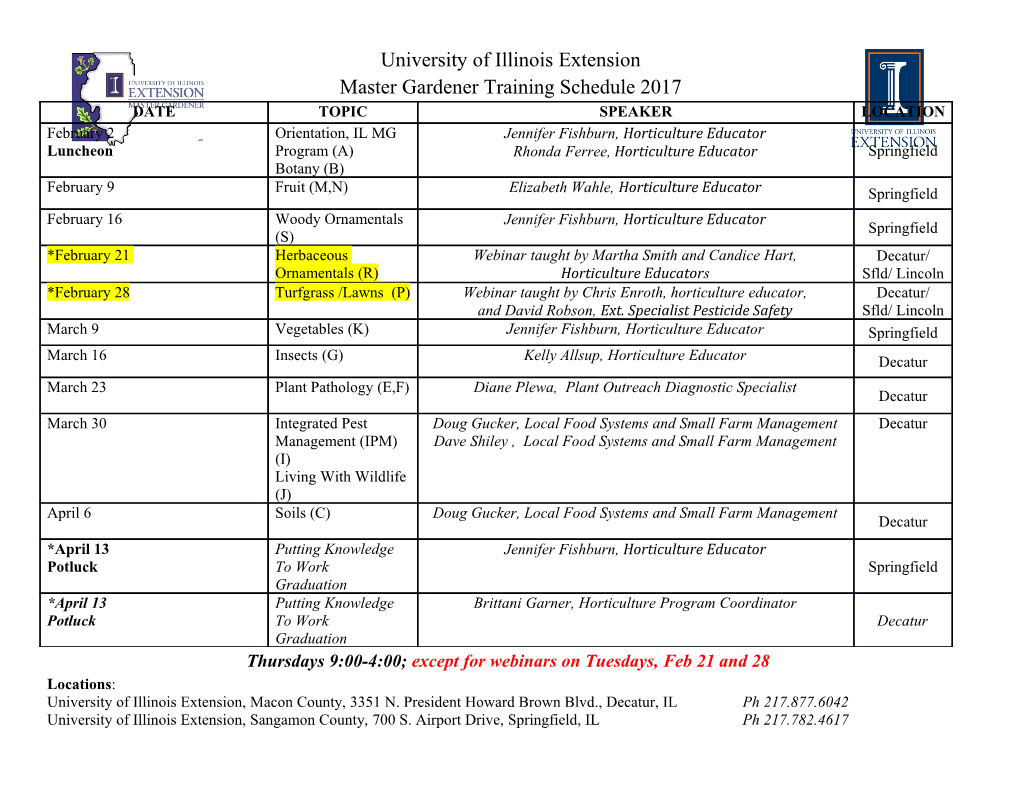
Overview Integrating Functionality Synthetic Multifunctional Metallic-Intermetallic Laminate Composites Kenneth S. Vecchio The field of material microstructure ing properties exhibited by hierarchical to develop synthetic multifunctional design targeted for a specific set of multiphase complex natural composites, materials. Mollusk shells are known to structural and functional properties such as mollusk shells,3,4 to design and possess hierarchical structures highly is now a recognized field of focus in synthesize multifunctional composites optimized for toughness. The two mol- materials science and engineering. This to optimize specific structural properties lusks that have been studied most exten- paper describes a new class of structural while facilitating low-cost, designable, sively are Haliotis rufescens (abalone) materials called metallic-intermetallic and functional microstructures. and Pinctata (conch) shells. Considering laminate (MIL) composites, which can Biological systems often exhibit a the weak constituents the shells are have their micro-, meso- and macro- wide array of multifunctional materials made from—namely calcium carbonate structure designed to achieve a wide and offer great biomimetic motivation (CaCO3) and a series of organic binders, array of material properties and tailored the mechanical properties of these shells to achieve specific functionalities. The are outstanding. Their tensile strength superior specific properties of this class varies between 100 MPa and 300 MPa of composites makes them extremely and fracture toughness between 3 MPa 1/2 attractive for high-performance aero- and 7 MPa-m . CaCO3 has correspond- space applications, and the fabrication ing strength and toughness values of 30 method for creating MIL composites MPa and <1 MPa-m1/2, respectively.5–9 allows new embedded technologies to be These mollusks owe their extraordinary incorporated into the materials, enhanc- mechanical properties to a hierarchically ing their functionality and utility. a 2 µm organized structure starting with single crystals of CaCO , with dimensions of INTRODUCTION 3 4–5 nm (nanostructure) and proceeding The field of material microstructural with bricks with dimensions of 0.5–10 design to achieve a set of targeted µm (microstructure, Figure 1a), and mechanical and functional properties finishing with layers of ~0.2–0.5 mm has become a mainstay of new mate- (mesostructure, Figure 1b). rial development strategies. Structural Building on the laminate microstruc- materials, which by their very nature ture design found in shells, Ti-Al3Ti MIL are intended to carry mechanical loads composites have been produced to mimic in service, can be designed to provide these structures from elemental titanium additional performance-enhancing func- and aluminum foils by a novel one-step tions through tailoring of meso-, micro-, process utilizing a controlled reaction at or nano-structures. Structural materials elevated temperature and pressure.2 The with these performance-enhancing novelty of this fabrication process lies capabilities have been termed “synthetic in the fact that it is performed in open multifunctional materials.”1 Structural air and produces a fully dense laminate composites, by their multiphase nature, composite. Figure 2 shows an illustration offer many opportunities for the design b 300 µm of the processing setup for fabrication of of performance-enhancing multifunc- Figure 1. (a) An SEM micrograph of the MIL composites using a simple open- the fracture surface of an abalone shell tional materials. Recently, a new class of showing the individual hexagonal aragonite air heated platen press. The thickness of structural materials has been developed tiles comprising the microstructure. (b) the original titanium and aluminum foils at the University of California, San An optical micrograph of the mesoscale is chosen to ensure that the entire alu- laminate structure of the abalone shell in Diego, termed metallic-intermetallic a bend fracture sample showing the crack minum layer is consumed upon reaction 2 laminate (MIL) composites. The goal of deflection achieved in this multi-layered with the adjacent titanium layers. Such a this materials development effort was to material. layering scheme results in a composite extrapolate upon the positive engineer- with alternate layers of Al3Ti (to mimic 2005 March • JOM 25 the hard CaCO3 layers in shells) and residual titanium (to mimic the tough protein layers in shells). The thickness of the final layers is dependent upon the thickness of the original aluminum and titanium foils. This process is highly flexible since metal/alloy foils other than titanium can be used individually, or in combination, within the same composite, to produce their respective metal/metal- aluminide combinations. For example, MIL