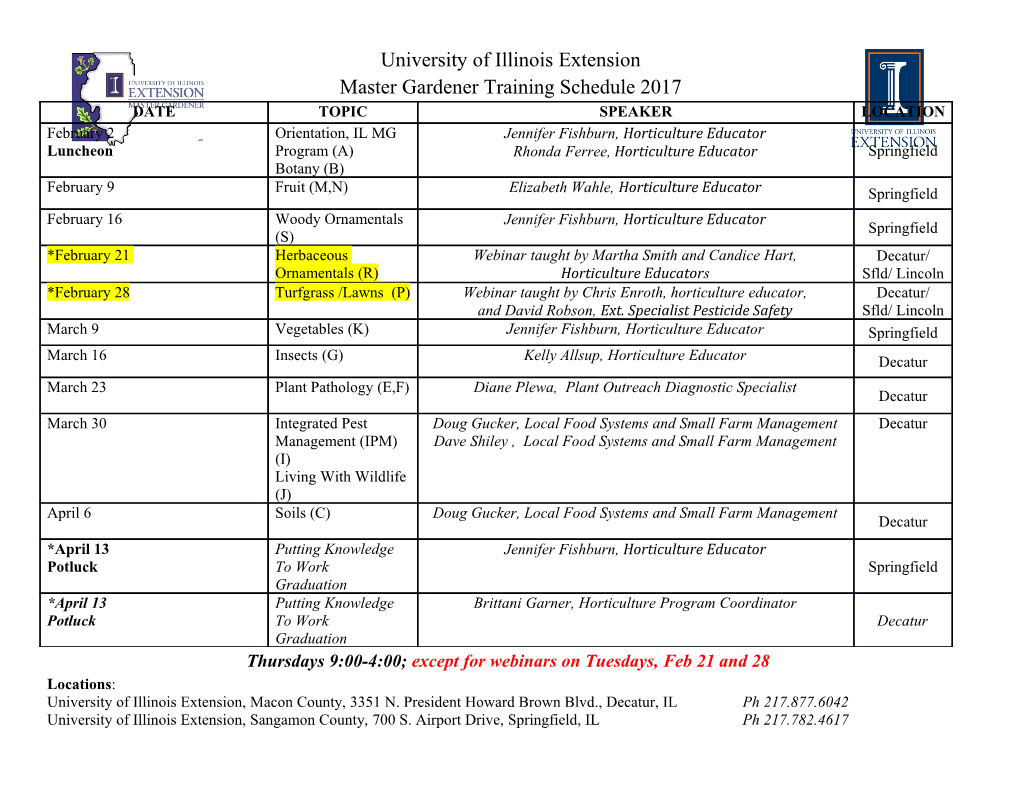
ADVANCED DIE MATERIALS AND LUBRICATION SYSTEMS TO REDUCE DIE WEAR IN HOT AND WARM FORGING Dr. Taylan Altan, Professor and Director, and Mr. Manas Shirgaokar, Graduate Research Associate ERC for Net Shape Manufacturing, the Ohio State University, 339 Baker Systems, 1971 Neil Ave, Columbus OH 43210 USA www.ercnsm.org ABSTRACT Hot and warm forging processes subject the dies to severe cyclic thermal and mechanical fatigue subsequently resulting in die failure primarily through wear, plastic deformation and heat checking. This ongoing study aims to reduce die wear through application of proprietary hot-work tool steels and ceramic-based materials through combination of computational analysis and shop floor experimentation. As part of this initiative guidelines will be developed for a) die design under hot and warm forging conditions, and b) selection of optimum lubrication systems for increased die life. The goals of this FIERF-sponsored study will be achieved through active cooperation with a number of FIA member companies involved in forging, lubrication and tooling. 1 INTRODUCTION Die costs can constitute up to 30% of the production cost of a part and also affect its profitability directly (die manufacturing cost) and indirectly (repair, press downtime, scrap, rework etc). Hot and warm forging processes subject the dies to severe thermal and mechanical fatigue due to high pressure and heat transfer between the dies and the workpiece. High cyclic surface temperatures result in thermal softening of the surface layers of the dies, subsequently increasing die wear and susceptibility to heat checking. Conventional methodologies such as nitriding or boriding result in a significant increase in die surface hardness but have not resulted in substantial improvements in die service life. Recently, a number of advanced grades of proprietary hot-work tool steels have been introduced targeted specifically for warm and hot forging applications. Additionally, the potential for use of ceramic and carbide-based materials in appropriate applications is also of interest. This study proposes to investigate the application of these advanced die materials along with the optimum lubrication system for substantial improvement of die service life in hot and warm forging. It is also emphasized that die design improvements need to be implemented along with the use of advanced die materials in order to realize their maximum potential. This is demonstrated here through some research and production case studies from this project and overseas (Germany and Japan). 1 2 OBJECTIVES AND APPROACH This study officially started on July 15, 2006 with a proposed duration of 12 months and the overall goal of developing techniques to predict and improve die life in hot and warm forging. The following objectives were outlined when the study commenced: a) Improvement of die life in warm and hot forging through application of advanced die materials. b) Development of guidelines for selecting the optimum (cost/productivity) die material and lubrication system for a given application. The goals of this study will be achieved through computational analysis using the commercial finite element simulation code DEFORM™ and subsequent validation with forging trials in cooperation with participating companies. 3 CURRENT STATUS The following is a brief summary of the current project status: • A project website has been created in order to provide up-to-date access to all project documentation to the participating companies. This information can be accessed through the official website of the Center for Precision Forming (formerly Engineering Research Center for Net Shape Manufacturing) at www.ercnsm.org. • Detailed questionnaires were prepared and sent to a) the participating forging companies in order to gather process and die wear related information, and b) the tooling companies to collect die material properties. • A project kick-off meeting was organized on September 28, 2006 at The Ohio State University in Columbus, OH. The purpose of this meeting was to outline the scope of the study and identify common die wear related issues. A few potential parts and die materials were selected for future analysis and trials. • FE analysis was conducted for a few selected parts. A hot forged component was selected in cooperation with Impact Forge (Columbus, IN) for initial analysis and production trials. Die design changes were suggested to reduce contact time with the heated part in critical regions of the dies. Forging trials with advanced hot-work tool steels have been planned tentatively for March 2007. 