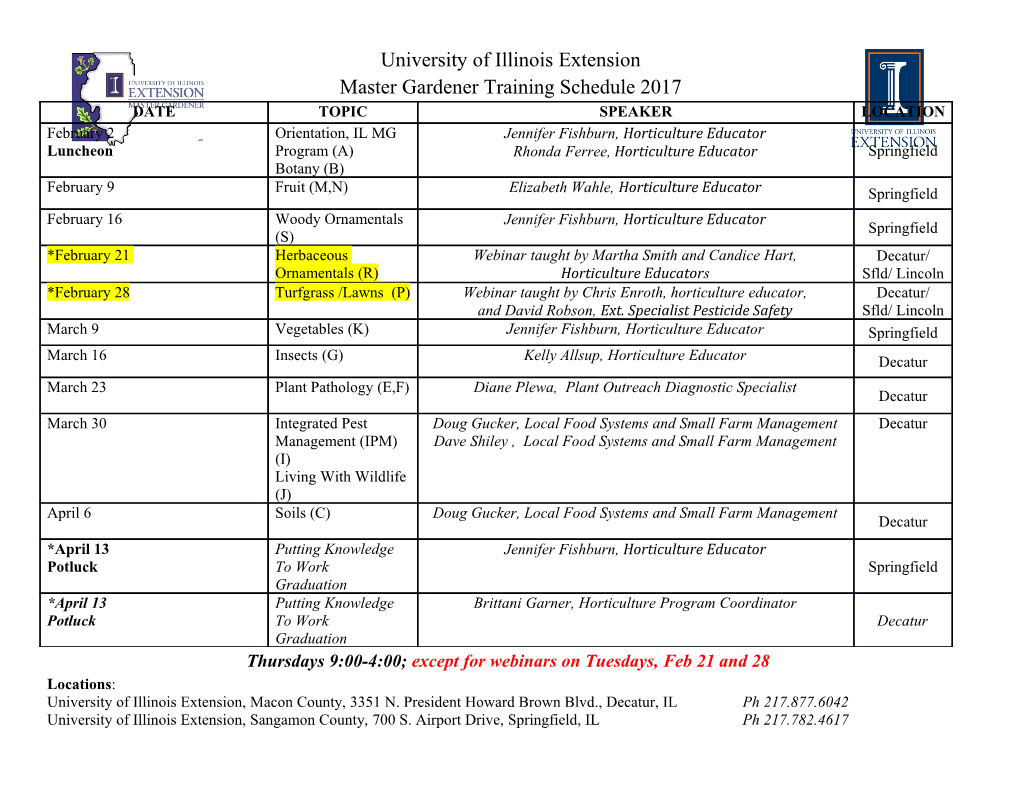
IIIUS005753190A United States Patent 19 11 Patent Number: 5,753,190 Haseltine et al. 45 Date of Patent: May 19, 1998 54 WACUUM SYSTEM FOR CONTROLLING FOREIGN PATENT DOCUMENTS PRESSURE INA POLYESTER PROCESS O685502A2 12/1995 European Pat. Off. 158786 C 2/1983 German Dem. Rep. (75) Inventors: Douglas M. Haseltine; Thomas L. 2809113 A1 10/1979 Germany. Yount; Jimmy L. Ryans, all of 56-59842. A 5/1981 Japan . Kingsport, Tenn. 788404 7/1995 Japan. 73) Assignee: Eastman Chemical Company, OTHER PUBLICATIONS Kingsport, Tenn. Patent Abstracts of Japan, vol. 10, No. 321, C-382, abstract of JPA61-130336 (Toyobo Co Ltd), 18 Jun. 1986. 21) Appl. No.: 505,428 Patent Abstracts of Japan, vol. 10, No. 4, C-322, abstract of 22 Filed: Jul. 21, 1995 JPA60-163918 (Toyo Boseki K.K.), 26 Aug. 1985. Patent Abstracts of Japan, vol. 10, No. 194, C-358, abstract Related U.S. Application Data of JPA61-37819 (Toray Ind Inc), 22 Feb. 1986. Ryans, J. L. and D. L. Roper, Process Wacuum System 62 Division of Ser. No. 401,375, Mar. 9, 1995, Pat. No. Design & Operation, McGraw-Hill Book Company, New 5,466,765. York, 1986, pp. 230-237. 51 Int. Cl. .............. C08F 2/00 Primary Examiner-Christopher Kim (52) U.S. Cl. ... ... 422/131; 422/134; 203/73; Attorney, Agent, or Firm-Karen A. Harding; Harry J. 203/77 Gwinnell 58) Field of Search ..................................... 422/131, 134; 526/65, 71; 528/272,308.3,308.5; 203/73. 57 ABSTRACT 77, 87 The present invention discloses a polymerization system having at least two reaction chambers wherein vacuum is 56) References Cited used to remove vapors therefrom comprising a single U.S. PATENT DOCUMENTS vacuum system for supplying vacuum in increasing amounts to successive reaction chambers. Also disclosed is a poly 3.157,619 11/1964 Bell et al. 3.250,747 5/1966 Mitchell et al. merization process having at least first and second reaction 3,359,074 12/1967 Dobo. chambers in which the pressure is decreased successively 3,468,849 9/1969 Rothert. from said first chamber to a final chamber. 4,758,650 7/1988 Van Endert .......................... 528/308.3 5,466,776 11/1995 Krautstrunk et al. ..................... 526/68 8 Claims, 2 Drawing Sheets U.S. Patent May 19, 1998 Sheet 1 of 2 5,753,190 Fig. PRIOR ART U.S. Patent May 19, 1998 Sheet 2 of 2 5,753,190 5,753,190 1 2 WACUUM SYSTEM FOR CONTROLLING vacuum system is quite large. In addition to raising the PRESSURE N A POLYESTER PROCESS capital cost per pound of polymer produced, the extra items diminish the overall reliability of the polymer plant. This is a divisional application of application Ser. No. Moreover, each vacuum system has its own motive fluid 08/401.375 filed Mar. 9, 1995, now U.S. Pat. No. 5466,765. 5 requirements. Thus, additional vacuum systems greatly increase the amount of motive fluid which must be treated to FIELD OF THE INVENTION remove environmental hazards. Accordingly, there remains The present invention relates to an apparatus for removal a need in the polymer production art for a simplified system of by-products and excess glycol from a commercial scale to condense vapor discharged from the reaction chambers 10 and to generate the required vacuum levels for the respective polymerization reaction. reaction chambers. BACKGROUND OF THE INVENTION DESCRIPTION OF THE DRAWINGS In a conventional condensation polymerization system the FIG. 1 shows a schematic of conventional apparatus