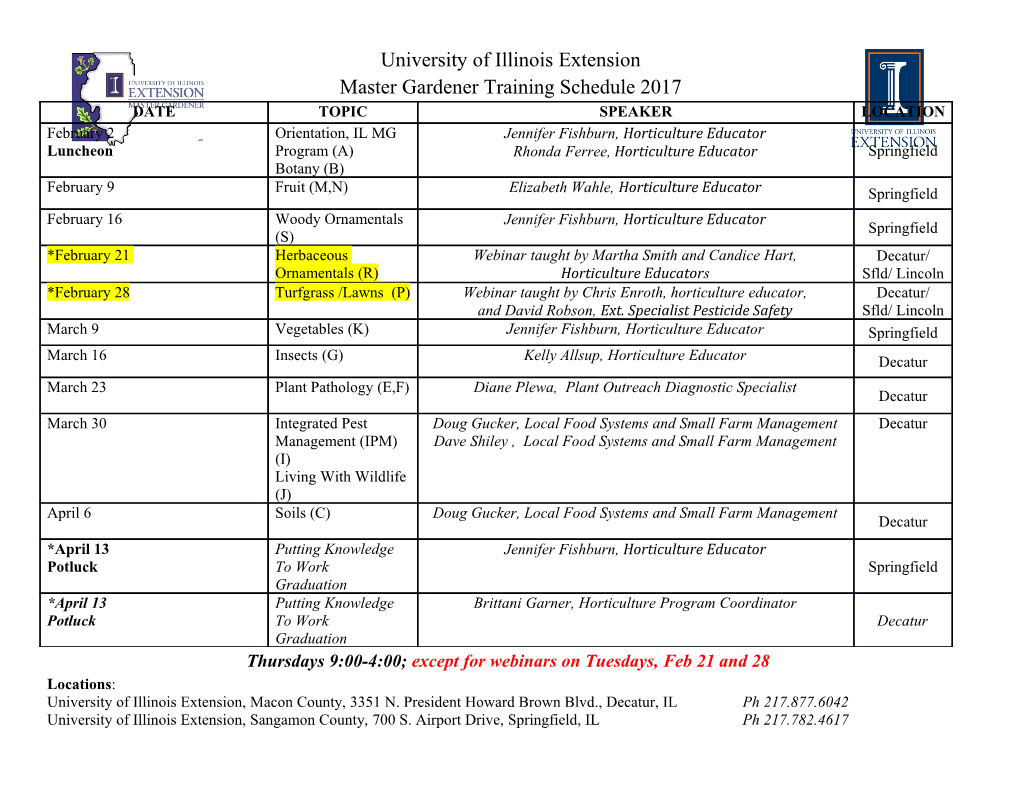
cs & Aero ti sp au a n c o e r E e Hadjez and Necib, J Aeronaut Aerospace Eng 2015, 4:1 n A g f i o n Journal of Aeronautics & Aerospace l e DOI: 10.4172/2168-9792.1000138 a e r n i r n u g o J Engineering ISSN: 2168-9792 Research Article Open Access Stress Analysis of an Aircraft Fuselage with and without Portholes using CAD/CAE Process Fayssal Hadjez* and Brahim Necib University of Constantine, Faculty of Science and Technology, Department of Mechanical Engineering, Algeria Abstract The airline industry has been marked by numerous incidents. One of the first, who accompanied the start of operation of the first airliners with jet engines, was directly related to the portholes. Indeed, the banal form of the windows was the source of stress concentrations, which combined with the appearance of micro cracks, caused the explosion in flight of the unit. Since that time, all aircraft openings receive special attention in order to control and reduce their impact on the aircraft structure. In this paper we focus on the representation and quantification of stress concentrations at the windows of a regional jet flying at 40000 feet. To do this, we use a numerical method, similar to what is done at major aircraft manufacturers. The Patran/Nastran software will be used the finite element software to complete our goals. Keywords: Aircraft; Bay; Modeling; Portholes; Fuselage; gradually. It is then necessary to pressurize the cabin to the survival Pressurization; Loads and passenger comfort. However this pressurization is not beneficial to the structure as it involves additional structural loads. The first airliner Introduction to experience the consequences of these additional expenses is the There are some methods to realize the appearance of additional Dehavilland Comet 1. This aircraft was the first commercial aircraft to expenses at the window. The calculation by finite element is one of the fly with jet engines, allowing pressurization of the unit. However, the main methods used [1], particularly by aircraft manufacturers in the first version of this unit possessed rectangular windows, which were the interests of economy, speed and reliability [2]. This case will have to cause of many accidents. Indeed, the banal form of the windows was obtain internal loads and levels constraints from well-defined external the stress concentration source combined with the appearance of micro loads [3-6]. To do this, Figure 1 shows the process of generating cracks caused the explosion in flight of the unit. internal loads. Thus, the action plan is shown in the following figure. The windows, like other openings in an aircraft when receive To do this, we will use the calculation by finite element software special attention. Among the openings, gates, baggage doors, cut-out Patran/Nastran, which is considered standard in the aerospace industry for kerosene tanks, or openings for antennas, etc., are all sensitive parts and is used in all major aerospace companies [7]. The launch into the on aircraft. heart of this paper will be done after an upgrade on the operation of In this project we focus on the representation and quantification of this software. Geometric modeling is the most important step in the stress concentrations at the windows of the aircraft flying at 40,000 feet process of degeneration of internal forces, to the extent that it serves as support for the creation of the finite element mesh [8]. Thus, our body is composed of frames, stiffeners, coating and finally the floor. The stiffeners support larger primary times, resume compression- tension efforts, and are guarantor of the overall stiffness. Frames give the external shape of the fuselage and support, in large part, the circumferential stress upon pressurization. The coating shows a part of shear efforts then distributes to the stiffeners, which in turn transfer them to the frames. The floor, meanwhile, adds to the rigidity on the transverse and longitudinal planes [9-12]. Table 1 below summarizes all the geometric data used for modeling. Description of the Problem Figure 1: Problem solving process. The issue is part of a structural analysis context. Indeed, aircraft are subjected to various loads and load cases during their flight cycles. *Corresponding author: Fayssal Hadjez, Professor, University of Constantine, Then there exists in each flight phase, one, or even several cases of Faculty of Science and Technology, Department of Mechanical Engineering, loading. It is then necessary to situate our study, Phase flight on which Alegeria, Tel: +213699195188; E-mail: [email protected] you will base our analysis. In our case, we focus on the “cruise” phase Received April 08, 2015; Accepted April 23, 2015; Published May 10, 2015 of a commercial flight. During this phase of flight several loading cases may exist depending on the portion to be analyzed on the