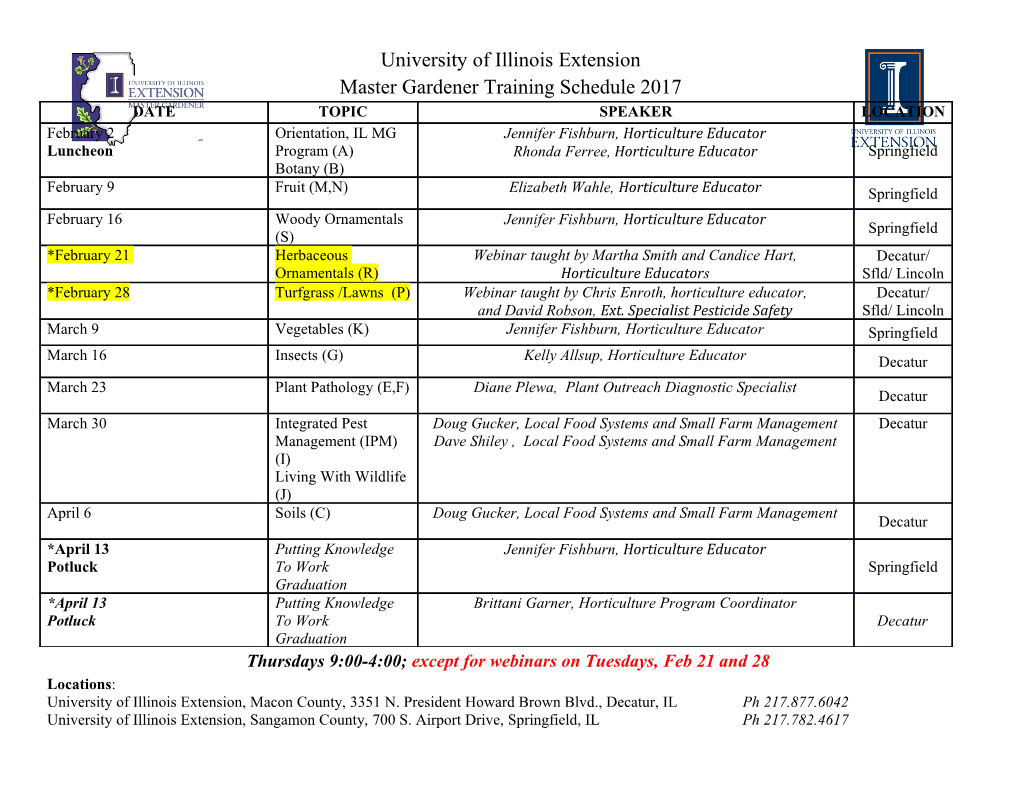
Nov. 21, 1939. H. J. NESS 2,181,093 HEAT TREATMENT OF METALS Filed Jan. 26, 1938 MM 1// M 1. 11221,MM-77 1222 / / / / / /27 / /2222277/2 / / / / / / / / / 2.7/ / /- /, ., ,. ,. M2 2 2.M& N NSy 70 A/A A/yd 6AS INVENTOR sweezy Aaro?ez-MAess BY 22. --Cee ATAORNEY | Patented Nov. 21, 1939 2,181,093 UNITED STATES PATENT office 2,181,093 EEAT TREAMNT OF METALS arold J. Ness, Bloomfield, N.J., assignor to Nes alloy Products, inc., New York, N. Y., a corpool ration of New Jersey Application January 26, 1938, serial No. 186,941 2 Claims. (C. 148-16) This invention relates to the metallurgy of both surface of the part and may be discovered only ferrous and non-ferrous metals and more particul on failure of the part in use. Similar decarburi larly to the provision of an atmosphere for the zation and scaling problems arise in the reheating heating and heat treatment of such metals for of billets and the heating of bars, wire bars and 5 mechanical working, normalizing, hardening, etc. slabs for rolling, piercing, as in tube making, in This application is a continuation in part of the SOaking of steel ingots, and in the heat treat my applications Serial No. 67,547, fled March 6, ment of finished or partially finished parts for 1936, and entitled "Metallurgical process and ap hardening, normalizing, etc. Troublesome oxide paratus', Serial No. 79,968, filed May 15, 1936, formations also Occur in the heating and heat 0. and entitled 'Metallurgical process', and Serial treatment of such metals as brass, copper and 0 No. 84,413, filed June 6, 1936, and entitled "Pre aluminum, for forging, rolling, drawing, spin vention of scale formation on ferrous metals'. ning, etc. In the forging of steel for the fabrication of It is, therefore, one of the objects of the pres such parts as connecting rods, crank shafts, auto ent invention to eliminate decarburization and/or 5 mobile axles, aircraft engine cylinders, gears, Scaling of iron, and steel parts during heating in 5 cutlery, etc., it is necessary to heat the steel to preparation for the mechanical working thereof, the forging temperature, usually between 2000' F. Or for normalizing or hardening thereof. and 2600° F. During such heating decarburiza Another object is to provide uniformity in tion of the surface of the metal occurs and a weight and size of parts being heated or treated. 20 heavy layer of scale accumulates on the surface Still another object is to provide a method of 20 thereof, which scale must be removed before preventing carburization, and/or scale formation forging. This is usually accomplished by impact during heating of iron and steel, which method and scraping and by directing a stream of live will be simple, inexpensive and dependable. steam at considerable pressure against the bars Another object is to prevent oxide formation or blanks. These procedures, however, do not On non-ferrous metals, such as copper, brass completely remove the scale, and as a Conse and aluminum, during heating thereof. quence there is a large proportion of rejections Another object is to enable forgings and other of forged parts due to the scale falling into the mechanically worked metal parts of superior qual forging die and being hammered or forced into ity to be obtained. 30 the surface of the forging during the forging Op Another object is to prevent detrimental alter 30 eration. Moreover, due to the abrasive action of ation of the composition or structure of metal, this scale, the life of the forging dies is materially ordinarily resulting from contact with the fur shortened. In the forging of large or complicat nace gases, during the heating thereof. ed parts many operations are required and often Another object is to protect the metal both it is necessary to reheat the parts several times, physically and chemically, against oxidation, de before the forging operation is completed. Each carburization or detrimental alteration of its heating of the metal, of course, causes additional composition or structure, during the heating scale formation, decarburization, etc., and the thereof and during the subsequent Working resultant reduction in size of the part caused and/or cooling thereof. by the removal of the scale or the deepened de A still further object is to degasify metal, im 40 carburization thereof must be allowed for. How prove its grain refinement and enhance its physi ever, the depth of scale formation or decarburi cal properties. zation is variable depending. On the length and Another object is to condition steel to facili temperature of the heating and the composi tate nitriting thereof. 45 tion of the furnace gases and of the metal, and A still further object is to enable the foregoing 45 hence they cannot be accurately compensated for. objects to be accomplished in a furnace of the Therefore, considerable machining of the parts electric, oil or gas fired type. to remove the decarburized surface portion there Other objects and advantages will hereinafter of and to bring the parts to accurate size is usu appear. 