composites using iron-based, nickel-based, and cobalt-based alloys as the starting metal layer (instead of tita- nium) have been successfully fabricated using the described technique. The MIL composites produced by this method are Figure 2. An illustration of metallic- Figure 3. The microstructures typical of not hierarchical structures in the manner intermetallic laminate composite heated Ti-Al Ti MIL composites. using platen press apparatus for fabrication 3 that natural shells are, but are rather of planar laminates. Complex platen two-dimensional laminate structures. In designs can be used to fabricate 3-D, near-net-shape MIL composites in the these structures, the scale of the layering same one-step, open-air operation. can be controlled, tailored, subdivided, and compositionally altered to achieve desired properties and functions. The composition, physical, and mechanical properties of the MIL com- posites can be varied and tailored within the thickness of the composite by simply 0.1 varying the individual foil compositions, thicknesses, and layering sequence. The fabrication of MIL composites using this approach has several key advantages that make it ideally suited for the production of commercially scalable structural Specific Compressive Strength Specific Compressive materials as well as microstructures 0.01 designed for specific functionalities. First, since the initial materials utilized are in the form of commercially available 0.01 Specific Modulus 0.1 metallic foils, the initial material cost is Figure 4. A materials property map comparing specific compressive strength versus specific material stiffness. reasonably low compared to many of the exotic material processing routes that 10−1 are commonly pursued in small-scale research environments. This also means 10−2 that a wide array of compositions can be ready produced, although this paper will focus on the Ti-Al system because of its 10−3 high specific properties. Second, the use of initially ductile 10−4 metallic foils enables the layers to be formed into complex shapes. This opens da/dN mm/cyc the door for non-planar structures, such 10−5 as rods, tubes, shafts, and cones, as well as simple machining of individual foils a 10−6 for complex, three-dimensional (3-D) Figure 5. (a) Quasi-static three-point structures and near-net shape forming bend samples for fracture-toughness of parts. The use of initial metallic 10−7 measurements, and (b) fatigue foils also allows the individual foils crack growth curves for various MIL 1 2 4 6 8 10 20 40 60 100 composites. b ∆K MPa√m to be machined to contain cavities and pathways facilitating the incorporation 26 2005 March • JOM of embedded functionalities, such as 5 passive damping or sensors, prior to ) 3 processing. /kg/m Third, the processing conditions, 1/2 0.01 in terms of temperature, pressure, and atmosphere are very modest. Processing temperatures, in the case of aluminum-foil-containing samples, are below 700 C and the processing ° 0.03 pressures are below 4 MPa.2 Perhaps the most remarkable feature of the processing of these MIL composites is that the processing is carried out in open (MPam Toughness/Density Fracture air, and no special inert gas or vacuum chamber facilities are necessary. 0.01 0.1 The combination of these processing Young’s Modulus/Density (GPa/(kg/m3)) features makes the processing method Figure 6. A specific-fracture-toughness versus specific-modulus property map for an array of structural materials. Plot includes MIL (Ti-Al3Ti) composites (dark gray colored) itself low cost, allows for complex and other laminate systems (identified by (L) and outlined in red), metals, alloys, and shape fabrication, and is amenable to composites. computer control. Finally, the microstructure of the MIL composites is determined by the foil thickness and composition and the processing condition. Since the material make-up is based on the selection of the metal foils, it is possible to completely tailor the microstructure from one surface to the other. In addition, the physical and mechanical properties of a the MIL composites can be tailored by selection of the foil composition and Figure 7. (a) A cross section thickness, making the MIL composite of the impact location from material system ideally suited for a ballistic test on an MIL composite (the plate thickness is engineering the microstructure to 2 cm). (b) An optical micrograph achieve specific performance goals. of a ceramic-fiber-reinforced Of the various possible aluminides in MIL composite for enhanced ballistic performance. the Ti-Al system, the formation of the intermetallic Al3Ti is thermodynami- b 500 mm cally and kinetically favored over other aluminides when reacting aluminum directly with titanium.
Details
-
File Typepdf
-
Upload Time-
-
Content LanguagesEnglish
-
Upload UserAnonymous/Not logged-in
-
File Pages7 Page
-
File Size-