aircraft. Citation: Hadjez F, Necib B (2015) Stress Analysis of an Aircraft Fuselage with and without Portholes using CAD/CAE Process. J Aeronaut Aerospace Eng 4: 138. In our case, we will analyze the fuselage. A major case of loading in doi:10.4172/2168-9792.1000138 the fuselage pressurization. This usually occurs in the cabin given its Copyright: © 2015 Hadjez F, et al. This is an open-access article distributed under importance to the survival of the passengers, at high altitude. Indeed, the terms of the Creative Commons Attribution License, which permits unrestricted taking the altitude the air is thinner and lower atmospheric pressure use, distribution, and reproduction in any medium, provided the original author and source are credited. J Aeronaut Aerospace Eng ISSN: 2168-9792 JAAE, an open access journal Volume 4 • Issue 1 • 1000138 Citation: Hadjez F, Necib B (2015) Stress Analysis of an Aircraft Fuselage with and without Portholes using CAD/CAE Process. J Aeronaut Aerospace Eng 4: 138. doi:10.4172/2168-9792.1000138 Page 2 of 8 above sea level. It should be noted that during the initial presentation the fuselage and Al 7475-T7351 for those of the lower crown (0.1676 of the project, the subject referred to “openings” in their globalities. in2 for the area). Regarding the portholes thereof are in fact methyl Given the impossibility of treating all types of possible openings for polymethanecrylate (PMMA or Perspex with 0.02” thick). this project, I chose to restrict and deepen my study of the case of the The fuselage will be subject to pressurization loads firstly, then portholes. We will analyze first place pressurization and now and then twisting the fuselage. torque secondly. We are part of a cruise context to 40,000 feet, and we assume the cabin altitude of 6,000 feet. Thus, a closed cylinder The objective is to achieve the most important two stages namely pressurization in induces the appearance of a circumferential stress obtaining a finite element model of integrity, and the calculation of (hoop stress σH) and longitudinal (σL) as shown in Figure 4. internal forces as shown in the examples in the Figures 2 and 3. To represent the loading on the finite element model, we have to Methodology Employee manually apply the longitudinal stress, through MPC, because our body is not closed. This σL stress is 3624 psi and strength associated As stated previously, the modeling by finite element based on the 65578,359 lbs. An internal pressurization 9.06 psi is then applied to all geometry, to be defined. Due to the CQUAD4 surfaces elements are the plates of the covering. The results speak for themselves. Regarding obtained and through the curves, CROD elements. The frames are the stiffeners, we note that height openings in a baie without openings, made of soles, modeled by CROD elements, and their soul is modeled they do not include any load, their presence in this area is therefore with CQUAD4 elements, their normal pointing backwards to ensure virtually useless. By against the stiffeners located immediately above consistent results. The stiffeners are modeled by CROD elements, the and below the openings experimenting stress concentration factors of coating of CQUAD4 elements. Normal of these elements should always up to 1.56. For managers we can say that the plates are at the openings, point outwards from the cabin. The floor beams are made of soles and the top of the fuselage and about at the floor, undergo an increase souls. The soles are then modeled by CROD elements and the core elements by CQUAD4 with their normal pointing backward or outside in internal stress with a stress concentration factor of up to 1.29. In of the aircraft. As regards the properties of the elements, the coating is addition, it appears that top plates immediately resumes lower fewer made of aluminum alloy Al 2024-T3 having a thickness of 0.06 ‘’, the loads (Figure 5). frames are Al 7475-T7351 (with a thickness of 0.06 ‘’ for CQUAD and Geometric modeling an area of 0.2508 in2 for ROD) along the floor (with a thickness of 0.1 ‘’ and for CQUAD 0.51in2 area for ROD). Finally the stiffeners are made Firstly revisit the structure of a fuselage. Airliner fuselages are very by 2024-T62 (0.1272 in2 for the area) to those of the upper crown of similar. The type of the most commonly used structure is the semi- monocoque, that is to say, an enhanced cell. The semi-monocoque structure is effective for its weight compared to its rigidity. It allows among other things, to tolerate a crack avoiding the whole structure is affected by the redistribution of loads in other members. Thus, partitions (bulkheads), frames, stiffeners (stringers) and spars are regularly used to give support to the structure. Figure 6 highlights the set of these components.
Details
-
File Typepdf
-
Upload Time-
-
Content LanguagesEnglish
-
Upload UserAnonymous/Not logged-in
-
File Pages8 Page
-
File Size-