4 LITERATURE REVIEW OF DIE WEAR STUDIES An important part of the current research study is to review the global hot and warm forging technology with an emphasis on die wear related studies. Two literature reports have so far been provided covering research work conducted in some German institutes along with production case studies from Japan using ceramic/cermet die materials. Development of some proprietary hot-work tool steel grades for warm and hot forging was also covered along with production case studies. Some of these examples are briefly mentioned in the following sections. 2 4.1.1 Case Studies from Germany The examples provided in this section relied on extensive university-based experiments conducted under practical hot forging conditions. Different coating systems and joining techniques for ceramic inserts were investigated for axisymmetric parts and precision forged gears. This information was obtained from the following two sources through contacts established by the CPF (ERC/NSM): • Institute of Metal Forming and Metal Forming Machine Tools (IFUM), University of Hannover. • Chair of Manufacturing Technology, University of Erlangen. Multi-layer duplex coatings and ceramic inserts (SiAlON and silicon nitride) were applied to hot forging of helical spur gears. The 18 layer duplex system showed superior wear reduction over 1000 and 2000 forging cycles (Figure 1). The coatings were applied according to their final achievable hardness in order to give a smooth transition from the coating with maximum hardness (TiC) to that with the lowest hardness (TiN). Figure 1: Performance of ceramic multi-layer coatings compared to nitrided hot- work tool steel (1). For investigations with ceramic inserts, two assembly techniques were explored as shown in Figure 2a. Of these two techniques, brazing is more flexible since it allows the application of inserts in complex tool geometries in wear critical areas. One of the drawbacks of this method, however, is the residual stresses generated from brazing. Thermal shrinking on the other hand is better suited for axisymmetric geometries. The different insert geometries investigated are shown in Figure 2b. The effect of different interference fits and preheat temperatures was not investigated in these studies. Figure 3 shows the wear performance for the ceramic dies compared to nitrided hot- work tool steel for two different forging (workpiece) temperatures after 500 forging cycles. Silicon nitride showed superior wear resistance (3 to 6 times less wear) among the die materials selected. 3 a) Two types of insert design investigated viz. shrink-fit and brazed. b) Different types of shrink-fit designs investigated in forging trials. Figure 2: Die designs investigated in forging trials with ceramic inserts (1). Figure 3: Performance of ceramic die materials in forging trials (1). It was observed during the trials with active brazed inserts that solder quality has to be controlled consistently in order to prevent premature failure of the die in service. A hot forging die with 16 inserts was being considered for precision forging of spur gears (Figure 4). Results from these trials are not currently available. 4 Figure 4: Die with ceramic inserts for precision hot forging of spur gears (1). 4.1.2 Case Studies from Japan There have been cases of successful production application of cermet/ceramic dies in Japan. These publications were in Japanese and only provided limited information. Nissan Motor Co. is using cermet dies made of MoB (ceramic). The material is powder formed and sintered. In production tests, two die materials were tested on forward extrusion of outer race part under warm forging conditions (Figure 5), namely, a) nickel- based superalloy, and b) MoB cermet. Figure 5: Forward extrusion of outer race part (2). Figure 6 shows the high temperature strength of the two die materials. Though the axes are not labeled, it can clearly be seen that MoB cermet die can withstand higher temperature (800°C/1470°F) than the superalloy. Figure 6b also shows die seizure observed with the superalloy material. Figure 7 shows two shrink-fitted hot forging die design examples using ceramic and cermet die inserts with shrink-rings made of hot-work tool steel. Both die designs were implemented in production and involved in-depth experimental analyses of the effect of preheat and forging temperatures on the interference fits at the shrink ring interfaces. It was found that the thermal expansion from preheating and forging had a significant measurable effect on the pre-stress from shrink-fitting. For the Ti alloy preforms, an 82% reduction in shrink-fit was observed after preheating to a temperature of 540°C (1000°F) with just the inner shrink ring (5 in Figure 7a). With the outer shrink ring 5 installed a 47% reduction was observed (3). These examples demonstrate that the use of room temperature dimensions and shrink-fit values for analysis of hot and warm
Details
-
File Typepdf
-
Upload Time-
-
Content LanguagesEnglish
-
Upload UserAnonymous/Not logged-in
-
File Pages26 Page
-
File Size-