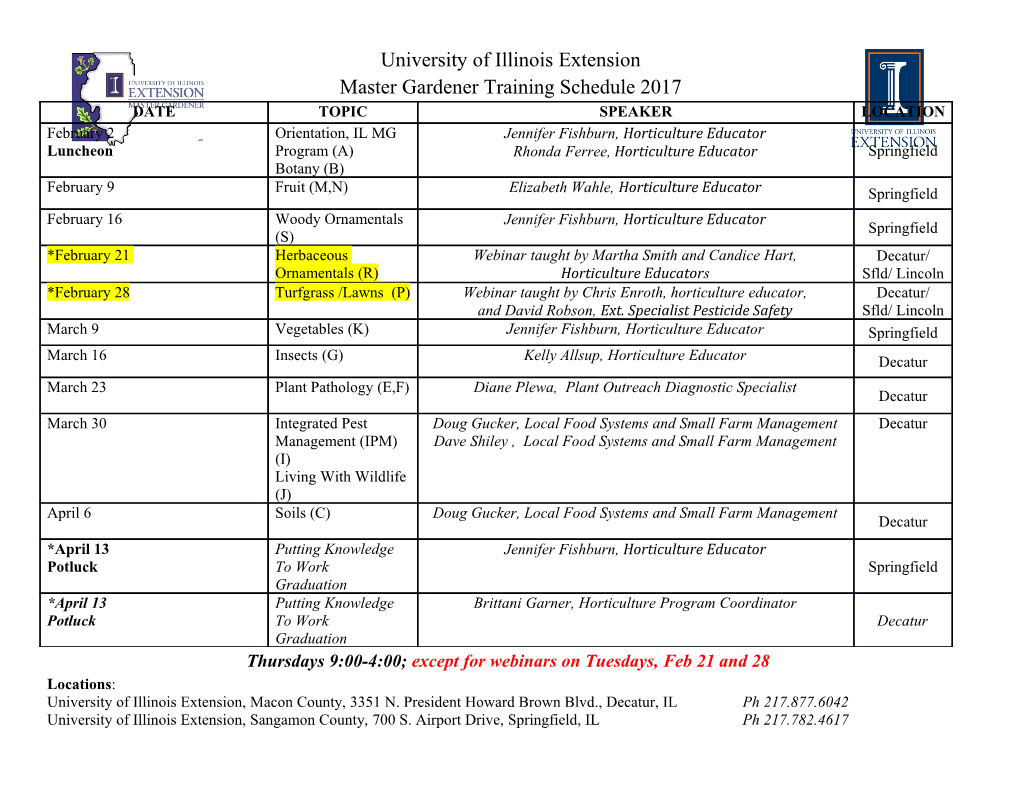
Energies 2010, 3, 216-240; doi:10.3390/en3020216 OPEN ACCESS energies ISSN 1996-1073 www.mdpi.com/journal/energies Review Gasification Processes Old and New: A Basic Review of the Major Technologies Ronald W. Breault NETL-US DOE, PO Box 880 Morgantown, WV 26507, USA; E-Mail: [email protected]; Tel.: +01-304-285-4486; Fax: +01-304-285-4403. Received: 8 January 2010 / Accepted: 3 February 2010 / Published: 23 February 2010 Abstract: This paper has been put together to provide a single source document that not only reviews the historical development of gasification but also compares the process to combustion. It also provides a short discussion on integrated gasification and combined cycle processes. The major focus of the paper is to describe the twelve major gasifiers being marketed today. Some of these are already fully developed while others are in various stages of development. The hydrodynamics and kinetics of each are reviewed along with the most likely gas composition from each of the technologies when using a variety of fuels under different conditions from air blown to oxygen blown and atmospheric pressure to several atmospheres. Keywords: gasification; gasifier; IGCC; gas composition 1. Introduction Gasification has been around for more than 200 years, so why the interest in it now? There are to be sure, many reasons, but the two most significant reasons are the continuing high price of natural gas and highway transportation fuels. Granted, over the past year and a half, these prices have moderated considerably. However over the past month, the price of gasoline has inched upward about 30 cents per gallon. The second significant reason is the need for energy independence. In other words, the use of domestic energy sources such as coal not only for electricity production but also for synthetic natural gas (SNG) and liquids for transportation is a must. Gasification is a key fundamental baseline technology for converting coal to anything other than electrons and can potentially be competitive even there [1]. For example, gasification it the key conversion step for converting coal to H2, SNG, liquid fuels, and the capture of CO2 for sequestration. Energies 2010, 3 217 Gasification has excellent environmental performance such that some states’ Public Utility Commissions have identified Integrated Gasification Combined Cycle (IGCC) plants for power generation as the best available control technology (BACT). In addition, the uncertainty of carbon management requirements and the potential suitability of IGCC for CO2 controls make it an ideal choice for power. So, what is gasification? Gasification is a conversion technology converts any carbon-containing material, coal for example, into synthesis gas as shown in Figure 1. Carbon reacts with water in the form of steam and oxygen at relatively high pressure typically greater that 30 Bar and at temperatures typically reaching 1,500 K to produce raw synthesis gas or syngas, a mixture composed primarily of carbon monoxide and hydrogen and some minor byproducts. The byproducts are removed to produce a clean syngas that can be used as a fuel to generate electricity or steam, as a basic chemical building block for a large number of uses in the petrochemical and refining industries, and for the production of hydrogen. Gasification adds value to low- or negative-value feed stocks by converting them to marketable