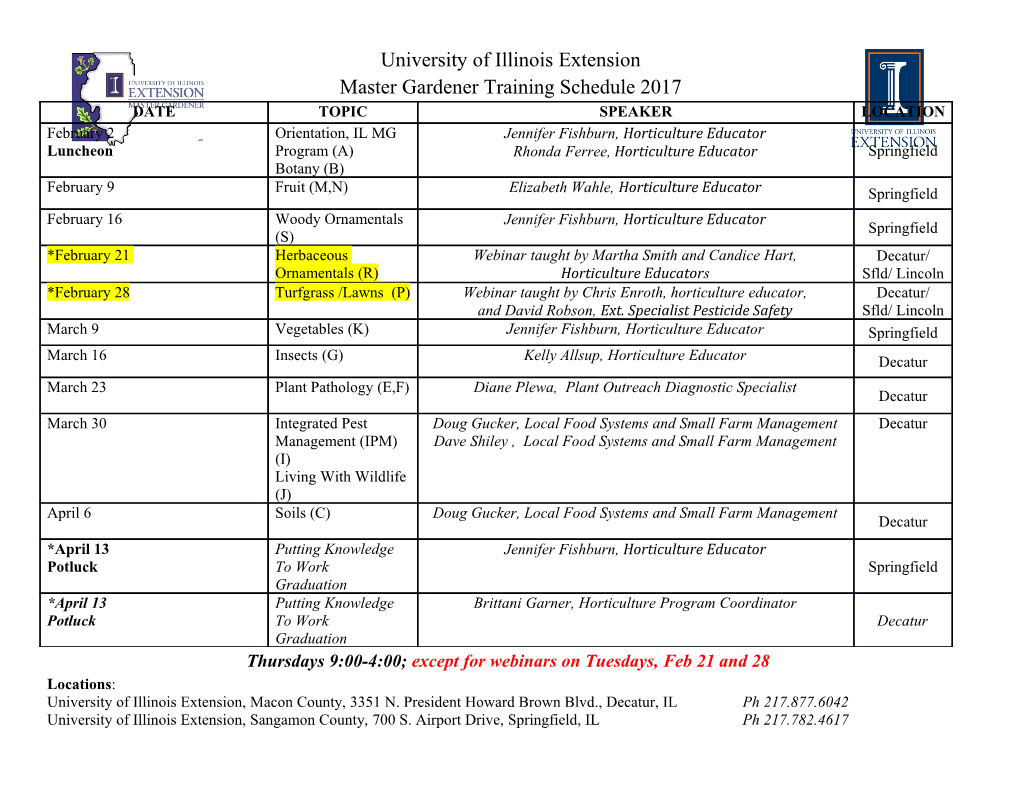
United States Patent Office Patented DC2,862,788 2, 1958 1. 2 potassium salts, such as kainite. In accordance with the instant invention, the liquor remaining following the re 2,862,788 moval of the mixed salts, which liquor will be termed "potassium sulfate reject liquor,” is treated in a manner PROCESS FOR PURIFYING IMPURE SOLID-PHASE to permit the recovery of magnesium values therefrom, KANTE but is also treated to recover a major proportion of Willian N. Stanley, Jr., and William B. Dancy, Carlsbad, the potassium values therefrom in the form of high N. Mex, assignors to International Minerais & Chem. grade potassium salts, such as leonite. In accordance ical Corporation, a corporation of New York with a specific embodiment of the instant invention, be O tween about 60% and about 70% of the potassium values Application May 3, 1955, serial No. 505,717 contained in potassium sulfate reject liquor are recovered as potassium sulfate. ..' . 4 Claims. (CI. 23-38) It is an object of the present invention to increase the overall recovery of potash values from langbeinite. The present invention relates to a process for the treat 5 It is another object of this invention to recover the ment of liquors to recover potassium values therefrom potassium values from kainite containing substantial and more particularly, to a process for recovering po amounts of sodium chloride. tassium and magnesium values from potassium sulfate It is a further object of this invention to provide a reject liquor. - - - - - - - - - - - - - process for recovering potash values from potassium sul In the past, processes have been developed involving 20 fate reject liquor. the production of potassium sulfate over and above the In accordance with the instant invention, kainite con quantities naturally present in langbeinite taining a substantial quantity of sodium chloride as an impurity is treated with water in a manner to remove (KSO-2MgSO) substantially all of the sodium chloride from the solid by reacting an aqueous solution or slurry of potassium 25 kainite without altering or dissolving any substantial chloride substantially free from sodium chloride with amounts of the kainite. The kainite can then be utilized leonite and/or schoenite having the formulate, respective as a low grade potash salt or it may be converted to a ly, K2SO4·MgSO4.4H2O and K2SO4 MgSO46HO, to higher grade potash salt in accordance with one or more produce potassium sulfate and a potassium-containing specific embodiments of this invention. The invention is mother liquor. The leonite and schoenite are produced 30 carried out by treating kainite which may contain up by reacting langbeinite substantially free of sodium chlo to about 25% sodium chloride, by weight, with about 1. ride with the mother liquor separated from the potas part of water for each 3 to 4 parts of kainite-sodium chlo sium sulfate crystals. In this manner a portion of the ride mixture, for a period of less than about 2 minutes, potassium content of the high potassium-containing preferably for less than about 1 minute at a temperature mother liquor is recovered by the production of the 35 of less than about 35° C., preferably at a temperature solid salts, leonite and schoenite, which can be used in of less than about 30° C. Following the treatment, the the reaction step with potassium chloride to produce liquid phase containing dissolved sodium chloride is potassium sulfate. As practiced in the past, these proc separated from the solid kainite. The treatment of the esses have necessarily involved the use of reactants which kainite-sodium chloride mixture with water results in are substantially free of sodium chloride, but it is neces 40 the removal of at least about 75% of the sodium chlo sary to follow a complicated system for handling the ride. The purified kainite can be used directly as a intermediate solids and liquors as outlined in processes, low grade potash for fertilizer purposes or may be treat such as those disclosed by U. S. Patent 2,295,257 to ed to recover the potassium values in the form of a Butt et al. In addition, concentrations of sodium chlo higher grade potash salt. ride, such as are present as impurities in commercially 45 In accordance with a specific embodiment of this in available langbeinite and 60% muriate of potash, seri vention, potassium values in potassium sulfate reject ously reduce the overall recoveries when practicing the liquor may be recovered in the form of potassium sul processes heretofore known. It has been found in prac fate. The potassium sulfate reject liquor which con tice that actual recoveries of the order of between about tains essentially sulfate, chloride, magnesium and po 65% and about 70% of the KO values of the raw mate 50 tassium ions is reacted with carnallite rials are about as high as can be expected by following the processes heretofore practiced. (KCl MgCl2, 6H2O) U. S. Patent 2,684,285 