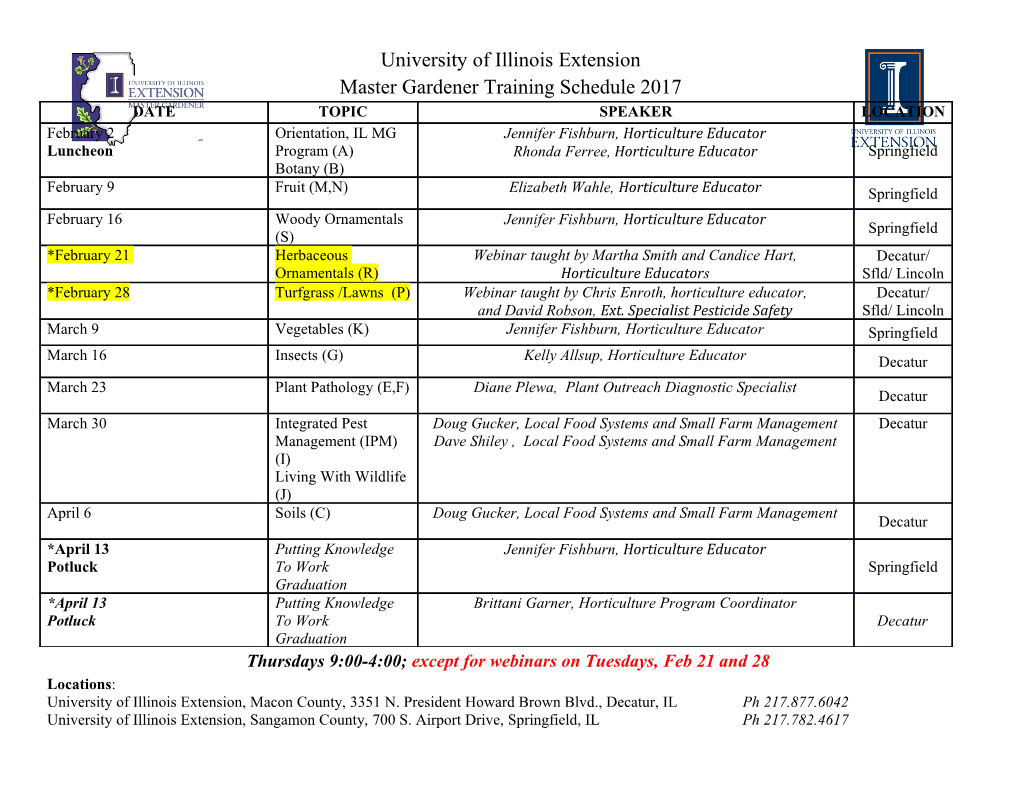
HYDROFORMING An opportunity for You in our business Address: via Ercolano 2 tel: (+ 39) 039 20 45 21 fax: (+ 39) 039 59 64 588 I-20052 Monza MI - Italy [email protected] www.maspero.it The story… Since July ,1st, 1909 we have been dealing with non-ferrous metals. Starting from these roots, always trying to improve ourselves and explore new frontiers, we have experienced many technologies and achieved a very high competence in our core business: non ferrous-metal hot forging. HYDROFORMING : Why In 2004 our company made a Business Unit to develop hydroforming technology. This technology allows to shape tubes and sheets of aluminium, stainless steel and every other metal by using pressed water. By using hydroforming, designers’ creativeness can get rid of the limits of the traditional press technologies in order to achieve extraordinary aesthetical standards with the same mechanical features of the items made with traditional technologies. Hydroforming process scheme for tubes – THF Let’s start from the beginning… The first R & D project concerning Hydroforming Maspero started in 2004 was focused on THF ( Tubes HydroForming) in order to produce items with different sections without any welding process starting from metal extruded tubes. The project was settled to increase company competitiveness developing our knowledge in a technology fit to exploit the physical property of water to transmit pressure in every direction with the same force when pressed. This feature is important since the traditional buckling technologies made with a core can work just in the direction the core is pushed ahead. Moreover it is possible to make undercut as water flows when pressure vanishes. The R&D project - 1 We therefore decided to go on with our project in THF (Tubes Hydro Forming) using what we have learnt in the previous tests to shape two tubes one inside the other, at the same time. We took great advantage by using simulation softwares (Forge and Autoform) we have been using since 2005. These softwares let us increase our knowledge, engineer hydroforming processes and increase our speed in answering to our Customers. This step of the project was mainly involved in the production of a motorcycle exhausted pipe made of two different tubes one inside the other in order to give a long lasting life to the chrome plating of the pipe. At the same time we started working also on items for furniture with very inventive shapes which were very expensive to produce with traditional technologies, thus giving the designers new opportunities to their creativity. Research project After further tests we started to develop tap and fitting items of innovating shape which couldn’t be produced through traditional casting and to make prototypes which could replace traditional soldered motorcycle frames with only one high resistant steel hydroformed part. We have also improved the hydroforming technology for the buckling of sheets in the small batch of production items. At this stage the research has focused on the precompetitive development, on the hydroforming process industrialization, and on the improvement of the simulation techniques. All these experiences have highlighted a growing attention to this technological process, often hindered by too heavy costs of the tools in the past. The aim of this stage of the project has been to deepen our knowledge of the process, in order to be able to industrialize the hydroforming productive process. Where we are now Now we have a new bound to explore, how changing in the temperature affects the possible result. All the previous experiences and tried simulations have highlighted unbelievable opportunities in the use of heat. We are still at an early stage of the search for a technical solution able to find all the advantages coming from plasticity of the high temperature of the item. A solution to this particular problem would widen the utilization possibilities of this technology enormously. Our latest investment In 2008 Maspero bought a new hydroforming press with closing strength of 3,000 tons and hydroforming maximum pression of 4,000 Bars. This investment was made in order to offer a more complete range of productive technologies to our customers and to give a deeper meaning to the idea of productive partnership. Our professional skills begin where your creativity seems to end! Discover the incredible opportunities of this innovating process. Send us a request or a drawing at [email protected] An overview of our products… An overview of our products… An overview of our products… An overview of our products… An overview of our products… An overview of our products… An overview of our products… An overview of our products… An overview of our products… Here the final result! We are waiting for you !.
Details
-
File Typepdf
-
Upload Time-
-
Content LanguagesEnglish
-
Upload UserAnonymous/Not logged-in
-
File Pages20 Page
-
File Size-