50 ally required. Moreover, any scale driven into In accordance with the present invention I the forging in one of the early operations is heat the metal for treatment Or in preparation for Worked deeper into the metal as subsequent op mechanical working, in an atmosphere contain erations are performed thereon and may weaken ing lithium, which in contact with the metal and render the part defective. Such defects are serves to deoxidize or partially deoxidize the same 55 not always detectable by an examination of the and preyent decarburization of the metal or oxide 55 2 2,181,093 formations on the surface thereof. In the pro Oxygen from that required for complete combus duction and maintenance of the required lithium tion so that the furnace gases will contain a Small containing atmosphere in the treating furnace, percentage of carbon monoxide, the purpose of I prefer to employ a lining for the furnace which which will hereinafter appear. The lithium com s does not absorb too great a quantity of the lithium pounds introduced into the furnace results in the or react detrimentally therewith during the heat formation of lithium metal, lithium oxide and ing process. It is desirable to condition the lining lithium carbonate in the furnace atmosphere. before use by heating the lining, either before The lithium metal serves to eliminate free oxygen or after assembly in the furnace, in the presence from the furnace atmosphere with the formation O of a vapor of lithium or compound of lithium, of lithium oxide. The lithium oxide unites with 0. preferably at a temperature of about 2000 F. The carbon monoxide in the furnace atmosphere to treatment can also be effected by applying to the form lithium carbonate and metallic lithium. lining a compound of lithium, such as lithium The lithium carbonate thermally dissociates into chloride. The compound may be applied as a carbon dioxide and lithium oxide. When the 5 water solution or suspended or dissolved in other metal to be heated is placed in the furnace, com 5 volatile vehicles, as fully set forth in my copend pounds of lithium, mainly the Oxide or carbonate ing application Serial No. 112,988, filed November So present in the atmosphere condense thereon 27, 1936, and entitled "Furnaces'. and form a protective coating over the surface, While a furnace lining so treated will give off protecting the same from any oxidation, decar 20 lithium vapor for a considerable period, it is de burization or other detrimental alteration of the 20 sirable, in Order to maintain such atmosphere, composition or structure of the metal that might that additional amounts of lithium be supplied as otherwise occur. This protective coating remains the process continues. This may be accomplished on the metal throughout the heating process and by generating a vapor from a supply of lithium the Subsequent working and/or cooling of the contained in the furnace but I prefer to intro metal, and will remain on the parts during a sub 25 duce it into the furnace from the outside. A very sequent limited heating thereof in a non-lithiated effective way I have found of supplying lithium atmosphere. to the furnace is mixed with the air or fuel either In carrying out the heat treating process of the continuously or periodically. When introduced present invention, the furnace is brought up to periodically, the lining serves as a storage and the proper treating temperature and the lithium 30 liberating medium whereby the desired atmos compound is continuously or substantially con phere is maintained within the furnace between tinuously introduced into the furnace or into the the periods of introduction of the lithium. air or fuel stream leading to the furnace in such In place of introducing metallic lithium into quantity as to produce a rich lithium color in the the furnace, a compound thereof, such as the flame. The lithium not only neutralizes the oxi 35 chloride, fluoride, hydroxide, or carbonate of dizing effect of the furnace gases but the metal, as lithium, or lithium containing ores such as stated, immediately becomes coated with a protec spodumene or amblygonite, or mixtures thereof, tive layer composed primarily of lithium com may be used. The lithiated atmosphere may be pounds. At the time the metal is placed in the provided in a gas fired furnace, for instance, by furnace and for a brief interval thereafter, a 40 introducing a small quantity of a compound of copious supply of the lithium compound may be lithium in powdered form, into the air or gas introduced into the furnace, if desired, in order stream leading into the furnace or it may be to promote a rapid formation of the protective injected or blown directly into the furnace coating on the parts to be heated, and thereafter through an aperture provided in the walls thereof.
Details
-
File Typepdf
-
Upload Time-
-
Content LanguagesEnglish
-
Upload UserAnonymous/Not logged-in
-
File Pages7 Page
-
File Size-