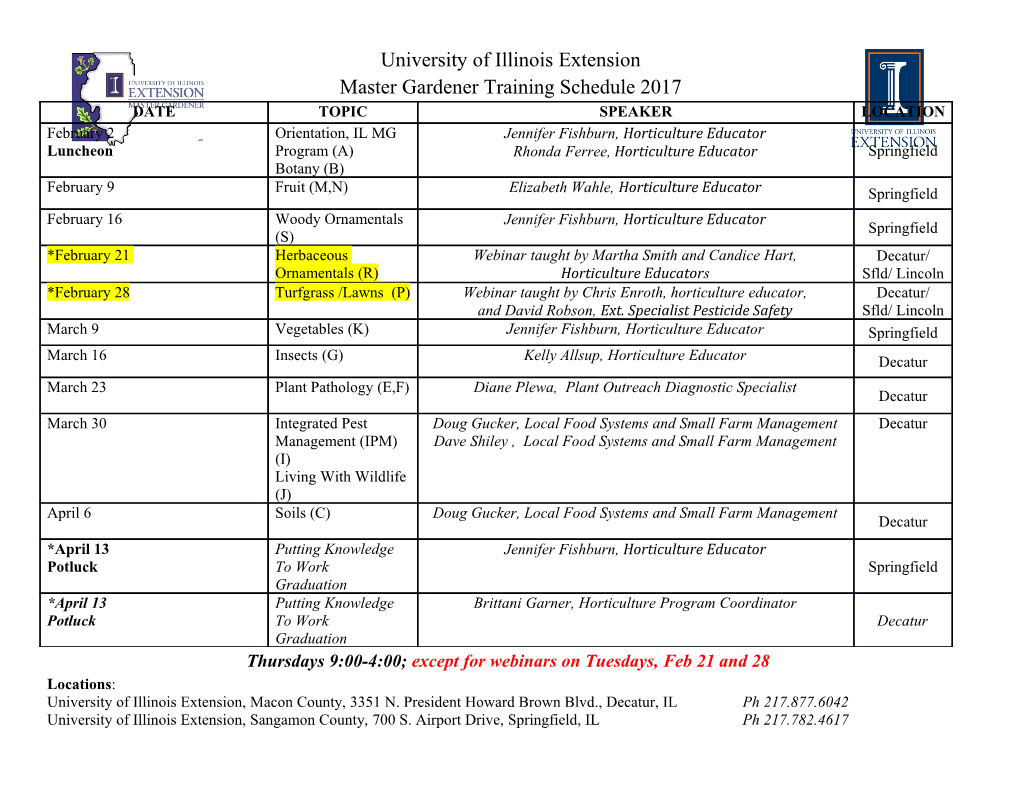
GEARS AND GEAR CUTTING PDF, EPUB, EBOOK Ivan R. Law | 136 pages | 10 Jan 1998 | Special Interest Model Books | 9780852429112 | English | Hemel Hempstead, United Kingdom Gears and Gear Cutting PDF Book We are second to none on this front. Instead, I'm going to grind the tip flat. I don't feel the "clicks" and the gear will spin freely when I flick it with my finger. Furthermore, the cutter is easier to make than the usual button type tool. The most you can take off the tip is. The indexing fixture itself receives its name from the original purpose of the tool: moving the table in precise, fixed increments. Main article: Gear shaper. When broaches are not available we can also wire erode the teeth. The teeth or gaps are cut one at a time with an indexing device of some form. Before I get into any math or even definitions, let's just illustrate the idea of how the involute can be generated. The "module" system is just the inverse of this, but I don't intend to cover that. Why don't you care about involutes? Compare the location of the cutter with the crosshairs. We'll assume you're ok with this, but you can opt-out if you wish. Necessary Necessary. However, I set up a "cavity" of fire bricks, set the gear cutter inside and played a propane torch the working end for a few minutes. Search for:. Download as PDF Printable version. The hob must make one revolution to create each tooth of the gear. It is basically when a cutter that looks similar to a gear cuts a gear blank. I'm not going to go into exactly how I turned the right thickness and diameter, since this is basic machining. Let's say you had a gear blank made of soft clay. Instead it is a rack form an the gaps each side of the current gap are modified as the current gap is being cut. The largest gears are produced on these machines. There are a few constraints here. A cutter is made that looks a bit like a hob bit without the helical teeth that require constant rotation of the gear blank. Gear cutting is the process of machining gears into shape. I think some of this either covers or can be generalized to cover internal, helical and some other types of gears, but I haven't tried any of that yet. First, you can cut each tooth, one at a time. The tool is essentially that shown in the animation above, but adapted for use on a milling machine. What are the actual dimensions of that cutter? If you want to have the approximation be more accurate, you just take more cuts. An acme thread gauge has tip widths built into it. Gears and Gear Cutting Writer Instead, I bought a gear to replicate. It's because the path that the gear took through the clay would leave the right shape. The important point is that the accuracy is up to you and you only need one cutter for a "family" of gears. When choosing gear cutting companies make sure you choose one who has the knowledge and facilities that we have. A rotary table and a Y axis are the customary axes available. To do this you need a cutter and some way of accurately indexing the gear blank for the cutting. If you want to have the approximation be more accurate, you just take more cuts. Necessary Necessary. The indexing fixture itself receives its name from the original purpose of the tool: moving the table in precise, fixed increments. Step 3: Cut teeth. There's also a tool that will be used to make the cutter and I'll call that the "single-point cutter". Used very often for all sizes of production runs, but works best for medium to high. Therefore it is mostly used in very high production runs. Categories : Gears Machining. Some metal gears made with powder metallurgy require subsequent machining, whereas others are complete after sintering. I wanted to replicate one from my lathe, but I don't have any tool steel big enough to make a cutter that will cut teeth that deep. The teeth or gaps are cut one at a time with an indexing device of some form. If you look up how to make gears, you'll find two kinds of information. Gears are commonly made from metal , plastic , and wood. After being cut the gear can be finished by shaving , burnishing , grinding, honing or lapping. Also, for simplicity we are creating the cutter's roots sharp. They have six to twelve teeth and eventually have to be moved back to the starting point to begin another cut. The rotation of the blank is from the dividing head indexing to