used reactors are separate vessels; and each of the vessels has its 15 for the polymer production. own vacuum system with a direct-contact spray condenser. FIG. 2 shows a schematic of the apparatus of the present Frequently these systems experience problems as invention. by-products of the reaction and excess reactants are removed from the melt. Some monomer and low-molecular-weight DESCRIPTION OF THE INVENTION polymer, which have a high propensity for solidification, 20 The present invention discloses a polymerization system foul or plug condensers and vacuum equipment. This fouling having at least two reaction chambers wherein vacuum is is one of the most frequent reasons polymer plants lose used to remove vapors therefrom the improvement which annual production capacity. comprises a single vacuum system for supplying vacuum in Fundamentally, components have solubility limits of con increasing amounts to successive reaction chambers said centration in the fluids that are present in vapor-handling 25 single vacuum system comprising: equipment. Fouling can occur whenever the concentration of a component exceeds its solubility limit. When these limits a condenser connected to each reaction chamber except are exceeded in the laboratory or full-scale production the final reaction chamber, said condenser connected by a plants, one observes cloudy condensates; and fouling of condenser conduit; equipment is likely. Over time, this fouling causes opera 30 a reaction chamber ejector connected to each of said tional problems that must be dealt with. Often, production condensers and said final reaction chamber by an ejector plants must interrupt normal operations to handle the solid conduit; wherein said ejectors use condensed vapor from the build-up. They lose valuable production capacity during that reaction chamber as motive fluid; time. ejector discharge conduits connecting each of said ejec To alleviate the fouling in vapor handling equipment, 35 tors to the condenser of the preceding stage such that each several approaches have been developed. First, equipment is ejector discharges into the condenser connected to the pre jacketed to raise the surface temperatures. In theory, higher ceding reaction chamber; surface temperatures allow higher concentrations to be a finishing ejector connected to the first stage condenser present before solubility limits are exceeded. This is only by an ejector conduit; marginally effective, however, because the solvent tends to a vacuum pump connected to said finishing ejector via a evaporate. Where the mixtures are somewhat stagnant, this pump line; and evaporation enriches the mixture in solids-forming motive fluid feed lines which are connected to each of said ingredients, concentrations rise above solubility limits, and ejectors and which feed motive fluid into said ejectors. solids adhere to the surfaces. Also disclosed is a polymerization process having at least Design and operation of the condenser to handle relatively 45 first and second reaction stages in which the pressure is high levels of solids-forming material is another approach. decreased successively from said first stage to a final stage. Scraped-surface condensers are common now in many poly said process comprising the steps of: mer plants. These devices have moving mechanical parts maintaining a vacuum in said final stage by removing that remove solids as they build up on surfaces. final stage vapors therefrom