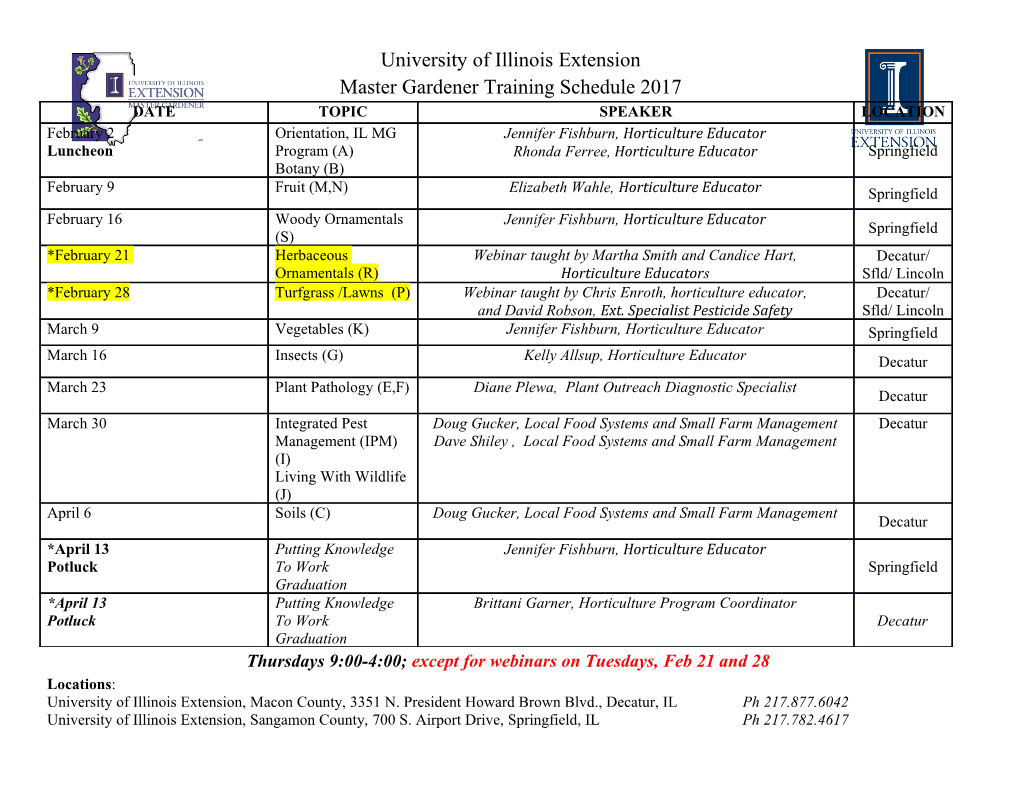
RPN20130114P016.qxp 1/9/2013 3:27 PM Page 1 16 Rubber & Plastics News ● January 14, 2013 www.rubbernews.com Techinical Evolution of calender roll adjust systems By Lawrence Gooch were added to the lifter assembly to re- Gooch Engineering Associates duce friction and permit the reduction of “Calender roll adjust systems” describes Executive summary clearance in the total assembly. the means of adjusting one roll with re- The evolving technologies for calender roll position and nip pressure control Screw thread profiles and the number spect to another. are reviewed and compared in this paper. of threads per inch have been experi- The description is usually specific to The influence of roll nip control on the uniformity of sheet thickness, “strike mented with, and screws have increased the mechanism for opening or closing through” in fabric coating/laminating operations and cord spacing when double- in size to improve stiffness. the gap between two adjacent rolls. For coating reinforcing cord and wire are discussed. Broad guidelines for the selec- Screw and nut roll positioning sys- our purposes we will broaden the defini- tion and employment of available technologies are developed with an emphasis tems are gap control systems. The posi- tion to include the means of correcting on practical application across the spectrum of calendering operations common tion of the roll bearing box is adjusted to for changes in roll deflection—roll cross- to the tire industry. achieve the gap necessary between two ing or skewing, and roll bending—and adjacent rolls to produce a sheet or layer extend it still further to the control of of material of the desired thickness; to pressure in the laminating nip. tration and/or “strike-through” is de- chanical screw and nut, hybrid hy- successfully transfer the sheet or layer While the specifics of what follows pendent on the closeness of the weave draulic/screw and nut, and full hy- to a substrate; and, to fully encapsulate deal explicitly with calenders employed and the intended application. draulic. cord or wire. In the case of thickness, to coat fabric or cord and wire for the The principal focus of this discussion Screw and nut. For well over a cen- with some form of measurement—even production of tires, much of what will be is the relationship between certain me- tury and a half, the primary mechanism as simple as manual “snap gauging,” the covered is equally applicable to any chanical components of the calender and for adjusting the gap between two adja- gap could be adjusted to achieve the de- coating operation carried out in a calen- one of the classic problems in coating cent rolls has utilized a screw and a nut. sired result. It was generally understood der. fabric, cord or wire: Ensuring sufficient The screw bears against the bearing box that in the case of laminating or coating Tire cord calendering initially was force or pressure in the coating or lami- of the moveable roll. The bearing box is operations, gap or position control was a carried out in three-roll vertical calen- nating nip to accomplish the full encap- coupled to the end of the screw by gravi- “stand in” for pressure. ders. A layer or coat of rubber of the re- sulation of the cord or wire while main- ty (for the bottom roll in a vertical stack) In the early 1950s load cell technology taining the proper cord or wire spacing. or by means of a lifter mechanism, with evolved and it became possible to build TECHNICAL NOTEBOOK In the case of fabric coating, the prob- some means of rotating the screw in the into roll adjust systems a strain gauge Edited by Harold Herzlichh lem is one of achieving sufficient pres- nut. load cell to actually measure the force sure to accomplish the transfer of the Over the years, various methods have being supported by the roll adjust sys- quired thickness was formed between rubber or compound from the calender been employed to improve precision and tem—and, at least in theory, providing the top roll and middle roll, and trans- roll to the substrate and “striking operation of these mechanisms. Initial- the ability to control that force. In prac- ferred or laminated to the substrate be- through” the fabric, or at least penetrat- ly, roll adjust drive trains were com- tice, the electronics of the time were at tween the middle roll and the bottom ing the weave sufficiently to minimize prised of a large hand wheel with a sim- best cumbersome to use. roll. air entrapment and ensure proper bond- ple transmission, jack shafts, bevel In most instances, for another 20 Double coating was accomplished by ing in subsequent assembly and curing gears and cross shafts with jaw clutches years or so, load cells in calenders so running the web back through the cal- operations. to worms and worm gears—all open equipped were more useful as means of