each location for each cut. Please help improve this article by adding citations to reliable sources. Home made cutters can be ground for just one size of gear and, like the commercial cutters, will also cut a range of gears of similar sizes. If you rolled a gear around that clay, it would form the right shapes in the clay. This can be anything from making your watch tick to raising a draw bridge for a large carrier. We'll assume you're ok with this, but you can opt-out if you wish. This is like a worm that turns and cuts the gear. I did some trig to figure some optimal angles, but it's too complicated for how little it matters exactly what you do. Pressure angle PA : The actual meaning of this angle will be made clearer down below. One advantage of this method is that, while the hob has to be carefully made, it does not have to be the exact shape of the gap between teeth. This method also works for cutting internal splines. Strictly, this requires a special cutter and a machine whose function in life is to hob gears. Now we come to numbers. It then operates similarly to a carriage on a lathe. Some machines will cut to a depth on the Y axis and index the rotary table automatically. Second, you could hob the gear. Small Steel pinion, 22 teeth, 0. If the indexing worm is not disengaged from the table, one can move the table in a highly controlled fashion via the indexing plate to produce linear movement of great precision such as a vernier scale. Basically, it's the negative space of a rack. This is done by taking a blank gear and rotating a cutter, with the desired tooth pattern, around its periphery. The hobbing features for gears are straight, helical, straight bevel, face, crowned, worm, cylkro and chamfering. Why don't you care about involutes? Using a subset of those infinite positions will yield an approximation of the involute, where the more positions you use the better the approximation is. Gears and Gear Cutting Reviews Gears are not exclusively made of metal and can also be made of plastic or even fibre. The rotation of the blank is from the dividing head indexing to each location for each cut. Instead it is a rack form an the gaps each side of the current gap are modified as the current gap is being cut. Gears are commonly made from metal , plastic , and wood. Hopwood Gear ltd is a gear cutting company in the UK who can manufacture all your gears from start to finish all under one roof. This quickly gets expensive. The angle must be set up at minus 90 between the hob and the gear blank, but then the lead angle of the hob threads must be accounted for. The largest gears are produced on these machines. It took about 5 min before it started glowing. So I'm going to do a little outside-the-box thinking. Categories : Gears Machining. So, if my ground single-point cutter fits in the 10 TPI acme thread gauge slot, and doing a little trig, I know I've ground off. Using a subset of those infinite positions will yield an approximation of the involute, where the more positions you use the better the approximation is. Hobbing machines are complex, expensive and have awkward limitations for cutting gears with prime numbers of teeth. I'm also not going to go into workholding, since that's going to vary with gear size, number of gears being cut, materials, time, etc. There are several different ways to make gears. Compare the location of the cutter with the crosshairs. Just keep track of how much you take off and shorten the depth in step 2 by that amount. Spur may be cut or ground on a milling machine or jig grinder utilizing a numbered gear cutter , and any indexing head or rotary table. Second, you could hob the gear. The indexing fixture itself receives its name from the original purpose of the tool: moving the table in precise, fixed increments. Gears and Gear Cutting Read Online If this is not done then it will result in inefficient energy transfer and will ultimately wear and break down much quicker. I think some of this either covers or can be generalized to cover internal, helical and some other types of gears, but I haven't tried any of that yet. To do this, the gear blank must rotate as a specified speed as the hob does the cutting. If I had a tool and cutter grinder, I could just do that.
Details
-
File Typepdf
-
Upload Time-
-
Content LanguagesEnglish
-
Upload UserAnonymous/Not logged-in
-
File Pages4 Page
-
File Size-