via a final stage ejector con A solution to plugging in ejectors is described in U.S. Pat. 50 nected thereto by a vacuum line; No. 3.468,849. Instead of using steam as the motive fluid for directing discharge from said final chamber ejector into a an ejector, they use a solvent that tends to dissolve the first chamber precondenser to produce first chamber non solids-forming materials. For polyethylene terephthalate condensed materials and condensed first chamber ejector (PET), the motive fluid is ethylene glycol vapor. Since 55 motive fluid; ethylene glycol is a primary reactant for the PET reaction directing said first chamber ejector non-condensed mate and a good solvent, it is an ideal fluid for the ejectors. rials from said first chamber precondenser to a second The apparatus disclosed in U.S. Pat. No. 3.468,849 has ejector connected thereto by a vacuum line; several independent reaction vessels or chambers. Since a directing discharge from said second ejector into a second single ejector cannot practically be designed to achieve the condenser to produce second condenser non-condensed very low pressures required by the process, each reaction materials and condensed second ejector motive fluid; chamber has its own multistage vacuum system to compress wherein said second condenser is connected to a vacuum the inerts from the given reaction chamber. pump. However, this configuration has been found to be unde Preferably, the vacuum system of the present invention sirable in several respects. The capital cost of an additional 65 comprises at least three serially attached vacuum means condenser and an additional vacuum system and the auxil which are selectively attached to the appropriate reaction iary equipment required for operation of the condenser and chambers. 5,753,190 3 4 The apparatus is further described with reference to FIG. Once the raw materials have formed the desired oligomers 2. the solution passes through the first seal (2) into the second reaction chamber (C2). If the reaction is conducted in The raw materials necessary for the desired polymeriza multichambered single vessel reactor the mixture passes tion are introduced into the first chamber (C1) of the reaction through a seal or valve. Any configuration capable of vessel (5) via line 1. Suitable raw materials for introduction maintaining a liquid seal between the reaction chambers, into (C1) include the reaction products of dicarboxylic acids which operate at different pressures, may be used. Examples such as, but not limited to terephthalic acid, isophthalic acid, include conventional pipe traps where the discharge is cyclohexane dicarboxylic acid, naphthalenedicarboxylic elevated sufficiently above the inlet to keep the trap full of acid and mixtures thereof. dicarboxylic esters such as, but liquid (a height equivalent to the maximum static pressure not limited to dimethylterephthalate, dimethylisophthalate, 10 difference between the two chambers, plus the fictional dimethylnaphthalene dicarboxylate and mixtures thereof, pressure loss due to flow in the pipe) and otherflow channels and glycols such as, but not limited to ethylene glycol, that are not circular, but also accomplish a full liquid seal to diethylene glycol and cyclohexane dimethanol and mixtures prevent vapor flow between chambers.
Details
-
File Typepdf
-
Upload Time-
-
Content LanguagesEnglish
-
Upload UserAnonymous/Not logged-in
-
File Pages7 Page
-
File Size-