fuels and products. Figure 1. Gasification process basics. Oxygen Extreme Conditions: 30 bar or more 1000 to 1,500 Deg K Corrosive slag and H2S gas Coal Products (syngas) CO (Carbon Monoxide) Gas H2 (Hydrogen) Clean-Up [CO/H2 ratio can be adjusted] Before Product By-products Use H2S (Hydrogen Sulfide) CO2 (Carbon Dioxide) Slag (Minerals from Coal) Water There are a number of previous reviews and extended writings on gasification that can be reviewed in conjunction with this paper to get a deeper understanding of the process and various gasification technologies. These include Higmans book sited as [4], the Gasification Technologies Council website http://www.gasification.org/, the DOE Gasification website http://www.netl.doe.gov/technologies/ coalpower/gasification/index.html, and numerous conferences including Gasification Technologies Annual Conference , the Clearwater Conference and the Pittsburgh Coal Conference. Energies 2010, 3 218 1.1. History of gasification Town gas, a gaseous product manufactured from coal, containing approximately 50% hydrogen, with the rest comprised of mostly methane and carbon dioxide, with 3% to 6% carbon monoxide, is a gaseous product manufactured from coal. It supplied lighting and heating for industrializing America and Europe beginning in the early 1800s. The first public street lighting with gas took place in Pall Mall, London on January 28, 1807. Not long after that, Baltimore, Maryland began the first commercial gas lighting of residences, streets, and businesses in 1816. A typical town gas plant for the era is shown in Figure 2. Figure 2. Baltimore’s Bayard Street Station from ―Progressive Magazine‖ of 1889 picturing plant prior to 1850 [2]. Since that time, gasification has had its ups and downs with more and longer periods of down as communities began to electrify. The few highpoints of gasification during the past hundred years are worthy of identification. Gasification was used extensively during World War II to convert coal into transportation fuels via the Fischer-Tropsch process. It has been used extensively in the last 50 to 60 years to convert coal and heavy oil into hydrogen—for the production of ammonia/urea fertilizer. The chemical industry and the refinery industry applied gasification in the 1960s and 1980s, respectively, for feedstock preparation. In the past 10 to 15 years, it has started to be used by the power industry in Integrated Gasification Combined Cycle (IGCC) plants. 2. Integrated Gasification Combined Cycle IGCC plants as shown in Figure 3 convert carbonaceous fuels/materials into electricity and could be considered first generation plants—those not requiring CO2 separation or sequestration. In this plant, the carbon containing material is fed to the gasifier along with oxygen and steam to produce the raw syngas. The raw syngas is cleaned of particulate matter and sulfur. The clean syngas is fed to the combustion turbine with the products going to a heat recovery steam generator and steam turbine. IGCC systems with carbon capture are similar to IGCC systems without carbon capture as can be seen by comparing Figures 3 and 4. Figure 4 shows the IGCC system with pre-combustion capture of the carbon for sequestration. The primary difference between the two processes is that the clean syngas passes through a shift reactor and an absorption tower to remove the carbon in the form of carbon Energies 2010, 3 219 dioxide. The shift