discloses a process which is suspended in an aqueous medium saturated with respect an improvement over the process of U. S. Patent 2,295,- to magnesium chloride, the reaction taking place at a 257. The former patent concerns a process whereby 55 temperature between about 60° C. and about 85° C. the potassium sulfate mother liquor obtained, following When the reaction is substantially complete, kainite a reaction between langbeinite and aqueous potassium solids comprising kainite salts which are formed during chloride to produce potassium sulfate and the removal the reaction are separated from the mother liquor. of potassium sulfate from the reaction mixture, is con- 60 The mother liquor from which the kainite salts have centrated and evaporated to produce certain mixed salts, been removed contains substantial quantities of mag namely, potassium chloride and leonite along with some nesium chloride. This mother liquor is evaporated to kainite (KCl-Mg-SO3H2O). These mixed salts are a point near saturation with respect to bischofite. recycled to the reaction vessel where the reaction between (MgCl, 6HO) langbeinite and potassium chloride takes place. By re cycling the mixed salts to the initial reaction vessel, the 65 that is, to a magnesium chloride concentration of be recovery of potash from langbeinite is improved and the tween about 36%- - and- - about 40%, by weight. Evap oration is usually carried out at a temperature above overall process is more efficient than the process of U. S. about 60° C., preferably at a temperature between about PatentHeretofore, 2,295,257. the liquor remaining following the removal 115° C. and about 120° C. The resulting mixture is of mixed salts has been discarded as waste or treated to 70 then cooled and thickened, preferably at a temperature recover the magnesium values therefrom. The potash of about 90° C., which is the optimum temperature for values, if recovered at all, were recovered as low grade this thickening step. However, temperatures below about 2,862,788 - - - 3 4. 90° C. may also be employed for the thickening step. the liquid phase of which is substantially saturated with If the evaporation is carried out at a temperature above magnesium chloride, is added to the potassium sulfate about 90° C., the concentrated mixture is cooled and reject liquor so that the resulting liquor will be nearly thickened at a temperature below about 90° C. If the saturated with respect to carnallite, for example, kainite is evaporation is carried out at a temperature below about obtained by mixing between about 1.15 parts and about 90° C., the slurry is thickened at the evaporating tem 1.35 parts, by weight, of potassium sulfate reject liquor perature without additional cooling. The underflow from per part of carnallite slurry. Kainite is formed in the the thickener containing carnallite is recycled to the po above described slurry at a temperature between about tassium sulfate reject liquor reaction. 10° C. and about 85° C. Although kainite is formed in It is important that the potassium sulfate reject liquor 0. the slurry throughout the entire temperature range men prior to its reaction wih carnallite be adjusted with, for tioned, the rate of formation of kainite is sufficiently rapid example, an alkaline compound such as sodium hydroxide, to be commercially feasible only at temperatures above to a pH of between about 5.5 and about 6.5, preferably to about 60° C. The kainite salts which are separated from a pH of about 6. If the potassium sulfate reject liquor the solution have a KO content of about 22% and mag has a pH substantially below about 6, for example, a pH 5 nesium oxide content of about 15%. The kainite-form of about 4 or less, considerable corrosion of equipment ing reaction is carried out until the formation of kainite occurs and equally, if not more important, the kainite is substantially complete. This usually requires between salts formed as a result of the reaction between the. about 2 hours and about 4 hours. The kainite salts pro carnallite slurry and a highly acidic reject liquor are duced by the reaction between carnallite and potassium very difficult to filter. If, however, the potassium sul 20 sulfate reject liquor have a typical analysis after washing fate reject liquor is adjusted to a pH between about 5.5 and drying as follows: and about 6.5, the kainite salts formed are very easily Percent by weight filterable. Potassium chloride -------------------------- 34.97 The kainite formed by the reaction between carnallite Magnesium sulfate -------------------------- 44.67 and potassium sulfate reject liquor, upon separation from 25 Sodium chloride ---------------------------- 19.77 the mother liquor, is filtered to remove any excess water About 93% of the KO values in the potassium sulfate which may be present.
Details
-
File Typepdf
-
Upload Time-
-
Content LanguagesEnglish
-
Upload UserAnonymous/Not logged-in
-
File Pages5 Page
-
File Size-