ender with the other side up. Efficiency Accomplishing this objective success- gearing. Eventually, most systems set- obtaining design data than as a means was improved by adding a second, or fully under a variety of operating condi- tled on individual two-speed motors of feedback for adjusting the roll posi- tandem, three-roll calender, and coating tions requires an understanding of the with brakes driving each screw or nut tioning system. the second side of the web in line. relationship between product (com- through two-stage worm gear reducers. Splice relief. As calender lines be- In more recent times, four-roll calen- pound) characteristics, the mechanics of Thrust bearings of various types have came more sophisticated and line speeds ders have become the prevalent choice. rolls, the operation of the roll position- been interposed between the screw and increased, it became desirable to splice In a four-roll calender one layer of rub- ing systems, the method and operation the roll bearing box. Some builders opt- the tail end of one roll of fabric or cord to ber is developed between the first and of the coating or web thickness measure- ed for rotating nuts with non-rotating the leading end of the next, first to re- second rolls, a second layer between the ment system, and the interplay between screws—thereby moving the thrust duce thread-up time, and then to avoid third and fourth rolls, and two layers the sheet forming operation in the first bearing from the bearing box to the cal- having to change line speed—to run as are simultaneously coated on the sub- nip and the laminating or coating opera- ender frame or housing. Thrust bearings continuously as possible. strate between the second and third tion in the second. rolls. Fig. 2. Roll deflection, crown and crown correction. In the case of cord or wire, the objec- Roll adjust or positioning systems tive is to fully coat each cord or wire; in There are three primary systems in the case of a fabric the degree of pene- use today, each with variations: me- Fig. 1. Cord spacing, calendered wire or tire cord. RPN20130114P017.qxp 1/10/2013 3:46 PM Page 1 www.rubbernews.com Rubber & Plastics News ● January 14, 2013 17 Technical Some means was needed to permit the splice relief cylinders. The design necessary to provide feedback to the ser- pression, these clearances are one side rapidly opening and re-closing the lami- and/or implementation of these systems vo valves. of the tooth or bearing; when adjusted nating nip to permit a splice to pass. were driven by three different potential The combination of precision position under no load conditions, depending on The solution was a short-stroke hy- advantages: measurement, rapid signal processing the orientation of the screw, they are on draulic cylinder interposed between the ● The theoretical ability, with the and precise and rapid valve response the other side. roll adjust thrust bearing and the roll proper controls and valves, to respond provided the means necessary to control To improve control of the roll position, bearing housing. The cylinder was usu- very rapidly to changes in operating for the change in volume of the oil in the or perhaps more accurately, the center ally built into the lifter assembly itself, conditions—specifically, the ability to cylinder when a load was applied. of rotation of the roll journal, preload or and close observation was necessary to change the effective gap quickly in re- Two different approaches to imple- zero-clearance bearings were added to detect their presence. sponse to measured deviations from tar- menting full hydraulic roll positioning the roll adjust positioning system. In some more recent four-roll “Z” or get gauge or thickness. were pursued: Preloads consist of a second bearing “S” calenders, the splice relief cylinder ● The capability of rapidly opening a ● In the late 1960s and early 1970s, outboard of the main bearing coupled to has been installed between what would roll nip in the event of an accident or a Farrel developed and fielded two varia- the calender frame by a means of apply- normally be the “fixed” roll and the cal- loss of product, and tions of an hydraulic roll adjust system ing load to that bearing. The arrange- ender end frame or housing, a choice ● Protection of the roll from overload. that essentially made the roll adjust ment permits pulling the roll closer to made possible both by virtue of the roll The retention of the adjusting screw system itself a large servo-valve; and the position it will operate in when un- arrangement and the almost universal and nut in the design permitted opera- ● With the evolution of hydraulic con- der load, and at the same time, removes adoption of individual roll drive.
Details
-
File Typepdf
-
Upload Time-
-
Content LanguagesEnglish
-
Upload UserAnonymous/Not logged-in
-
File Pages4 Page
-
File Size-