reactor converts the CO in the syngas by reacting it with water to form H2 and CO2 with the latter going to sequestration. Figure 3. IGCC system without carbon capture [1]. Figure 4. IGCC with carbon capture [1]. Particulate Gas Shift Gas Removal Cleanup Reactor Separator Carbon Dioxide to Sequestration Gasifier Particulates Sulfur By-product Fly ash Gaseous By-product Constituents Combustor Air Separator Oxygen Air Coal, Compressed Air Gas Petroleum coke, Solids Turbine Biomass, Waste, etc. Air Electric Power Generator Air Heat Recovery Steam Generator Steam Stack Slag By-product Steam Generator Electric Steam Turbine Power Energies 2010, 3 220 Figure 5 shows a conceptual poly-generation IGCC plant. In this concept, the clean syngas is shifted to change the CO/H2 ratio. A partial shift adjusts the ratio to be comparable to the end hydrocarbon product being synthesized. If power is being made as the product, the gas stream will undergo a full shift. Figure 5. Poly-generation plant [1]. Particulate Gas Shift Synthesis Gas Removal Cleanup Reactor Conversion Fuels and Chemicals Gasifier Particulates Sulfur Carbon Dioxide By-product Gas Sequestration Fly ash Separation Gaseous By-product Constituents Hydrogen Combustor Air Separator Fuel Cells Air Electric Power Oxygen Coal, Compressed Air Gas Petroleum coke, Solids Turbine Biomass, Waste, etc. Air Electric Power Generator Air Heat Recovery Steam Generator Steam Stack Slag By-product Steam Generator Electric Steam Turbine Power 3. Gasification Versus Combustion Gasification and combustion can essentially be considered as two ends of a continuum for reactions of coal and oxygen, although water can be added as a reactant to increase the H2 content of the products. Table 1 provides a list of the most significant reactions and the enthalpy change associated with each of these reactions. Looking at the first two reactions in the table, it is seen that coal denoted here with a C for carbon is reacted with one oxygen atom denoted here as 1/2 O2 to get carbon monoxide and with two oxygen atoms (2) to get carbon dioxide. In reality, this second reaction is not a one step process as the solid phase carbon reacts with one oxygen atom to produce carbon monoxide which then reacts with the second oxygen atom to form carbon dioxide. All of the reactions in the table are exothermic except the two reactions identified as gasification with steam and gasification with carbon dioxide. These two endothermic reactions are the reactions that are most often referred to as gasification, where the solids carbon is turned into a reactive gas through a reaction with a ―non-reactive‖ gas (H2O or CO2). In addition to these two reactions being endothermic, they also require high temperatures to proceed. Energies 2010, 3 221 Table 1. Gasification and Combustion Chemistry. Reaction Process Chemical Formula Change in Enthalpy Gasification with Oxygen C + ½ O2 → CO –3,922 Btu/lb C Combustion with Oxygen C + O2 → CO2 –14,111 Btu/lb C Gasification with Carbon Dioxide C + CO2 → 2 CO 6,267 Btu/lb C Gasification with Steam C + H2O → CO + H2 4,750 Btu/lb C Gasification with Hydrogen C + 2 H2 → CH4 –2,672 Btu/lb C Water Gas Shift CO + H2O → CO2 + H2 –650 Btu/lb CO Methanation CO + 3 H2 → CH4 + H2O –3,181 Btu/lb CO Table 2 contrasts combustion and gasification.
Details
-
File Typepdf
-
Upload Time-
-
Content LanguagesEnglish
-
Upload UserAnonymous/Not logged-in
-
File Pages25 Page
-
File Size-